更新时间 | 2024年02月18日 |
查看更多海尔集团采购项目,点击此处
1 项目概述
为承接斐科腾智能科技(青岛)有限公司对自动化设备的需求,特邀请贵司参与外销铁油箱自动焊接线项目竞标,在此对本次竞标情况作出说明。
1.1 目标读者
本项目业务干系人员,参加此项目的团队以及参加该项目投标的供应商团队。
1.2 项目目标
此项目不允许出现安全问题、质量缺陷、预算超标等问题,同时需满足工期要求。(技术要求)
2 相关背景分析
2.1 需求背景
斐科腾智能科技(青岛)有限公司(以下简称甲方)与竞标方(以下简称乙方)项目合作模式如下:
1. 甲方提供技术要求、技术方案。
2. 甲方负责提供订单工期。
3. 乙方入厂人员应按甲方厂内要求来执行相关规定(安全、行为规范),并指定专人负责所有入厂人员的管理。
2.2 项目背景
技术要求具体需求如下:
产品信息
1.1工件尺寸规格
板材尺寸公差值范围参考
序号 | 详细要求 |
1 | 材质:DC01/不锈钢板/Q235、SPHC、DC01 |
2 | 重量:最小重量: 100Kg 最大重量:250Kg |
3 | 板材尺寸:板材长度:450-2000mm、板材宽度:2000-3700mm、板材厚度:2-3mm |
4 | 板材平面翘曲公差范围:±2.5mm,且可以被吸附。 |
5 | 来料板材对角线差值:≤3mm |
6 | 整垛板料位置精度:±5mm ,(上料不同批次之间不保证差值,自加工板材码垛位置精度不大于100mm) |
7 | 板材放置位置偏差:≤100mm。 |
8 | 同批次板材屈服强度差值符合国标要求 |
9 | 来料板材厚度公差值符合国标要求 |
现有规格输入原料信息
截面(mm) | 材质 | 料厚(mm) | 壳体长度(mm) | 圆角 | 质量(kg) | |
1 | 750*750 | DC01/不锈钢板/Q235 | 2-3 | 450~2000 | 平面圆弧R2000-无限大 四角过渡R100 | 100~250 |
2 | 700*700 | |||||
3 | 750*900 | |||||
4 | 950*950 | |||||
5 | 750*800 | SPHC | 四角过渡R100 | |||
6 | 680*650 | DC01 | 500-1200 | 平面直线 四角过渡R100 | 100-120 | |
7 | 650*620 |
1.2图纸
1.3工艺流程
设备生产工艺流程详细要求
序号 | 详细要求 |
1 | 板料上料折方生产方式:上料装置→对中装置→全自动四辊折方机生产→升降输送线 |
2 | 油箱筒纵焊生产方式:折方油箱桶180°翻转装置→折方油箱桶上料装置→油箱筒导向定位→纵焊专机→输送线 |
3 | 油箱筒冲孔生产方式:油箱桶定位→机械手上料→油箱桶冲孔机→机械手下料→输送线 |
4 | 隔板压装生产方式:隔板搬运上料→油箱桶上料→油箱桶导向定位→隔板压装机→油箱桶下料→输送线 |
5 | 隔板焊接生产方式:油箱桶上料→机器人焊接+激光跟踪(倾斜)→油箱桶下料→输送线 |
6 | 油箱桶端盖环焊生产方式:油箱桶上料→端盖上料→机器人焊接+激光跟踪(倾斜)→油箱桶下料→输送线 |
7 | 激光打标生产方式:油箱桶上料→激光打标机→油箱桶下料→输送线 |
详细要求 · 1.设备设计符合人机原理,操作方便安全,可最大限度减少工艺动作,降低劳动强度并不会对操作人员的个人身体条件提出高于平常的要求。 · 2.充分考虑设备的运行可靠性和无维修设计,设备运行稳定故障率低,易于维修。 · 3.设备安装、调整、换模、移位方便可靠。因发生以上工作时,设备不得出现因结构不合理引起的变形或破坏。 · 4.设备设计制造充分考虑了产品质量的稳定性和品种适应性,有开放性结构方便后来的品种、型号变换和设备技术的升级换代。 · 5.设备整体设计和安装质量符合国家或者国际有关规范,设备外型美观,结构工艺性合理并按规范工艺安装到位。 · 6.设备元器件齐全完整,动作灵敏可靠;安全防护装置设计周到,防护合理。 · 7.设计充分考虑了工艺操作和安全生产所需要的分控制、启停、急停、连动、保护等,可最大程度保证生产连续、流畅、均衡进行,可最大限度减少设备急开紧停、系统等待等原因引发的效率损失。 · 8.设备运行过程中无异常声音,振动、无异常气味、温升符合标准;压力在允许范围之内。 · 9.润滑装置、气、油等过滤装置齐全有效,系统工作良好能耗正常,无跑,冒,滴,漏现象。 · 10.设备原材料和部件选择必须选择知名品牌的优质产品,并采用国际或中国国标互换通用标准零部件接口,不得采用非标技术特殊化组件接口,原材料和部件无设计缺陷和明显的加工缺陷,连续启停动作100次以上无失效和过度磨损现象。 · 11.设备设计应充分考虑部件的标准化和通用性,一般不得采用技术独享性质的元器件,而应自国内和国际知名的供应商处选取。 · 12.该设备的设计加工是建立在对使用方产品、工艺、工位操作排布、使用条件和环境完全了解的基础上并与之相适应。 · 13.设备接地良好,保证静电及时释放,保证安全生产。 |
注:清理、去毛刺、子件焊接、清及气密工序甲方负责,乙方做好工序之间的流转。端盖压装、焊之后,乙方负责输送至补焊、子件焊工站,后续补焊、子件焊及气密性检测完全由甲方负责。
1.4产线要求
1.产线节拍:5.5min/件,以DS055G11010074(铁质)与DS055G11010072(不锈钢材质)油箱为准核定产能节拍。其产线节拍偏差不超过0.5min。
2. 直产人数要求:加工人数≤5人(包括试水工位2人)。其加工人数偏差不超过1个人。
3. 设备使用寿命大于100000小时
4. 本生产线的制作具备良好的工艺性、美观大方;
5.故障率<0.8%,综合效率>90%,单台设备可动率达到98%;
6. 具备良好的安全性。在各设备加装安全保护装置,以保证操作员与产品的安全,让设备具有良好的安全生产特性;
7. 各工序参数可调,能适应不同规格油箱产品的流水自动化作业;
8.具有良好的操作便捷、可维性。在整套生产线的设计中应考虑操作便捷,维护方便,各设备运动面要求自动润滑,各设备应预留维护与保养空间;
9. 设备布局合理;气路、动力线、控制线路铺设应符合国家要求,产线设备音噪不超过80分贝;
10.流水线需保留人工介入,产线设计时,必须满足人体工学,需要人工参与的工序加工人仅承担辅助工作,不需承担搬运、上下料、焊接等高强度或技能型劳动(子件焊接、补焊除外,但不需承担搬运、上下料等高强度动作);
11.产线整体控制系统由供应商提供,包括四台自制的油压机设备。
12.本项目是包括设备提供、系统集成在内的交钥匙工程,完成立体生产线系统的设计、制造、运输、安装、调试和售后服务内容;
13、需要上料的工位,全部布置在过道侧,上料过程中应安全、便捷,不得和产线运行发生干涉,焊丝上料除外;
14、供方提供的货物必须是全新的、未使用的原装产品,且在正常安装、使用和保养的条件下,其使用寿命周期内各项指标均达到质量要求;
15、所有焊接设备设计时应考虑焊丝更换周期,焊丝更换周期小于8小时,必要时应采用桶装焊丝;
16、生产所用原材料及子件采取配送制,配送人员不计入整线直产人员中,但原材料及子件料斗放置区域应便于人工(叉车、行车)或自动(AGV小车)补料;
17、焊接成品工件,必须满足GB18296相关性能要求;
18、乙方的设备、工装设计及制造,必须以甲方的图纸或者实物为主。
二、产线要求
2.1车间平面图
2.2设备功能要求
2.2.1送料小车、分张器
a. 上料小车可切换自动和手动模式
自动模式:每台料车拆垛完成料空后可返回上料工位,料车自动退出并声光报警。(预留信息化自动换料对接接口)
手动模式:小车的开进、开出为人工安全确认自动运行,操作者只要启动按钮,所有的动作全部自动完成
b. 上料小车进出时有声光报警器提示。
c. 小车导轨沉于地下,无突出干涉。
d. 上料台车上配置定位装置以便操作者方便地垛放把托盘和料到位。定位装置可以快速拆下并安装到其他位置以便适应不同大小的定尺料。
e. 在每个小车上设有末料检测开关,用于有无料检测和便于最后一张时提前换料,也可以通过操作面板设置板料数量,以便板料抓取装置取料和停止,同时设有声光警示装置,以提醒操作者。
f. 上料小车配备强力分张系统,使上层坯料实现简便分离。分张装置的数量和尺寸可确保坯料完全分离。
g. 上料小车的分张系统需要实现不锈钢板的分张,保证不锈钢板可以正常生产;
h. 分张器实现长度范围450-2000mm,宽度范围2000-3700mm,厚度范围2-3mm板材的分张工作
i. 不需要人员的干预下,分张器可实现0-300mm高度范围内的板材分张;
j. 分张器工作时,需保证使用人员安全;
k. 分张后的板材能够被板材上料机吊装;
l. 板材放置位置偏差≤100mm,都可实现分张。
m. 台车载重(含托盘):最大18吨
n. 上料小车运行时有防护罩防止伤脚。
o. 人工或者AGV给上料小车放料时上料位置需要设置上料原点或者基准,降低上料小车上板材放置位置的偏差。
2.2.2板材上料机
a. 取料平稳、吸附力紧,取料过程中不能发生倾斜、掉落等现象;(气动元件选型及气路设计时需要保证抓取机构在断电、断气情况下气路保压板料不发生掉落)
b. 保证板料表面无划伤、压痕等外观缺陷;
c. 板料码垛后,位置精度±5mm;
d. 吸盘位置及数量可调整,便于不同尺寸板料取料;
e. 增加断电保护,断电后,板材不会掉落;
f. 板材平面翘曲±2.5mm范围内,可以被吸附,且不会掉落。
g. 可以实现长度范围500-2000mm,宽度2000-3700mm,厚度2-3mm,重量≤240kg范围内板材的吊装;
h. 板材放置位置偏差≤100mm,都可实现吊装;
i. 线首拆垛板材上料机带双板料检测功能及抖料装置。
j. 要求采用真空吸盘系统实现自动取放板料操作。真空吸盘系统由吸盘+真空发生器+气缸+电磁阀组成,根据产品的需要,每套吸盘架吸盘数量一次性配置,吸真空可独立控制,切换型号后自动切换吸盘使用数量。在触摸屏上有相应设定界面;
k. 板材上料机抓取物料后在输送过程中必须保证板材产品的质量;
l. 真空发生器真空端安装灰尘过滤器,具备真空检测功能,检测信号与板材上料机动作对接;
m. 端拾器吸盘数量及位置根据产品型号组合,满足设备需求方产品的生产。
2.2.3伺服控制全自动四辊折方机
a. 折方过程不应对板材产生划伤,压痕等表面问题;
b. 各辊轴运动(升降、旋转)需采用伺服电机驱动;
c. 需配置自动出料机构,在出料过程中,保证壳体表面无磕碰、划伤等外观缺陷;
d. 出料机器手与折方机进行联动,在折方时给与油箱支撑,防止油箱自重及刚性不足导致的失稳和重叠现象;
e. 可以实现长度≤2000mm油箱壳体的折方;
f. 板材进出料方式:上料移载机械手真空吸盘吸取单张板材放置于自动进料台中,进料台自动对中板材并将板材送入折方机折方,自动推出折方机;
g. 板材定位方式:以板材两侧面对中,以中心线为基准定位,后端由推板推动并精确定位板材的初始定位位置;
h. 板材折方方式:板材通过上下辊之间,移动下辊挤压板材进行折弯;
i. 折弯半径通过下辊组件上下移动的位置精确控制。四角R值要求从R100-R120,可以连续调整,误差±5mm;四边R值要求从R100-R无穷大(直线)可以连续调整,误差±5mm;折方截面尺寸满足工件尺寸规格,误差(+5、0),对角线差值≤3mm;
j. 控制系统具有手动和自动控制功能:在手动状态下,可以在控制面板上手动输入,实现每一步的动作控制;在自动状态下,系统接收启动信号后,设备按设定的程序逻辑完成自动动作;
k. 根据折方动作及产品型号,折方程序可设定多段,每段的参数均可单独设定并存储;参数应于公置单位进行表达;
l. 折方机两边进给精度要求误差不超过±0.2mm/1000mm;
m. 箱体成型重复一致性误差不超过1mm;
n. 壳体对中压紧后,对接缝隙小于0.5mm;
o. 折方后筒体开口:0~+15mm,直线段长度小于10mm,筒体前后错边量小于3mm/m;
p. 辊轴需选用强度和稳定性好的材料,连续运转5年或者30万件产品辊轴不能变形,设备精度不能下降;
q. 按工件尺寸规格制造设备,应实现在精度要求范围全尺寸可调;
r. 设备配送料平台要求牢固、可靠,方便叉车或AGV小车上料,送料平台与机架应连接为一个整体;
s. 箱体成型后四角圆弧与四边圆弧接合处应过渡圆滑,不允许存在折痕,急剧过渡等影响美观及装配要求的问题;
t. 设备内需设有不同截面参数存储功能;
u. 折方机应设计为龙门式,不得采用悬臂梁结构,折方轧辊运动应具有较高的精度±0.1mm;设计时考虑便于调整及维护;
v. 设备运动部件都应设有安全防护装置;
w. 筒体折方速度≥850mm/min;
x. 折方后筒体自由状态两端口尺寸与理论数据小于2.5mm(检测方法:在一平板上做一环槽,深度8mm,,内边小于工件内边2.5mm,外边大于工件外边2.5mm。卷板后筒体自由状态能够不受外力的情况下轻松放入槽内)
2.2.4筒体纵缝焊接专机
a. 专机焊接,焊接工艺:MAG焊接;
b. 焊接方式:琴键夹具压紧工件,焊枪自动行走,实现纵缝自动焊接。
c. 只需更换保护气和焊丝,就能够实现不锈钢和碳钢焊接,焊缝强度大于母材强度;
d. 焊缝连续、美观,不能出现扭曲、断点、焊透等外观缺陷;
e. 纵焊垫板采用铬锆铜等导电性、导热性好、硬度高的材质;
f. 焊缝内部要求:焊缝内部质量优良,不得存在裂纹、密集气孔、未熔合等缺陷,焊缝内部满足气密试验要求;
g. 单面焊接,双面成型;
h. 焊缝余高1-3mm,焊宽8-10mm
i. 焊缝气密合格率≥99%;
j. 焊接过程中,不得造成壳体变形,焊接完成后壳体尺寸精度(+5、0),对角线差值≤3mm;
k. 工件进出料方式:同端进料与出料或一端进料、一端出料,带有辅助进料和出料的装置;
l. 带有辅助对缝装置,保证壳体焊缝快速对中固定并夹紧;
m. 壳体焊缝对齐夹紧工装可以实现400mm-2500mm范围内壳体纵焊缝对齐夹紧,夹紧对齐之后,工装不得和纵焊机琴键压紧机构发生干涉;
n. 纵焊机的琴键压紧机构将筒体压紧之后,压紧面不得呈V字形,两个面夹角需要控制在179.5°-180.5°之间;
o. 纵焊机下方需要增加壳体举升托架,在焊接时防止因为重力作用导致壳体变形;
p. 纵焊机焊接速度要求500-1000mm/min,焊缝强度及成型均应满足要求;
q. 参数应于公制单位进行表达;
r. 焊接变形≤5mm/m;
s. 纵焊机悬臂高度需满足产品焊接要求;
t. 纵焊缝在筒体中央,或者焊缝距一侧150mm时,均应满足以上要求;
u. 琴键系统包含一个安全连锁开关,防止芯轴挂钩没有到位时,系统发生误操作。芯轴挂钩将通过气缸驱动打开和关闭,开合顺畅,减少人工操作。
v. 琴键式夹紧机构可夹持并焊接的最长工件为2500mm。每对琴键的宽度为40mm,相对琴键间的距离在0-30 mm之间可调,以适应不同焊接工艺的要求。为适应不同厚度焊件的焊接,琴键压紧力在0-75Kg/cm2之间可调。琴键设计有推进功能,可自动将工件的一边向前推进,推进距离约0.4mm,以消除对中间隙;琴键材料选用高强度及热导率高的铝合金材料,配有可以两面使用的铜合金指尖。
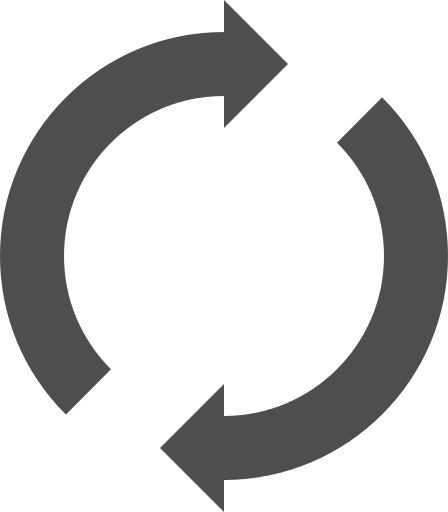