10kt/a海绵钛生产线升级改造创新项目
1、建设项目基本信息
企业基本信息
**** | 建设单位代码类型:|
****2300MA6P5G837X | 建设单位法人:陈建立 |
张玉琼 | 建设单位所在行政区划:**省**禄** |
**省**州****工业园 |
建设项目基本信息
10kt/a海绵钛生产线升级改造创新项目 | 项目代码:**** |
建设性质: | |
2021版本:064-常用有色金属冶炼;贵金属冶炼;稀有稀土金属冶炼;有色金属合金制造 | 行业类别(国民经济代码):C321-C321-常用有色金属冶炼 |
建设地点: | **省**禄** ****工业园****现有生产厂区内 |
经度:102.30134 纬度: 25.08702 | ****机关:****生态环境厅 |
环评批复时间: | 2023-03-21 |
云环审〔2023〕1-7号 | 本工程排污许可证编号:****2300MA6P5G837X001P |
2023-07-01 | 项目实际总投资(万元):44153.47 |
1724 | 运营单位名称:**** |
****2300MA6P5G837X | 验收监测(调查)报告编制机构名称:**硕利****公司 |
****2300MA6N1M0X4L | 验收监测单位:******公司 |
****0100MA6KW1FH8F | 竣工时间:2023-12-01 |
调试结束时间: | |
2024-06-17 | 验收报告公开结束时间:2024-07-12 |
验收报告公开载体: | https://www.****.com/gs/detail/2?id=40617rExvA |
2、工程变动信息
项目性质
改建 | 实际建设情况:改建 |
(一)项目主体工程发生变动 1、环评报告中,本次技改对2#氯化炉进行技术改造,改造后2#氯化炉粗四氯化钛生产能力达到170t/d,两台氯化炉可同时生产(检修时间为约50天),增加氯化熔盐渣及收尘渣水淬工序。项目实际建设情况:本次技改对2#氯化炉进行技术改造,改造后2#氯化炉粗四氯化钛生产能力达到170t/d,两台氯化炉可同时生产(检修时间为约50天),项目未建设水淬工序,氯化熔盐渣及收尘渣依托厂区熔盐氯化综合示范性项目水淬工序进行水淬。项目变动情况:项目未建设水淬工序,项目运营期产生的氯化熔盐渣及收尘渣依托厂区熔盐氯化综合示范性项目水淬工序进行水淬。项目变动原因:厂区熔盐氯化综合示范性项目已建设完成水淬工序,用于氯化熔盐渣及收尘渣水淬,****公司发展规划,项目运营期产生的氯化熔盐渣及收尘渣依托厂区熔盐氯化综合示范性项目水淬工序进行处理,本项目不再建设水淬工序,厂区熔盐氯化综合示范性项目水淬工序满足本项目氯化熔盐渣及收尘渣处理需求。 2、环评报告中,本次技改在现有精制车间内增加一套初级蒸馏装置(含初级蒸馏釜、初级蒸馏塔、空气冷却器等)和一套一级精馏塔(含一级精馏蒸馏釜、一级精馏塔、空气冷却器等),使精四氯化钛处理能力达到8万t/a。精制除矾工艺采用新型除钒剂,取消低价钛制备系统和钒渣水解工艺。项目实际建设情况:本次技改在现有精制车间内增加二套初级蒸馏装置(含初级蒸馏釜、初级蒸馏塔、空气冷却器等)、一套一级精馏塔(含一级精馏蒸馏釜、一级精馏塔、空气冷却器等)、一套二级精馏塔(含二级精馏蒸馏釜、二级精馏塔、空气冷却器等),使精四氯化钛处理能力达到8万t/a。精制除矾工艺采用新型除钒剂,取消低价钛制备系统和钒渣水解工艺。项目变动情况:初级蒸馏装置数量由一套变更为二套,新增一套二级精馏塔(含二级精馏蒸馏釜、二级精馏塔、空气冷却器等)。项目变动原因:为了满足项目生产需求,项目实际增加一套初级蒸馏装置和一套二级精馏塔,其余安装设备满足项目生产需求。 3、环评报告中,****处理厂房(24×12m,与现有厂房间隔6m,并连成一个车间使用),厂房内配置一台10t双梁桥式起重机。项目实际建设情况:****处理厂房(36×15m,与现有厂房间隔6m,并连成一个车间使用),厂房内配置一台10t双梁桥式起重机。项目变动情况:渣处理厂房占地面积增加252m2。项目变动原因:为了满足项目运营期产生的氯化水淬渣、还原蒸馏渣****公司后期其他项目固废处理需求,****处理厂房占地面积增加252m2。 (二)储运工程发生变动 1、环评报告中,依托现有还蒸车间四氯化钛储罐3个(容积均为100m3)、厂区盐酸储罐区盐酸储罐10个(容积均为60m3),30%氢氧化钠储罐2个(容积均为100m3),98%硫酸储罐2个(容积均为7.5m3)、93%硫酸储罐1个(容积14m3)。项目实际建设情况:依托现有还蒸车间四氯化钛储罐3个(容积均为100m3)、厂区盐酸储罐区盐酸储罐10个(容积均为100m3),30%氢氧化钠储罐2个(容积均为100m3),98%硫酸储罐2个(容积均为7.5m3)、93%硫酸储罐1个(容积14m3)。项目变动情况:依托现有的盐酸储罐总容积增加400m3。项目变动原因:由于厂区原有60m3盐酸储罐安装较早,使用时间较长,罐体腐蚀,因此公司将10个容积均为60m3的盐酸储罐更换为10个容积均为100m3的盐酸储罐。盐酸储罐更换后可满足本项目副产品盐酸储存需求。 (三)环保工程 1、环评报告中,项目在厂区现有基础上进行改建,不新增用地,项目建设不新增厂区初期雨水量,厂区现有初期雨收集池2座(容积分别为4000m3、1600m3)。初期雨水用管道重力排至初期雨水收集池。初期雨水经收集、暂存后,****处理站处理后回用于生产。项目实际建设情况:项目在厂区现有基础上进行改建,不新增用地,项目建设不新增厂区初期雨水量,厂区现有初雨收集池2座(容积分别为4000m3、3200m3)。初期雨水用管道重力排至初期雨水收集池。初期雨水经收集、暂存后,****处理站处理后回用于生产。项目变动情况:项目实际依托原有初期雨水收集池总容积增加1600m3。项目变动原因:由于厂区原有1600m3初期雨水收集池已作为废水收集池使用,因此厂区已重**设1座容积为3200m3的初期雨收集池代替原有1600m3初期雨水收集池收集厂区初期雨水。 2、环评报告中,厂区北侧初期雨水排入****处理站处理,海绵钛****处理站处理规模50m3/h、1200m3/d;厂区南侧初期雨水排入厂区3万吨海绵钛****处理站处理,处理规模为1000m3/d。项目实际建设情况:厂区北侧初期雨水排入****处理站处理,海绵钛****处理站处理规模50m3/h、1200m3/d;厂区南侧初期雨水排入厂区3万吨海绵钛****处理站处理,总处理规模为768m3/d(低含盐废水处理系统处理规模360m3/d,高含盐废水处理系统处理规模408m3/d)。项目变动情况:项目依托厂区3万吨海绵钛****处理站处理规模减少232m3/d。项目变动原因:厂区3万吨海绵钛项目实际分两期建设,一期项目含盐废水产生量减小,****处理站处理规模进行调整。 3、环评报告中,海绵钛厂区现已建成2****处理站,(处理规模均为10m3/h),均采用A-O工艺,处理后的水用于厂区绿化和道路清扫,不外排,本项目建设不新增工作人员不新增厂区生活污水量。项目实际建设情况:海绵钛厂区现已建成2****处理站,(处理规模均为10m3/h),均采用A-O工艺,已建成4个化粪池,总容积30m3,生活污水经现有****园区污水管网,最终****处理厂处理,本项目建设不新增工作人员不新增厂区生活污水量。厂区现有2****处理站作为备用废水处理设施,****处理厂设备故障或检修期间,项目生活污水进入2****处理站处理达标后回用于厂区绿化及道路浇洒。项目变动情况:职工生活废水经化粪池****园区污水处理厂处理。厂区现已建成的2****处理站作为备用废水处理设施。项目变动原因:****管理委员会的要求,职****园区污水处理厂处理。因此,厂区职工生活污水经化粪****园区污水处理厂处理。 4、环评报告中,本次改造后利旧现有闲置2套旋风除尘器及2根20m高排气筒)。 包装工段设置1套旋风除尘器及1根20m高排气筒,粉尘经处理后排放。在现有破碎、包装工序的收尘系统进行升级改造,现有各旋风除尘器基础上新增一级除尘,共新增5套旋风除尘器。项目实际建设情况:本次改造后利旧现有闲置2套旋风除尘器作为军工小粒度产品破碎生产线的除尘设施,并在2套旋风除尘器基础上新增2套一级旋风除尘器,2根20m高排气筒合并成1根20m高排气筒排放。在现有破碎、包装工段3套旋风除尘器的基础上新增3套一级旋风除尘器,3根20m高排气筒合并成1根20m高排气筒排放。破碎包装车间共新增5套旋风除尘器。项目变动情况:军工小粒度产品破碎废气2根排气筒合并为1根排气筒;破碎、包装废气3根排气筒合并为1根排气筒。项目变动原因:由于军工小粒度产品破碎生产线2根排气筒排放的污染物相同,破碎、包装工段3根排气筒排放的污染物相同,为了方便管理,项目将军工小粒度产品破碎废气2根排气筒合并为1根排气筒;将破碎、包装废气3根排气筒合并为1根排气筒。 4、环评报告中,废膜由厂家回收处理;废机油依托****公司厂区现有42m2废机油暂存间暂存后,委托有资质单位处置;生活垃圾委托地方环卫部门清运。项目实际建设情况:废膜由厂家回收处理;项目**1间占地面积为54m2的危险废物暂存间,废机油经油桶收集后暂存于危险废物暂存间,委托****清运处置;生活垃圾经垃圾箱收集后委托环卫部门清运处置。项目变动情况:废机油由****厂区**的54m2危险废物暂存间暂存后委托**广莱再生**清运处置,不再依托****公司废机油暂存间暂存。项目变动原因:****公司废机油及其他危险废物储存和管理,****厂区**1间占地面积为54m2的危****公司生产过程产生的危险废物,因此本项目产生的废机油在该暂存间内暂存后委托**广莱再生**清运处置,不再依托****公司废机油暂存间暂存,**的危险废物暂存间满足本项目废机油暂存需求。 5、环评报告中,生产废渣依托****公司渣场堆存,****公司渣场位于厂区西南面270m处,占地约131亩,设计有效库容81.94万m3;渣场于2009年12月开工建设,于2011年底竣工,渣场建设有拦渣坝、拦污坝、防渗系统、截洪沟、地下水收集盲沟、渗滤液收集盲沟、渗滤液回喷系统等。目前该渣场正在扩容扩容后渣场总坝高为73.5m,全库容193.77万m3。项目实际建设情况:渣场由****经营管理,本项目产****公司渣场进行堆存,渣场位于厂区西南面270m处,占地约131亩,设计有效库容94.34万m3;渣场于2009年12月开工建设,于2011年底竣工,渣场建设有拦渣坝、拦污坝、防渗系统、截洪沟、地下水收集盲沟、渗滤液收集盲沟、渗滤液回喷系统等。本次渣场扩容主要对2号库进行扩容,2号库区扩容从1905.0m标高开始在周边取土扩大容积,在原设计堆高1915.0m基础上加高堆坝至1935.0m,增加有效库容 126.71万m3。新增征地面积126亩,****填埋场总坝高为69m,总容积237.14万m3(1号堆渣区+2号堆渣区),增加服务年限约7.4年。项目变动情况:项目依托渣场经营管理单位变更,总库容增加43.97万m3。项目变动原因:为了方便渣场管理,渣场经营管理单位由****公司变更为****;****填埋场内2号库区经重新设计后,实际建设库容增大,满足本项目运营期产生的废渣堆存要求。 6、环评报告中,本项目升级改造后将**一座2200m3事故池。项目实际建设情况:项目实际依托厂区现有一座容积为3100m3的闲置空池作为事故应急池,收集事故状态下产生的废水。环评提出的2200m3事故池不再建设。项目变动情况:本项目依托厂区现有一座容积为3100m3的闲置空池作为事故应急池,未建设2200m3事故池。项目变动原因:由于场地限制及基于成本考虑,项目实际采用厂区熔盐氯化综合示范性项目建设的一座容积为3100m3的闲置空池(该池子原为盐水中转池,目前已不再使用)作为本项目事故应急池,不再建设2200m3事故池。该闲置池子已按照重点防渗要求进行防渗处理,容积相比环评阶段增加900m3,满足事故状态下废水收集需求。 | 是否属于重大变动:|
规模
项目生产海绵钛2万t/a,其中军工小颗粒海绵钛4000t/a,商品海绵钛15000t/a,等外钛988.883t/a。 | 实际建设情况:项目生产海绵钛2万t/a,其中军工小颗粒海绵钛4000t/a,商品海绵钛15000t/a,等外钛988.883t/a。 |
无 | 是否属于重大变动:|
生产工艺
本项目主要在厂区现有1万吨/年海绵钛生产线基础上进行改造,项目改造前后主体生产工艺流程不变(改造后主要生产装置规模发生变化)。项目主体生产工艺主要由氯化工序(粗四氯化钛生产)、四氯化钛精制工序、海绵钛生产工序(还蒸、破碎等工段)、镁电解和精炼工序组成,另外还包括尾气处理等。 项目主体工艺为高钛渣、氯化钠与煅后焦在氯化炉中与氯气发生反应生成粗四氯化钛,粗四氯化钛在蒸馏塔中通过蒸馏和精馏得到精四氯化钛,精四氯化钛在反应炉中与镁发生还原反应生成海绵钛和氯化镁,冷却后得到海绵钛坨,海绵钛坨经剪切、破碎、分级加工后成为成品。氯化镁进入电解车间电解成氯气和金属镁,氯气回用于氯化工段、金属镁回用于还蒸工段。 1、氯化工艺 本项目氯化工艺采用熔盐氯化技术,主要包括配料、氯化、收尘、冷凝、沉降分离等过程。 (1)配料 高钛渣、氯化钠和石油焦三种原料经各自的料仓、电动插板阀、皮带计量秤、三通阀进入埋刮板运输机混合输送到炉前料仓。三种物料的配比为高钛渣:氯化钠:煅后焦=100:21.4:18.7。炉前料仓中混合好的炉料经螺旋加料机连续不断地加入熔盐氯化炉。各运转设备采取密闭、低速度运行,配料系统依托现有两套布袋除尘器收集配料过程产生的粉尘。 补充氯和镁电解的返回氯气通过氯气管道连续不断地加进熔盐氯化炉。 (2)氯化 氯化是在700~800℃熔盐中通入氯气,在有炭存在的条件下,使炉料中的TiO2和Ti2O3等钛氧化物和氯气发生氯化反应,反应如下: TiO2+C+2Cl2=TiCl4+CO2+Q1 2Ti2O3+3C+8Cl2=4TiCl4+3CO2+Q2 伴随着TiO2和 Ti2O3等钛氧化物被氯化,原料中的 Al2O3、MgO、CaO、FeO、MnO、SiO2等杂质也将被氯化并生成相应的氯化物混入四氯化钛蒸汽中,同时产生大量的化学反应热,从熔盐氯化炉出来的炉气除了从熔盐氯化炉出来的炉气除了四氯化钛外,还会携带一些小颗粒的固体粉尘,这种炉气其实是四氯化钛蒸汽和各种氯化物蒸汽以及粉尘组成的气体混合物,这些固体粉尘在冷凝成粗四氯化钛产品前设收尘器予以分离。 氯化工段现有2套氯化炉生产线,每条生产线的粗四氯化钛生产能力为130t/d,一开一备,根据现有氯化炉使用情况,现有氯化工序一台氯化炉经常处于闲置,仅在另一套氯化炉检修期间才进行开启。本次技术改造充分利用现有设备基础上进行优化改造,对2#氯化炉进行改造,炉膛底部直径由1500mm增加到1840mm,氯化炉高度有11470mm增加到11840mm,使2#氯化炉粗四氯化钛产能达到170t/d,改造后2套氯化炉能够同时运行合计产能为300t/d。正常情况两台氯化炉同时运行,两台氯化炉不同时检修,当一条氯化生产线检修期间另一条生产线正常运行。单条线设计年检修时间为50天。 (3)收尘 从熔盐氯化炉出来的炉气温度高达450~550℃,不仅含有各种杂质氯化物,如Cl2、HCl、FeCl2、FeCl3、MgCl2、AlCl3、MnCl2,还有一定数量的固体粉尘,设置收尘器收尘。熔盐氯化炉出来的炉气进入收尘器,炉气温度下降,固体杂质和一些高熔点氯化物将冷凝固化,固体杂质及固体冷凝物沉降而与气体分离。 每座氯化炉设2台收尘器,交替使用。 (4)冷凝系统 收尘器出口处气体混合物的温度降至350~400℃,再进入喷淋式淋洗塔,喷淋式淋洗塔内利用冷却的四氯化钛直接喷淋混合气体,使混合气体的温度降至140~150℃左右,大量的高沸点杂质成分冷凝分离,得到的比较纯净的混合气体送入冷凝塔。 冷凝塔冷凝的目的使有价成分四氯化钛从比较纯净的混合气体中冷凝为液态,从而与CO2、CO、Cl2、HCl、O2、N2等气体杂质分离,产出粗四氯化钛。 冷凝分两段,一段水冷是通过循环泵将液态四氯化钛打入套管冷却器,与循环水进行间接热交换,然后从冷凝塔上的喷嘴喷出,与气态混合物接触,大部分气体四氯化钛被冷凝为液体收集下来。二段深度冷凝(采用-25℃的冷冻盐水作为冷凝介质),通过套管冷却器的间接热交换,使循环喷淋的四氯化钛温度更低,当低温四氯化钛在冷凝塔中与气体四氯化钛接触后,一段未被冷凝的气体四氯化钛冷凝成液体,从而收集下来。二段冷凝过程中上部排出不凝尾气进入尾气洗涤处理系统处理。 (5)沉降分离 冷凝系统四氯化钛冷凝成液体再经浓密搅拌后沉降分离,清液作为粗四氯化钛送入粗四氯化钛储槽;其过程中产生的沉降泥浆返回氯化炉回收四氯化钛。 (6)渣水淬 由于氯化渣(熔盐渣及氯化渣)中含盐量高,本项目技改后对氯化工序排出的熔盐渣及收尘渣进行水淬。水淬粗盐水经NaOH中和后送至隔膜压滤机压滤,所得中和****处理厂房,压滤液送至****公司MVR盐水处理车间,委托其生产出产品固体盐可用于****公司高盐废水处理装置生产氯气,蒸发余液返回水淬渣系统使用。 2、四氯化钛精制工艺 本项目现有四氯化钛精制流程设施包括一级蒸馏除钒和两级精馏。蒸馏除钒是在蒸馏釜中实现的,在蒸馏釜中除钒剂和粗四氯化钛中的三氯氧钒在蒸馏釜中反应,生成不溶于四氯化钛的二氯氧钒沉淀。 本次技改除矾工艺采用新型除钒剂除矾,对现有工艺流程进行优化,取消低价钛制备系统和钒渣水解工艺,精制车间的生产辅料取消铝粉和氯气,增加新型除钒剂消耗罐。现有精制车间内现有生产系统新增一套一级蒸馏除钒和一套一级精馏工序,与原有精制流程并联,使精四氯化钛产能增加至8万t/a(主要精馏项目氯化工序生产的粗四氯化钛)。 蒸馏除矾:项目氯化工段生产的粗四氯化钛自高位槽(消耗罐)经管道连续、均匀、自流进入蒸馏釜,除钒剂(类似矿物油)自消耗罐通过计量泵进入蒸馏釜,除钒剂与粗四氯化钛在蒸馏釜内混合后,加热至有机物碳化温度,有机物逐渐裂解为高度分散、高活性的微细碳粒,这种新形态的微细碳粒可选择性吸附或还原VOCl3,使其以固态形式沉淀。反应如下: 2VOCl3+C=VOCl2+CCl4 脱除钒的四氯化钛和少量未反应的含钒四氯化钛,由于被加热而成为气态沿着蒸馏塔上升继续反应,同时也与塔顶流下来的液体四氯化钛进行热交换,使得少量高沸点杂质和反应釜内生成的VOCl2及部分四氯化钛倒流进入蒸馏釜,从而使得VOCl2和高沸点杂质被有效分离而除去。使得四氯化钛以气态的形式通过塔顶,并进入空气冷却器进行冷却,再进入下一道精馏工序。而高沸点杂质以及VOCl2沉淀物在釜底排出,达到除钒和除高沸点杂质的目的。 釜底排出钒泥进入沉降槽沉降分离,沉降时间为24h,间断作业,共设沉降槽4个,交替使用。沉降结束放出上清液送四氯化钛沉降槽,剩下的底流,从沉降槽底部排出并加入少量石灰,送蒸发炉以分离四氯化钛和VOCl2等固体杂质。蒸发四氯化钛冷却后送入四氯化钛沉降槽,沉降的上清液返回粗四氯化钛储罐,底流返回淋洗循环槽。 精馏:除钒合格的中间产物后续还要除低沸点杂质,才能产出合格的精四氯化钛产品。精馏主要是为了除去四氯化硅、空气、氯气等低沸点杂质。 精馏采用2级精馏在釜和塔的温度控制上,精馏的目的是使低沸点杂质从精馏塔塔顶除去,该塔塔顶温度低于四氯化钛的沸点,以便使四氯化钛在塔内冷凝并回流到塔底送入精四氯化钛收集罐。低沸点的杂质以气态形式从塔顶进入空气冷却器,冷凝后进入低沸点物收集罐,低沸点物主要成分是四氯化钛(>99.5)含少量的四氯化硅(含约0.01-0.02%的四氯化硅),外售****公司作为钛白粉生产线氧化工序原料(由于低沸点物为含少量硅的四氯化钛,****公司钛白粉生产线氧化工序,四氯化钛中的四氯化硅高温下与氧气反应生成二氧化硅,二氧化硅对产品钛白粉有利,有利于增加钛白粉的耐候性,且钛白粉产品对硅含量指标没有的要求)。未被冷凝的气体送尾气洗涤处理系统。精馏过程高沸点杂质留在蒸馏釜底部周期地排出,与除钒蒸馏釜排出的钒渣浆一起处理。 项目精制工段生产的8万吨/a精四氯化钛作为中间产品送至本项目后续海绵钛生产车间作为原料。 3、海绵钛生产工艺 (1)还原-蒸馏 镁还原法生产海绵钛是在氩气保护下利用纯镁还原精四氯化钛生成海绵钛。本项目现有设施采****研究院引进的“I型”半联合法生产工艺,故本次技术改造继续采用“I型”半联合法生产工艺,还原-蒸馏工序的主要能源为电。 本项目技术改造完成后年产海绵钛坨为20190.791t。****公司提供的实际生产数据,通过对还原、蒸馏过程的操作参数进行优化调整,还原过程时间由110h缩短为93h,蒸馏过程时间由144h缩短为133h,蒸馏冷却时间由84h缩短为70h。需还原炉台数为32台,车间内现有还原炉22台,本次技术改造新增还原炉10台。项目技改后需蒸馏炉46台,车间内现有蒸馏炉33台,渗钛炉1台,本次技术改造新增蒸馏炉13台。项目技改后需蒸馏冷却器24台,车间内现有蒸馏冷却器18台,本次技术改造新增蒸馏冷却器6台。 还原:由于钛极易和氧反应生成氧化物,因此用精镁还原精四氯化钛反应必须是在密闭容器中,在氩气保护下完成。先是对组装好的反应器检漏,合格后方可投入生产。 镁锭熔融是在镁电解车间精炼炉进行,采用电加热方式融化镁锭,熔融金属镁通过抬包车运至还蒸车间,向抬包内充入氩气使得金属镁通过还原炉顶部密闭加料管进入还原炉内。加镁完毕后,精TiCl4以预先设定好的速度通过泵入还原炉内(还原炉采用电加热炉),TiCl4与熔融态金属镁发生剧烈的还原反应,生成金属钛和MgCl2。还原反应主反应方程式如下: TiCl4 + 2Mg = Ti + 2MgCl2 副反应: 2TiCl4 + 2Mg = 2TiCl3 +MgCl2 TiCl4 + Mg = TiCl2 + MgCl2 2TiCl3 + Mg = 2TiCl + 2MgCl2 2TiCl3 + Mg = 2Ti + 3MgCl2 TiCl2 + Mg = Ti + MgCl2 反应过程中,液态的镁由于比重轻而浮在上面,露出表面的镁液与加入的四氯化钛不断反应生成固体海绵钛和氯化镁,氯化镁比重较大,就逐渐沉到还原器底部,定期定量排出,用氯化镁抬包运往镁电解车间,作为电解镁的原料。还原过程排出的工艺尾气进入尾气洗涤系统。 蒸馏:还原工段得到的海绵钛中含有大量的残余镁和氯化镁。采用真空蒸馏方法使残余的Mg、MgCl2蒸发,从而达到与海绵钛分离的目的。真空蒸馏法是根据Mg和MgCl2在温度700~1000℃下的蒸气压较高,而钛在同温度下蒸气压很低,从而利用它们在高温下蒸气压相差较大而进行分离。 将还原结束后的反应器使用行车从还原炉中吊出,通过行车吊装进蒸馏炉,蒸馏炉与冷凝炉通过连接管连接在一起,然后开始进入蒸馏工序。蒸馏炉采用电加热方式。 真空蒸馏是在0.133~53.2Pa的条件下,把反应器的温度加热到980~1020℃,使镁和氯化镁蒸发,气态的镁和氯化镁在真空抽力的作用下,沿反应器上升至冷凝器(用作冷凝用的反应器),在冷凝器中,由于温度降低,镁和氯化镁就冷凝沉积于冷凝器的器壁上。 由于真空蒸馏是在高温、高真空条件下进行的生产作业,为避免反应器在高温、压力和重力作用下产生变形破坏,工艺采取反真空措施,控制蒸馏器内外压力差,即控制蒸馏炉炉膛压力保持在5.33-13.3 KPa。 当蒸馏器内的压力达到并保持于6.65~9.31Pa,且蒸馏时间达到预定的期限时,蒸馏作业即告结束。 蒸馏结束,关闭蒸馏炉电源并停止抽真空,接着向蒸馏器中充入氩气,同时向蒸馏炉炉膛送入空气,始终控制炉膛和蒸馏器的压差小于5.33~13.33KPa。当炉膛压力达到外界压力后,拆去真空管、冷却水管和氩气管,当炉温降至900℃,就吊出蒸馏器并送到蒸馏冷却器中冷却。 当蒸馏器温度降到50℃以下,转入拆卸作业。拆卸下来带有冷凝物的反应器返回还原工序,检漏合格后用于还原生产作业;拆卸下来带有海绵钛的反应器送破碎工序顶出海绵钛砣。 (2)破碎工序 破碎工段包括海绵钛坨顶出、剪切、破碎、分级等工艺过程,由油压顶出机、油压剪切机、破碎机、筛分设备、输送设备等共同完成。 本项目现有破碎产能为10kt/a海绵钛,本项目技术改造完成后年产海绵钛2万吨(商品级15000t,军工小颗粒海绵钛4000t,等外钛988.883t),其中商品海绵钛利用现有破碎生产线改造使现有破碎生产线达到15000t/a,本项目在车间内现有等外钛破碎区域进行改造,新增一条4000t/a军工小颗粒破碎生产线。顶出机和混料包装系统继续利用现有设施可满足生产要求。 从还蒸车间运至海绵钛剪切、包装车间的含有海绵钛砣的还原器,利用油压顶出机顶出海绵钛砣,油压顶出机的顶推力为500t。海绵钛砣顶出后,还原器返回还原蒸馏使用。 剪切取出的海绵钛砣先利用风镐将表面清理剥皮,清理下来的钛块由人工进行分拣,质量好的并入商品海绵钛加工流程,质量差的送等外钛破碎流程。 清理后的海绵钛砣进行目测和质量评估,高质量的海绵钛送商品海绵钛破碎加工生产线。经破碎、筛分、磁选、手选、均和、取样、送检等工序产出合格产品。 本项目军工小颗粒产品与商品海绵钛产品主要是在破碎工段的区别,各级破碎物料粒度不同,最终产品粒度不同(军工小颗粒产品粒度要求≤12.7mm,商品海绵钛产品粒度要求≤25mm)。项目增加军工小粒度破碎线,挑选出较高质量的海绵钛进行破碎,破碎线上各级破碎机有单独的粒度要求。破碎后的产品进过检测,0级以上的作为军工小粒度产品进行外售,0级品以下的作为商品海绵钛进行销售。 边皮和顶、底部剥下来的杂质含量高的等外钛,送往等外钛加工生产线,经过破碎、筛分、手选、送检等工序产出满足粒度要求的等外钛。 破碎作业完成后,不论是军工小粒度产品、商品级海绵钛还是等外钛均要取样分析,并按批次包装,包装好的海绵钛先抽真空再充氩气,待分析结果出来后,对应贴上标签和检验报告,入库待售。破碎筛分过程设置旋风收尘器,收集产生的粉尘。 4、镁电解及镁精炼 本项目技术改造完成后年产精镁21240.08t,单台电解槽产能为3t/d。需电解槽数量为21240.076/(3×365)=19.39台。车间内现有电解槽14台(12用2备),本次技术改造将2台中转炉拆除,**2台电解槽,运行方案为14用2备。另外,在镁电解车间轴22-26轴**8台电解槽,运行方案为6用2备。同时拆除轴15到轴17区域的2台坩埚炉**1台氯化镁沉降槽,实现氯化镁中转。 (1)镁电解 还原过程中产生的氯化镁电解采用多级电解槽工艺电解。氯化镁电解生产金属镁工艺的实质,是用直流电流通过熔融电解质把Mg2+离子还原为金属镁的过程。 还原工序产出的氯化镁用氯化镁抬包运送到镁电解车间,将氯化镁排放入氯化镁中转炉中,配以一定量的氯化钠、氯化钙、氟化钙,待固体熔化后,使用通用抬包将熔融液抽出,加入到电解槽中,在电解槽中通入(50~165)kA的直流电进行电解,一般使用110kA的直流电进行电解,电解温度控制在(665±5)℃,且电解质必须保平衡,电解生成粗镁和氯气,粗镁汇集到电解槽的集镁室,定期利用预热好的真空抬包抽出送往精炼炉。氯气使用输送管道输送至氯压机室进行净化处理。 具体反应方程式如下: Mg2++2Cl-=Mg+Cl2↑ MgCl2反应率为99.96%。 镁电解车间现有电解槽14台(12用2备),本次技术改造将**10台电解槽,改造后运行方案为20用4备,单台电解槽产能为3t/d。 在电解进行过程中,随着金属镁的产出,电解质中的MgCl2的含量逐渐下降。为了保证电解正常进行,必须定期加入熔融MgCl2。同时由于出镁、出渣和电解质在高温下的挥发,电解槽中的电解质的水平下降。随着电解的进行,电解质成分在电解槽中积累,使电解的合理成分发生改变。这样会导致电解的工作情况变坏,所以必须调整电解质成分,根据电解质的分析数据添加氯化物熔体,使其电解质成分保持在合理的范围内。 随着电解过程的进行,在电解槽的底部会逐渐积累起黑色或黑褐色黏性沉淀物,这就是槽渣主要由氧化镁、铁、钛、电解槽内衬脱落物等组成的渣。形成的槽渣的主要原因是,随着加料带入了一部分氧化镁以及氯化镁水解生成物,另外还有一些电解质中的杂质和副反应产污沉降到槽底。沉积在槽底的渣,如果不定期排除,会引起电解槽发生的短路现象,造成电解质和电极的局部过热。另外由于电解槽中电解质的循环,把槽渣中的氧化镁带到阴极表面积存起来,从而影响了金属镁在阴极表面的附着,这就是所谓的“阴极迟钝”,这会使电流效率降低,因此槽渣必须经常定从电解槽中排出。 除渣时稀渣通过多功能抬包取出,放到渣分离槽进行澄清分离,分离得到的电解质用多功能抬包取出返回电解槽,多次澄清分离沉淀在渣分离槽底部的残渣,采用气动抓斗进行清理,清理出来放到渣箱冷却,冷却后用叉车送渣处理工段进一步处理后送渣场。沉积于集镁室底部的稠渣,需要人工清除,清除出来后放到渣箱冷却,再用叉车送渣处理工段进一步处理后送渣场。 本项目电解采用的是多级无隔板电解槽工艺,无隔板电解槽槽体结构紧凑,阴、阳极间的极距减小,槽电压低,且单槽产能大;阴极上析出的镁从阴极上部埋浸在电解质中的导镁槽导到集镁室中,金属镁的损失减少,使电流效率提高,电耗降低。 阳极从整体盖上插入电解室下端浸入熔融电解质中。整个电解室中电解质上部的空间是连通的,都密封在整体槽盖下。产生的阳极氯气从槽盖上部的后侧开孔排出槽外。整个电解过程中没有阴极气体。由于密封性较好,所以减少了氯气泄漏损失和热量损失,氯气浓度可提高到90%~95%。 (2)氯气处理 电解过程中,阳极上析出氯气,氯气从每台电解槽的阳极气体支管导入氯气总管。在导出的气体中,除了氯气以外还有从熔融的电解槽表面挥发的氯化物。 阳极氯气离开电解槽后,温度就显著下降。这时从高温的电解质中挥发出来的氯化物就会冷凝成粉末状细粉,称为升华物。 氯气总管把阳极氯气引入袋滤器,用于过滤阳极气体中的升华物,使阳极氯气得到净化。除尘后的氯气经氯气分配器后进入干燥洗涤塔(采用98%浓硫酸淋洗工艺)干燥,进一步去除氯气中的水分。硫酸通过泵送至干燥器顶部,喷淋净化氯气,硫酸经换热器冷却后回用。当硫酸浓度低于94%(即93%硫酸)时排出。这部分硫酸将储存于废酸贮罐,定期外售。经除尘和干燥后的氯气液环式氯气压缩机进行压缩,压缩机出口氯气压力控制在0.15~0.2MPa,送项目氯化车间氯化炉。袋滤器清灰采用氯气脉冲反吹,清出的升华物经收集后送渣场堆存。 (3)镁精炼 电解槽产生的镁称为粗镁,粗镁含有少量杂质。这些杂质的存在对镁的质量有重大的影响,对用于海绵钛生产的金属镁,这些杂质会直接影响海绵钛的质量。由于以上原因,粗镁中的杂质应该清除,以供生产海绵钛使用。为此必须对粗镁进行精炼,使杂质含量达到使用标准。镁精炼的原理是利用杂质(包括MgCl2等)和金属镁比重不同而将之除去,以提高海绵钛的产品质量。 来自电解工段的粗镁通过通用抬包加入到精炼炉中,精炼炉内液镁温度控制在(685~710)℃,在精炼过程中,使用氩气对液镁进行保护,防止液镁氧化。续精炼炉采用电阻丝加热,精炼温度稍高于镁金属熔点,低于MgCl2熔点,使得MgCl2在炉内分离出来。粗镁精炼完成后采用精镁抬包抽出精镁并通过抬包车运输至还蒸车间。连续精炼炉炉渣定期排渣,清理后送至渣场堆存。 精炼炉中的粗镁加入和精镁排出均通过抬包进行输送,抬包对接精炼炉接口瞬间,接口法兰处会有少量气体溢出。抬包和精炼炉对接完成后,粗镁加入和精镁排出过程均为密闭操作,无气体溢出。 5、尾气处理及渣处理系统 (1)尾气处理系统 ①氯化工艺尾气洗涤系统 氯化工段现有2套氯化炉生产线,1套氯化工艺废气净化系统(原设计中已按2套氯化工艺废气净化系统进行设计并建成,其中1套已安装净化设备,另1套设备安装位置预留),现状两条氯化炉生产线交替运行。本次技改完成后,现有氯化工艺废气净化系统与1#氯化炉生产线配合使用;现有氯化工艺尾气采用5段吸收,先用2段水吸收(回收盐酸)后用3段碱吸收(氢氧化钠溶液洗涤)。本次**2#氯化工艺废气净化系统,并对现有氯化尾气洗涤进行改造,本次改造后两套氯化炉氯化工艺废气洗涤处理工艺一致,尾气处理采用6级洗涤“两级水洗+三级氯化亚铁洗涤塔+一级碱洗塔+捕滴器”组合工艺处理后尾气全部通过现有80m高排气筒排放。 氯化工艺尾气主要含有CO、CO2、SO2、Cl2、HCl、TiCl4等尾气,氯化氢气体易溶于稀酸中,生成盐酸,氯化工艺尾气首先经过稀盐酸洗涤,吸收尾气中的氯化氢及四氯化钛,反应方程式为:TiCl4+2H2O=TiO2+4HCl,主要采用第二洗涤塔排出的稀盐酸进行循环洗涤,当循环槽盐酸浓度>20%时将部分吸收液排入储罐区的盐酸储槽,作为副产品。 经第一洗涤塔洗涤后的尾气进入第二个洗涤塔,塔顶用循环水喷淋,进一步吸收HCl,经循环洗涤后的稀盐酸排出,作为第一洗涤塔的洗涤液。经第二洗涤塔水洗除HCl后尾气进入第三、四、五洗涤塔(FeCl2洗涤塔),氯化炉内因操作失误出现Cl2突破床层时,尾气中就会含有氯气,塔内加入FeCl2溶液,吸收尾气中的氯气。反应方程式为:2FeCl2+Cl2=2FeCl3,塔内FeCl2溶液主要来自龙佰**钛业渣处理产生的FeCl2溶液,FeCl2洗涤塔内洗涤液一部分用于循环洗涤,并排除部分洗涤液进入废水处理,并补充新FeCl2溶液。 经FeCl2洗涤塔洗涤后的尾气再加入碱洗塔采用NaOH溶液进行再次洗涤进一步去除尾气中少量Cl2及HCl、SO2等,主要反应:NaOH+HCl=NaCl+H2O,2NaOH+Cl2= NaCl+NaClO+H2O,NaOH+SO2= Na2SO3+H2O。 碱洗塔底部设置收集池,池壁上安装浓度计,收集池碱液部分通过碱液循环泵,泵送到塔顶循环喷入,部分启动废水外排泵,至废水处理。 ②氯化卫生尾气洗涤系统 本项目氯化卫生尾气净化系统主要是收集氯化炉排盐时和更换收尘渣罐过程产生的废气,技术改造完成后,两台氯化炉错峰完成排盐和更换收尘渣罐。现有氯化卫生尾气净化设施通过错峰使用可满足使用要求,现有氯化卫生尾气主要采用两级水洗+两级碱洗,为优化洗涤效果,在一级和二级水洗洗涤塔之间增加一级吸收塔(采用水作为吸收剂)。 氯化卫生尾气主要含有Cl2、HCl、TiCl4等尾气,改造后采用5级洗涤(三级水洗+两级碱洗)组合工艺处理后尾气全部通过现有80m高排气筒排放。氯化卫生尾气在三级水洗喷淋吸收塔被水洗涤吸收尾气中的HCl、TiCl4,反应方程式为:TiCl4+2H2O=TiO2+4HCl,少部分TiCl4被氧气被氧化TiCl4+O2=TiO2+2Cl2。 当一级洗涤塔循环槽盐酸浓度达到要求时,打开喷淋吸收塔循环泵出口排液阀门将部分吸收液排入储罐区的盐酸储槽,作为副产品。而未被吸收的尾气进入碱洗喷淋吸收塔+碱洗喷淋填料吸收塔被NaOH溶液洗涤吸收尾气中的Cl2、HCl后,其中碱液吸收后产生的废碱液一部分用于循环,部分启动废水外排泵,至废水处理。 ③精制尾气洗涤系统 本项目精制尾气包括精制过程工艺尾气及卫生尾气,根据建设单位提供相关设计资料现有精制尾气洗涤系统能够满足洗涤需求。精制过程中产生的主要含TiCl4、HCl尾气,主要采用三段吸收洗涤(两级水洗+一级碱洗)工艺处理后尾气全部通过现有80m高排气筒排放。 精制尾气在两级水洗喷淋吸收塔被水洗涤吸收尾气中的HCl、TiCl4,当一级洗涤塔循环槽盐酸浓度达到要求时,打开喷淋吸收塔循环泵出口排液阀门将部分吸收液排入储罐区的盐酸储槽,作为副产品。而未被吸收的尾气进入碱洗喷淋吸收塔被NaOH溶液洗涤吸收尾气中的Cl2、HCl后,其中碱液吸收后产生的废碱液一部分用于循环,部分启动废水外排泵,至废水处理。 ④还蒸尾气洗涤系统 还蒸尾气洗涤系统主要收集洗涤还蒸车间的尾气及镁电解车间坩埚炉熔炼过程产生含尘烟气,主要采用3级洗涤(两级水洗+1级碱洗)工艺处理后尾气全部通过现有80m高排气筒排放。根据建设单位提供相关设计资料通过错峰排放氯化镁的操作,还蒸精尾气洗涤系统能够满足洗涤需求。 还原、蒸馏尾气中主要含HCl、颗粒物,镁电解车间坩埚炉熔炼废气主要含烟尘,上述废气在两级水洗喷淋吸收塔被水洗涤吸收尾气中的HCl,并除尘,当一级洗涤塔循环槽盐酸浓度达到要求时,打开喷淋吸收塔循环泵出口排液阀门将部分吸收液排入储罐区的盐酸储槽,作为副产品。而未被吸收的尾气进入碱洗喷淋吸收塔被NaOH溶液洗涤吸收尾气中的HCl后,其中碱液吸收后产生的废碱液一部分用于循环,部分启动废水外排泵,至废水处理。 | 实际建设情况:本项目主要在厂区现有1万吨/年海绵钛生产线基础上进行改造,项目改造前后主体生产工艺流程不变(改造后主要生产装置规模发生变化)。项目主体生产工艺主要由氯化工序(粗四氯化钛生产)、四氯化钛精制工序、海绵钛生产工序(还蒸、破碎等工段)、镁电解和精炼工序组成,另外还包括尾气处理等。 项目主体工艺为高钛渣、氯化钠与煅后焦在氯化炉中与氯气发生反应生成粗四氯化钛,粗四氯化钛在蒸馏塔中通过蒸馏和精馏得到精四氯化钛,精四氯化钛在反应炉中与镁发生还原反应生成海绵钛和氯化镁,冷却后得到海绵钛坨,海绵钛坨经剪切、破碎、分级加工后成为成品。氯化镁进入电解车间电解成氯气和金属镁,氯气回用于氯化工段、金属镁回用于还蒸工段。 1、氯化工艺 本项目氯化工艺采用熔盐氯化技术,主要包括配料、氯化、收尘、冷凝、沉降分离等过程。 (1)配料 高钛渣、氯化钠和石油焦三种原料经各自的料仓、电动插板阀、皮带计量秤、三通阀进入埋刮板运输机混合输送到炉前料仓。三种物料的配比为高钛渣:氯化钠:煅后焦=100:21.4:18.7。炉前料仓中混合好的炉料经螺旋加料机连续不断地加入熔盐氯化炉。各运转设备采取密闭、低速度运行,配料系统依托现有两套布袋除尘器收集配料过程产生的粉尘。 补充氯和镁电解的返回氯气通过氯气管道连续不断地加进熔盐氯化炉。 (2)氯化 氯化是在700~800℃熔盐中通入氯气,在有炭存在的条件下,使炉料中的TiO2和Ti2O3等钛氧化物和氯气发生氯化反应,反应如下: TiO2+C+2Cl2=TiCl4+CO2+Q1 2Ti2O3+3C+8Cl2=4TiCl4+3CO2+Q2 伴随着TiO2和 Ti2O3等钛氧化物被氯化,原料中的 Al2O3、MgO、CaO、FeO、MnO、SiO2等杂质也将被氯化并生成相应的氯化物混入四氯化钛蒸汽中,同时产生大量的化学反应热,从熔盐氯化炉出来的炉气除了从熔盐氯化炉出来的炉气除了四氯化钛外,还会携带一些小颗粒的固体粉尘,这种炉气其实是四氯化钛蒸汽和各种氯化物蒸汽以及粉尘组成的气体混合物,这些固体粉尘在冷凝成粗四氯化钛产品前设收尘器予以分离。 氯化工段现有2套氯化炉生产线,每条生产线的粗四氯化钛生产能力为130t/d,一开一备,根据现有氯化炉使用情况,现有氯化工序一台氯化炉经常处于闲置,仅在另一套氯化炉检修期间才进行开启。本次技术改造充分利用现有设备基础上进行优化改造,对2#氯化炉进行改造,炉膛底部直径由1500mm增加到1840mm,氯化炉高度有11470mm增加到11840mm,使2#氯化炉粗四氯化钛产能达到170t/d,改造后2套氯化炉能够同时运行合计产能为300t/d。正常情况两台氯化炉同时运行,两台氯化炉不同时检修,当一条氯化生产线检修期间另一条生产线正常运行。单条线设计年检修时间为50天。 (3)收尘 从熔盐氯化炉出来的炉气温度高达450~550℃,不仅含有各种杂质氯化物,如Cl2、HCl、FeCl2、FeCl3、MgCl2、AlCl3、MnCl2,还有一定数量的固体粉尘,设置收尘器收尘。熔盐氯化炉出来的炉气进入收尘器,炉气温度下降,固体杂质和一些高熔点氯化物将冷凝固化,固体杂质及固体冷凝物沉降而与气体分离。 每座氯化炉设2台收尘器,交替使用。 (4)冷凝系统 收尘器出口处气体混合物的温度降至350~400℃,再进入喷淋式淋洗塔,喷淋式淋洗塔内利用冷却的四氯化钛直接喷淋混合气体,使混合气体的温度降至140~150℃左右,大量的高沸点杂质成分冷凝分离,得到的比较纯净的混合气体送入冷凝塔。 冷凝塔冷凝的目的使有价成分四氯化钛从比较纯净的混合气体中冷凝为液态,从而与CO2、CO、Cl2、HCl、O2、N2等气体杂质分离,产出粗四氯化钛。 冷凝分两段,一段水冷是通过循环泵将液态四氯化钛打入套管冷却器,与循环水进行间接热交换,然后从冷凝塔上的喷嘴喷出,与气态混合物接触,大部分气体四氯化钛被冷凝为液体收集下来。二段深度冷凝(采用-25℃的冷冻盐水作为冷凝介质),通过套管冷却器的间接热交换,使循环喷淋的四氯化钛温度更低,当低温四氯化钛在冷凝塔中与气体四氯化钛接触后,一段未被冷凝的气体四氯化钛冷凝成液体,从而收集下来。二段冷凝过程中上部排出不凝尾气进入尾气洗涤处理系统处理。 (5)沉降分离 冷凝系统四氯化钛冷凝成液体再经浓密搅拌后沉降分离,清液作为粗四氯化钛送入粗四氯化钛储槽;其过程中产生的沉降泥浆返回氯化炉回收四氯化钛。 (6)渣水淬 由于氯化渣(熔盐渣及氯化渣)中含盐量高,本项目技改后对氯化工序排出的熔盐渣及收尘渣进行水淬。本项目熔****公司熔盐氯化综合示范性项目水淬工序进行处理。 水淬粗盐水经NaOH中和后送至隔膜压滤机压滤,所得中和****处理厂房,压滤液送至****公司MVR盐水处理车间,委托其生产出产品固体盐可用于****公司高盐废水处理装置生产氯气,蒸发余液返回水淬渣系统使用。 2、四氯化钛精制工艺 本项目现有四氯化钛精制流程设施包括一级蒸馏除钒和两级精馏。蒸馏除钒是在蒸馏釜中实现的,在蒸馏釜中除钒剂和粗四氯化钛中的三氯氧钒在蒸馏釜中反应,生成不溶于四氯化钛的二氯氧钒沉淀。 本次技改除矾工艺采用新型除钒剂除矾,对现有工艺流程进行优化,取消低价钛制备系统和钒渣水解工艺,精制车间的生产辅料取消铝粉和氯气,增加新型除钒剂消耗罐。现有精制车间内现有生产系统新增一套一级蒸馏除钒和一套一级精馏工序,与原有精制流程并联,使精四氯化钛产能增加至8万t/a(主要精馏项目氯化工序生产的粗四氯化钛)。 蒸馏除矾:项目氯化工段生产的粗四氯化钛自高位槽(消耗罐)经管道连续、均匀、自流进入蒸馏釜,除钒剂(类似矿物油)自消耗罐通过计量泵进入蒸馏釜,除钒剂与粗四氯化钛在蒸馏釜内混合后,加热至有机物碳化温度,有机物逐渐裂解为高度分散、高活性的微细碳粒,这种新形态的微细碳粒可选择性吸附或还原VOCl3,使其以固态形式沉淀。反应如下: 2VOCl3+C=VOCl2+CCl4 脱除钒的四氯化钛和少量未反应的含钒四氯化钛,由于被加热而成为气态沿着蒸馏塔上升继续反应,同时也与塔顶流下来的液体四氯化钛进行热交换,使得少量高沸点杂质和反应釜内生成的VOCl2及部分四氯化钛倒流进入蒸馏釜,从而使得VOCl2和高沸点杂质被有效分离而除去。使得四氯化钛以气态的形式通过塔顶,并进入空气冷却器进行冷却,再进入下一道精馏工序。而高沸点杂质以及VOCl2沉淀物在釜底排出,达到除钒和除高沸点杂质的目的。 釜底排出钒泥进入沉降槽沉降分离,沉降时间为24h,间断作业,共设沉降槽4个,交替使用。沉降结束放出上清液送四氯化钛沉降槽,剩下的底流,从沉降槽底部排出并加入少量石灰,送蒸发炉以分离四氯化钛和VOCl2等固体杂质。蒸发四氯化钛冷却后送入四氯化钛沉降槽,沉降的上清液返回粗四氯化钛储罐,底流返回淋洗循环槽。 精馏:除钒合格的中间产物后续还要除低沸点杂质,才能产出合格的精四氯化钛产品。精馏主要是为了除去四氯化硅、空气、氯气等低沸点杂质。 精馏采用2级精馏在釜和塔的温度控制上,精馏的目的是使低沸点杂质从精馏塔塔顶除去,该塔塔顶温度低于四氯化钛的沸点,以便使四氯化钛在塔内冷凝并回流到塔底送入精四氯化钛收集罐。低沸点的杂质以气态形式从塔顶进入空气冷却器,冷凝后进入低沸点物收集罐,低沸点物主要成分是四氯化钛(>99.5)含少量的四氯化硅(含约0.01-0.02%的四氯化硅),外售****公司作为钛白粉生产线氧化工序原料(由于低沸点物为含少量硅的四氯化钛,****公司钛白粉生产线氧化工序,四氯化钛中的四氯化硅高温下与氧气反应生成二氧化硅,二氧化硅对产品钛白粉有利,有利于增加钛白粉的耐候性,且钛白粉产品对硅含量指标没有的要求)。未被冷凝的气体送尾气洗涤处理系统。精馏过程高沸点杂质留在蒸馏釜底部周期地排出,与除钒蒸馏釜排出的钒渣浆一起处理。 项目精制工段生产的8万吨/a精四氯化钛作为中间产品送至本项目后续海绵钛生产车间作为原料。 3、海绵钛生产工艺 (1)还原-蒸馏 镁还原法生产海绵钛是在氩气保护下利用纯镁还原精四氯化钛生成海绵钛。本项目现有设施采****研究院引进的“I型”半联合法生产工艺,故本次技术改造继续采用“I型”半联合法生产工艺,还原-蒸馏工序的主要能源为电。 本项目技术改造完成后年产海绵钛坨为20190.791t。****公司提供的实际生产数据,通过对还原、蒸馏过程的操作参数进行优化调整,还原过程时间由110h缩短为93h,蒸馏过程时间由144h缩短为133h,蒸馏冷却时间由84h缩短为70h。需还原炉台数为32台,车间内现有还原炉22台,本次技术改造新增还原炉10台。项目技改后需蒸馏炉46台,车间内现有蒸馏炉33台,渗钛炉1台,本次技术改造新增蒸馏炉13台。项目技改后需蒸馏冷却器24台,车间内现有蒸馏冷却器18台,本次技术改造新增蒸馏冷却器6台。 还原:由于钛极易和氧反应生成氧化物,因此用精镁还原精四氯化钛反应必须是在密闭容器中,在氩气保护下完成。先是对组装好的反应器检漏,合格后方可投入生产。 镁锭熔融是在镁电解车间精炼炉进行,采用电加热方式融化镁锭,熔融金属镁通过抬包车运至还蒸车间,向抬包内充入氩气使得金属镁通过还原炉顶部密闭加料管进入还原炉内。加镁完毕后,精TiCl4以预先设定好的速度通过泵入还原炉内(还原炉采用电加热炉),TiCl4与熔融态金属镁发生剧烈的还原反应,生成金属钛和MgCl2。还原反应主反应方程式如下: TiCl4 + 2Mg = Ti + 2MgCl2 副反应: 2TiCl4 + 2Mg = 2TiCl3 +MgCl2 TiCl4 + Mg = TiCl2 + MgCl2 2TiCl3 + Mg = 2TiCl + 2MgCl2 2TiCl3 + Mg = 2Ti + 3MgCl2 TiCl2 + Mg = Ti + MgCl2 反应过程中,液态的镁由于比重轻而浮在上面,露出表面的镁液与加入的四氯化钛不断反应生成固体海绵钛和氯化镁,氯化镁比重较大,就逐渐沉到还原器底部,定期定量排出,用氯化镁抬包运往镁电解车间,作为电解镁的原料。还原过程排出的工艺尾气进入尾气洗涤系统。 蒸馏:还原工段得到的海绵钛中含有大量的残余镁和氯化镁。采用真空蒸馏方法使残余的Mg、MgCl2蒸发,从而达到与海绵钛分离的目的。真空蒸馏法是根据Mg和MgCl2在温度700~1000℃下的蒸气压较高,而钛在同温度下蒸气压很低,从而利用它们在高温下蒸气压相差较大而进行分离。 将还原结束后的反应器使用行车从还原炉中吊出,通过行车吊装进蒸馏炉,蒸馏炉与冷凝炉通过连接管连接在一起,然后开始进入蒸馏工序。蒸馏炉采用电加热方式。 真空蒸馏是在0.133~53.2Pa的条件下,把反应器的温度加热到980~1020℃,使镁和氯化镁蒸发,气态的镁和氯化镁在真空抽力的作用下,沿反应器上升至冷凝器(用作冷凝用的反应器),在冷凝器中,由于温度降低,镁和氯化镁就冷凝沉积于冷凝器的器壁上。 由于真空蒸馏是在高温、高真空条件下进行的生产作业,为避免反应器在高温、压力和重力作用下产生变形破坏,工艺采取反真空措施,控制蒸馏器内外压力差,即控制蒸馏炉炉膛压力保持在5.33-13.3 KPa。 当蒸馏器内的压力达到并保持于6.65~9.31Pa,且蒸馏时间达到预定的期限时,蒸馏作业即告结束。 蒸馏结束,关闭蒸馏炉电源并停止抽真空,接着向蒸馏器中充入氩气,同时向蒸馏炉炉膛送入空气,始终控制炉膛和蒸馏器的压差小于5.33~13.33KPa。当炉膛压力达到外界压力后,拆去真空管、冷却水管和氩气管,当炉温降至900℃,就吊出蒸馏器并送到蒸馏冷却器中冷却。 当蒸馏器温度降到50℃以下,转入拆卸作业。拆卸下来带有冷凝物的反应器返回还原工序,检漏合格后用于还原生产作业;拆卸下来带有海绵钛的反应器送破碎工序顶出海绵钛砣。 (2)破碎工序 破碎工段包括海绵钛坨顶出、剪切、破碎、分级等工艺过程,由油压顶出机、油压剪切机、破碎机、筛分设备、输送设备等共同完成。 本项目现有破碎产能为10kt/a海绵钛,本项目技术改造完成后年产海绵钛2万吨(商品级15000t,军工小颗粒海绵钛4000t,等外钛988.883t),其中商品海绵钛利用现有破碎生产线改造使现有破碎生产线达到15000t/a,本项目在车间内现有等外钛破碎区域进行改造,新增一条4000t/a军工小颗粒破碎生产线。顶出机和混料包装系统继续利用现有设施可满足生产要求。 从还蒸车间运至海绵钛剪切、包装车间的含有海绵钛砣的还原器,利用油压顶出机顶出海绵钛砣,油压顶出机的顶推力为500t。海绵钛砣顶出后,还原器返回还原蒸馏使用。 剪切取出的海绵钛砣先利用风镐将表面清理剥皮,清理下来的钛块由人工进行分拣,质量好的并入商品海绵钛加工流程,质量差的送等外钛破碎流程。 清理后的海绵钛砣进行目测和质量评估,高质量的海绵钛送商品海绵钛破碎加工生产线。经破碎、筛分、磁选、手选、均和、取样、送检等工序产出合格产品。 本项目军工小颗粒产品与商品海绵钛产品主要是在破碎工段的区别,各级破碎物料粒度不同,最终产品粒度不同(军工小颗粒产品粒度要求≤12.7mm,商品海绵钛产品粒度要求≤25mm)。项目增加军工小粒度破碎线,挑选出较高质量的海绵钛进行破碎,破碎线上各级破碎机有单独的粒度要求。破碎后的产品进过检测,0级以上的作为军工小粒度产品进行外售,0级品以下的作为商品海绵钛进行销售。 边皮和顶、底部剥下来的杂质含量高的等外钛,送往等外钛加工生产线,经过破碎、筛分、手选、送检等工序产出满足粒度要求的等外钛。 破碎作业完成后,不论是军工小粒度产品、商品级海绵钛还是等外钛均要取样分析,并按批次包装,包装好的海绵钛先抽真空再充氩气,待分析结果出来后,对应贴上标签和检验报告,入库待售。破碎筛分过程设置旋风收尘器,收集产生的粉尘。 4、镁电解及镁精炼 本项目技术改造完成后年产精镁21240.08t,单台电解槽产能为3t/d。需电解槽数量为21240.076/(3×365)=19.39台。车间内现有电解槽14台(12用2备),本次技术改造将2台中转炉拆除,**2台电解槽,运行方案为14用2备。另外,在镁电解车间轴22-26轴**8台电解槽,运行方案为6用2备。同时拆除轴15到轴17区域的2台坩埚炉**1台氯化镁沉降槽,实现氯化镁中转。 (1)镁电解 还原过程中产生的氯化镁电解采用多级电解槽工艺电解。氯化镁电解生产金属镁工艺的实质,是用直流电流通过熔融电解质把Mg2+离子还原为金属镁的过程。 还原工序产出的氯化镁用氯化镁抬包运送到镁电解车间,将氯化镁排放入氯化镁中转炉中,配以一定量的氯化钠、氯化钙、氟化钙,待固体熔化后,使用通用抬包将熔融液抽出,加入到电解槽中,在电解槽中通入(50~165)kA的直流电进行电解,一般使用110kA的直流电进行电解,电解温度控制在(665±5)℃,且电解质必须保平衡,电解生成粗镁和氯气,粗镁汇集到电解槽的集镁室,定期利用预热好的真空抬包抽出送往精炼炉。氯气使用输送管道输送至氯压机室进行净化处理。 具体反应方程式如下: Mg2++2Cl-=Mg+Cl2↑ MgCl2反应率为99.96%。 镁电解车间现有电解槽14台(12用2备),本次技术改造将**10台电解槽,改造后运行方案为20用4备,单台电解槽产能为3t/d。 在电解进行过程中,随着金属镁的产出,电解质中的MgCl2的含量逐渐下降。为了保证电解正常进行,必须定期加入熔融MgCl2。同时由于出镁、出渣和电解质在高温下的挥发,电解槽中的电解质的水平下降。随着电解的进行,电解质成分在电解槽中积累,使电解的合理成分发生改变。这样会导致电解的工作情况变坏,所以必须调整电解质成分,根据电解质的分析数据添加氯化物熔体,使其电解质成分保持在合理的范围内。 随着电解过程的进行,在电解槽的底部会逐渐积累起黑色或黑褐色黏性沉淀物,这就是槽渣主要由氧化镁、铁、钛、电解槽内衬脱落物等组成的渣。形成的槽渣的主要原因是,随着加料带入了一部分氧化镁以及氯化镁水解生成物,另外还有一些电解质中的杂质和副反应产污沉降到槽底。沉积在槽底的渣,如果不定期排除,会引起电解槽发生的短路现象,造成电解质和电极的局部过热。另外由于电解槽中电解质的循环,把槽渣中的氧化镁带到阴极表面积存起来,从而影响了金属镁在阴极表面的附着,这就是所谓的“阴极迟钝”,这会使电流效率降低,因此槽渣必须经常定从电解槽中排出。 除渣时稀渣通过多功能抬包取出,放到渣分离槽进行澄清分离,分离得到的电解质用多功能抬包取出返回电解槽,多次澄清分离沉淀在渣分离槽底部的残渣,采用气动抓斗进行清理,清理出来放到渣箱冷却,冷却后用叉车送渣处理工段进一步处理后送渣场。沉积于集镁室底部的稠渣,需要人工清除,清除出来后放到渣箱冷却,再用叉车送渣处理工段进一步处理后送渣场。 本项目电解采用的是多级无隔板电解槽工艺,无隔板电解槽槽体结构紧凑,阴、阳极间的极距减小,槽电压低,且单槽产能大;阴极上析出的镁从阴极上部埋浸在电解质中的导镁槽导到集镁室中,金属镁的损失减少,使电流效率提高,电耗降低。 阳极从整体盖上插入电解室下端浸入熔融电解质中。整个电解室中电解质上部的空间是连通的,都密封在整体槽盖下。产生的阳极氯气从槽盖上部的后侧开孔排出槽外。整个电解过程中没有阴极气体。由于密封性较好,所以减少了氯气泄漏损失和热量损失,氯气浓度可提高到90%~95%。 (2)氯气处理 电解过程中,阳极上析出氯气,氯气从每台电解槽的阳极气体支管导入氯气总管。在导出的气体中,除了氯气以外还有从熔融的电解槽表面挥发的氯化物。 阳极氯气离开电解槽后,温度就显著下降。这时从高温的电解质中挥发出来的氯化物就会冷凝成粉末状细粉,称为升华物。 氯气总管把阳极氯气引入袋滤器,用于过滤阳极气体中的升华物,使阳极氯气得到净化。除尘后的氯气经氯气分配器后进入干燥洗涤塔(采用98%浓硫酸淋洗工艺)干燥,进一步去除氯气中的水分。硫酸通过泵送至干燥器顶部,喷淋净化氯气,硫酸经换热器冷却后回用。当硫酸浓度低于94%(即93%硫酸)时排出。这部分硫酸将储存于废酸贮罐,定期外售。经除尘和干燥后的氯气液环式氯气压缩机进行压缩,压缩机出口氯气压力控制在0.15~0.2MPa,送项目氯化车间氯化炉。袋滤器清灰采用氯气脉冲反吹,清出的升华物经收集后送渣场堆存。 (3)镁精炼 电解槽产生的镁称为粗镁,粗镁含有少量杂质。这些杂质的存在对镁的质量有重大的影响,对用于海绵钛生产的金属镁,这些杂质会直接影响海绵钛的质量。由于以上原因,粗镁中的杂质应该清除,以供生产海绵钛使用。为此必须对粗镁进行精炼,使杂质含量达到使用标准。镁精炼的原理是利用杂质(包括MgCl2等)和金属镁比重不同而将之除去,以提高海绵钛的产品质量。 来自电解工段的粗镁通过通用抬包加入到精炼炉中,精炼炉内液镁温度控制在(685~710)℃,在精炼过程中,使用氩气对液镁进行保护,防止液镁氧化。续精炼炉采用电阻丝加热,精炼温度稍高于镁金属熔点,低于MgCl2熔点,使得MgCl2在炉内分离出来。粗镁精炼完成后采用精镁抬包抽出精镁并通过抬包车运输至还蒸车间。连续精炼炉炉渣定期排渣,清理后送至渣场堆存。 精炼炉中的粗镁加入和精镁排出均通过抬包进行输送,抬包对接精炼炉接口瞬间,接口法兰处会有少量气体溢出。抬包和精炼炉对接完成后,粗镁加入和精镁排出过程均为密闭操作,无气体溢出。 5、尾气处理及渣处理系统 (1)尾气处理系统 ①氯化工艺尾气洗涤系统 氯化工段现有2套氯化炉生产线,1套氯化工艺废气净化系统(原设计中已按2套氯化工艺废气净化系统进行设计并建成,其中1套已安装净化设备,另1套设备安装位置预留),现状两条氯化炉生产线交替运行。本次技改完成后,现有氯化工艺废气净化系统与1#氯化炉生产线配合使用;现有氯化工艺尾气采用5段吸收,先用2段水吸收(回收盐酸)后用3段碱吸收(氢氧化钠溶液洗涤)。本次**2#氯化工艺废气净化系统,并对现有氯化尾气洗涤进行改造,本次改造后两套氯化炉氯化工艺废气洗涤处理工艺一致,尾气处理采用6级洗涤“两级水洗+三级氯化亚铁洗涤塔+一级碱洗塔+捕滴器”组合工艺处理后尾气全部通过现有80m高排气筒排放。 氯化工艺尾气主要含有CO、CO2、SO2、Cl2、HCl、TiCl4等尾气,氯化氢气体易溶于稀酸中,生成盐酸,氯化工艺尾气首先经过稀盐酸洗涤,吸收尾气中的氯化氢及四氯化钛,反应方程式为:TiCl4+2H2O=TiO2+4HCl,主要采用第二洗涤塔排出的稀盐酸进行循环洗涤,当循环槽盐酸浓度>20%时将部分吸收液排入储罐区的盐酸储槽,作为副产品。 经第一洗涤塔洗涤后的尾气进入第二个洗涤塔,塔顶用循环水喷淋,进一步吸收HCl,经循环洗涤后的稀盐酸排出,作为第一洗涤塔的洗涤液。经第二洗涤塔水洗除HCl后尾气进入第三、四、五洗涤塔(FeCl2洗涤塔),氯化炉内因操作失误出现Cl2突破床层时,尾气中就会含有氯气,塔内加入FeCl2溶液,吸收尾气中的氯气。反应方程式为:2FeCl2+Cl2=2FeCl3,塔内FeCl2溶液主要来自龙佰**钛业渣处理产生的FeCl2溶液,FeCl2洗涤塔内洗涤液一部分用于循环洗涤,并排除部分洗涤液进入废水处理,并补充新FeCl2溶液。 经FeCl2洗涤塔洗涤后的尾气再加入碱洗塔采用NaOH溶液进行再次洗涤进一步去除尾气中少量Cl2及HCl、SO2等,主要反应:NaOH+HCl=NaCl+H2O,2NaOH+Cl2= NaCl+NaClO+H2O,NaOH+SO2= Na2SO3+H2O。 碱洗塔底部设置收集池,池壁上安装浓度计,收集池碱液部分通过碱液循环泵,泵送到塔顶循环喷入,部分启动废水外排泵,至废水处理。 ②氯化卫生尾气洗涤系统 本项目氯化卫生尾气净化系统主要是收集氯化炉排盐时和更换收尘渣罐过程产生的废气,技术改造完成后,两台氯化炉错峰完成排盐和更换收尘渣罐。现有氯化卫生尾气净化设施通过错峰使用可满足使用要求,现有氯化卫生尾气主要采用两级水洗+两级碱洗,为优化洗涤效果,在一级和二级水洗洗涤塔之间增加一级吸收塔(采用水作为吸收剂)。 氯化卫生尾气主要含有Cl2、HCl、TiCl4等尾气,改造后采用5级洗涤(三级水洗+两级碱洗)组合工艺处理后尾气全部通过现有80m高排气筒排放。氯化卫生尾气在三级水洗喷淋吸收塔被水洗涤吸收尾气中的HCl、TiCl4,反应方程式为:TiCl4+2H2O=TiO2+4HCl,少部分TiCl4被氧气被氧化TiCl4+O2=TiO2+2Cl2。 当一级洗涤塔循环槽盐酸浓度达到要求时,打开喷淋吸收塔循环泵出口排液阀门将部分吸收液排入储罐区的盐酸储槽,作为副产品。而未被吸收的尾气进入碱洗喷淋吸收塔+碱洗喷淋填料吸收塔被NaOH溶液洗涤吸收尾气中的Cl2、HCl后,其中碱液吸收后产生的废碱液一部分用于循环,部分启动废水外排泵,至废水处理。 ③精制尾气洗涤系统 本项目精制尾气包括精制过程工艺尾气及卫生尾气,根据建设单位提供相关设计资料现有精制尾气洗涤系统能够满足洗涤需求。精制过程中产生的主要含TiCl4、HCl尾气,主要采用三段吸收洗涤(两级水洗+一级碱洗)工艺处理后尾气全部通过现有80m高排气筒排放。 精制尾气在两级水洗喷淋吸收塔被水洗涤吸收尾气中的HCl、TiCl4,当一级洗涤塔循环槽盐酸浓度达到要求时,打开喷淋吸收塔循环泵出口排液阀门将部分吸收液排入储罐区的盐酸储槽,作为副产品。而未被吸收的尾气进入碱洗喷淋吸收塔被NaOH溶液洗涤吸收尾气中的Cl2、HCl后,其中碱液吸收后产生的废碱液一部分用于循环,部分启动废水外排泵,至废水处理。 ④还蒸尾气洗涤系统 还蒸尾气洗涤系统主要收集洗涤还蒸车间的尾气及镁电解车间坩埚炉熔炼过程产生含尘烟气,主要采用3级洗涤(两级水洗+1级碱洗)工艺处理后尾气全部通过现有80m高排气筒排放。根据建设单位提供相关设计资料通过错峰排放氯化镁的操作,还蒸精尾气洗涤系统能够满足洗涤需求。 还原、蒸馏尾气中主要含HCl、颗粒物,镁电解车间坩埚炉熔炼废气主要含烟尘,上述废气在两级水洗喷淋吸收塔被水洗涤吸收尾气中的HCl,并除尘,当一级洗涤塔循环槽盐酸浓度达到要求时,打开喷淋吸收塔循环泵出口排液阀门将部分吸收液排入储罐区的盐酸储槽,作为副产品。而未被吸收的尾气进入碱洗喷淋吸收塔被NaOH溶液洗涤吸收尾气中的HCl后,其中碱液吸收后产生的废碱液一部分用于循环,部分启动废水外排泵,至废水处理。 |
项目变动情况:项目未建设水淬工序,项目运营期产生的氯化熔盐渣及收尘渣依托厂区熔盐氯化综合示范性项目水淬工序进行水淬。项目变动原因:厂区熔盐氯化综合示范性项目已建设完成水淬工序,用于氯化熔盐渣及收尘渣水淬,****公司发展规划,项目运营期产生的氯化熔盐渣及收尘渣依托厂区熔盐氯化综合示范性项目水淬工序进行处理,本项目不再建设水淬工序,厂区熔盐氯化综合示范性项目水淬工序满足本项目氯化熔盐渣及收尘渣处理需求。 | 是否属于重大变动:|
环保设施或环保措施
1、废水治理措施 (1)初期雨水 项目在厂区现有基础上进行改建,不新增用地,项目建设不新增厂区初期雨水量,厂区现有初雨收集池2座(容积分别为4000m3、1600m3)。初期雨水用管道重力排至初期雨水收集池。初期雨水经收集、暂存后,****处理站处理后回用于生产。厂区北侧初期雨水排入****处理站处理,海绵钛****处理站处理规模50m3/h、1200m3/d;厂区南侧初期雨水排入厂区3万吨海绵钛****处理站处理,处理规模为1000m3/d。 (2)生产废水 项****处理站一座,处理规模20m3/h,处理工艺拟采用“预处理+超滤+反渗透+浓水反渗透”工艺。设备清洗废水、地面冲洗废水、尾气洗涤系****处理站浓水,为高****公司租用的龙佰**钛业钛白粉厂含盐废水处理蒸发装置处理。龙佰**钛业钛白粉厂区现有已建含盐废水处理蒸发装置处理能力为20m3/h。在建两套65m3/hMVR蒸发装****公司租用一套)。 (3)生活废水 海绵钛厂区现已建成2****处理站,(处理规模均为10m3/h),均采用A-O工艺,处理后的水用于厂区绿化和道路清扫,不外排,本项目建设不新增工作人员不新增厂区生活污水量。 2、废气治理措施 (1)备料车间废气 依托现有尾气处置措施,并在现有袋式除尘器前增加一级旋风除尘,(技改后原料备料系统工作时间为8760h/a)。 (2)氯化、精制、还蒸尾气 ①**2#氯化工艺废气净化系统,并对现有1#氯化工艺尾气洗涤进行改造,本次改造后两套氯化炉氯化工艺废气洗涤处理工艺一致,尾气处理采用6级洗涤“两级水洗+三级氯化亚铁洗涤塔+一级碱洗塔+捕滴器”组合工艺处理。②现有氯化卫生尾气现主要采用两级水洗+两级碱洗,对现有氯化卫生尾气洗涤系统进行改造,改造后采用5级洗涤(三级水洗+两级碱洗)组合工艺处理。③依托现有精制尾气净化系统设施,采用三段吸收洗涤(二段水吸收+碱洗)工艺处理。④还蒸车间尾气依托现有还蒸尾气洗涤系统,主要采用3级洗涤(两级水洗+1级碱洗)工艺处理,镁电解车间坩埚炉废气并入还蒸尾气处理系统进行处理。⑤上述尾气经洗涤处理后全部并入厂区现有80m(内径1m)高排气筒排放,并进行在线监测。 (3)破碎及包装废气 本次改造后利旧现有闲置2套旋风除尘器及2根20m高排气筒)。包装工段设置1套旋风除尘器及1根20m高排气筒,粉尘经处理后排放。在现有破碎、包装工序的收尘系统进行升级改造,现有各旋风除尘器基础上新增一级除尘,共新增5套旋风除尘器。 (4)抬包加热废气 本次改造后采用电加热抬包,不在使用天然气。取消台包加热废气排气筒。 3、噪声治理措施 新增设备选用低噪声设备,对噪声源采取消声、隔声、减振等措施。 4、固废治理措施 废膜由厂家回收处理;废机油依托****公司厂区现有42m2废机油暂存间暂存后,委托有资质单位处置;生活垃圾委托地方环卫部门清运。生产废渣依托****公司渣场堆存,****公司渣场位于厂区西南面270m处,占地约131亩,设计有效库容81.94万m3;渣场于2009年12月开工建设,于2011年底竣工,渣场建设有拦渣坝、拦污坝、防渗系统、截洪沟、地下水收集盲沟、渗滤液收集盲沟、渗滤液回喷系统等。目前该渣场正在扩容扩容后渣场总坝高为73.5m,全库容193.77万m3。 5、地下水污染防控措施 (1)防渗措施 针对本次新增的主要装置区按照地下水章节防渗要求进行防渗。 (2)监控井 依托现有海绵钛厂区东侧泉点、海绵钛厂区西侧泉点、GW1、GW2、GW3设置为地下水跟踪监测井。 6、环境风险措施 项目建设不新增四氯化钛储罐,厂区现有四氯化钛储罐为卧式罐储存,储罐进出口管道设置紧急切断阀,储罐顶部采用微正压(0.02~0.05MPa)的氮气气封,并设置了液位计。储罐四周设置围堰(围堰容积120m3),防止液体外漏,防止液体外漏;在罐区设干砂槽,四氯化钛泄漏时采用干砂覆盖;储罐储存区域设置了安全警示标志。项目不新增盐酸、硫酸及碱液储罐,厂区现有风险物质均采用储罐贮存,储罐区设置围堰;厂区内南面设置总容积2200m3事故池。本项目升级改造后将**一座2200m3事故池。 | 实际建设情况:1、废水治理措施 (1)初期雨水 项目在厂区现有基础上进行改建,不新增用地,项目建设不新增厂区初期雨水量,厂区现有初雨收集池2座(容积分别为4000m3、3200m3)。初期雨水用管道重力排至初期雨水收集池。初期雨水经收集、暂存后,****处理站处理后回用于生产。厂区北侧初期雨水排入****处理站处理,海绵钛****处理站处理规模50m3/h、1200m3/d;厂区南侧初期雨水排入厂区3万吨海绵钛****处理站处理,总处理规模为768m3/d(低含盐废水处理系统处理规模360m3/d,高含盐废水处理系统处理规模408m3/d)。 (2)生产废水 项****处理站一座,处理规模20m3/h,处理工艺采用“预处理+超滤+反渗透+浓水反渗透”工艺。设备清洗废水、地面冲洗废水、尾气洗涤系****处理站浓水为高盐废水,****公司租用的****公司现有含盐废水处理蒸发装置处理。****公司厂区现有3套含盐废水处理蒸发装置,包含1套处理能力为20m3/h含盐废水处理蒸发装置和2套处理能力为65m3/h含盐废水处理蒸发装置。****租用****公司其中1套处理能力为65m3/h含盐废水处理蒸发装置处理本项目产生的高含盐废水。 (3)生活废水 海绵钛厂区现已建成2****处理站,处理规模均为10m3/h,均采用A-O工艺,已建成4个化粪池,总容积30m3,生活污水经现有****园区污水管网,最终****处理厂处理,本项目建设不新增工作人员不新增厂区生活污水量。厂区现有2****处理站作为备用废水处理设施,****处理厂设备故障或检修期间,项目生活污水进入2****处理站处理达标后回用于厂区绿化及道路浇洒。 2、废气治理措施 (1)备料车间废气 依托现有尾气处置措施,并在现有袋式除尘器前增加一级旋风除尘,(技改后原料备料系统工作时间为8760h/a)。 (2)氯化、精制、还蒸尾气 ①**2#氯化工艺废气净化系统,并对现有1#氯化工艺尾气洗涤进行改造,本次改造后两套氯化炉氯化工艺废气洗涤处理工艺一致,尾气处理采用6级洗涤“两级水洗+三级氯化亚铁洗涤塔+一级碱洗塔+捕滴器”组合工艺处理。②现有氯化卫生尾气现主要采用两级水洗+两级碱洗,对现有氯化卫生尾气洗涤系统进行改造,改造后采用5级洗涤(三级水洗+两级碱洗)组合工艺处理。③依托现有精制尾气净化系统设施,采用三段吸收洗涤(二段水吸收+碱洗)工艺处理。④还蒸车间尾气依托现有还蒸尾气洗涤系统,主要采用3级洗涤(两级水洗+1级碱洗)工艺处理,镁电解车间坩埚炉废气并入还蒸车间尾气净化系统设施进行处理。⑤上述尾气经洗涤处理后全部并入厂区现有80m(内径1m)高排气筒排放,并进行在线监测。 (3)破碎及包装废气 本次改造后利旧现有闲置2套旋风除尘器作为军工小粒度产品破碎生产线的除尘设施,并在2套旋风除尘器基础上新增2套一级旋风除尘器,2根20m高排气筒合并成1根20m高排气筒排放。在现有破碎、包装工段3套旋风除尘器的基础上新增3套一级旋风除尘器,3根20m高排气筒合并成1根20m高排气筒排放。破碎包装车间共新增5套旋风除尘器。 (4)抬包加热废气 本次改造后采用电加热抬包,不在使用天然气。取消台包加热废气排气筒。 3、噪声治理措施 新增设备选用低噪声设备,对噪声源采取消声、隔声、减振等措施。 4、固废治理措施 废膜由厂家回收处理;项目**1间占地面积为54m2的危险废物暂存间,废机油经油桶收集后暂存于危险废物暂存间,委托****清运处置;生活垃圾经垃圾箱收集后委托环卫部门清运处置。渣场由****经营管理,本项目产****公司渣场进行堆存,渣场位于厂区西南面270m处,占地约131亩,设计有效库容94.34万m3;渣场于2009年12月开工建设,于2011年底竣工,渣场建设有拦渣坝、拦污坝、防渗系统、截洪沟、地下水收集盲沟、渗滤液收集盲沟、渗滤液回喷系统等。本次渣场扩容主要对2号库进行扩容,2号库区扩容从1905.0m标高开始在周边取土扩大容积,在原设计堆高1915.0m基础上加高堆坝至1935.0m,增加有效库容 126.71万m3。新增征地面积126亩,****填埋场总坝高为69m,总容积237.14万m3(1号堆渣区+2号堆渣区),增加服务年限约7.4年。 5、地下水污染防控措施 (1)防渗措施 项目渣处理车间已有地面按照耐酸砖、环氧胶泥、150mm厚混凝土、两层SBS、素土夯实自下而上的防渗方式进行重点防渗处理;废气洗涤平台已有地面已按照150mm厚混凝土、素土夯实自下而上的防渗方式进行重点防渗处理。**的渣处理车间已按照耐酸砖、环氧胶泥、150mm厚混凝土、两层SBS、素土夯实自下而上的防渗方式进行重点防渗处理;****处理站、事故水池已按照重点防渗要求进行防渗处理,原料库、氯化车间、精制车间、还原蒸馏车间、海绵钛破碎车间、****泵站已有地面按照耐酸砖、环氧胶泥、150mm厚混凝土、两层SBS、素土夯实自下而上的防渗方式进行一般防渗处理;原料库、****泵站**部分已按照耐酸砖、环氧胶泥、150mm厚混凝土、两层SBS、素土夯实自下而上的防渗方式进行一般防渗处理,2#还蒸镁电解循环水冷却站已按照一般防渗要求进行防渗处理。配电室、氯压机室、制冷站、空压站已有地面按照150mm厚混凝土、素土夯实自下而上的防渗方式进行简单防渗处理,**的整流所、装车平台、10kv变配电所已按照简单防渗要求进行防渗处理。 (2)监控井 依托海绵钛生产区东侧泉点(项目区下游,E102.304873;N25.084415)、海绵钛生产区西北侧钻孔(项目区下游,E102.2990;N25.08990)、海绵钛综合仓库旁钻孔GW1(项目区下游,E102.298044;N25.082849)、海绵钛厂区西侧钻孔GW2(项目区下游,E25.087570;N102.297957)、****处理站旁钻孔GW3(项目区下游,E102.309776;N25.093393)。 6、环境风险措施 项目建设不新增四氯化钛储罐,厂区现有四氯化钛储罐为卧式罐储存,储罐进出口管道设置紧急切断阀,储罐顶部采用微正压(0.02~0.05MPa)的氮气气封,并设置了液位计。储罐四周设置围堰(围堰容积120m3),防止液体外漏,防止液体外漏;在罐区设干砂槽,四氯化钛泄漏时采用干砂覆盖;储罐储存区域设置了安全警示标志。项目不新增盐酸、硫酸及碱液储罐,厂区现有风险物质均采用储罐贮存,储罐区设置围堰;厂区内南面设置总容积2200m3事故池。项目实际依托厂区现有一座容积为3100m3的闲置空池作为事故应急池,收集事故状态下产生的废水。环评提出的2200m3事故池不再建设。 |
1、项目变动情况:项目实际依托原有初期雨水收集池总容积增加1600m3。项目变动原因:由于厂区原有1600m3初期雨水收集池已作为废水收集池使用,因此厂区已重**设1座容积为3200m3的初期雨收集池代替原有1600m3初期雨水收集池收集厂区初期雨水。 2、项目变动情况:项目依托厂区3万吨海绵钛****处理站处理规模减少232m3/d。项目变动原因:厂区3万吨海绵钛项目实际分两期建设,一期项目含盐废水产生量减小,****处理站处理规模进行调整。 3、项目变动情况:职工生活废水经化粪池****园区污水处理厂处理。厂区现已建成的2****处理站作为备用废水处理设施。项目变动原因:****管理委员会的要求,职****园区污水处理厂处理。因此,厂区职工生活污水经化粪****园区污水处理厂处理。 4、项目变动情况:军工小粒度产品破碎废气2根排气筒合并为1根排气筒;破碎、包装废气3根排气筒合并为1根排气筒。项目变动原因:由于军工小粒度产品破碎生产线2根排气筒排放的污染物相同,破碎、包装工段3根排气筒排放的污染物相同,为了方便管理,项目将军工小粒度产品破碎废气2根排气筒合并为1根排气筒;将破碎、包装废气3根排气筒合并为1根排气筒。 5、项目变动情况:废机油由****厂区**的54m2危险废物暂存间暂存后委托**广莱再生**清运处置,不再依托****公司废机油暂存间暂存。项目变动原因:****公司废机油及其他危险废物储存和管理,****厂区**1间占地面积为54m2的危****公司生产过程产生的危险废物,因此本项目产生的废机油在该暂存间内暂存后委托**广莱再生**清运处置,不再依托****公司废机油暂存间暂存,**的危险废物暂存间满足本项目废机油暂存需求。 6、项目变动情况:项目依托渣场经营管理单位变更,总库容增加43.97万m3。项目变动原因:为了方便渣场管理,渣场经营管理单位由****公司变更为****;****填埋场内2号库区经重新设计后,实际建设库容增大,满足本项目运营期产生的废渣堆存要求。 7、项目变动情况:本项目依托厂区现有一座容积为3100m3的闲置空池作为事故应急池,未建设2200m3事故池。项目变动原因:由于场地限制及基于成本考虑,项目实际采用厂区熔盐氯化综合示范性项目建设的一座容积为3100m3的闲置空池(该池子原为盐水中转池,目前已不再使用)作为本项目事故应急池,不再建设2200m3事故池。该闲置池子已按照重点防渗要求进行防渗处理,容积相比环评阶段增加900m3,满足事故状态下废水收集需求。 | 是否属于重大变动:|
其他
无 | 实际建设情况:无 |
无 | 是否属于重大变动:|
3、污染物排放量
0 | 0 | 0 | 0 | 0 | 0 | 0 | |
0 | 0 | 0 | 0 | 0 | 0 | 0 | |
0 | 0 | 0 | 0 | 0 | 0 | 0 | |
0 | 0 | 0 | 0 | 0 | 0 | 0 | |
0 | 0 | 0 | 0 | 0 | 0 | 0 | |
122199.58 | 54644.442 | 0 | 62631.58 | 0 | 114212.442 | -7987.138 | / |
24.825 | 6 | 0 | 24.825 | 0 | 6 | -18.825 | / |
3.964 | 0 | 0 | 3.964 | 0 | 0 | -3.964 | / |
19.429 | 10.588 | 0 | 11.506 | 0 | 18.511 | -0.918 | / |
0 | 0 | 0 | 0 | 0 | 0 | 0 | / |
6.991 | 2.427 | 0 | 4.389 | 0 | 5.029 | -1.962 | / |
9.648 | 0.505 | 0 | 4.433 | 0 | 5.72 | -3.928 | / |
4、环境保护设施落实情况
表1 水污染治理设施
1 | 厂区雨污分流管网 | 无 | 厂区雨污分流管网 | 未监测 | |
2 | 依托原有初期雨水收集池2个(3200m3、4000m3) | 无 | 依托原有初期雨水收集池2个(3200m3、4000m3) | 未监测 | |
3 | ****处理站2套(处理规模1200m3/d、处理规模768m3/d) | 无 | ****处理站2套(处理规模1200m3/d、处理规模768m3/d) | 未监测 | |
4 | 依托原有化粪池4个(总容积30m3) | 《污水排入城镇下水道水质标准》(GB/T31962-2015)表1A级标准 | 依托原有化粪池4个(总容积30m3) | 已监测 | |
5 | ****处理站2套(处理规模均为10m3/h) | 《污水排入城镇下水道水质标准》(GB/T31962-2015)表1A级标准 | ****处理站2套(处理规模均为10m3/h) | 已监测 | |
6 | ****处理站1座(处理规模20m3/h) | 《城市污水再生利用 工业用水水质》(GB/T19923-2005)中冷却用水等标准 | ****处理站1座(处理规模20m3/h) | 已监测 | |
7 | 依托****公司已建成的65m3/h的MVR蒸发器 | 无 | 依托****公司已建成的65m3/h的MVR蒸发器 | 未监测 |
表2 大气污染治理设施
1 | 2套处理工艺为“一级旋风除尘器+袋式除尘器+20m高排气筒”的备料车间废气处理设施 | 《镁、钛工业污染物排放标准》(GB25468-2010)表5标准和本项目环评及批复规定的排放限值 | 2套处理工艺为“一级旋风除尘器+袋式除尘器+20m高排气筒”的备料车间废气处理设施 | 已监测 | |
2 | 2套处理工艺为“两级水洗+三级氯化亚铁洗涤塔+一级碱洗塔+捕滴器+80m高排气筒”的氯化工艺废气处理设施 | 《镁、钛工业污染物排放标准》(GB25468-2010)表5标准和本项目环评及批复规定的排放限值 | 2套处理工艺为“两级水洗+三级氯化亚铁洗涤塔+一级碱洗塔+捕滴器+80m高排气筒”的氯化工艺废气处理设施 | 已监测 | |
3 | 1套处理工艺为“三级水洗+两级碱洗+80m高排气筒”的氯化卫生尾气处理设施 | 《镁、钛工业污染物排放标准》(GB25468-2010)表5标准和本项目环评及批复规定的排放限值 | 1套处理工艺为“三级水洗+两级碱洗+80m高排气筒”的氯化卫生尾气处理设施 | 已监测 | |
4 | 1套处理工艺为“二段水吸收+碱洗+80m高排气筒”的精制尾气处理设施 | 《镁、钛工业污染物排放标准》(GB25468-2010)表5标准和本项目环评及批复规定的排放限值 | 1套处理工艺为“二段水吸收+碱洗+80m高排气筒”的精制尾气处理设施 | 已监测 | |
5 | 1套处理工艺为“两级水洗+1级碱洗+80m高排气筒”的还蒸车间尾气和镁电解车间尾气处理设施 | 《镁、钛工业污染物排放标准》(GB25468-2010)表5标准和本项目环评及批复规定的排放限值 | 1套处理工艺为“两级水洗+1级碱洗+80m高排气筒”的还蒸车间尾气和镁电解车间尾气处理设施 | 已监测 | |
6 | 2套处理工艺为“二级旋风除尘器+20m高排气筒”的军工小粒度产品破碎废气处理设施 | 《镁、钛工业污染物排放标准》(GB25468-2010)表5标准和本项目环评及批复规定的排放限值 | 2套处理工艺为“二级旋风除尘器+20m高排气筒”的军工小粒度产品破碎废气处理设施 | 已监测 | |
7 | 3套处理工艺为“二级旋风除尘器+20m高排气筒”的商品海绵钛破碎包装废气处理设施 | 《镁、钛工业污染物排放标准》(GB25468-2010)表5标准和本项目环评及批复规定的排放限值 | 3套处理工艺为“二级旋风除尘器+20m高排气筒”的商品海绵钛破碎包装废气处理设施 | 已监测 |
表3 噪声治理设施
1 | 采取对产噪设备加设减振基础及消声设备、选用低噪声设备、厂房隔声、合理布置生产设备、加强设备维护保养等措施 | 《工业企业厂界环境噪声排放标准》(GB12348-2008)3类标准限值 | 采取对产噪设备加设减振基础及消声设备、选用低噪声设备、厂房隔声、合理布置生产设备、加强设备维护保养等措施 | 已监测 |
表4 地下水污染治理设施
1 | 落实地下水和土壤污染防治措施。按照“源头控制、分区防渗、污染监控、应急响应”的原则进行地下水污染防治。项目实施分区防渗,**的渣处理车间、****处理站、2#还蒸镁电解循环水冷却站、事故油池、****泵站等区域需按照《环境影响评价技术导则 地下水环境》(HJ610—2016)中重点防渗区的要求进行防渗,防渗效果等效于厚度大于6.0米、渗透系数≤1.0×10-7厘米/秒的黏土层的防渗性能;除重点防渗区以及绿化带外,其余地面均需采用水泥硬化处理。按照《中华人民**国地下水保护条例》《地下水污染源防渗技术指南(试行)》《地下水环境监测技术规范》(HJ164—2020)等要求,制定并落实地下水跟踪监测计划及检漏措施,继续沿用原设置的5个地下水监测井进行跟踪监测。严格落实周边土壤跟踪监测方案。 | 项目已严格落实地下水和土壤污染防治措施。按照“源头控制、分区防渗、污染监控、应急响应”的原则进行地下水污染防治。(1)厂区已按清污分流分质处理的原则,建成三大排水系统,确保生产废水、生活污水、初期雨水有组织地分别排入对应的系统管网和处理系统处理。(2)项目已进行分区防渗处理:渣处理车间已有地面按照耐酸砖、环氧胶泥、150mm厚混凝土、两层SBS、素土夯实自下而上的防渗方式进行重点防渗处理;废气洗涤平台已有地面已按照150mm厚混凝土、素土夯实自下而上的防渗方式进行重点防渗处理。**的渣处理车间已按照耐酸砖、环氧胶泥、150mm厚混凝土、两层SBS、素土夯实自下而上的防渗方式进行重点防渗处理;****处理站和事故应急池已按照重点防渗要求进行防渗处理,原料库、氯化车间、精制车间、还原蒸馏车间、海绵钛破碎车间、****泵站已有地面按照耐酸砖、环氧胶泥、150mm厚混凝土、两层SBS、素土夯实自下而上的防渗方式进行一般防渗处理;原料库、****泵站**部分已按照耐酸砖、环氧胶泥、150mm厚混凝土、两层SBS、素土夯实自下而上的防渗方式进行一般防渗处理,2#还蒸镁电解循环水冷却站已按照一般防渗要求进行防渗处理。配电室、氯压机室、制冷站、空压站已有地面按照150mm厚混凝土、素土夯实自下而上的防渗方式进行简单防渗处理,**的整流所、装车平台、10kv变配电所已按照简单防渗要求进行防渗处理。根据工程监理单位出具的《****10kt/a海绵钛生产线升级改造创新项目工程质量评估报告》,本工程使用的各种建筑材料均为合格材料,工程质量验收合格,隐蔽工程验收合格。 (3)项目已严格按照排污许可证自行监测要求,定期对项目周边5个地下水监测井、地下水出露点、主导风向下风向土壤和项目区西北侧农田开展监测。 |
表5 固废治理设施
1 | 加强固体废物综合利用和妥善处置。按照“减量化、**化、无害化”原则,对固体废物进行分类收集、处理处置,确保不造成二次污染。 工业固体废物应立足于回收利用,须规范分类收集、贮存、处置。需按危险废物鉴别相关工作要求对项目生产所产生水淬渣、还原蒸馏渣、钒渣、钛铁残渣、电解渣、精炼渣、升华物、尾气洗涤系统泥渣、污水站污泥等固体废物开展属性鉴别,按鉴别结果进行处置。危险废物应严格按照《危险废物贮存污染控制标准》(GB18597-2023)及修改单等要求进行贮存及管理,委托有资质的单位进行处置;一般工业固废进入渣库堆存。现有渣场按照《一般工业固体废物贮存和填埋污染控制标准》(GB18599-2020)Ⅱ类堆场要求进行管理,废机油按照危险废物管理相关要求贮存和处理处置。加强物料堆放场、渣场环境管理,严格采取防渗漏、防流失、防扬散等措施。生活垃圾统一收集,定期委托环卫部门清运。 | 项目已加强固体废物综合利用和妥善处置,根据建设单位提供的固废危险特性初筛分析报告,项目精炼渣、电解渣、水淬渣(盐泥)检测结果未超过《危险废物鉴别标准 腐蚀性鉴别》(GB5085.1-2007)、《危险废物鉴别标准 浸出毒性鉴别》(GB5085.3-2007)、《危险废物鉴别标准 反应性鉴别》(GB5085.5-2007)、《危险废物鉴别标准 毒性物质含量鉴别》(GB5085.6-2007)中的相关限值,排除其腐蚀性、浸出毒性、毒性物质含量和反应性。项目委托******公司对钒渣、尾气处理泥渣、还原蒸馏渣、电解渣、精炼炉渣、升华物、废耐火砖、氯化水淬渣进行腐蚀性和浸出毒性鉴别,鉴别结果均未超过《危险废物鉴别标准 腐蚀性鉴别》(GB5085.1-2007)、《危险废物鉴别标准 浸出毒性鉴别》(GB5085.3-2007)相应标准限值,排除其腐蚀性、浸出毒性。****“****填埋场主体扩容及公辅设施配建工程竣工环境保护验收”委托******公司对氯化炉渣、收尘渣、污水站污泥、钛铁残渣进行腐蚀性和浸出毒性鉴别,鉴别结果均未超过《危险废物鉴别标准 腐蚀性鉴别》(GB5085.1-2007)、《危险废物鉴别标准 浸出毒性鉴别》(GB5085.3-2007)相应标准限值,排除其腐蚀性、浸出毒性。项目产生的氯化水淬渣、还原蒸馏渣、钛铁残渣、电解渣、精炼炉渣、升华物、尾气洗涤系统泥渣、废耐火材料、污水站污泥运至********填埋场填埋。****正在组织制定钒渣企业标准,****管理部门批准并核发《**工业产品生产许可证》后,钒渣作为副产品外售。项目废机油采用专用容器收集后在厂区危险废物暂存间进行暂存,危险废物暂存间占地面积54m2,按照《危险废物贮存污染控制标准》(GB18597-2023)要求进行建设和管理,危险废物暂存间设置标识牌,设置危险废物管理制度,危险废物转移联单,废机油委托****定期清运处置。****处理站产生的废膜集中收集由厂家回收处置。项目职工生活垃圾经垃圾箱收集后委托环卫部门清运处置。********填埋场已按照《一般工业固体废物贮存和填埋污染控制标准》(GB18599-2020)Ⅱ类堆场要求进行管理。****填埋场已设置专职人员进行管理,已采取防渗漏、防流失、防扬散等措施。 |
表6 生态保护设施
1 | 加强施工期环境管理。采取洒水降尘、道路清扫、封闭车辆运输、合理安排施工时间等措施减缓施工对周围环境的不良影响。项目建设过程中,施工期环境监理纳入工程监理内容,各项生态环境保护措施纳入施工、工程监理等招标文件及合同,并明确责任,对防渗工程进行验收,确保环境保护设施符合有关要求。 | 加强施工期环境管理。采取洒水降尘、道路清扫、封闭车辆运输、合理安排施工时间等措施减缓施工对周围环境的不良影响。项目建设过程中,施工期环境监理纳入工程监理内容,各项生态环境保护措施纳入施工、工程监理等招标文件及合同,并明确责任,对防渗工程进行验收,确保环境保护设施符合有关要求。 |
表7 风险设施
1 | 加强环境风险防范和管理。建立健全风险防控体系和事故排放污染收集系统,做好环境风险的巡查、监控等管理,杜绝环境风险事故发生。加强环境保护设施运行维护,确保正常运行。按照《突发环境事件应急管理办法》《企事业单位突发环境事件应急预案备案管理办法(试行)》等要求,严格落实厂区及周边各项环境风险防范措施与事故应急措施,强化液氯、四氯化钛等风险物质的生产、贮存、输送和使用环节的风险管理,罐区设置围堰、检漏、喷淋、碱洗、报警等相关设施,更新环境事故应急预案并备案,****环境局、****环境局**分局,加强应急培训和演练。 | 项目已加强环境风险防范和管理。①厂区已设置5个地下水监控井,分别为:海绵钛生产区东侧泉点(项目区下游,E102.304873;N25.084415)、海绵钛生产区西北侧钻孔(项目区下游,E102.2990;N25.08990)、海绵钛综合仓库旁钻孔GW1(项目区下游,E102.298044;N25.082849)、海绵钛厂区西侧钻孔GW2(项目区下游,E25.087570;N102.297957)、****处理站旁钻孔GW3(项目区下游,E102.309776;N25.093393)。公司已按照环评批复及排污许可证提出的监测计划,定期开展地下水监测。②厂区现已设置相应的风险防范措施,本次技改不新增储罐及氯气总管道等,升级改造后新增的氯压机室内新增6台氯气检测报警仪,新增的电解槽区域设置10台氯气检测报警仪。精制车间新增设备区新增12台氯化氢检测报警仪。并对改造新增的设备间物料输送通过PLC系统控制运行,并与DCS系统连接。③技改后根据新增装置的情况增加视频监控设备,确保能够监控技改后整个项目的实时情况。④依托厂区现有一座容积为3100m3的闲置空池作为事故应急池,收集事故状态下产生的废水。⑤设置二级报警装置。在厂界南侧、西侧、东侧增设氯气及氯化氢检测报警仪(共设置3个),在出现氯气或四氯化钛泄漏出现氯气或氯化氢气体向厂界外蔓延时,公司可第一时间启动氯气和氯化氢泄漏应急处置措施,减小氯气及氯化氢泄漏对周边环境的影响。⑥项目已设置厂界外800米的卫生防护距离,防****学校、医院、居民点等敏感目标。⑦****于2024年1月编制了《****突发环境事件应急预案(2024年修订版)》,并于2024年1月31****环境局**分局备案,备案号:532331-2024-006-H。 |
5、环境保护对策措施落实情况
依托工程
无 | 验收阶段落实情况:无 |
/ |
环保搬迁
无 | 验收阶段落实情况:无 |
/ |
区域削减
无 | 验收阶段落实情况:无 |
/ |
生态恢复、补偿或管理
无 | 验收阶段落实情况:无 |
/ |
功能置换
无 | 验收阶段落实情况:无 |
/ |
其他
1、落实清洁生产要求。应将清洁生产纳入生产管理和环境管理中,以清洁生产要求指导生产的全过程。单位产品能耗、物耗、水耗、**综合利用和污染物产生量等指标应达到清洁生产先进水平,定期实施清洁生产审核。 2、落实环境监测及环境信息公开要求。根据相关标准、技术规范要求和《报告书》中提出的监测计划,制定并严格落实自行监测方案,强化大气、地下水、土壤、噪声等的监测,重点加强对外排废气中颗粒物、氯气、氯化氢、二氧化硫等污染物的监测,自行****生态环境局备案,****环境局**分局。组织对污染物排放状况及其对周边环境质量的影响开展自行监测,防范环境污染,发现异常情****政府及相关部门并采取措施处理。按照信息公开相关规定,主动向社会公开污染源监测等相关信息。 3、严格落实污染物排放总量控制规定和各项措施。根据《报告书》,扩建项目建成后,大气污染物外排环境量初步核定为颗粒物14.63吨/年、二氧化硫12.41吨/年、氮氧化物0吨/年,其他污染物排放按照《报告书》要求做好控制。严格落实《建设项目主要污染物排放总量指标审核及管理暂行办法》(环发〔2014〕197号)要求,****环境局纳入主要污染物排放总量控制管理。加大二氧化碳排放控制力度,积极制定并实施二氧化碳综合利用措施,减少项目二氧化碳排放。 4、****公司全部建设项目防护范围,参照3万吨转子级项目环评批复文件,该项目整体执行800米卫生防护距离相关规定。 5、《报告书》经批准后,如工程的性质、规模、工艺、地点或者防治污染、防止生态破坏的措施发生重大变动的,应当重新报批环境影响评价文件,否则不得实施建设。在项目建设、运行过程中产生不符合经审批的《报告书》情形的,应当组织开展环境影响后评价,采取改进措施,按规定备案。项目正式投入生产或者运营后三至五年内组织开展环境影响后评价。《报告书》自批准之日起满5年,建设项目方开工建设的,《报告书》应当报我厅重新审核。 6、严格落实“三同时”制度。你公司应落实生态环境保护主体责任,建立内部生态环境管理体系,明确机构、人员、职责和制度,加强生态环境管理,推进各项生态环境保护措施落实。项目建设必须严格执行配套建设的环境保护设施与主体工程同时设计、同时施工、同时投产使用的环境保护“三同时”制度。应将优化和细化后的各项生态环境保护措施及概算纳入设计以及施工、工程监理等招标文件及合同,并明确责任。认真落实施工期环境监理工作,项目投运前向社会公开工程环境监理报告。制定并落实施工期和运营期生态环境跟踪监测方案,根据结果不断优化各项生态环境保护和污染防治措施。项目正式投运前,应当按照规定的标准和程序,对配套建设的环境保护设施进行验收。施工期环境监测报告和环境监理报告应作为项目竣工环境保护验收的依据之一。 7、在项目完成建设发生实际排污行为之前,按照经批准的《报告书》认真落实各项环境保护措施,污染物排放清单及其他有关内容载入排污许可证,有机衔接环境影响评价与排污许可证申领,并按证排污。项目运行应符合排污许可管理相关要求。 8、你单位收到本批复20个工作日内,应将批准后的《报告书》及批复****生态环境局、****环境局**分局,认真落实污染防治主体责任,及时排查消除环境风险隐患,接受各级生态环境主管部门的监督检查并完成检查反馈环境问题整改。 | 验收阶段落实情况:1、项目已将清洁生产纳入生产管理和环境管理中,以清洁生产要求指导生产的全过程。项目运营期降低产品能源消耗、物料消耗、生产用水消耗,加强**综合利用,生产过程产生的废水处理后全部回用,生活污水经过处理后回用于厂区绿化和道路浇洒。项目使用品位较高的原料进行生产,降低污染物的产生。公司已定期实施清洁生产审核。 2、项目已根据《环评报告书》提出的监测计划和《排污许可证》自行监测要求,对项目区及周边大气、地下水、土壤和噪声开展环境监测,并将自行监****生态环境局****环境局**分局备案,项目氯化、精制、还蒸尾气已安装在线监测设备对颗粒物、Cl2、HCl等污染物进行连续监测。公司对备料车间废气排气筒、剪切破碎包装废气排气筒排放的颗粒物开展季度监测。公司对项目区及周边地下水井开展年度监测,对项目主导下风向土壤和西北侧农田开展年度监测,发现异常****政府部门及相关部门并采取措施处理。项目污染物监测信息严格按照排污许可证监测管理要求按时在污染源监测信息平台录入监测结果并公开;在厂区门口显示屏同步公示污染物监测信息。 3、项目已严格落实污染物排放总量控制规定和各项措施。根据本次验收监测结果,有组织废气排放量为:54644.442万m3/a,颗粒物排放量为:10.588t/a、二氧化硫排放量为:6t/a、氮氧化物排放量为:0t/a、氯化氢排放量为:0.505t/a、氯气排放量为:2.427t/a,项目实际大气污染物排放总量满足环评及批复要求。 4、项目整体执行800米卫生防护距离相关规定,建设单******局汇报防护距离范围,******局出具的《情况说明》,卫生防护距离内现状无居民点,并防止在该防****学校、医院、居民区等环境敏感点。 5、根据本次验收现场调查,项目性质、性质、规模、工艺、地点未发生变动,项目实际建设过程中,部分主体工程、环保设施、生产设备发生变动,对照《镁、钛冶炼建设项目重大变动清单(试行)》(环办环评函〔2019〕934号),本项目变动内容不属于重大变动,无需重新报批环境影响评价文件。 6、项目已严格落实“三同时”制度,确保环境保护设施与主体工程同时设计、同时施工、同时投产使用。公司内部已建立生态环境管理体系,明确机构、人员、职责和制度,确保各项生态环境保护措施落实,污染物达标排放。 7、****在本项目投产前,于2023年7月27日变更《排污许可证》,排污许可证编号:****2300MA6P5G837X001P,将本项目环保设施、污染物排放清单等其他有关内容纳入排污许可证进行管理,确保项目按证排污。项目运行符合排污许可证的管理要求。 8、****已将本项目批准后的《10kt/a海绵钛生产线升级改造创新项目环境影响报告书》及其批复****生态环境局、****环境局**分局备案,认真落实污染防治主体责任,及时排查消除环境风险隐患,接受各级生态环境主管部门的监督检查并完成检查反馈环境问题整改。 |
/ |
6、工程建设对项目周边环境的影响
/ |
/ |
/ |
/ |
/ |
/ |
7、验收结论
1 | 未按环境影响报告书(表)及其审批部门审批决定要求建设或落实环境保护设施,或者环境保护设施未能与主体工程同时投产使用 |
2 | 污染物排放不符合国家和地方相关标准、环境影响报告书(表)及其审批部门审批决定或者主要污染物总量指标控制要求 |
3 | 环境影响报告书(表)经批准后,该建设项目的性质、规模、地点、采用的生产工艺或者防治污染、防止生态破坏的措施发生重大变动,建设单位未重新报批环境影响报告书(表)或环境影响报告书(表)未经批准 |
4 | 建设过程中造成重大环境污染未治理完成,或者造成重大生态破坏未恢复 |
5 | 纳入排污许可管理的建设项目,无证排污或不按证排污 |
6 | 分期建设、分期投入生产或者使用的建设项目,其环境保护设施防治环境污染和生态破坏的能力不能满足主体工程需要 |
7 | 建设单位因该建设项目违反国家和地方环境保护法律法规受到处罚,被责令改正,尚未改正完成 |
8 | 验收报告的基础资料数据明显不实,内容存在重大缺项、遗漏,或者验收结论不明确、不合理 |
9 | 其他环境保护法律法规规章等规定不得通过环境保护验收 |
不存在上述情况 | |
验收结论 | 合格 |
相关公告
招标导航更多>>
工程建筑
交通运输
环保绿化
医疗卫生
仪器仪表
水利水电
能源化工
弱电安防
办公文教
通讯电子
机械设备
农林牧渔
市政基建
政府部门
换一批
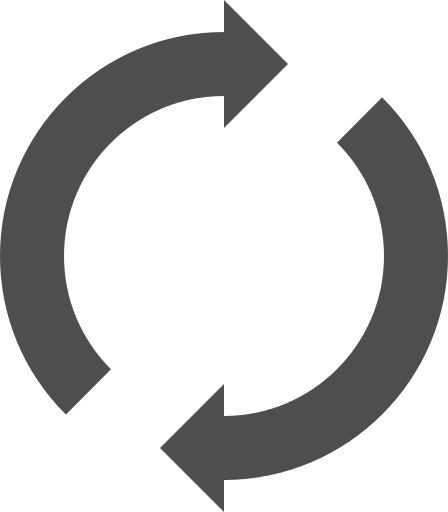