广东喜珍电路科技有限公司新建年产384万平方米线路板建设项目(二期工程288万平方米线路板)
1、建设项目基本信息
企业基本信息
**** | 建设单位代码类型:|
****1200MA53LX3B2E | 建设单位法人:徐向东 |
梁洪敏 | 建设单位所在行政区划:**省**市**区 |
**省**市**区**新区科创大道11****学园1栋1楼 |
建设项目基本信息
******年产384万平方米线路板建设项目(二期工程288万平方米线路板) | 项目代码:|
建设性质: | |
2018版本:083-电子元件及电子专用材料制造 | 行业类别(国民经济代码):C398-C398-电子元件及电子专用材料制造 |
建设地点: | **省**市**区 **新区科创大道11****学园1栋1楼 |
经度:112.66779 纬度: 23.18578 | ****机关:****生态环境厅 |
环评批复时间: | 2020-12-21 |
粤环审〔2020〕310号 | 本工程排污许可证编号:**** |
项目实际总投资(万元): | 88000 |
2928 | 运营单位名称:**** |
****1200MA53LX3B2E | 验收监测(调查)报告编制机构名称:**** |
****1200MA53LX3B2E | 验收监测单位:******公司 |
****1203MA5506CT0A | 竣工时间:2023-12-01 |
调试结束时间: | |
2024-05-22 | 验收报告公开结束时间:2024-06-20 |
验收报告公开载体: | https://www.****.com/gs/detail/2?id=40522CtYQl |
2、工程变动信息
项目性质
** | 实际建设情况:** |
二期工程增加1条OSP线,为中间生产工序,不增加最终产品产能。 变动报告中开料、钻孔、成型等工序产生的粉尘分别经7套袋式除尘器处理后由2条排气筒高空排放,实际建设为粉尘分别经7套袋式除尘器处理后合并1条排气筒高空排放(DA051)。 | 是否属于重大变动:|
规模
二期建设年产288万平方米/年双面板、多层印制电路板 | 实际建设情况:年产288万平方米/年双面板、多层印制电路板 |
无 | 是否属于重大变动:|
生产工艺
二期工程产品类型包括双面板及多层板生产线(含沉镍金、电金、沉银、沉锡工序)。 1、内层制作 将覆有铜箔的基板开料裁剪成所需尺寸的板材,然后经过内层前处理工序,除去铜箔表面的氧化物和粗化表面,便于后续干膜和铜表面结合;然后,在板材表面贴干膜覆盖,并利用底片曝光原理将电路图形呈现在板面上;接着,进入显影、蚀刻、去膜,完成内层线路制作;为了能进行有效层压,需对内层板面进行棕氧化,使内层板线路表面形成一层高抗撕裂强度的黑/棕色氧化铜绒晶,增加后续压合工序的结合能力;然后,配合半固化片/覆盖胶膜及铜箔进行迭板层压形成多层板。 (1)内层制作前处理工艺 将基材板按需要裁切成所需尺寸,然后经过水洗将基板表面粉尘去除。 (2)内层显影/蚀刻/去膜/涂布 主要是为了形成线路板的内层线路。 ①化学前处理:包括微蚀、酸洗工序,以硫酸为主剂,除去板面上油脂。再以吹干的方式去除水洗残留在板面上的水分。 ②压干膜或涂布油墨 刚性板采用涂布油墨工艺。另外,**度互连印制电路板内层如果需要打孔采用贴膜工艺,如果不需要则和多层板内层相同,均采用涂布油墨工艺。 压干膜采用的干膜是由聚酯薄膜、光致抗蚀剂薄膜和聚乙烯保护膜三部分组成。聚酯薄膜是支撑感光胶层的载体,使之涂布成膜。聚乙烯保护膜是覆盖在感光胶层上的保护膜,防止灰尘等污物粘污干膜。贴膜是以适当的温度及压力将干膜紧密贴覆在铜面上。 涂布油墨是利用滚涂油墨涂布机将抗蚀性感光油墨滚涂在覆铜箔基板上。 ③曝光:将线路图案底片置于感光干膜/油墨上,利用感光干膜/油墨在紫外光照时形成集合反应,在紫外光照射下曝光显影,使线路图案下的油墨感光硬化,将设计的图形转移到线路板上。 ④D.E.S(显影/蚀刻/去膜):项目内层蚀刻采用酸性蚀刻工艺,即:压干膜或涂布油墨后,经显像液(Na2CO3)将线路以外未感光硬化的油墨或干膜去除,然后以酸性蚀刻液将铜箔上未覆盖抗蚀性油墨的铜面全部溶蚀掉,仅剩被硬化的油墨或干膜保护的线路铜,再进行脱模(NaOH),溶解线路铜上硬化的油墨或干膜,使线路铜裸露出来,并进行多级水洗后烘干。 酸性蚀刻的化学反应式: Cu+CuCl2→Cu2Cl2 在蚀刻过程中,氯化铜中的Cu2+具有氧化性,可将板面上的铜氧化为Cu2+,形成Cu2Cl2不溶于水,当有过量的Cl-存在的情况下,就形成可溶性的络离子。 Cu2Cl2+4Cl-→2[CuCl3]2- 溶液中的Cu2+随着线路板不断被蚀刻而增多,蚀刻液的蚀刻能力随之下降,或失去蚀刻能力,此时会更换槽液(委外处理处置),再重新调配(采用次氯酸钠、盐酸按照一定比例进行混合调配)投入使用。 (3)AQI(自动光学检测) AOI(AutomaticOpticInspection)的全称是自动光学检测,是基于光学原理来对线路板生产中遇到的常见缺陷进行检测的设备。在D.E.S工序后对基板进行AOI检测,剔除不合格的基板。 (4)棕氧化/压合/锣边 将已形成内层线路的多个双面板进行叠合压制,形成多层板,具体工序包括: ①酸洗、碱洗:先酸性除油剂除去铜面氧化物,再进行碱性除油。 ②预浸:主要目的为活化铜表面。 ③棕化:为了能进行有效层压,需对内层板面进行棕氧化,均匀咬蚀铜面使板面粗化,并形成棕化膜,增加铜面与绝缘材料的接触面积,提高结合力。 ④熔合:卷状半固化片(pp片)裁切成工件要求的尺寸后叠放到棕化板两侧,并通过几个固定点固定在一起。 ⑤排版:按要求将熔合后的多片内层板、PP片及铜箔叠合在一起。 ⑥压合:项目先采用热压合,再采用冷压合。热压合是将叠合好的多层板热压在一起,热压温度为200~220℃,压力为2.45Mpa,为时2小时。 ⑦锣边:除去线路板边上多余半固化片,按产品外形锣出所需形状尺寸。 2、外层线路制作 (1)外层前处理 根据不同产品的规格,在线路板上钻出各类孔。具体工程包括: ①钻靶:利用X光钻靶机找到内层板的靶标,钻出定位孔。 ②机械钻孔:用铝板、纸底板将多层芯板固定,然后利用钻机在线路板上钻出各种非导通或导通孔。 (2)沉铜线(PTH) 根据企业建设情况,一期建设除胶沉铜线条为4条。其中,2条生产线进行竣工环境保护验收。 ①沉铜线(PTH)工序 即为沉铜工序,利用化学沉铜原理在通孔表面形成一层铜膜导电层,起到连接多层铜板的目的。 PTH工序主要包括膨松、除胶渣(去钻污)、化学沉铜等。在化学沉铜前,需对基板进行除胶渣,主要是用高锰酸钾去除前面钻孔遗留的氧化物。另外需要进行微蚀,主要是为了粗化铜的表面,为后续沉铜、板电提供良好的附着面。 化学沉铜使经钻孔后的非导体(除胶渣后通孔内有的地方是半固化片(绝缘层))通孔壁上沉积一层密实牢固并具导电性的金属铜层,作为后续全板电镀铜的底材。化学镀铜是一种催化氧化还原反应,因为化学镀铜层的机械性能较差,在经受冲击时易产生断裂,所以化学镀铜只是作为后续电镀铜的前处理工序。其基本原理为化学氧化还原反应,即:铜离子在催化表面上被还原剂还原沉积成金属膜,反应方程式为: Cu2++2CHCHO+4OH-→Cu+H2+2H2O+2HCHCOO- 生产上,以甲醛作为还原剂,由于甲醛只有在碱性条件下才具有足够的还原能力,故镀液中需加入络合剂以防止氢氧化铜沉淀的产生。现有项目沉铜槽主要是添加沉铜药水(主要成分为铜离子、氢氧化钠、EDTA、甲醛)。由化学反应式可知,在沉铜反应时,氢气的溢出会带出一部分的甲醛气体。 ②全板镀铜工序 项目全板镀铜采用DVCP线,以铜球作阳极,CuSO4和H2SO4作电解液,在钻孔及整个半成品表面形成一层薄的铜膜,不仅使通孔内的铜层加厚,同时也可使热压在外表面的铜箔加厚,为后续的电镀提供基底。 (1)AQI AOI(Automatic Optic Inspection)的全称是自动光学检测,是基于光学原理来对线路板生产中遇到的常见缺陷进行检测的设备。在D.E.S工序后对基板进行AOI检测,剔除不合格的基板。 (2)棕氧化 将已形成内层线路的多个双面板进行叠合压制,形成多层板,工艺具体为: 酸洗、碱洗:先酸性除油剂除去铜面氧化物,再进行碱性除油。 预浸:主要目的为活化铜表面。 棕化:为了能进行有效层压,需对内层板面进行棕氧化,均匀咬蚀铜面使板面粗化,并形成棕化膜,增加铜面与绝缘材料的接触面积,提高结合力。 熔合:卷状半固化片(pp片)裁切成工件要求的尺寸后叠放到棕化板两侧,并通过几个固定点固定在一起。 排版:按要求将熔合后的多片内层板、PP片及铜箔叠合在一起。 压合:项目先采用热压合,再采用冷压合。热压合是将叠合好的多层板热压在一起,热压温度为200~220℃,压力为2.45Mpa,为时2小时。 锣边:除去线路板边上多余半固化片,按产品外形锣出所需形状尺寸。 2、表面加工成型工艺 (1)阻焊 阻焊工艺包含丝印、阻焊预烤和阻焊后烤三个步骤。丝印和阻焊预烤设置在全封闭的无尘车间(厂房)内操作,车间环境属于微正压,通过中央空调送风及设备抽风系统维持车间内压力及环境空气质量。丝印机设置围罩,同时采用进行抽风,收集效率按90%计。 预烤、后烤隧道炉和烤箱顶部均设置废气抽排风管的废气收集方式,且隧道炉和烤箱在运行过程中均为密闭状态,只有线路板进出时会有少量有机废气排出。 (2)终检 OSP(Organic Solderability Preservatives)为有机保护膜,即在洁净的裸铜表面上,用化学的方法所生长的一层有机皮膜,厚度在0.2-0.5μm间,防止裸铜氧化。主要包括除油、微蚀、成膜等工序。 (3)成型、成品清洗、检测及包装入库 使用专用模具将线路板的外型按设计要求冲切出来,将不需要的废料和电路板分离。然后进行成品清洗,洗掉板面上的灰尘。采用电测和目检的方式,检查线路板的线路是否形成回路,是否导通或断开,剔除不合格品。最后包装入库。 在基板表面导体上先镀上一层镍后再镀上一层金,目的是提高耐磨性,降低接触电阻,防止铜氧化,提高连接的可靠性。但铜表面直接镀金会因铜金界面扩散形成疏松态,在空气中形成铜盐而影响可靠性,为此,镀金前先镀一层镍,能有效阻止铜金相互扩散。化学镀镍为自催化氧化还原反应,一般以次磷酸盐作为还原剂,反应式如下: H2PO2-+H2O→HPO32-+H++2H Ni2++2H→Ni↓+2H+ 2H2PO2-+H→HPO32-+H2O+P+H2↑ 化学镀金其机理为置换反应,具体反应式如下: Ni+2Au(CN)2→2Au+Ni2++2CN- 化学镀镍槽、镀金槽中均设有回收水洗工序,回收槽液通过配套的树脂回收机定期回收其中的贵金属后分别作为含镍废水、****处理站进行处理。 此外,化学镍槽7天炸缸保养1次,每次炸缸持续时间12小时左右,在常温下采用25%硝酸进行镍的氧化消解,炸缸采用低浓度硝酸、炸缸过程中添加烟雾抑制剂等措施,避免高浓度硝酸雾产生。 沉锡生产线采用硫酸亚锡为沉锡溶液,在电路板上积沉纯锡层。化学沉锡的机理是通过改变铜离子的化学电位使槽液中的锡离子发生化学置换反应,其实质是电化学反应,被还原的锡金属沉积在基板铜的表面上形成锡镀层,且其浸镀层上吸附的金属络合物对锡离子还原为金属锡起催化作用,以使锡离子继续还原成锡,确保化学沉锡镀层之厚度。 主要是提高线路的耐磨性,减低接触电阻,防止铜氧化,提高连接的可靠性,即在基板表面导体上沉积很薄的金属银层,化学镀银槽及后续二级逆流漂洗槽排放出的清洗废水进入废水处理系统的漂洗废水收集池。 本项目采用无氰镀银工艺,镀液由银盐、还原剂两种溶液组成,银盐(化学沉银药水A)主要由硝酸银组成,还原剂(化学沉银药水B)主要为酒石酸钾钠,根据化学电位差之原理,因银与铜之间的电位差距,使得铜与银离子间进行自发性的置换反应,使得铜表面浸上一层薄银。 | 实际建设情况:二期工程产品类型包括双面板及多层板生产线(含沉镍金、电金、沉银、沉锡工序)。 1、内层制作 将覆有铜箔的基板开料裁剪成所需尺寸的板材,然后经过内层前处理工序,除去铜箔表面的氧化物和粗化表面,便于后续干膜和铜表面结合;然后,在板材表面贴干膜覆盖,并利用底片曝光原理将电路图形呈现在板面上;接着,进入显影、蚀刻、去膜,完成内层线路制作;为了能进行有效层压,需对内层板面进行棕氧化,使内层板线路表面形成一层高抗撕裂强度的黑/棕色氧化铜绒晶,增加后续压合工序的结合能力;然后,配合半固化片/覆盖胶膜及铜箔进行迭板层压形成多层板。 (1)内层制作前处理工艺 将基材板按需要裁切成所需尺寸,然后经过水洗将基板表面粉尘去除。 (2)内层显影/蚀刻/去膜/涂布 主要是为了形成线路板的内层线路。 ①化学前处理:包括微蚀、酸洗工序,以硫酸为主剂,除去板面上油脂。再以吹干的方式去除水洗残留在板面上的水分。 ②压干膜或涂布油墨 刚性板采用涂布油墨工艺。另外,**度互连印制电路板内层如果需要打孔采用贴膜工艺,如果不需要则和多层板内层相同,均采用涂布油墨工艺。 压干膜采用的干膜是由聚酯薄膜、光致抗蚀剂薄膜和聚乙烯保护膜三部分组成。聚酯薄膜是支撑感光胶层的载体,使之涂布成膜。聚乙烯保护膜是覆盖在感光胶层上的保护膜,防止灰尘等污物粘污干膜。贴膜是以适当的温度及压力将干膜紧密贴覆在铜面上。 涂布油墨是利用滚涂油墨涂布机将抗蚀性感光油墨滚涂在覆铜箔基板上。 ③曝光:将线路图案底片置于感光干膜/油墨上,利用感光干膜/油墨在紫外光照时形成集合反应,在紫外光照射下曝光显影,使线路图案下的油墨感光硬化,将设计的图形转移到线路板上。 ④D.E.S(显影/蚀刻/去膜):项目内层蚀刻采用酸性蚀刻工艺,即:压干膜或涂布油墨后,经显像液(Na2CO3)将线路以外未感光硬化的油墨或干膜去除,然后以酸性蚀刻液将铜箔上未覆盖抗蚀性油墨的铜面全部溶蚀掉,仅剩被硬化的油墨或干膜保护的线路铜,再进行脱模(NaOH),溶解线路铜上硬化的油墨或干膜,使线路铜裸露出来,并进行多级水洗后烘干。 酸性蚀刻的化学反应式: Cu+CuCl2→Cu2Cl2 在蚀刻过程中,氯化铜中的Cu2+具有氧化性,可将板面上的铜氧化为Cu2+,形成Cu2Cl2不溶于水,当有过量的Cl-存在的情况下,就形成可溶性的络离子。 Cu2Cl2+4Cl-→2[CuCl3]2- 溶液中的Cu2+随着线路板不断被蚀刻而增多,蚀刻液的蚀刻能力随之下降,或失去蚀刻能力,此时会更换槽液(委外处理处置),再重新调配(采用次氯酸钠、盐酸按照一定比例进行混合调配)投入使用。 (3)AQI(自动光学检测) AOI(AutomaticOpticInspection)的全称是自动光学检测,是基于光学原理来对线路板生产中遇到的常见缺陷进行检测的设备。在D.E.S工序后对基板进行AOI检测,剔除不合格的基板。 (4)棕氧化/压合/锣边 将已形成内层线路的多个双面板进行叠合压制,形成多层板,具体工序包括: ①酸洗、碱洗:先酸性除油剂除去铜面氧化物,再进行碱性除油。 ②预浸:主要目的为活化铜表面。 ③棕化:为了能进行有效层压,需对内层板面进行棕氧化,均匀咬蚀铜面使板面粗化,并形成棕化膜,增加铜面与绝缘材料的接触面积,提高结合力。 ④熔合:卷状半固化片(pp片)裁切成工件要求的尺寸后叠放到棕化板两侧,并通过几个固定点固定在一起。 ⑤排版:按要求将熔合后的多片内层板、PP片及铜箔叠合在一起。 ⑥压合:项目先采用热压合,再采用冷压合。热压合是将叠合好的多层板热压在一起,热压温度为200~220℃,压力为2.45Mpa,为时2小时。 ⑦锣边:除去线路板边上多余半固化片,按产品外形锣出所需形状尺寸。 2、外层线路制作 (1)外层前处理 根据不同产品的规格,在线路板上钻出各类孔。具体工程包括: ①钻靶:利用X光钻靶机找到内层板的靶标,钻出定位孔。 ②机械钻孔:用铝板、纸底板将多层芯板固定,然后利用钻机在线路板上钻出各种非导通或导通孔。 (2)沉铜线(PTH) 根据企业建设情况,一期建设除胶沉铜线条为4条。其中,2条生产线进行竣工环境保护验收。 ①沉铜线(PTH)工序 即为沉铜工序,利用化学沉铜原理在通孔表面形成一层铜膜导电层,起到连接多层铜板的目的。 PTH工序主要包括膨松、除胶渣(去钻污)、化学沉铜等。在化学沉铜前,需对基板进行除胶渣,主要是用高锰酸钾去除前面钻孔遗留的氧化物。另外需要进行微蚀,主要是为了粗化铜的表面,为后续沉铜、板电提供良好的附着面。 化学沉铜使经钻孔后的非导体(除胶渣后通孔内有的地方是半固化片(绝缘层))通孔壁上沉积一层密实牢固并具导电性的金属铜层,作为后续全板电镀铜的底材。化学镀铜是一种催化氧化还原反应,因为化学镀铜层的机械性能较差,在经受冲击时易产生断裂,所以化学镀铜只是作为后续电镀铜的前处理工序。其基本原理为化学氧化还原反应,即:铜离子在催化表面上被还原剂还原沉积成金属膜,反应方程式为: Cu2++2CHCHO+4OH-→Cu+H2+2H2O+2HCHCOO- 生产上,以甲醛作为还原剂,由于甲醛只有在碱性条件下才具有足够的还原能力,故镀液中需加入络合剂以防止氢氧化铜沉淀的产生。现有项目沉铜槽主要是添加沉铜药水(主要成分为铜离子、氢氧化钠、EDTA、甲醛)。由化学反应式可知,在沉铜反应时,氢气的溢出会带出一部分的甲醛气体。 ②全板镀铜工序 项目全板镀铜采用DVCP线,以铜球作阳极,CuSO4和H2SO4作电解液,在钻孔及整个半成品表面形成一层薄的铜膜,不仅使通孔内的铜层加厚,同时也可使热压在外表面的铜箔加厚,为后续的电镀提供基底。 (1)AQI AOI(Automatic Optic Inspection)的全称是自动光学检测,是基于光学原理来对线路板生产中遇到的常见缺陷进行检测的设备。在D.E.S工序后对基板进行AOI检测,剔除不合格的基板。 (2)棕氧化 将已形成内层线路的多个双面板进行叠合压制,形成多层板,工艺具体为: 酸洗、碱洗:先酸性除油剂除去铜面氧化物,再进行碱性除油。 预浸:主要目的为活化铜表面。 棕化:为了能进行有效层压,需对内层板面进行棕氧化,均匀咬蚀铜面使板面粗化,并形成棕化膜,增加铜面与绝缘材料的接触面积,提高结合力。 熔合:卷状半固化片(pp片)裁切成工件要求的尺寸后叠放到棕化板两侧,并通过几个固定点固定在一起。 排版:按要求将熔合后的多片内层板、PP片及铜箔叠合在一起。 压合:项目先采用热压合,再采用冷压合。热压合是将叠合好的多层板热压在一起,热压温度为200~220℃,压力为2.45Mpa,为时2小时。 锣边:除去线路板边上多余半固化片,按产品外形锣出所需形状尺寸。 2、表面加工成型工艺 (1)阻焊 阻焊工艺包含丝印、阻焊预烤和阻焊后烤三个步骤。丝印和阻焊预烤设置在全封闭的无尘车间(厂房)内操作,车间环境属于微正压,通过中央空调送风及设备抽风系统维持车间内压力及环境空气质量。丝印机设置围罩,同时采用进行抽风,收集效率按90%计。 预烤、后烤隧道炉和烤箱顶部均设置废气抽排风管的废气收集方式,且隧道炉和烤箱在运行过程中均为密闭状态,只有线路板进出时会有少量有机废气排出。 (2)终检 OSP(Organic Solderability Preservatives)为有机保护膜,即在洁净的裸铜表面上,用化学的方法所生长的一层有机皮膜,厚度在0.2-0.5μm间,防止裸铜氧化。主要包括除油、微蚀、成膜等工序。 (3)成型、成品清洗、检测及包装入库 使用专用模具将线路板的外型按设计要求冲切出来,将不需要的废料和电路板分离。然后进行成品清洗,洗掉板面上的灰尘。采用电测和目检的方式,检查线路板的线路是否形成回路,是否导通或断开,剔除不合格品。最后包装入库。 在基板表面导体上先镀上一层镍后再镀上一层金,目的是提高耐磨性,降低接触电阻,防止铜氧化,提高连接的可靠性。但铜表面直接镀金会因铜金界面扩散形成疏松态,在空气中形成铜盐而影响可靠性,为此,镀金前先镀一层镍,能有效阻止铜金相互扩散。化学镀镍为自催化氧化还原反应,一般以次磷酸盐作为还原剂,反应式如下: H2PO2-+H2O→HPO32-+H++2H Ni2++2H→Ni↓+2H+ 2H2PO2-+H→HPO32-+H2O+P+H2↑ 化学镀金其机理为置换反应,具体反应式如下: Ni+2Au(CN)2→2Au+Ni2++2CN- 化学镀镍槽、镀金槽中均设有回收水洗工序,回收槽液通过配套的树脂回收机定期回收其中的贵金属后分别作为含镍废水、****处理站进行处理。 此外,化学镍槽7天炸缸保养1次,每次炸缸持续时间12小时左右,在常温下采用25%硝酸进行镍的氧化消解,炸缸采用低浓度硝酸、炸缸过程中添加烟雾抑制剂等措施,避免高浓度硝酸雾产生。 沉锡生产线采用硫酸亚锡为沉锡溶液,在电路板上积沉纯锡层。化学沉锡的机理是通过改变铜离子的化学电位使槽液中的锡离子发生化学置换反应,其实质是电化学反应,被还原的锡金属沉积在基板铜的表面上形成锡镀层,且其浸镀层上吸附的金属络合物对锡离子还原为金属锡起催化作用,以使锡离子继续还原成锡,确保化学沉锡镀层之厚度。 主要是提高线路的耐磨性,减低接触电阻,防止铜氧化,提高连接的可靠性,即在基板表面导体上沉积很薄的金属银层,化学镀银槽及后续二级逆流漂洗槽排放出的清洗废水进入废水处理系统的漂洗废水收集池。 本项目采用无氰镀银工艺,镀液由银盐、还原剂两种溶液组成,银盐(化学沉银药水A)主要由硝酸银组成,还原剂(化学沉银药水B)主要为酒石酸钾钠,根据化学电位差之原理,因银与铜之间的电位差距,使得铜与银离子间进行自发性的置换反应,使得铜表面浸上一层薄银。 |
无 | 是否属于重大变动:|
环保设施或环保措施
设置总处理能力为6600m3/d的生产废水处理系统(含总处理产水能力规模为3600m3/d的中水回用系统);共设置32套袋式除尘器排气筒(共4处排气筒)、1套水喷淋除尘、12套预处理(碱喷淋+除雾)+UV+蜂窝活性炭吸附装置(全厂配套1套活性炭离线脱附催化燃烧再生系统)、35套酸、碱废气喷淋装置、2处导热油炉排气筒、1处备用发电机排气筒、1处喷淋+****处理站臭气,1套脱氨废水处理装置;1个280m2的一般工业固废仓库,位于环保站1层;1个800m2的危废仓库,位于环保站1层;1个20m3含锡废液储罐1个20m3炸缸废液储罐1个20m3酸性蚀刻废液储罐1个20m3碱性蚀刻废液储罐;项目厂区内设置总容积4161m3事故应急池。其中环保站设置容积3561m3事故应急池;厂区东面设置2个单个容积为300m3的事故应急池。 | 实际建设情况:二期建设13套袋式除尘器(共1处排气筒)、5套预处理(碱喷淋+除雾)+UV+蜂窝活性炭吸附装置(全厂配套1套活性炭离线脱附催化燃烧再生系统)、17套酸、碱废气喷淋装置、1处导热油炉排气筒;环保站地下设置一个容积为3561m3事故应急池和一个71m3的含镍废水应急池。 |
设置总处理能力为6900m3/d的生产废水处理系统(含总处理能力规模为3200m3/d的中水回用系统)。废水处理站臭气处理工艺变动,工艺由“水喷淋+活性炭”变更为“水喷淋+UV”,污水站臭气处理设施变成2套;二期的钻孔机、成型机、钻嘴研磨机、钻孔机、PP开料系统、裁磨线、回流拆解线产生的粉尘分别经7套袋式除尘器处理后合并1条排气筒高空排放(DA051);因未建设酸性蚀刻液回收系统和碱性蚀刻液回收系统,对应排气筒和废气治理设施亦未建;一楼压合车间硫酸雾经**1套碱喷淋装置经排气筒高空排放(DA055) | 是否属于重大变动:|
其他
/ | 实际建设情况:二期工程增加1条OSP线,为中间生产工序,不增加最终产品产能。 |
根据生产需要,增加1条OSP线,为中间生产工序,不增加最终产品产能。 | 是否属于重大变动:|
3、污染物排放量
0 | 86.5392 | 0 | 0 | 0 | 86.539 | 86.539 | |
0 | 20.7694 | 33.4 | 0 | 0 | 20.769 | 20.769 | |
0 | 0.418 | 1.67 | 0 | 0 | 0.418 | 0.418 | |
0 | 0 | 0 | 0 | 0 | 0 | 0 | |
0 | 0 | 0 | 0 | 0 | 0 | 0 | |
0 | 0 | 0 | 0 | 0 | 0 | 0 | / |
0.017 | 0.0232 | 1.166 | 0 | 0 | 0.04 | 0.023 | / |
0.642 | 0.1162 | 5.784 | 0 | 0 | 0.758 | 0.116 | / |
0 | 0 | 0 | 0 | 0 | 0 | 0 | / |
13.0675 | 6.4541 | 29.719 | 0 | 0 | 19.522 | 6.454 | / |
4、环境保护设施落实情况
表1 水污染治理设施
自建污水处理设施 | 外排生产废水中甲醛、色度执行**省《水污染物排放限值》(DB44/26-2001)第二时段一级标准,其他污染物执行**省《电镀水污染物排放标准》(DB44/1597-2015)表2“珠三角”排放限值、《地表水环境质量标准》(GB3838-2002)IV类标准以及《电子工业水污染物排放标准》(GB39731-2020)表1印制电路板直接排放限值三者较严值。 | 已建成 | 正常 | ||
化粪池 | **省《水污染物排放限值》(DB4426-2001)第二时段三级标****处理厂进水标准较严值 | 已建设 | 正常 |
表2 大气污染治理设施
碱液喷淋净化塔 | 《大气污染物排放限值》(DB44/27-2001)中第二时段二级标准 | 已建设。镭射钻机产生的粉尘通过收集后经碱液喷淋净化塔处理后引至高空排放(DA019) | 正常 | ||
袋式除尘器 | 执行**省地方标准《大气污染物排放限值》(DB44/27-2001)中第二时段二级标准 | 已建设。钻孔机、成型机、钻嘴研磨机、钻孔机、PP开料系统、裁磨线、回流拆解线产生的粉尘通过收集后经7套袋式除尘器处理后合并引至高空排放(DA051) | 正常 | ||
碱液喷淋净化塔、次氯酸钠+碱液喷淋净化塔 | 硫酸雾、氯化氢、氰化氢、氮氧化物执行国家标准《电镀污染物排放标准》(GB21900-2008)表5**企业大气污染物排放限值;甲醛执行**省地方标准《大气污染物排放限值》(DB44/27-2001)中第二时段二级标准 | 酸雾主要来源于:硫酸雾、氯化氢、氰化氢、氮氧化物、甲醛。硫酸雾主要来自Desmear DMSE、前处理工序、棕化、DES线和化学品储罐、DVCP、清洗线、显影等工序和环节;氯化氢主要来自前处理工序、棕化、DES线和化学品储罐等工序和环节;氮氧化物;氰化氢主要来自沉金线工序;甲醛主要来自沉铜工序。 建设单位在主厂房设置了车间抽排风装置,并将车间的酸性废气引至楼顶的废气处理设施。本次验收内容建设,此类废气采用17套碱液喷淋净化塔(排气筒:DA008、DA035、DA036、DA037、DA038、DA039、DA040、DA041、DA042、DA043、DA044、DA045、DA015、DA016、DA017、DA019、DA055)和1套次氯酸钠+碱液喷淋净化塔装置(排气筒:DA018)进行处理后通过排气筒高空排放。 | 正常 | ||
碱液喷淋净化塔 | VOCs执行**省地方标准《印刷行业挥发性有机化合物排放标准》(DB44/815-2010)表2排气筒VOCs排放限值凹版印刷、丝网印刷、平板印刷(以金属、陶瓷、玻璃为承印物的平板印刷)Ⅱ时段排放限值 | VOCs主要来自涂布线、烤炉、三级连印、丝印、洗网、活性炭脱附等工序。 涂布线、烤炉、三级连印、丝印、洗网等产生有机废气工序所在房间均设置车间抽排风装置,车间的排风通过管道分别引至5套预处理(碱喷淋+除雾)+UV+蜂窝活性炭吸附装置(配套活性炭离线脱附催化燃烧再生系统)废气处理设施处理后高空排放(排气筒:DA046、DA047、DA048、DA049、DA050) | 正常 | ||
水喷淋+除雾+活性炭吸附 | VOCs执行**省地方标准《印刷行业挥发性有机化合物排放标准》(DB44/815-2010)表2排气筒VOCs排放限值凹版印刷、丝网印刷、平板印刷(以金属、陶瓷、玻璃为承印物的平板印刷)Ⅱ时段排放限值 | 活性炭离线脱附催化燃烧再生装置产生有机废气经水喷淋+除雾+活性炭吸附废气处理设施处理后高空排放(排气筒:DA033)。 | 正常 | ||
2套喷淋塔+UV光解废气处理设施 | 臭气浓度、氨、硫化氢执行国家标准《恶臭污染物排放标准》(GB14554-93)表2恶臭污染物排放标准值。 | 已建设。****处理站产生的臭气浓度、氨、硫化氢收集后分别引至2套喷淋塔+UV光解废气处理设施后高空排放(排气筒:Q1污水处理废气排放口、Q2污水处理废气排放口)。 | 正常 | ||
2套静电除油器 | 油烟参照执行国家标准《饮食业油烟排放标准》(GB18483-2001)表2最高允许排放浓度限值 | 厨房油烟收集后分别引至2套静电除油器处理后高空排放(Q3厨房油烟排放口、Q4厨房油烟排放口)。 | 正常 |
表3 噪声治理设施
减噪措施 | 噪声厂界北面、东面执行《声环境质量标准》(GB3096-2008)中4a类标准,其余厂界执行《声环境质量标准》(GB3096-2008)中3类标准。 | (1)合理布局,重视总平面布置 合理布置高噪声设备的位置,利用距离和建筑物来阻隔声波的传播,减少对周围环境的影响。 (2)防治措施 ①对于运行时由振动产生噪声的设备,对设备基础进行减振,可有效降低噪声级10~ 15 分贝。 ②对风机安装消声装置,对设备底座设置减振装置,做好运行维护。 (3)加强管理建立设备定期维护、保养的管理制度,以防止设备故障形成的非生产噪声,同时确保环保措施发挥最有效的功能;加强职工环保意识教育,提倡文明生产,防止人为噪声;强化行车管理制度,严禁鸣号,低速行驶,最大限度减少流动噪声源。 | 正常 |
表4 地下水污染治理设施
表5 固废治理设施
严格落实固体废物分类处理处置要求。蚀刻废液、废活性炭、废电路板等危险废物,送有资质的单位处理处置。边角料、废包装材料等一般固体废物交由回收企业综合利用。生活垃圾交由环卫部门处理。 | 已落实固体废物分类处理处置要求。危险废物交由有资质单位处理处置。一般固体废物交由回收企业综合利用。生活垃圾交由环卫部门处理。 |
表6 生态保护设施
表7 风险设施
进一步完善并严格落实厂区内外的环境风险防范措施和应急预 案,建立健全环境事故应急体系。加强污染防治设施的管理和维护,设置足够容积的废水事故应急池,切实防范环境污染事故发生,保障西江水环境安全。 | 已完善并落实环境风险防范措施和应急预案,企业突发环境事件应急预案已于2024年4月9日完成备案。本公司已设置足够容积的废水事故应急池。 |
5、环境保护对策措施落实情况
依托工程
无 | 验收阶段落实情况:无 |
/ |
环保搬迁
无 | 验收阶段落实情况:无 |
/ |
区域削减
无 | 验收阶段落实情况:无 |
/ |
生态恢复、补偿或管理
无 | 验收阶段落实情况:无 |
/ |
功能置换
无 | 验收阶段落实情况:无 |
/ |
其他
本项目大气污染物二氧化硫、氮氧化物、挥发性有机化合物排放总量应分别控制在1.7吨/年、9吨/年、57吨/年以内,生产废水水污染物化学需氧量、氨氮排放总量应分别控制在33.6吨/年、1.7吨/年以内,具体总量****生态环境局核拨。 | 验收阶段落实情况:根据验收监测数据核算,二期工程建成后污染物排放满足环评批复、变动分析报告、国家排污许可证的总量要求。 |
/ |
6、工程建设对项目周边环境的影响
/ |
/ |
/ |
/ |
/ |
/ |
7、验收结论
1 | 未按环境影响报告书(表)及其审批部门审批决定要求建设或落实环境保护设施,或者环境保护设施未能与主体工程同时投产使用 |
2 | 污染物排放不符合国家和地方相关标准、环境影响报告书(表)及其审批部门审批决定或者主要污染物总量指标控制要求 |
3 | 环境影响报告书(表)经批准后,该建设项目的性质、规模、地点、采用的生产工艺或者防治污染、防止生态破坏的措施发生重大变动,建设单位未重新报批环境影响报告书(表)或环境影响报告书(表)未经批准 |
4 | 建设过程中造成重大环境污染未治理完成,或者造成重大生态破坏未恢复 |
5 | 纳入排污许可管理的建设项目,无证排污或不按证排污 |
6 | 分期建设、分期投入生产或者使用的建设项目,其环境保护设施防治环境污染和生态破坏的能力不能满足主体工程需要 |
7 | 建设单位因该建设项目违反国家和地方环境保护法律法规受到处罚,被责令改正,尚未改正完成 |
8 | 验收报告的基础资料数据明显不实,内容存在重大缺项、遗漏,或者验收结论不明确、不合理 |
9 | 其他环境保护法律法规规章等规定不得通过环境保护验收 |
不存在上述情况 | |
验收结论 | 合格 |
招标导航更多>>
工程建筑
交通运输
环保绿化
医疗卫生
仪器仪表
水利水电
能源化工
弱电安防
办公文教
通讯电子
机械设备
农林牧渔
市政基建
政府部门
换一批
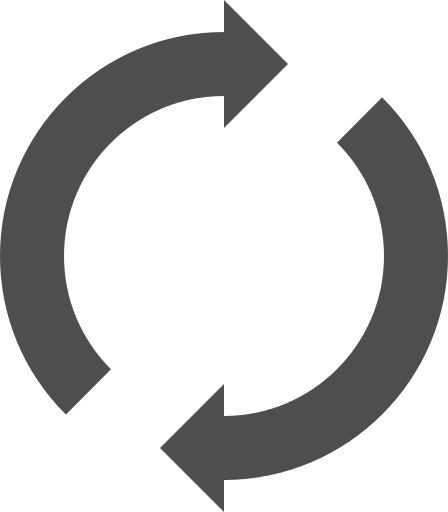