部门:美的集团股份_职能部
需求OU:**美芝制冷
发布时间:2023-06-21
1. 设备变更点
1.1 入口输送线飞水、接水盘设计过小、线路按规定分布、具体审图尺寸标定
1.2液压油管外围到设备部位安装方式改善、方便日常维修
1.3 卡盘工件压紧改用标准液压缸使用
1.4 入口顶升装置轴密封性不良、改进轴与托盘之间密封
1.5 液压系统增加油量检测功能
1.6 主轴冷却增加流量液位功能
1.7 整机气体需配置增压缸储气罐
机加工轴承镗床技术协议
合同编号:
签约时间:
签约地点:
2. 设备信息
2.1. 设备名称: 轴承内孔镗床
2.2. 设备型号:
2.3. 设备编码:
2.4. 设备数量:
2.5. 设备方案:
3. 机床采用立式加工形式。每台设备有相对应的两组主轴和夹具,每套夹具一次装夹1件,一次加工共完成两件。滑台伺服驱动,进给速度可灵活调整。夹具采用油压夹紧。采用冷却液进行冷却,自动上下料。机床整机形式如下图:
4. 工艺路径图:
5. 设备布局图:
5.1. 设备结构:
5.2. 设计要求:
部件序号
名称
配置要求
参考示意图
①
夹具结构
定位方式:轴承下基准面定位,精密卡盘定位,换型采用整体换型夹紧手抓,每种零件对应一套夹紧手爪工装。
夹紧方式: 气压夹紧、液压压紧(压点与支点一一对应)。
②
主轴结构
1、装配前保证各零件的清洁度,并 注意操作方式及装配环境的清洁;
2、冷却管路布局美观**;
3、主轴推荐转速为3600rpm。
③
冷却系统
配置专用冷却箱,加工用切削液进行精过滤,全部过滤冷却液精度2级过滤,强磁分离+纸带精过滤≤20μm,其中冲洗两个定心工位的过滤精度增加SMC超精密过滤装置(磁性+精过滤+超精密过滤≤5μm),并有自动反冲洗功能,确保不因切削液过脏造成工件加工直角度不良,完成切削的润滑和冷却,床身的清洁,排屑机的反冲水过滤,排屑装置使用“**沃邦XQCF-400”。设备冷却系统采用独立冷却系统,每台设备配带一个冷却交换器“**神威BC-519T”,设备磨削液实现自主循环冷却,并安装支架及接水盘,主冷冻水管路由甲方制作,正常生产中,过滤纸带的24H走纸不超过5次(5米)。
④
液压系统
邮箱尺寸高200*宽476,
⑤
润滑系统
数控滑台导轨丝杠的润滑是采用自动润滑泵集中自动供油润滑方式,油品和甲方现场的通用,配置机油壶设计放置点。
⑥
气动系统
气压检测OK,灯亮绿色
反之, 则显示灯,亮黑色
⑦
主轴滑台机构
1、装配前保证各零件的清洁度,并注意操作 方式及装配环境的清洁;
2、轴承允填进口长效润滑脂; 3、配磨轴承压盖,使其轴承有合适的预紧力;
4、装配完成后要求丝杠跳动0.01mm以内。
⑧
手动画面
进入每个工位的调整画面,自动参数设置画面;执行每个工位的单循环操作
切换到辅助功能(水泵,润滑,气动,夹具,主轴)画面;执行单循环过程中,对应工位绿灯闪烁
⑨
自动画面
当操作盘上的“手/自动选择开关”在“自动”状态下时,灯亮绿色
反之, 则灯亮黑色
⑩
电气控制系统
三菱Q系列PLC系统,Q03UDVCPU,QD77MS16运动模块,MR-JE伺服驱动器控制器
6. 设备主要结构及具体要求
2.1.1 设备专机要求:
2.1.2
2.1.3 前工序流入设备前通过电机/感应器调整工件至指定角度后方可搬运至加工工位,工件夹紧/压紧后主轴启动镗削工件内孔,加工完毕后搬运工件至测量工位检测内孔直径,根据内孔直径值与设定值差异可自动调整镗刀直径尺寸,之后工件流出设备进入下一工序。
2.1.4 夹紧/压紧机构保证工件加工过程中稳固,且无变形;
2.1.5 自动测量可以显示内孔直径具体尺寸,当检测值超出设定值一定范围,设备报警停机,人为干预后方可继续生产,当检测值与设定值偏差在较小范围内,设备可以根据检测值对镗刀直径进行小范围调整;自动测量需要定期校准,并进行定期校准提示。
2.1.6 机床结构形式:
床身采用HT250灰铁铸成,铸造外表面需刀检, Ra12.5以下。床身采用后排屑形式,且非安装面带有铸造斜度,内部配有大排量冷却液冲刷系统,便于切屑的排除,外壳使用201不锈钢不喷漆,机床底座喷漆。
1) 数控滑台和动力头:数控滑台基座与床身一体铸造,丝杠导轨采用上银产品,由三菱伺服电机驱动,主轴配备2套数控刀具补偿系统,加工完成后,每个工件对应检测、反馈,实现刀具磨损补偿的同时可以让刀退刀,避免退刀痕的产生。
2)夹具:采用精密卡盘定位,避免装卸工件造成的压力波动对加工的影响。
3)电气设备:由控制箱,可编程序控制器(PLC),操作盒,及模拟显示部件等组成。给予设备以各种程序的动作,触摸屏10寸。操作盘至少可以180度旋转。
4)自动上下料机构:工件定位后,机床配有自动上下料机构,外部桁架物流,每次横移搬送2个工件。伺服电机(品牌(三菱))+齿轮齿条传动,配上下输送链,上料输送链长度:2800mm,下料输送链长度:3000mm,高度上料暂定1210mm,链体安装翻转装置、寻位装置,以确保不管前后工序物料的正反向都不需甲方另行增加,同时出口输送链体与后工序的铰珩入口链体合并考虑。(输送链高度双方审图确定)。
5)冷却系统:
配置专用冷却箱,加工用切削液进行精过滤,全部过滤冷却液精度2级过滤,强磁分离+纸带精过滤≤20μm,其中冲洗两个定心工位的过滤精度增加SMC超精密过滤装置(磁性+精过滤+超精密过滤≤5μm),并有自动反冲洗功能,确保不因切削液过脏造成工件加工直角度不良,完成切削的润滑和冷却,床身的清洁,排屑机的反冲水过滤,排屑装置使用“**沃邦XQCF-400”。设备冷却系统采用独立冷却系统,每台设备配带一个冷却交换器“**神威BC-519T”,设备磨削液实现自主循环冷却,并安装支架及接水盘,主冷冻水管路由甲方制作,正常生产中,过滤纸带的24H走纸不超过5次(5米)。
6)润滑系统:数控滑台导轨丝杠的润滑是采用自动润滑泵集中自动供油润滑方式,油品和甲方现场的通用,配置机油壶设计放置点。
7)电气控制系统:采用三菱Q03系列PLC,设备具有刀具加工件数报警功能。设备各部分具有可靠的安全保护、保险措施,以防止误操作或意外事故致使机床受损或造成人身伤亡。
8)机床防护:机床门为拉合式(推拉门)结构(双方审图确定)外壳使用201不锈钢不喷漆,以方便刀具更换、设备维修和保养;机床危险区域应有醒目的标示;机床设计符合国家环保要求,噪声小于78分贝。
9)镗床夹具:夹具及布置图照片如下所示。
定位方式:轴承下基准面定位,精密卡盘定位,换型采用整体换型夹紧手抓,每种零件对应一套夹紧手爪工装。
夹紧方式: 气压夹紧、液压压紧(压点与支点一一对应)。
10)依据双方前期方案交流,使用刀具等消耗品单耗不能高于甲方量产水平。
11)翻转装置安装在入口链上(翻转方式审图时确定)。
12)开有安全门时配报警安全开关,主机采用全封闭防护罩,避免生产过程中切屑和切削液的溅出。
13机床静态精度表:(附件五(静态精度))
14)夹具卡盘调整需要顶丝调整,方便调整**度,直线度;
1. 详细技术要求
机床主要配置
序号
参数名称
单位
数值
1
刀补主轴最大转速
r/min
5000
2
主轴最大行程
mm
200
3
主轴个数
个
2
4
工作台工位数(含检测)
个
4
加工对象和加工要求(轴承内孔镗床加工工艺要求)
1.设备与前后工序有机械手及信号对接,完成自动搬送物物料的生产线,自动上下料的配置参考技术协议书。
2.可加工机种
2.1验收机种
上轴承M线: SK-1(MC****1611)、SM-5(MC****1010)、SN-2(MC****1110)
上轴承L线:SN-2(MC****1110)、SK-1(MC****1611)
下轴承C线: SN-3(MC****4010)、SK-C(MC****1010)、SK-1(MC****0210)、SN-2(MC****4410)
下轴承D线:SM-5(MC****1310)、SF(MC****1710)
2.2兼容机种
上轴承M线:HSM(MC****0110)
上轴承L线:SN-2A(MC****1910)
下轴承C线:SN-F(MC****3410)
下轴承D线:SM-51 VA(MC****0810)
3.技术要求及参数
通过段取工装夹具可以实现加工机种尺寸:
验收机种:上轴承:SN-2/SK-1/SM-5/SN-2、下轴承:SN-3/SK-C/SK-1/SM-5/SF/SN-2(每个系列一个机型),11个机型均需乙方配置工装图纸和实物。
兼容机种:上轴承:HSM/SN-2A、下轴承:SN-F/SM-51 VA(每个系列一个机型),4个机型均尽可能与验收机种共用一套工装,如需更换工装,乙方提供需更换的工装图纸,不要求提供实物。
配置原则如下:
1、通用型工装配1套;
2、非通用型工装根据产品特征配置,保证验收机种内每一个机种都有工装可生产;
3、极易磨损的工装额外配2套或以上。
工装设计:需保证与甲方量产设备工装通用。
3.1加工对象:轴承内径精加工。
3.1.1机种名称:上轴承:SN-2/SK-1/SM-5/SN-2、下轴承:SN-3/SK-C/SK-1/SM-5/SF/SN-2
3.1.2加工位置及精度(未描述项目及测量方法详见加工图)
项目
保证值
测量方法和备考
机种
上轴承:SN-2/SK-1/SM-5/SN-2
下轴承:SN-3/SK-C/SK-1/SM-5/SF/SN-2
内径尺寸
±0.003mm
气动量仪
圆度(半径)
≤0.003mm
真圆度仪(应不是棱圆或多边形状)
圆柱度
≤0.006mm
气动量仪
内径直角度
按《零件加工规格书》《检查规格书》
气动量仪
内径粗糙度
≤Rz6
粗糙度仪其他地方描述有争议以此为准
3.2加工余量:满足加工前后图纸要求
3.3加工节拍:
CT=MT+HT≤ 10/件(含上下料时间);后移载装置要求≤9.5 秒/件 (CT 含上下料时间)。
3.4.1系列内段取时间:≦10分钟(相关更换机种的螺丝需考虑快速化,只包括硬件更换时间)
3.4.2系列间段取时间: ≦30分钟,只包括硬件更换时间
3.4.3段取方式的设计:方便段取、定位精度准确。
4.设备说明书份数:三套(随机提供电子版U盘,消耗品、工装、易损零件图提供CAD可修改电子版)
5. 设备验收
5.1. 预验收在乙方厂进行,验收内容包涵(但不限于):
设备加工能力验收:连续加工零件各150件,尺寸公差、同轴度、圆柱度、垂直度、圆度及表面粗糙度每5件抽检1件,共抽检30件。全部符合3.1.2为通过。
5.2预验收和正式验收在甲方厂进行,验收内容包涵(但不限于):
1) 工装验收
2)工装夹具图纸及CDROM(CAD版本)验收
3)设备加工能力验收:
NO
项目
详细内容
要求
1
生产节拍
① 加工时间(MT):从启动按钮到设备加工休止时间
② 辅助时间(HT):从设备休止到按启动按钮的时间,即加工下一个零件的时间,包括零件的装卸时间
③ 生产节拍:CT=MT+HT
④ 连续加工100个零件,计算每件零件加工需要的平均时间
内孔高度≤40mm,CT=MT+HT≤11 秒/件(含上下料时间);40mm<内孔高度≤55mm,CT=MT+HT≤ 12/件(含上下料时间);硬件软件不低于轴承 K 线。后移载装置要求≤9.5 秒/件 (CT 含上下料时间)。
2
工序能力
加工机种的选择
预验收
正式验收
加工数
150个/机种
小批量:500个/机种
大批量:5000个/机种
测定工件个
30个/机种
小批量:30个/机种
大批量:30个/机种
加工及测定工件
上轴承:SN/SK/HSM
下轴承:SN/SK/SM/SF
上轴承:SN/SK/HSM
下轴承:SN/SK/SM/SF
满足《零件加工规格书》和《检查规格书》中的尺寸精度要求。
3
正式验收对加工稳定性验证
按正常生产条件连续加工24H以上,设备无故障,加工零件连续加工按1件/40分钟,共取样30个,按《零件加工规格书》《检查规格书》中的要求进行尺寸检查。
无因设备关系的原因引起的停机或异常
零件精度合格率100%
注:1)初验收过程:由甲方提供验收机型每个机种工件100件,供乙方进行设备初验收,超出部分由乙方承担。
2)设备在甲方厂内调试至设备终验收完成期间,产生报废工件,甲方可承担200件,超出部分由乙方承担。
2. 机床主要配置:
序号
主要零部件
配套厂家
1
三菱 PLC
日本三菱Q03系列,带网口、配交换机
2
主旋主轴
电主轴(**睿莹/数格,质保2年)
3
往复伺服电机
日本三菱
4
气缸、气阀
日本SMC
5
滚珠丝杠
**HIWIN、THK
6
滚动导轨
**HIWIN、THK
7
主轴轴承
NSK
8
电动润滑泵
**贝奇尔
9
按钮旋钮
施耐德
10
三色灯
西门子
11
电柜空调
迪威特( DLQ05B.Wa)
12
对刀仪
1台
13
入口输送带
1套(乙方配置,可以手摇调整输送宽度)
其它要求:
1、电柜门需安装密封条,保证外部油雾、水雾无法侵入电柜;
2、主电柜门配置检测开门的开关,当电柜门打开时,设备降低速2秒运行;
3、电箱需前工程与后工程各2个联机继电器,并配置信号线及作好标识;
4、配置1个停机继电器,继电器线圈由甲方控制,继器接通后设备实现循环停机;
5、设备故障率:设备故障率≤1.0%(故障率=故障时间/开机时间);
6、设备颜色要求:设备表面:Munsell 2.5G 9/10 设备防护栏:Munsell 2.5Y 8/12;
7、 机床安全门上安装锁止保护开关与接近开关,自动中开关扣着安全门不能打开,手动后开关解锁才能开门后,安全门防护要求接近开关和锁止开关由可编程安全控制器与PLC双回路控制,品牌要求:欧姆龙 规格:D4DS-25FS、E2E-X3D1-N,立宏 规格SM-602(配通讯线)。( 符合附件二《设备安全防护要求》 )。
机床防护罩、防护门、操作面板使用201不锈钢,不要喷漆。
8、设备资料:设备说明书3套;电子版说明书1套、PLC带注释程序、触摸屏、所有控制器程序放入U盘提供甲方(有密码的需提供密码)。
自动化设备设计及制造 | 原厂直销 | 100万元以上 | 中国 | **省 | 150 | 12 | 10年以上 |
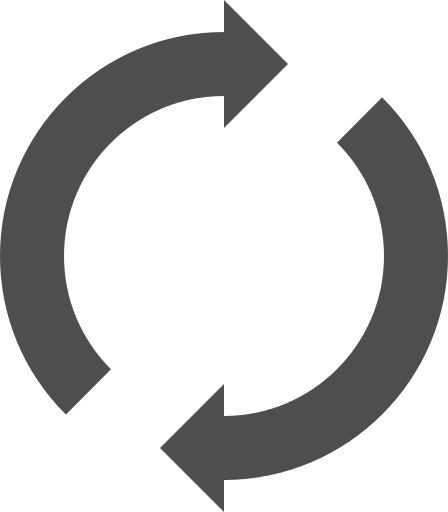