中粮粮谷漯河搬迁新建90万吨/年小麦加工项目
1、建设项目基本信息
企业基本信息
**** | 建设单位代码类型:|
914********153605W | 建设单位法人:张秀岩 |
闫苗苗 | 建设单位所在行政区划:**省漯****开发区 |
**经济技术产****经济开发区)**路东侧、发展**侧 |
建设项目基本信息
中粮粮谷**搬迁**90万吨/年小麦加工项目 | 项目代码:|
建设性质: | |
2021版本:015-谷物磨制;饲料加工 | 行业类别(国民经济代码):C1312-C1312-小麦加工 |
建设地点: | **省漯****开发区 **路东侧、发展**侧 |
经度:114.10801 纬度: 33.54493 | ****机关:****开发区****环保局 |
环评批复时间: | 2021-09-15 |
漯开环监表〔2021〕31号 | 本工程排污许可证编号:**** |
项目实际总投资(万元): | 85935 |
3817.5 | 运营单位名称:**** |
914********153605W | 验收监测(调查)报告编制机构名称:**市****公司 |
914********664996J | 验收监测单位:**市****公司 |
914********664996J | 竣工时间:2023-08-31 |
调试结束时间: | |
2024-06-27 | 验收报告公开结束时间:2024-07-24 |
验收报告公开载体: | http://www.****.com/newsshow.php?cid=17 id=147 |
2、工程变动信息
项目性质
** | 实际建设情况:** |
无 | 是否属于重大变动:|
规模
90万吨/年小麦加工 | 实际建设情况:90万吨/年小麦加工 |
无 | 是否属于重大变动:|
生产工艺
1、初清入仓:本项目卸粮入地坑工段,设置卸粮罩棚,卸粮罩棚在卸粮过程关门密闭卸粮,共设置3个卸粮坑,密闭空间设置有吸风系统保持该空间微负压,收集后气体经除尘器处理后达标排放。 地坑内原粮经过刮板机输送至斗式提升机,提升至工作塔通过圆筒筛、磁选、组合筛、风选等设备,初步筛去大的土块、石子、金属异物、绳头、玻璃、秸秆等大杂、小杂和轻杂后,除杂率一般是检验杂质的50%左右。该初清工段输送、筛分均在密闭空间内进行,但物料转输落料会产生一定量粉尘,该部分粉尘通过吸风系统收集后经除尘器处理后达标排放。 初清后原粮经提升机提到仓顶,经刮板机送到指定的仓内,提升机和刮板机均密闭,产生粉尘由吸风系统收集后经脉冲除尘器处理后达标排放。 2、配麦:根据产品特性需要,将不同麦仓、不同品质的原粮按一定比例配比,在仓底打开对应毛麦仓,利用小麦自身重力出仓进入绞龙,经过绞龙混合输送至匀质仓。由匀质仓再次根据产品特性需要配比进入毛麦仓进行再次配麦。该工段输送过程密闭,落料点产生粉尘由吸风系统收集后经脉冲除尘器处理后达标排放。 3、一次清理:经两次配麦后的物料进入一次清理工段,主要包括一清筛选(含磁选)、一清去石(含分级)、一清打麦(含磁选)、一清色选、一清着水、一清润麦工序。 ①一清筛选(含磁选):筛选功能:经过搭配的小麦通过组合筛不同筛孔的筛面,将小麦中的绳头、麦秸秆等大杂和小石子、小泥块等小杂质分出来,并对小麦中麦壳、麦灰、轻质粒通过吸风进行分离,达到小麦进一步清理的作用;磁选功能:原粮通过磁场强度在2000高斯以上的磁选器,去除小麦中的磁性金属杂质。 ②一清去石(含分级):小麦经过去石机,根据小麦和杂质的比重不同,将小麦中的石子有效去除。小麦经过分级机,根据小麦容重的不同,将容重高的和容重低的区分单独利用。 ③一清打麦(含磁选):用打麦机对小麦表面进行摩擦打击,使黏附在小麦表皮和腹沟中的麦毛、麦灰和部分强度较低的杂质得到分离,通过吸风系统将其清除。磁选功能:原粮通过磁场强度在2000高斯以上的磁选器,去除除小麦中的磁性金属杂质。 ④一清色选:根据小麦颜色的差异,利用光电技术将小麦中的霉变粒或赤霉粒分拣出来。 ⑤一清着水:一次清理后小麦经过着水机,着水机将水注入并通过桨叶将水充分均匀与小麦结合,使小麦的皮层韧性增加,胚乳和麦皮的结合力变弱,胚乳间的结合强度下降,从而有利于加工,加水量根据工艺需要设定。 ⑥一清润麦:着水后的小麦进入润麦仓进行静置润麦,根据小麦品质、温度不同,润麦时间一般控制在约16-30小时。 该工段输送、打麦、筛选过程密闭,落料点产生粉尘由吸风系统收集后经脉冲除尘器处理后达标排放。 4、二次清理:一次清理后的物料进入二次清理工段,主要包括二次着水、二次润麦、二次去石(含分级)、二次打麦(含磁选)、二次筛选、雾化着水、二请磁选工序。 ①二次着水:根据一次润麦的水分情况,在入磨前利用着水机进行二次着水。加水量根据工艺需要设定,使小麦适合工艺制粉操作,保证面粉水分符合要求。 ②二次润麦:一次润麦的小麦,根据小麦品质、外界温度,需进行二次润麦,润麦时间约4-10小时,让二次润麦的水分充分滋润小麦表皮,适合工艺制粉操作,保证面粉质量。 ③二次去石:同一次去石,主要是去除小麦中可能残留的小石块。 ④二次打麦(包含磁选):再次用打麦机对小麦表面进行摩擦打击,使黏附在小麦表皮和腹沟中的麦毛、麦灰和部分强度较低的杂质得到分离,通过吸风系统将其清除,润麦后原粮再次通过磁场强度在2000高斯以上的磁选器,去除原粮中可能残留的磁性金属杂质。 ⑤二次筛选:同一次筛选,再次对小麦中可能残留的大杂小杂进行清除。 ⑥雾化着水:二次润麦仓出来的小麦,由于润麦时间较长,小麦表皮变得干燥,在加工过程中表皮容易破碎,为了防止该现象的发生,通过喷雾着水机对通过喷雾着水机的小麦进行喷雾着水,用来湿润小麦表皮,增加表皮的韧性。 ⑦二清磁选:再次通过磁场强度在2000高斯以上的磁选器,去除小麦中可能残留的磁性金属杂质。该工段输送、打麦、筛选过程密闭,落料点产生粉尘由吸风系统收集后经脉冲除尘器处理后达标排放。 5、研磨:利用皮磨、心磨等专用磨粉机将麦粒碾开,分出大皮、麦渣、胚乳、麦心,并将胚乳磨成具有一定细度的小麦粉。该工段输送、磨制过程密闭,落料点产生粉尘由吸风系统收集后经脉冲除尘器处理后达标排放。 6、面粉筛理:小麦经过磨粉机研磨后,获得颗粒大小不同及质量不一的混合物料,利用不同规格的筛理设备将这些混合物分级,然后再研磨、筛理、分级,循环几次,直至获得需要的小麦粉。同时筛分出次粉和麸皮,筛分出次粉产品,通过定量包装机进行计量包装。经高方筛分离出的麸皮由打麸机进行打麸,清理粘附在麸皮的残留面粉,生产系统提取的麸皮产品依据水分指标,烘干或不烘干,烘干热能采用蒸汽。生产系统提取的麸皮产品,通过定量包装机进行计量包装。 该工段输送、筛分、烘干过程密闭,落料点产生粉尘由吸风系统收集后经脉冲除尘器处理后达标排放。 7、清粉、添加:清粉机根据物料的悬浮速度、颗粒不同,对一定的混合物料进行分级,得到较纯的物料送到下道磨粉机研磨。按生产方案指令添加或不添加,通过粉末分配机按规定比例将添加剂添加到粉流中。该工段输送、添加过程密闭,落料点产生粉尘由吸风系统收集后经脉冲除尘器处理后达标排放。 8、面粉收集:将系统所提取的面粉,按质量送入不同的集粉刮板中,通过集粉刮板将不同品质的粉/添加剂进行混合,组成二至五种基础小麦粉。该工段收集、混合、输送过程密闭,落料点产生粉尘由吸风系统收集后经脉冲除尘器处理后达标排放。 9、查筛、磁选:对刮板收集的基础粉通过筛理设备进行筛理,去除小麦粉中可能混入的异物、大的麸片等。查筛后的小麦粉在通过磁场强度在5000高斯以上的磁选器清除可能因设备脱落或磨损造成的磁性金属杂质。该工段输送、查筛、磁选过程密闭,落料点产生粉尘由吸风系统收集后经脉冲除尘器处理后达标排放。 10、正压吹送入粉仓:经过筛查和磁选的基础粉由过滤压缩后的空气正压吹送进入基粉仓,按不同品质分仓贮存。该工段输送过程密闭,落料点产生粉尘由吸风系统收集后经脉冲除尘器处理后达标排放。 11、配粉:产品需要时,按打包方案规定比例,称量改良剂,按秤添加到混合机中。根据产品需要,将不同基粉仓的基础粉按比例进行搭配,按比例进入到混合机中,进行均匀混合。基础粉经配粉混合或不经配粉混合,通过正压输送系统倒入打包仓。该工段输送、混合过程密闭,落料点产生粉尘由吸风系统收集后经脉冲除尘器处理后达标排放。 12、查筛、磁选:通过成品检查筛最后一次筛理,进一歩清除小麦粉中可能混入的异物,筛网孔径根据不同产品需要选择型号(36GG-72GG或6XX-9XX)。小麦粉在成品检查筛筛理后,再次通过磁场强度在5000高斯以上的磁选器清除可能因设备脱落或磨损造成的磁性金属杂质。该工段输送、查筛、磁选过程密闭,落料点产生粉尘由吸风系统收集后经脉冲除尘器处理后达标排放。 13、计量包装:面粉通过定量包装机,按照不同规格和品种进行计量包装。该工段计量、包装过程密闭,落料点产生粉尘由吸风系统收集后经脉冲除尘器处理后达标排放。 14、入库贮存:不同规格、品种的产品经输送带输送至成品库,分品种和批次码垛存放,要求仓库环境具备通风、干燥、阴凉,并具有防虫鼠设施。 15、外售运输:本项目不配置运输车辆,运输均为物流输送。 | 实际建设情况:1、初清入仓:本项目卸粮入地坑工段,设置卸粮罩棚,卸粮罩棚在卸粮过程关门密闭卸粮,共设置3个卸粮坑,密闭空间设置有吸风系统保持该空间微负压,收集后气体经除尘器处理后达标排放。 地坑内原粮经过刮板机输送至斗式提升机,提升至工作塔通过圆筒筛、磁选、组合筛、风选等设备,初步筛去大的土块、石子、金属异物、绳头、玻璃、秸秆等大杂、小杂和轻杂后,除杂率一般是检验杂质的50%左右。该初清工段输送、筛分均在密闭空间内进行,但物料转输落料会产生一定量粉尘,该部分粉尘通过吸风系统收集后经除尘器处理后达标排放。 初清后原粮经提升机提到仓顶,经刮板机送到指定的仓内,提升机和刮板机均密闭,产生粉尘由吸风系统收集后经脉冲除尘器处理后达标排放。 2、配麦:根据产品特性需要,将不同麦仓、不同品质的原粮按一定比例配比,在仓底打开对应毛麦仓,利用小麦自身重力出仓进入绞龙,经过绞龙混合输送至匀质仓。由匀质仓再次根据产品特性需要配比进入毛麦仓进行再次配麦。该工段输送过程密闭,落料点产生粉尘由吸风系统收集后经脉冲除尘器处理后达标排放。 3、一次清理:经两次配麦后的物料进入一次清理工段,主要包括一清筛选(含磁选)、一清去石(含分级)、一清打麦(含磁选)、一清色选、一清着水、一清润麦工序。 ①一清筛选(含磁选):筛选功能:经过搭配的小麦通过组合筛不同筛孔的筛面,将小麦中的绳头、麦秸秆等大杂和小石子、小泥块等小杂质分出来,并对小麦中麦壳、麦灰、轻质粒通过吸风进行分离,达到小麦进一步清理的作用;磁选功能:原粮通过磁场强度在2000高斯以上的磁选器,去除小麦中的磁性金属杂质。 ②一清去石(含分级):小麦经过去石机,根据小麦和杂质的比重不同,将小麦中的石子有效去除。小麦经过分级机,根据小麦容重的不同,将容重高的和容重低的区分单独利用。 ③一清打麦(含磁选):用打麦机对小麦表面进行摩擦打击,使黏附在小麦表皮和腹沟中的麦毛、麦灰和部分强度较低的杂质得到分离,通过吸风系统将其清除。磁选功能:原粮通过磁场强度在2000高斯以上的磁选器,去除除小麦中的磁性金属杂质。 ④一清色选:根据小麦颜色的差异,利用光电技术将小麦中的霉变粒或赤霉粒分拣出来。 ⑤一清着水:一次清理后小麦经过着水机,着水机将水注入并通过桨叶将水充分均匀与小麦结合,使小麦的皮层韧性增加,胚乳和麦皮的结合力变弱,胚乳间的结合强度下降,从而有利于加工,加水量根据工艺需要设定。 ⑥一清润麦:着水后的小麦进入润麦仓进行静置润麦,根据小麦品质、温度不同,润麦时间一般控制在约16-30小时。 该工段输送、打麦、筛选过程密闭,落料点产生粉尘由吸风系统收集后经脉冲除尘器处理后达标排放。 4、二次清理:一次清理后的物料进入二次清理工段,主要包括二次着水、二次润麦、二次去石(含分级)、二次打麦(含磁选)、二次筛选、雾化着水、二请磁选工序。 ①二次着水:根据一次润麦的水分情况,在入磨前利用着水机进行二次着水。加水量根据工艺需要设定,使小麦适合工艺制粉操作,保证面粉水分符合要求。 ②二次润麦:一次润麦的小麦,根据小麦品质、外界温度,需进行二次润麦,润麦时间约4-10小时,让二次润麦的水分充分滋润小麦表皮,适合工艺制粉操作,保证面粉质量。 ③二次去石:同一次去石,主要是去除小麦中可能残留的小石块。 ④二次打麦(包含磁选):再次用打麦机对小麦表面进行摩擦打击,使黏附在小麦表皮和腹沟中的麦毛、麦灰和部分强度较低的杂质得到分离,通过吸风系统将其清除,润麦后原粮再次通过磁场强度在2000高斯以上的磁选器,去除原粮中可能残留的磁性金属杂质。 ⑤二次筛选:同一次筛选,再次对小麦中可能残留的大杂小杂进行清除。 ⑥雾化着水:二次润麦仓出来的小麦,由于润麦时间较长,小麦表皮变得干燥,在加工过程中表皮容易破碎,为了防止该现象的发生,通过喷雾着水机对通过喷雾着水机的小麦进行喷雾着水,用来湿润小麦表皮,增加表皮的韧性。 ⑦二清磁选:再次通过磁场强度在2000高斯以上的磁选器,去除小麦中可能残留的磁性金属杂质。该工段输送、打麦、筛选过程密闭,落料点产生粉尘由吸风系统收集后经脉冲除尘器处理后达标排放。 5、研磨:利用皮磨、心磨等专用磨粉机将麦粒碾开,分出大皮、麦渣、胚乳、麦心,并将胚乳磨成具有一定细度的小麦粉。该工段输送、磨制过程密闭,落料点产生粉尘由吸风系统收集后经脉冲除尘器处理后达标排放。 6、面粉筛理:小麦经过磨粉机研磨后,获得颗粒大小不同及质量不一的混合物料,利用不同规格的筛理设备将这些混合物分级,然后再研磨、筛理、分级,循环几次,直至获得需要的小麦粉。同时筛分出次粉和麸皮,筛分出次粉产品,通过定量包装机进行计量包装。经高方筛分离出的麸皮由打麸机进行打麸,清理粘附在麸皮的残留面粉,生产系统提取的麸皮产品依据水分指标,烘干或不烘干,烘干热能采用蒸汽。生产系统提取的麸皮产品,通过定量包装机进行计量包装。 该工段输送、筛分、烘干过程密闭,落料点产生粉尘由吸风系统收集后经脉冲除尘器处理后达标排放。 7、清粉、添加:清粉机根据物料的悬浮速度、颗粒不同,对一定的混合物料进行分级,得到较纯的物料送到下道磨粉机研磨。按生产方案指令添加或不添加,通过粉末分配机按规定比例将添加剂添加到粉流中。该工段输送、添加过程密闭,落料点产生粉尘由吸风系统收集后经脉冲除尘器处理后达标排放。 8、面粉收集:将系统所提取的面粉,按质量送入不同的集粉刮板中,通过集粉刮板将不同品质的粉/添加剂进行混合,组成二至五种基础小麦粉。该工段收集、混合、输送过程密闭,落料点产生粉尘由吸风系统收集后经脉冲除尘器处理后达标排放。 9、查筛、磁选:对刮板收集的基础粉通过筛理设备进行筛理,去除小麦粉中可能混入的异物、大的麸片等。查筛后的小麦粉在通过磁场强度在5000高斯以上的磁选器清除可能因设备脱落或磨损造成的磁性金属杂质。该工段输送、查筛、磁选过程密闭,落料点产生粉尘由吸风系统收集后经脉冲除尘器处理后达标排放。 10、正压吹送入粉仓:经过筛查和磁选的基础粉由过滤压缩后的空气正压吹送进入基粉仓,按不同品质分仓贮存。该工段输送过程密闭,落料点产生粉尘由吸风系统收集后经脉冲除尘器处理后达标排放。 11、配粉:产品需要时,按打包方案规定比例,称量改良剂,按秤添加到混合机中。根据产品需要,将不同基粉仓的基础粉按比例进行搭配,按比例进入到混合机中,进行均匀混合。基础粉经配粉混合或不经配粉混合,通过正压输送系统倒入打包仓。该工段输送、混合过程密闭,落料点产生粉尘由吸风系统收集后经脉冲除尘器处理后达标排放。 12、查筛、磁选:通过成品检查筛最后一次筛理,进一歩清除小麦粉中可能混入的异物,筛网孔径根据不同产品需要选择型号(36GG-72GG或6XX-9XX)。小麦粉在成品检查筛筛理后,再次通过磁场强度在5000高斯以上的磁选器清除可能因设备脱落或磨损造成的磁性金属杂质。该工段输送、查筛、磁选过程密闭,落料点产生粉尘由吸风系统收集后经脉冲除尘器处理后达标排放。 13、计量包装:面粉通过定量包装机,按照不同规格和品种进行计量包装。该工段计量、包装过程密闭,落料点产生粉尘由吸风系统收集后经脉冲除尘器处理后达标排放。 14、入库贮存:不同规格、品种的产品经输送带输送至成品库,分品种和批次码垛存放,要求仓库环境具备通风、干燥、阴凉,并具有防虫鼠设施。 15、外售运输:本项目不配置运输车辆,运输均为物流输送。 |
项目生产过程6-9月麦麸烘干不使用蒸汽,采购的麸皮烘干设备技术改进,不需要使用蒸汽。 | 是否属于重大变动:|
环保设施或环保措施
(1)废水:餐厅废水经隔油池预处理后和职工生活废水一起进入化粪池处理,废水处理达到《污水综合排放标准》(GB8978-1996)表4二级标准要求后,再经市政管网进****开发区污水处理厂深度处理后排放至**。综上所述,项目废水不外排,对周围环境影响不大。 (2)废气:本项目运营过程主要为入仓、清麦、制粉、包装等****餐厅油烟。项目生产过程中各工段输送、及加工均在密闭空间进行,落料点产生的粉尘由吸风系统收集后经脉冲除尘器处理达到《大气污染物综合排放标准》(GB16297-1996)表2二级排放标准限值要求后达标排放。筒仓车间粉尘,共设置21套脉冲除尘器,21根排气筒(均大于15米),制粉车间粉尘共设置78套脉冲除尘器,78根排气筒(均大于15米);副产品车间共设置10套脉冲除尘器,10根排气筒。 (3)噪声:本项目主要产噪设备有磨粉机、打麦机、去石机、磁选机、筛分机、风机等,其噪声源强值65-75dB(A)之间,所选设备要采用低噪音设备;机械设备要采取基础减震;所有的窗户加装玻璃等进行密闭;设备与管道的连接采用柔性连接等方式,风机加装消音器等措施。经预测,项目厂界噪声贡献值能满足《厂界环境噪声排放标准》(GB12348-2008)中2类区标准限值(昼间≤60dB(A)、夜间≤50dB(A))。项目建设完成后,牛赵村的声环境预测值能满足《声环境质量标准》(GB3096-2008)2类噪声环境限值(昼间≤60dB(A)、夜间≤50dB(A))。 (4)固废:本项目生产过程中产生的固废主要为秸秆、石子、磁性金属物等杂质,着水机定期更换的滤芯,设备维护更换的废润滑油,清洗齿轮后废煤油和生活垃圾。生产过程中的秸秆、石子、磁性金属物等杂质收集后定期外售;着水机滤芯每年更换一次,滤芯由厂家更换直接带走。项目生产过程产生的危险废物主要有设备维护更换产生的废润滑油,清洗齿轮后的废煤油。分类暂存危废间后,定期交资质单位处置。 | 实际建设情况:1.废水:本项目无生产废水,排放废水主要为职工生活污水和食堂废水,主要污染物为COD、悬浮物、氨氮、动植物油类、五日生化需氧量等。食堂废水经隔油池预处理后和职工生活污水一起进入化粪池处理,废水处理达到《污水综合排放标准》(GB8978-1996)表4二级标准后,再经市政管网进****开发区污水处理厂深度处理后排放至**。餐厅废水经隔油池(30m3,2座)预处理后和职工生活污水一起进入化粪池(30m3,2座)处理,处理达标后再经市政管网进****开发区污水处理厂深度处理后排放至**。 2.废气:本项目废气主要为入仓、清麦、制粉、包装等****餐厅产生的油烟、非甲烷总烃。有组织粉尘经脉冲除尘器处理后执行《大气污染物综合排放标准》(GB16297-1996)表2二级标准,无组织粉尘经自然扩散后执行《大气污染物综合排放标准》(GB16297-1996)表2无组织排放监控浓度限值,餐厅油烟和非甲烷总烃经油烟净化装置处理后执行《餐饮业油烟污染物排放标准》(DB41/1604-2018)表1中型标准限值。本项目共安装高压脉冲袋式除尘器109套,109根排气筒,其中筒仓区共22根(卸粮坑3根、工作塔14根、筒仓3根、匀质仓2根),制粉车间80根,副产品车间7根。 3.噪声:本项目主要噪声源为磨粉机、打麦机、去石机、磁选机、筛分机、风机等生产噪声,其噪声值75~85dB(A)之间。通过采用低噪音设备;机械设备采取基础减振;所有的窗户加装玻璃等进行密闭隔音;设备与管道的连接采用柔性连接等方式,风机加装消音器等措施进行降噪。 4.固体废物:本项目生产过程中产生的固体废物主要为秸秆、石子、磁性金属物等杂质,着水机定期更换的滤芯,设备维护更换的废润滑油,清洗齿轮后废煤油和生活垃圾。 |
除尘器由(筒仓车间粉尘:密闭,21套脉冲除尘器,21根排气筒(高度均高于15米);制粉车间粉尘:密闭,78套脉冲除尘器,78根排气筒(高度均高于15米);副产品车间:密闭,10套脉冲除尘器,10根排气筒(高度均高于15米))变动为(筒仓车间粉尘:密闭,22套脉冲除尘器,22根排气筒(高度均高于15米);制粉车间粉尘:密闭,80套脉冲除尘器,80根排气筒(高度均高于15米);副产品车间:密闭,7套脉冲除尘器,7根排气筒(高度均高于15米)),变动原因:项目根据实际情况进行了设备空间布局优化,副产品除尘器转移至制粉车间;化粪池隔油池由25m3各1座变动为30m3各2座,变动原因:结合实际情况进行优化调整。 | 是否属于重大变动:|
其他
无 | 实际建设情况:无 |
无 | 是否属于重大变动:|
3、污染物排放量
0 | 5865 | 0 | 0 | 0 | 5865 | 5865 | |
0 | 0.176 | 0.176 | 0 | 0 | 0.176 | 0.176 | |
0 | 0.0088 | 0.0088 | 0 | 0 | 0.009 | 0.009 | |
0 | 0 | 0 | 0 | 0 | 0 | 0 | |
0 | 0 | 0 | 0 | 0 | 0 | 0 | |
0 | 0 | 0 | 0 | 0 | 0 | 0 | / |
0 | 0 | 0 | 0 | 0 | 0 | 0 | / |
0 | 0 | 0 | 0 | 0 | 0 | 0 | / |
0 | 20.55 | 76.5 | 0 | 0 | 20.55 | 20.55 | / |
0 | 0 | 0 | 0 | 0 | 0 | 0 | / |
4、环境保护设施落实情况
表1 水污染治理设施
1 | 化粪池隔油池 | 《污水综合排放标准》(GB8978-1996)表4二级标准****开发区污水处理厂收水标准 | 化粪池隔油池 | 2024年5月19日~5月20日验收监测期间,该项目废水总排口废水pH值范围为6.8~7.2;化学需氧量142mg/L;氨氮浓度范围为22.5~24.2mg/L,日均排放浓度为23.0mg/L和24.0mg/L;动植物油类浓度范围为2.66~4.62mg/L,日均排放浓度为4.48mg/L和2.82mg/L;悬浮物浓度范围为33~42mg/L,日均排放浓度为34mg/L和40mg/L;五日生化需氧量27.0~29.0mg/L,日均排放浓度为27.7mg/L和28.0mg/L;废水总排口废水pH、化学需氧量、氨氮、悬浮物、动植物油类、五日生化需氧量均满足《污水综合排放标准》(GB8978-1996)表4二级标准限值要求****开发区污水处理厂收水标准。浓度范围为474~496mg/L,日均排放浓度为480mg/L和483mg/L;氨氮浓度范围为66.7~71.5mg/L,日均排放浓度为68.5mg/L和70.0mg/L;动植物油类浓度范围为3.80~4.78mg/L,日均排放浓度为4.67mg/L和3.93mg/L;悬浮物浓度范围为117~126mg/L,日均排放浓度为124mg/L和119mg/L;五日生化需氧量139~146mg/L,日均排放浓度为142mg/L和144mg/L;其中pH值、动植物油类、悬浮物监测指标满足《污水综合排放标准》(GB8978-1996)表4二级标准,化学需氧量、氨氮、五日生化需氧量监测指标不满足《污水综合排放标准》(GB8978-1996)表4二级标准限值;化学需氧量、悬浮物、五日生化需氧量监测指标满****开发区污水处理厂收水标准,氨氮监测指标不满****开发区污水处理厂收水标准。 超标原因分析:通过与企业核实可知,本项目隔油池、化粪池建成至今未进行过清理,隔油池、化粪池沉积物中包含的有机氮会在厌氧微生物的影响下,可能会通过还原脱氨、水解脱氨及脱水脱氨等过程转化为氨氮释放到污水中,使得污水中COD、氨氮浓度升高,隔油池、化粪池沉积物长期不清理导致废水污染物指标超出《污水综合排放标准》(GB8978-1996)表4二级标准限值要求。 为进一步了解隔油池、化粪池正常运行情况下对废水的处理能力,企业对隔油池和化粪池进行了清理后,我公司于2024年6月14日~6月15日对废水总排口废水再次进行采样分析。废水总排口废水pH值范围为7.2~8.1;化学需氧量浓度范围为116~146mg/L,日均排放浓度为119mg/L和142mg/L;氨氮浓度范围为22.5~24.2mg/L,日均排放浓度为23.0mg/L和24.0mg/L;动植物油类浓度范围为2.66~4.62mg/L,日均排放浓度为4.48mg/L和2.82mg/L;悬浮物浓度范围为33~42mg/L,日均排放浓度为34mg/L和40mg/L;五日生化需氧量27.0~29.0mg/L,日均排放浓度为27.7mg/L和28.0mg/L;废水总排口废水pH、化学需氧量、氨氮、悬浮物、动植物油类、五日生化需氧量均满足《污水综合排放标准》(GB8978-1996)表4二级标准限值要求****开发区污水处理厂收水标准。 |
表2 大气污染治理设施
1 | 布袋除尘器 | 《大气污染物综合排放标准》(GB16297-1996)表2二级标准限值 | 脉冲除尘器 | 验收监测期间,该项目抽测的61套脉冲除尘器排气筒出口颗粒物排放浓度范围为1.0~3.7mg/m3,日均排放浓度范围为1.2~2.9mg/m3;排放速率范围为1.0×10-3~0.089kg/h,日均排放速率范围为1.0×10-3~0.078kg/h;颗粒物无组织排放浓度范围为0.308~0.413mg/m3;颗粒物有组织排放浓度及排放速率和无组织排放浓度均满足《大气污染物综合排放标准》(GB16297-1996)表2标准二级标准限值要求。 | |
2 | 高压静电油烟净化器 | 《餐饮业油烟污染物排放标准》(DB41/1604-2018)表1中型标准限值 | 高压静电油烟净化器 | 项目食堂油烟净化器出口油烟排放浓度范围为0.6~0.7mg/m3,日均排放浓度为0.7mg/m3;非甲烷总烃排放浓度范围为0.46~1.99mg/m3,日均排放浓度为1.01mg/m3和1.85mg/m3;食堂油烟净化器出口油烟和非甲烷总烃均满足《餐饮业油烟污染物排放标准》(DB41/1604-2018)表1中型标准限值要求。 |
表3 噪声治理设施
1 | 采用低噪音设备;机械设备采取基础减振;所有的窗户加装玻璃等进行密闭隔音;设备与管道的连接采用柔性连接等方式,风机加装消音器等措施进行降噪。 | 《工业企业厂界环境噪声排放标准》(GB 12348-2008)表1 2类标准限值 | 采用低噪音设备;机械设备采取基础减振;所有的窗户加装玻璃等进行密闭隔音;设备与管道的连接采用柔性连接等方式,风机加装消音器等措施进行降噪。 | 验收监测期间,厂区西厂界、南厂界噪声昼间监测值范围为52~56dB(A)、夜间监测值范围为46~49(A);昼、夜间噪声监测值均未超出《工业企业厂界环境噪声排放标 准》(GB12348-2008)表1中2类标准限值要求。 |
表4 地下水污染治理设施
1 | 项目化粪池采用防腐防渗结构、并做防渗漏处理。危废暂存间地面按照《危险废物贮存污染控制标准》(GB18597-2001)防渗要求做好防渗。油品库(润滑油、煤油储存)做好防渗措施和防泄漏措施。 | 项目化粪池采用防腐防渗结构、并做防渗漏处理。危废暂存间地面按照《危险废物贮存污染控制标准》(GB18597-2001)防渗要求做好防渗。油品库(润滑油、煤油储存)做好防渗措施和防泄漏措施。 |
表5 固废治理设施
1 | 一般工业固废暂存在固废暂存间,固废暂存间建设应满足《一般工业固体废物贮存和填埋污染控制标准》(GB18599-2020)相关要求,建立一般固体废物台账。 危险废物暂存在危废暂存间定期交资质单位处置,危废暂存建设应满足《危险废物贮存污染控制 标准》(GB18597-2001)及2013年修改单相关要求;制定危险废物危险废物管理制度;建立危险废物台账。 | 本项目的一般固体废物主要为秸秆、石子、磁性金属物等杂质、生活垃圾和废滤芯,危险废物主要为废润滑油和废煤油。其中秸秆、石子、磁性金属物等杂质收集后定期外售,生活垃圾由环卫部门定期清理,废滤芯由厂家直接更换后带走;设备维护更换的废润滑油和清洗齿轮后废煤油由厂区西北角危废暂存间暂存后,定期****公司处置。 |
表6 生态保护设施
1 | 项目建设过程中,在规划工地范围内施工,尽量减少占地面积,施工过程中做好裸露地面覆盖,尽量减少水土流失。施工过程应当保存好表土用于后期绿化。项目建设完成后绿化面积10879平方米,会补偿部分生物量。 | 与环评一致 |
表7 风险设施
1 | 1.润滑油、煤油存放于油品库,油品库地面做防腐蚀、防渗漏处理,并设置泄漏收集装置。 2.废润滑油、废煤油存放于危废暂存间,危废暂存间地面做防腐蚀、防渗漏处理,并设置泄漏收集装置。3. 油品库、危废暂存间设置沙池、灭火器等消防器材。 4.建立危险化学品管理条例和危险废物管理条例,设专人对危废进行管理。 5.建立危废台账,记录危废产生及处置情况,建立档案备查。 6.定期巡视油品库和危废暂存间,便于及时做好防范和及时对存在的环境风险进行排除。 7.建立环境风险应急处置卡,对员工就风险物质理化性质、应急处置过程、应急防护等进行培训,并建立培训档案。 | 与环评一致 |
5、环境保护对策措施落实情况
依托工程
无 | 验收阶段落实情况:无 |
/ |
环保搬迁
无 | 验收阶段落实情况:无 |
/ |
区域削减
无 | 验收阶段落实情况:无 |
/ |
生态恢复、补偿或管理
无 | 验收阶段落实情况:无 |
/ |
功能置换
无 | 验收阶段落实情况:无 |
/ |
其他
无 | 验收阶段落实情况:无 |
/ |
6、工程建设对项目周边环境的影响
/ |
/ |
/ |
/ |
/ |
/ |
7、验收结论
1 | 未按环境影响报告书(表)及其审批部门审批决定要求建设或落实环境保护设施,或者环境保护设施未能与主体工程同时投产使用 |
2 | 污染物排放不符合国家和地方相关标准、环境影响报告书(表)及其审批部门审批决定或者主要污染物总量指标控制要求 |
3 | 环境影响报告书(表)经批准后,该建设项目的性质、规模、地点、采用的生产工艺或者防治污染、防止生态破坏的措施发生重大变动,建设单位未重新报批环境影响报告书(表)或环境影响报告书(表)未经批准 |
4 | 建设过程中造成重大环境污染未治理完成,或者造成重大生态破坏未恢复 |
5 | 纳入排污许可管理的建设项目,无证排污或不按证排污 |
6 | 分期建设、分期投入生产或者使用的建设项目,其环境保护设施防治环境污染和生态破坏的能力不能满足主体工程需要 |
7 | 建设单位因该建设项目违反国家和地方环境保护法律法规受到处罚,被责令改正,尚未改正完成 |
8 | 验收报告的基础资料数据明显不实,内容存在重大缺项、遗漏,或者验收结论不明确、不合理 |
9 | 其他环境保护法律法规规章等规定不得通过环境保护验收 |
不存在上述情况 | |
验收结论 | 合格 |
招标导航更多>>
工程建筑
交通运输
环保绿化
医疗卫生
仪器仪表
水利水电
能源化工
弱电安防
办公文教
通讯电子
机械设备
农林牧渔
市政基建
政府部门
换一批
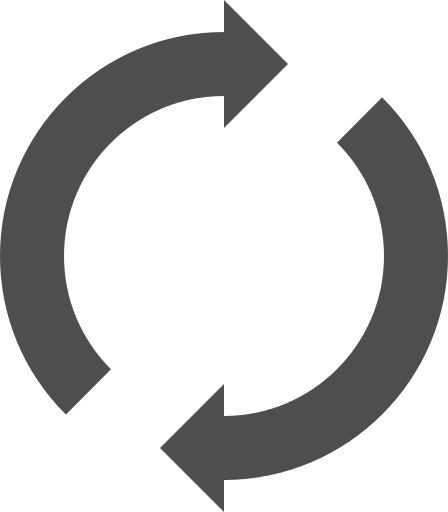