四川盛马化工股份有限公司100万吨/年汽柴油加氢精制装置和20000Nm3/h制氢装置项目
1、建设项目基本信息
企业基本信息
**** | 建设单位代码类型:|
915********3101940 | 建设单位法人:彭志军 |
汤莉君 | 建设单位所在行政区划:**省**市**县 |
****开发区****工业园区) |
建设项目基本信息
****100万吨/年汽柴油加氢精制装置和20000Nm3/h制氢装置项目 | 项目代码:|
建设性质: | |
2021版本:042-精炼石油产品制造;煤炭加工 | 行业类别(国民经济代码):C2511-C2511-原油加工及石油制品制造 |
建设地点: | **省**市**县 **省**市**县 ****开发区****工业园区) |
经度:105.29024 纬度: 30.58478 | ****机关:****环境局 |
环评批复时间: | 2019-06-28 |
遂环评函〔2019〕52号 | 本工程排污许可证编号:**** |
2014-01-19 | 项目实际总投资(万元):58360 |
1421 | 运营单位名称:**** |
915********3101940 | 验收监测(调查)报告编制机构名称:**爱****公司 |
****0100MA6CQF212E | 验收监测单位:**环华****公司 |
****0108MA69GAFA8X | 竣工时间:2024-03-04 |
2024-03-01 | 调试结束时间:2024-03-22 |
2024-07-02 | 验收报告公开结束时间:2024-07-29 |
验收报告公开载体: | https://www.****.com/shownews.asp?id=190 有咨询律师说公示不包括公示发布当天,故公示**至7月30日之后 |
2、工程变动信息
项目性质
技改 | 实际建设情况:技改 |
不涉及重大变动 | 是否属于重大变动:|
规模
本项目为企业现有油品质量升级改造项目,系在现有老厂项目基础上调整产品结构,不扩大加工能力,不新增产品种类。项目建设内容包括100万吨/年汽柴油加氢精制装置和20000Nm3/h制氢装置及配套设施和设备。 | 实际建设情况:本项目为企业现有油品质量升级改造项目,系在现有老厂项目基础上调整产品结构,不扩大加工能力,不新增产品种类。项目建设内容包括100万吨/年汽柴油加氢精制装置和20000Nm3/h制氢装置及配套设施和设备。 |
不涉及重大变动 | 是否属于重大变动:|
生产工艺
1、汽柴油加氢精制装置生产工艺流程 (1)反应部分 盛马化工老厂区燃料处理装置来的直馏柴油和直馏石脑油及催化裂化装置来的催化柴油经管道输送至原料罐储存,再经进料管道输送至装置混合后,通过反冲洗过滤器除去杂质后,再与精制柴油换热换热至100℃,进入原料油缓冲罐。 (2)加氢反应部分 自原料过滤部分来的原料油经原料油缓冲罐后,经加氢进料泵升压至9.5MPa与混合氢混合,混氢原料油与反应流出物经反应流出物/混合进料换热器换热,升温至305℃(末期为330℃);进入反应进料加热炉加热至325℃(末期为363℃),然后自上而下进入加氢精制反应器与加氢改质反应器,在催化剂的作用下,进行加氢脱硫、加氢脱氮、芳烃加氢饱和、选择性开环裂化等反应。反应产物(初期345℃左右,末期380℃左右)经反应流出物/混合进料换热器和反应流出物/低分油换热器冷却至158℃左右,再经反应流出物空冷器和反应流出物水冷器冷却至40℃左右,进入高压分离器进行气、油、水分离。为防止反应产物中NH3和H2S在低温下生成铵盐结晶析出,堵塞空冷器,在反应产物进入空冷器前注入除盐水。 高压分离器分离出的循环氢经循环氢脱硫塔脱除硫化氢后进入循环氢压缩部分。从高压分离器分离出的高分油经减压后进入低压分离器,进一步在低压下将其溶解的气体闪蒸出来。从高压分离器底部分离出的含硫污水减压后送入含硫污水罐,闪蒸后再送出装置。从低压分离器分离出的低分气送出装置,低分油进入分馏部分,含硫污水与高压分离器分离出的含硫污水混合直接进入含硫污水罐。 (3)分馏部分 低分油分别经反应流出物/低分油换热器和精制柴油/低分油换热器加热至258℃左右,进入产品分馏塔。产品分馏塔顶油气分别经产品分馏塔顶空冷器、产品分馏塔顶后冷器冷却至40℃左右后进入产品分馏塔顶回流罐进行气、油、水分离。回流罐分离出来的含硫气体送至装置外;分离出轻烃经分馏塔顶回流泵升压后,一部分作为产品分馏塔顶回流,一部分经粗汽油换热器与石脑油换热后进入稳定塔;底部分离出含硫污水至含硫污水罐。 分馏塔底油一部分经产品分馏塔底重沸炉泵加压后,在产品分馏塔底重沸炉加热至313℃左右后返回产品分馏塔;另一部分经精制柴油泵加压后,经稳定塔底重沸器、精制柴油/低分油换热器、精制柴油/原料油换热器冷却至130℃左右,再经精制柴油空冷器、柴油水冷器冷却至50℃送出装置。 稳定塔顶油气分别经稳定塔顶空冷器、稳定塔顶后冷器冷却后进入稳定塔顶回流罐进行气、油、水分离。回流罐分离出来的含硫气体至干气脱硫塔;分离出轻烃经稳定塔顶回流泵升压后,一部分作为稳定塔顶回流,一部分送出装置;底部分离出含硫污水至含硫污水罐。 稳定塔底油一部分经稳定塔底重沸器加热至至170℃左右返回稳定塔,一部分经石脑油/粗汽油换热器、石脑油空冷器、石脑油后冷器冷却后送至碱洗水洗罐,经过碱洗和水洗后送出装置。 (4)新氢及循环氢压缩部分 高压分离器分离出的循环氢,先经循环氢脱硫塔与贫胺液进行逆向吸收,脱除循环氢中H2S后进入循环氢压缩部分入口分液罐,再由循环氢压缩机升压,同新氢混合后返回反应系统。 制氢装置所产新氢经管道送入装置,在新氢压缩机部分入口分液罐分液后,由新氢压缩机升压至至9.3MPa,再与循环氢混合。混合氢与原料油混合后经反应流出物/混合进料换热器换热,再进入反应进料加热炉。 (5)催化剂硫化流程 硫化采用湿法硫化,以二甲基二硫化物为硫化剂。硫化时,系统内氢气按正常操作路线进行循环。自硫化剂罐来的DMDS与原料油混合后进入,升压后经进入加热炉,按催化剂硫化升温曲线升温至所要求的温度,通过加氢精制反应器及加氢改质反应器催化剂床层进行硫化反应。自加氢改质反应器出来的硫化油和循环氢经换热器和冷却器冷却后,进入高压分离器闪蒸分离。气相进入循环氢压缩部分进行氢气循环。液相经调节阀减压后进入低压分离器闪蒸分离,气相送出装置,液相循环回到。 (6)干气脱硫流程 来自低压分离器、产品分馏塔回流罐及稳定塔顶回流罐的干气通过干气脱硫塔脱硫后,净化干气进入低压瓦斯管网。 2、制氢装置生产工艺流程 以天然气为原料,采用烃类水蒸气转化及PSA提氢的工艺技术生产纯度为99.9%的氢气,装置规模为20000Nm3/h,所产的工业氢去100×104t/a汽柴油加氢精制装置。 装置主要由造气和PSA两部分组成,造气部分包括原料压缩预热、原料加氢脱硫、蒸汽转化及中温变换、中变气换热冷却分液、酸性水处理及蒸汽发生。 (1)进料系统 来自装置外的0.6MPa(G)天然气进入原料气缓冲罐,经原料气压缩机升压至3.1MPa(G)后进入原料预热炉,预热至380℃左右进入脱硫部分。 (2)脱硫部分 进入脱硫部分的原料气,首先进入绝热加氢反应器,在该反应器中有机硫加氢转化为硫化氢,然后进入脱硫反应器,在氧化锌脱硫反应器中首先进入脱氯段脱除原料中的氯,最后进入氧化锌脱硫段,在此氧化锌与硫化氢发生脱硫反应。精制后的气体中硫含量小于0.5ppm,氯小于0.2ppm进入转化部分。 (3)转化部分 精制后的原料气按水碳比3.5与水蒸汽混合,再经转化炉对流段预热至500℃,进入转化炉辐射段。在催化剂的作用下,发生复杂的水蒸汽转化反应,从而生产出氢气、甲烷、一氧化碳、二氧化碳和水的平衡混合物。 (4)变换部分 由转化部分来的约360℃的转化气进入中温变换反应器,在催化剂的作用下发生变换反应:CO+H2O→CO2+H2 将变换气中CO含量降至3%左右,同时继续生产氢气。中变气经过锅炉给水换热器、除盐水****回收部分余热后,再经中变气空冷器及水冷却器冷却至40℃,经分水后进入PSA部分。 (5)热回收及产汽系统 1)除盐水除氧系统 来自装置外的除盐水经过除盐水预热器预热至100℃左右,与酸性水汽提塔来的净化水混合后进入装置除氧器,除氧水经过中压锅炉给水泵升压后送至中压产汽系统。 2)中压产汽系统 来自中压锅炉给水泵的除氧水经过锅炉给水第一预热器和锅炉给水第二预热器换热到250℃左右进入中压汽水分离器中。饱和水通过自然循环的方式分别经过转化炉对流段的蒸发段及转化气蒸汽发生器发生3.5MPa的饱和蒸汽。所产生的蒸汽在转化炉的对流段过热到450℃,大部分作为工艺蒸汽使用;多余部分出装置。 3)加药系统及排污系统 固体的磷酸三钠加入到磷酸盐加药装置的溶药箱中,引入除氧水溶解。然后用磷酸盐加药装置的中压加药泵将药液送至中压汽水分离器内。为了减少系统热损失,设置了连续排污扩容器和定期排污扩容器,排污水送入连排,扩容蒸汽进入除氧器,污水进入定排,并加入新鲜水冷却至50℃以下排放。 (6)PSA部分 来自变换部分的中变气,自塔底进入吸附塔A~J中正处于吸附工况的塔(始终同时有两台),在其中多种吸附剂的依次选择吸附下,一次性除去氢以外的几乎所有杂质,获得纯度大于99.9%的产品氢气,经压力调节系统稳压后送出界区。 当吸附剂吸附饱和后,通过程控阀门切换至其它塔吸附,吸附饱和的塔则转入再生过程。在再生过程中,吸附塔首先经过连续四次均压降压过程尽量回收塔内死空间氢气,然后通过顺放步序将剩余的大部分氢气放入顺放气罐(用作以后冲洗步序的冲洗气源),再通过逆放和冲洗两个步序使被吸附杂质解吸出来。逆放解吸气进入解吸气缓冲罐,冲洗解吸气进入解吸气缓冲罐,然后经调节阀调节混合后稳定地送往转化炉用作燃气。 (7)净化水的回用 由各中变气分液罐排出的工艺冷凝水,在酸性水汽提塔内用蒸汽汽提净化后,经酸性水汽提塔底泵升压后,取样化验合格后送往装置内除氧器作为锅炉给水回用。 | 实际建设情况:1、汽柴油加氢精制装置生产工艺流程 (1)反应部分 盛马化工老厂区燃料处理装置来的直馏柴油和直馏石脑油及催化裂化装置来的催化柴油经管道输送至原料罐储存,再经进料管道输送至装置混合后,通过反冲洗过滤器除去杂质后,再与精制柴油换热换热至100℃,进入原料油缓冲罐。 (2)加氢反应部分 自原料过滤部分来的原料油经原料油缓冲罐后,经加氢进料泵升压至9.5MPa与混合氢混合,混氢原料油与反应流出物经反应流出物/混合进料换热器换热,升温至305℃(末期为330℃);进入反应进料加热炉加热至325℃(末期为363℃),然后自上而下进入加氢精制反应器与加氢改质反应器,在催化剂的作用下,进行加氢脱硫、加氢脱氮、芳烃加氢饱和、选择性开环裂化等反应。反应产物(初期345℃左右,末期380℃左右)经反应流出物/混合进料换热器和反应流出物/低分油换热器冷却至158℃左右,再经反应流出物空冷器和反应流出物水冷器冷却至40℃左右,进入高压分离器进行气、油、水分离。为防止反应产物中NH3和H2S在低温下生成铵盐结晶析出,堵塞空冷器,在反应产物进入空冷器前注入除盐水。 高压分离器分离出的循环氢经循环氢脱硫塔脱除硫化氢后进入循环氢压缩部分。从高压分离器分离出的高分油经减压后进入低压分离器,进一步在低压下将其溶解的气体闪蒸出来。从高压分离器底部分离出的含硫污水减压后送入含硫污水罐,闪蒸后再送出装置。从低压分离器分离出的低分气送出装置,低分油进入分馏部分,含硫污水与高压分离器分离出的含硫污水混合直接进入含硫污水罐。 (3)分馏部分 低分油分别经反应流出物/低分油换热器和精制柴油/低分油换热器加热至258℃左右,进入产品分馏塔。产品分馏塔顶油气分别经产品分馏塔顶空冷器、产品分馏塔顶后冷器冷却至40℃左右后进入产品分馏塔顶回流罐进行气、油、水分离。回流罐分离出来的含硫气体送至装置外;分离出轻烃经分馏塔顶回流泵升压后,一部分作为产品分馏塔顶回流,一部分经粗汽油换热器与石脑油换热后进入稳定塔;底部分离出含硫污水至含硫污水罐。 分馏塔底油一部分经产品分馏塔底重沸炉泵加压后,在产品分馏塔底重沸炉加热至313℃左右后返回产品分馏塔;另一部分经精制柴油泵加压后,经稳定塔底重沸器、精制柴油/低分油换热器、精制柴油/原料油换热器冷却至130℃左右,再经精制柴油空冷器、柴油水冷器冷却至50℃送出装置。 稳定塔顶油气分别经稳定塔顶空冷器、稳定塔顶后冷器冷却后进入稳定塔顶回流罐进行气、油、水分离。回流罐分离出来的含硫气体至干气脱硫塔;分离出轻烃经稳定塔顶回流泵升压后,一部分作为稳定塔顶回流,一部分送出装置;底部分离出含硫污水至含硫污水罐。 稳定塔底油一部分经稳定塔底重沸器加热至至170℃左右返回稳定塔,一部分经石脑油/粗汽油换热器、石脑油空冷器、石脑油后冷器冷却后送至碱洗水洗罐,经过碱洗和水洗后送出装置。 (4)新氢及循环氢压缩部分 高压分离器分离出的循环氢,先经循环氢脱硫塔与贫胺液进行逆向吸收,脱除循环氢中H2S后进入循环氢压缩部分入口分液罐,再由循环氢压缩机升压,同新氢混合后返回反应系统。 制氢装置所产新氢经管道送入装置,在新氢压缩机部分入口分液罐分液后,由新氢压缩机升压至至9.3MPa,再与循环氢混合。混合氢与原料油混合后经反应流出物/混合进料换热器换热,再进入反应进料加热炉。 (5)催化剂硫化流程 硫化采用湿法硫化,以二甲基二硫化物为硫化剂。硫化时,系统内氢气按正常操作路线进行循环。自硫化剂罐来的DMDS与原料油混合后进入,升压后经进入加热炉,按催化剂硫化升温曲线升温至所要求的温度,通过加氢精制反应器及加氢改质反应器催化剂床层进行硫化反应。自加氢改质反应器出来的硫化油和循环氢经换热器和冷却器冷却后,进入高压分离器闪蒸分离。气相进入循环氢压缩部分进行氢气循环。液相经调节阀减压后进入低压分离器闪蒸分离,气相送出装置,液相循环回到。 (6)干气脱硫流程 来自低压分离器、产品分馏塔回流罐及稳定塔顶回流罐的干气通过干气脱硫塔脱硫后,净化干气进入低压瓦斯管网。 2、制氢装置生产工艺流程 以天然气为原料,采用烃类水蒸气转化及PSA提氢的工艺技术生产纯度为99.9%的氢气,装置规模为20000Nm3/h,所产的工业氢去100×104t/a汽柴油加氢精制装置。 装置主要由造气和PSA两部分组成,造气部分包括原料压缩预热、原料加氢脱硫、蒸汽转化及中温变换、中变气换热冷却分液、酸性水处理及蒸汽发生。 (1)进料系统 来自装置外的0.6MPa(G)天然气进入原料气缓冲罐,经原料气压缩机升压至3.1MPa(G)后进入原料预热炉,预热至380℃左右进入脱硫部分。 (2)脱硫部分 进入脱硫部分的原料气,首先进入绝热加氢反应器,在该反应器中有机硫加氢转化为硫化氢,然后进入脱硫反应器,在氧化锌脱硫反应器中首先进入脱氯段脱除原料中的氯,最后进入氧化锌脱硫段,在此氧化锌与硫化氢发生脱硫反应。精制后的气体中硫含量小于0.5ppm,氯小于0.2ppm进入转化部分。 (3)转化部分 精制后的原料气按水碳比3.5与水蒸汽混合,再经转化炉对流段预热至500℃,进入转化炉辐射段。在催化剂的作用下,发生复杂的水蒸汽转化反应,从而生产出氢气、甲烷、一氧化碳、二氧化碳和水的平衡混合物。 (4)变换部分 由转化部分来的约360℃的转化气进入中温变换反应器,在催化剂的作用下发生变换反应:CO+H2O→CO2+H2 将变换气中CO含量降至3%左右,同时继续生产氢气。中变气经过锅炉给水换热器、除盐水****回收部分余热后,再经中变气空冷器及水冷却器冷却至40℃,经分水后进入PSA部分。 (5)热回收及产汽系统 1)除盐水除氧系统 来自装置外的除盐水经过除盐水预热器预热至100℃左右,与酸性水汽提塔来的净化水混合后进入装置除氧器,除氧水经过中压锅炉给水泵升压后送至中压产汽系统。 2)中压产汽系统 来自中压锅炉给水泵的除氧水经过锅炉给水第一预热器和锅炉给水第二预热器换热到250℃左右进入中压汽水分离器中。饱和水通过自然循环的方式分别经过转化炉对流段的蒸发段及转化气蒸汽发生器发生3.5MPa的饱和蒸汽。所产生的蒸汽在转化炉的对流段过热到450℃,大部分作为工艺蒸汽使用;多余部分出装置。 3)加药系统及排污系统 固体的磷酸三钠加入到磷酸盐加药装置的溶药箱中,引入除氧水溶解。然后用磷酸盐加药装置的中压加药泵将药液送至中压汽水分离器内。为了减少系统热损失,设置了连续排污扩容器和定期排污扩容器,排污水送入连排,扩容蒸汽进入除氧器,污水进入定排,并加入新鲜水冷却至50℃以下排放。 (6)PSA部分 来自变换部分的中变气,自塔底进入吸附塔A~J中正处于吸附工况的塔(始终同时有两台),在其中多种吸附剂的依次选择吸附下,一次性除去氢以外的几乎所有杂质,获得纯度大于99.9%的产品氢气,经压力调节系统稳压后送出界区。 当吸附剂吸附饱和后,通过程控阀门切换至其它塔吸附,吸附饱和的塔则转入再生过程。在再生过程中,吸附塔首先经过连续四次均压降压过程尽量回收塔内死空间氢气,然后通过顺放步序将剩余的大部分氢气放入顺放气罐(用作以后冲洗步序的冲洗气源),再通过逆放和冲洗两个步序使被吸附杂质解吸出来。逆放解吸气进入解吸气缓冲罐,冲洗解吸气进入解吸气缓冲罐,然后经调节阀调节混合后稳定地送往转化炉用作燃气。 (7)净化水的回用 由各中变气分液罐排出的工艺冷凝水,在酸性水汽提塔内用蒸汽汽提净化后,经酸性水汽提塔底泵升压后,取样化验合格后送往装置内除氧器作为锅炉给水回用。 |
不涉及重大变动 | 是否属于重大变动:|
环保设施或环保措施
1、废水 本项目含硫废水和脱硫富胺液进入硫磺回收装置处理,****水厂内回用,溶剂再生塔塔底再生贫胺液循环使用;低含油工艺废水、公辅及环保设施排水和生活****处理站隔油生化处理。****处理站出水达《石油炼制工业污染物排放标准》(GB31570-2015)表2间****处理厂设计进水标准后经排****处理厂,****处理厂处理达标后排入郪江。 2、废气 1)锅炉燃烧烟气 本项目**2台35t/h燃气锅炉,采用天然气及自产干气作为燃料,天然气为清洁能源,自产干气经脱硫处理,其燃烧废气中污染物浓度较低,污染物排放量少,同时采用低氮燃烧,该工艺为《排污许可证申请与核发技术规范 石化工业》(HJ853-2017)中锅炉烟气治理的可行技术,符合技术规范要求,其污染物排放可满足《锅炉大气污染物排放标准》(GB13271-2014)表3特别排放限值要求。 2)工艺加热炉烟气 本项目汽柴油加氢精制装置设置1台加热炉和1台重沸炉,采用天然气和自产干气为燃料;制氢装置设置1台转化炉采用天然气和PSA尾气为燃料,天然气为清洁能源,自产干气经脱硫处理,其燃烧废气中污染物浓度较低,污染物排放量少,同时采用低氮燃烧,该工艺为《污染源源强核算技术指南 石油炼制工业》(HJ982-2018)和《排污许可证申请与核发技术规范 石化工业》(HJ853-2017)中工艺加热炉烟气治理的可行技术,符合技术规范要求,污染物排放可满足《石油炼制工业污染物排放标准》(GB31570-2015)表4特别排放限值要求。 3)酸性气治理措施 本项目硫磺回收装置硫磺回收单元采用克劳斯工艺回收酸性气中硫,制硫尾气经焚烧炉焚烧处理,尾气中残存的硫化氢及其它硫化物几乎完全转化成二氧化硫,焚烧后的高温烟气经余热回收和换热后温度降至360℃,再经碱洗处理后烟气通过80m高烟囱排放。因此,本项目酸性气处理工艺为“两级克劳斯硫回收+焚烧+碱洗”,为《污染源源强核算技术指南 石油炼制工业》(HJ982-2018)和《排污许可证申请与核发技术规范 石化工业》(HJ853-2017)中酸性气回收装置治理的可行技术,符合技术规范要求,且碱洗技术适用于执行特别排放限值的污染源。因此,本项目硫磺回收装置尾气污染物排放满足《石油炼制工业污染物排放标准》(GB31570-2015)表4标准和《恶臭污染物排放标准》(GB14554-93)标准要求。 4****处理站废气治理措施 ****处理站工艺特点,共设2套废气处理装置,其中1套为污水预处理段高浓度废气除臭系统,实际采用“碱洗+催化燃烧”工艺;1套为污水生化段低浓度废气除臭系统,采用“碱洗+生物除臭+活性炭吸附”工艺。 1、高浓度废气除臭系统 高浓度除臭系统为预处理段工艺的除臭,主要包括集水池、调节罐、隔油池、气浮池、浓缩罐和低温干化设备,集水池、隔油池和气浮池的池体上部加盖,调节罐、浓缩罐和低温干化设备密闭负压收集废气,废气通过管道输送至除臭单元,采用“碱洗+催化燃烧”工艺,设计风量为8000m3/h。 低浓度除臭系统为生化段工艺的除臭,主要包括缺氧池、MBBR池、好氧池筑物的除臭,生化池的池体上部采取加盖收集废气,通过管道输送至除臭单元,采用“碱洗+生物除臭+活性炭吸附”工艺。 5)无组织排放废气治理措施 按照《石油炼制工业污染物排放标准》(GB31571-2015)中5.3 设备与管线组件泄漏污染控制要求和5.4 其他污染控制要求对项目的生产设施和生产过程实施全过程控制,最大程度降低挥发性有机物的无组织排放。 1、设备与管线组件泄漏污染控制措施 1)进行检漏的设备与管线组件 在运营期企业应开展设备与管线组件泄漏检测工作,应开展检漏的设备与管线组建包括泵、压缩机、阀门、开口阀或开口管线、法兰及其连接件等。 2)检测周期 根据设备与管件组件的类型,采用不同的泄漏检测周期: ①泵、压缩机、阀门、开口阀或开口管线、气体/蒸汽泄压设备、取样连接系统每3个月检测一次; ②法兰及其他连接件、其他密封设备每6个月检测一次; ③对于挥发性有机物流经的初次开工开始运转的设备和管线组件,在开工后30日内进行第一次检测; ④挥发性有机液体流经的设备和管线组件每周进行目视观察,检查其密封处是否出现滴液迹象。 3)泄漏的认定 ①有机气体和挥发性有机液体流经的设备与管线组件,采用氢火焰离子化检测仪(以甲烷或丙烷为校正气体),泄漏检测值大于等于2000umol/mol; ②其他挥发性有机物流经的设备与管线组件,采用氢火焰离子化检测仪(以甲烷或丙烷为校正气体),泄漏检测值大于等于500umol/mol; 4)泄漏修复 ①当检测到泄漏时,应尽快修复,要求不晚于发现泄漏后15日; ②首次维修要求在检测到泄漏后5日内,首次维修包括以下的相关设施:拧紧密封螺母或压盖、在设计压力及温度下密封冲洗; ③若检测到泄漏后,在不关闭工艺单元时,再15日内进行维修技术上不可行,则可以延迟维修,但不应晚于最近一个停工期。 4)记录 泄漏检测时记录检测时间、检测仪器读数;修复时记录修复时间和确认完成 修复的时间,记录修复后检测仪器读数,记录归档保存至少1年以上。 2、废水集输、储存和处理设施的污染控制措施 本项目装置区含油污水收集装置和处理装置应加盖密闭,挥发烃类气体和恶臭气体根据气浓度由管线送至相应除臭系统,处理达标后排放。 3、储罐污染控制措施 本项目**3座储罐区,分别为原料油罐区、汽油罐区和柴油罐区,原料油为外浮顶罐、汽柴油为内浮顶罐,内浮顶罐内浮盘与管壁之间采用了高效密封方式,浮盘上的开口、缝隙密封设施,以及浮盘与管壁之间的密封设施在工作状态保持密闭。 企业应开展LDARs工作,当检测到密封设施有泄漏的情况下,可在不关闭工艺单元的条件下,由检维修专业人员立即进行维修堵漏。 企业应建立浮盘定期检查制度,至少每6个月检测一次,并记录浮盘密封设施的状态,记录归档封存。 4、装卸过程 密闭设置油气回收和处置装置,废气排放可满足表4规定限值。 5、火炬系统的污染控制措施 本项目厂区设置火炬气回收装置,正常情况下装置区不凝气/干气经火炬气回收装置脱硫净化后由管道输送入全厂高压瓦斯系统,作为燃料气使用。装置在开停工及事故状态下放空的可燃气体以及球罐放空的可燃气体排放燃烧。企业严格按照相关规定要求进行监测,并记录火炬的工作状态等。 6、采样、检维修过程污染控制措施 本项目各装置采样口为密闭,项目输送、储存、含油废水收集池和污染雨水收集池等生产设施,在检维修时清扫气接入装置可燃气体收集管网,送至火炬系统处理。 7、大气防护距离的划定 为了确保大气环境防护区域之外叠加后的短期浓度也符合环境质量标准,项目建成后全厂以最远垂直距离(456.55m)划定大气防护距离,****政府《关于项目大气防护距离范围内居民搬迁的函》(大府函[2019]67号):“大气防护距离内分布有**镇**二小区163户650人、**村居民54户162人,其中**二小区已纳****园区管委会负责搬迁(大工管委函[2018]50号),**村居民54户162****政府负责项目投产前完成搬迁工作”。企业承诺在大气防护距离内现有居民搬迁完成前不投入生产(川盛化[2019]62号),目前大气防护距离范围内居民已搬迁。 通过划定大气环境防护距离,确保了大气环境防护区域之外叠加后的短期浓度也符合环境质量标准。 8、卫生防护距离的划定 本项目选址于******经济开发区内,根据《******局关于****公司厂区所在区域地形情况说明的函》(大国土资[2014]13号),项目所在区域属丘陵地形,可以满足《石油加工业卫生防护距离》(GB8195-2011)中定义的复杂地形。按照《石油加工业卫生防护距离》(GB8195-2011)4.2规定“地处复杂地形条件下的石油加工企业卫生防护距离的确定方法,参照《制定地方大气污染物排放标准的技术方法》(GB/T3840-1991)中的7.6规定:“地处复杂地形条件下的卫生防护距离,应根据大气环境质量评价报告,由建设单位主管部门与建设项目所在省、市、自治区的卫生与环境保护主管部门共同确定。”******管理委员会、****环境局、大****科学技术局****卫生健康局关于《****100万吨/年汽柴油加氢精制装置和20000Nm3/h制氢装置划定卫生防护距离的情况说明》认可项目环评报告中计算确定的卫生防护距离。 根据无组织污染物排放情况,本评价分别以以汽柴油加氢精制装置、硫磺回收装置区、****处理站边界向外分别划定200m、200m、200m和100m卫生防护距离。 通过划设卫生防护距离可避免因无组织排放而影响周边环境敏感点。 目前项目设定的防护距离内已按要求进行搬迁。 3、噪声 本项目建成后生产过程中产生的噪声主要为设备噪声,产生噪声的设备主要为加热炉、转化炉、压缩机、风机、冷水塔及各类生产用泵等,声源强度在85~95dB(A)之间。项目除了尽量选用低噪声的设备外,主要采取的降噪措施是针对设备采取消声、基础减振等措施,再通过利用距离衰减和厂区外绿化带阻隔,可使厂界噪声满足《工业企业厂界环境噪声排放标准》(GB12348-2008)3类标准要求。项目噪声治理措施技术经济可行。 4、固废 本项目固体废物包括:各类废催化剂、废保护剂、废吸附剂、废脱氯剂、废瓷球、脱硫固废、含油废渣、污水处理站污泥、罐底残渣、废油以及生活垃圾等。危险废物送资质单位处置,生活垃圾由当地环保部门统一清运。 | 实际建设情况:1、废水 本项目含硫废水和脱硫富胺液进入硫磺回收装置处理,****水厂内回用,溶剂再生塔塔底再生贫胺液循环使用;低含油工艺废水、公辅及环保设施排水和生活****处理站隔油生化处理。****处理站出水达《石油炼制工业污染物排放标准》(GB31570-2015)表2间****处理厂设计进水标准后经排****处理厂,****处理厂处理达标后排入郪江。 2、废气 1)锅炉燃烧烟气 本项目**2台35t/h燃气锅炉,采用天然气及自产干气作为燃料,天然气为清洁能源,自产干气经脱硫处理,其燃烧废气中污染物浓度较低,污染物排放量少,同时采用低氮燃烧,该工艺为《排污许可证申请与核发技术规范 石化工业》(HJ853-2017)中锅炉烟气治理的可行技术,符合技术规范要求,其污染物排放可满足《锅炉大气污染物排放标准》(GB13271-2014)表3特别排放限值要求。 2)工艺加热炉烟气 本项目汽柴油加氢精制装置设置1台加热炉和1台重沸炉,采用天然气和自产干气为燃料;制氢装置设置1台转化炉采用天然气和PSA尾气为燃料,天然气为清洁能源,自产干气经脱硫处理,其燃烧废气中污染物浓度较低,污染物排放量少,同时采用低氮燃烧,该工艺为《污染源源强核算技术指南 石油炼制工业》(HJ982-2018)和《排污许可证申请与核发技术规范 石化工业》(HJ853-2017)中工艺加热炉烟气治理的可行技术,符合技术规范要求,污染物排放可满足《石油炼制工业污染物排放标准》(GB31570-2015)表4特别排放限值要求。 3)酸性气治理措施 本项目硫磺回收装置硫磺回收单元采用克劳斯工艺回收酸性气中硫,制硫尾气经焚烧炉焚烧处理,尾气中残存的硫化氢及其它硫化物几乎完全转化成二氧化硫,焚烧后的高温烟气经余热回收和换热后温度降至360℃,再经碱洗处理后烟气通过80m高烟囱排放。因此,本项目酸性气处理工艺为“两级克劳斯硫回收+焚烧+碱洗”,为《污染源源强核算技术指南 石油炼制工业》(HJ982-2018)和《排污许可证申请与核发技术规范 石化工业》(HJ853-2017)中酸性气回收装置治理的可行技术,符合技术规范要求,且碱洗技术适用于执行特别排放限值的污染源。因此,本项目硫磺回收装置尾气污染物排放满足《石油炼制工业污染物排放标准》(GB31570-2015)表4标准和《恶臭污染物排放标准》(GB14554-93)标准要求。 4****处理站废气治理措施 ****处理站工艺特点,共设2套废气处理装置,其中1套为污水预处理段高浓度废气除臭系统,实际采用“碱洗+催化燃烧”工艺;1套为污水生化段低浓度废气除臭系统,采用“碱洗+生物除臭+活性炭吸附”工艺。 1、高浓度废气除臭系统 高浓度除臭系统为预处理段工艺的除臭,主要包括集水池、调节罐、隔油池、气浮池、浓缩罐和低温干化设备,集水池、隔油池和气浮池的池体上部加盖,调节罐、浓缩罐和低温干化设备密闭负压收集废气,废气通过管道输送至除臭单元,采用“碱洗+催化燃烧”工艺,设计风量为8000m3/h。 低浓度除臭系统为生化段工艺的除臭,主要包括缺氧池、MBBR池、好氧池筑物的除臭,生化池的池体上部采取加盖收集废气,通过管道输送至除臭单元,采用“碱洗+生物除臭+活性炭吸附”工艺。 5)无组织排放废气治理措施 按照《石油炼制工业污染物排放标准》(GB31571-2015)中5.3 设备与管线组件泄漏污染控制要求和5.4 其他污染控制要求对项目的生产设施和生产过程实施全过程控制,最大程度降低挥发性有机物的无组织排放。 1、设备与管线组件泄漏污染控制措施 1)进行检漏的设备与管线组件 在运营期企业应开展设备与管线组件泄漏检测工作,应开展检漏的设备与管线组建包括泵、压缩机、阀门、开口阀或开口管线、法兰及其连接件等。 2)检测周期 根据设备与管件组件的类型,采用不同的泄漏检测周期: ①泵、压缩机、阀门、开口阀或开口管线、气体/蒸汽泄压设备、取样连接系统每3个月检测一次; ②法兰及其他连接件、其他密封设备每6个月检测一次; ③对于挥发性有机物流经的初次开工开始运转的设备和管线组件,在开工后30日内进行第一次检测; ④挥发性有机液体流经的设备和管线组件每周进行目视观察,检查其密封处是否出现滴液迹象。 3)泄漏的认定 ①有机气体和挥发性有机液体流经的设备与管线组件,采用氢火焰离子化检测仪(以甲烷或丙烷为校正气体),泄漏检测值大于等于2000umol/mol; ②其他挥发性有机物流经的设备与管线组件,采用氢火焰离子化检测仪(以甲烷或丙烷为校正气体),泄漏检测值大于等于500umol/mol; 4)泄漏修复 ①当检测到泄漏时,应尽快修复,要求不晚于发现泄漏后15日; ②首次维修要求在检测到泄漏后5日内,首次维修包括以下的相关设施:拧紧密封螺母或压盖、在设计压力及温度下密封冲洗; ③若检测到泄漏后,在不关闭工艺单元时,再15日内进行维修技术上不可行,则可以延迟维修,但不应晚于最近一个停工期。 4)记录 泄漏检测时记录检测时间、检测仪器读数;修复时记录修复时间和确认完成 修复的时间,记录修复后检测仪器读数,记录归档保存至少1年以上。 2、废水集输、储存和处理设施的污染控制措施 本项目装置区含油污水收集装置和处理装置应加盖密闭,挥发烃类气体和恶臭气体根据气浓度由管线送至相应除臭系统,处理达标后排放。 3、储罐污染控制措施 本项目**3座储罐区,分别为原料油罐区、汽油罐区和柴油罐区,原料油为外浮顶罐、汽柴油为内浮顶罐,内浮顶罐内浮盘与管壁之间采用了高效密封方式,浮盘上的开口、缝隙密封设施,以及浮盘与管壁之间的密封设施在工作状态保持密闭。 企业应开展LDARs工作,当检测到密封设施有泄漏的情况下,可在不关闭工艺单元的条件下,由检维修专业人员立即进行维修堵漏。 企业应建立浮盘定期检查制度,至少每6个月检测一次,并记录浮盘密封设施的状态,记录归档封存。 4、装卸过程 密闭设置油气回收和处置装置,废气排放可满足表4规定限值。 5、火炬系统的污染控制措施 本项目厂区设置火炬气回收装置,正常情况下装置区不凝气/干气经火炬气回收装置脱硫净化后由管道输送入全厂高压瓦斯系统,作为燃料气使用。装置在开停工及事故状态下放空的可燃气体以及球罐放空的可燃气体排放燃烧。企业严格按照相关规定要求进行监测,并记录火炬的工作状态等。 6、采样、检维修过程污染控制措施 本项目各装置采样口为密闭,项目输送、储存、含油废水收集池和污染雨水收集池等生产设施,在检维修时清扫气接入装置可燃气体收集管网,送至火炬系统处理。 7、大气防护距离的划定 为了确保大气环境防护区域之外叠加后的短期浓度也符合环境质量标准,项目建成后全厂以最远垂直距离(456.55m)划定大气防护距离,****政府《关于项目大气防护距离范围内居民搬迁的函》(大府函[2019]67号):“大气防护距离内分布有**镇**二小区163户650人、**村居民54户162人,其中**二小区已纳****园区管委会负责搬迁(大工管委函[2018]50号),**村居民54户162****政府负责项目投产前完成搬迁工作”。企业承诺在大气防护距离内现有居民搬迁完成前不投入生产(川盛化[2019]62号),目前大气防护距离范围内居民已搬迁。 通过划定大气环境防护距离,确保了大气环境防护区域之外叠加后的短期浓度也符合环境质量标准。 8、卫生防护距离的划定 本项目选址于******经济开发区内,根据《******局关于****公司厂区所在区域地形情况说明的函》(大国土资[2014]13号),项目所在区域属丘陵地形,可以满足《石油加工业卫生防护距离》(GB8195-2011)中定义的复杂地形。按照《石油加工业卫生防护距离》(GB8195-2011)4.2规定“地处复杂地形条件下的石油加工企业卫生防护距离的确定方法,参照《制定地方大气污染物排放标准的技术方法》(GB/T3840-1991)中的7.6规定:“地处复杂地形条件下的卫生防护距离,应根据大气环境质量评价报告,由建设单位主管部门与建设项目所在省、市、自治区的卫生与环境保护主管部门共同确定。”******管理委员会、****环境局、大****科学技术局****卫生健康局关于《****100万吨/年汽柴油加氢精制装置和20000Nm3/h制氢装置划定卫生防护距离的情况说明》认可项目环评报告中计算确定的卫生防护距离。 根据无组织污染物排放情况,本评价分别以以汽柴油加氢精制装置、硫磺回收装置区、****处理站边界向外分别划定200m、200m、200m和100m卫生防护距离。 通过划设卫生防护距离可避免因无组织排放而影响周边环境敏感点。 目前项目设定的防护距离内已按要求进行搬迁。 3、噪声 本项目建成后生产过程中产生的噪声主要为设备噪声,产生噪声的设备主要为加热炉、转化炉、压缩机、风机、冷水塔及各类生产用泵等,声源强度在85~95dB(A)之间。项目除了尽量选用低噪声的设备外,主要采取的降噪措施是针对设备采取消声、基础减振等措施,再通过利用距离衰减和厂区外绿化带阻隔,可使厂界噪声满足《工业企业厂界环境噪声排放标准》(GB12348-2008)3类标准要求。项目噪声治理措施技术经济可行。 4、固废 本项目固体废物包括:各类废催化剂、废保护剂、废吸附剂、废脱氯剂、废瓷球、脱硫固废、含油废渣、污水处理站污泥、罐底残渣、废油以及生活垃圾等。目前企业已经与******公司、**兴蓉****公司签订危废协议处置危险废物,生活垃圾由当地环卫部门统一清运。 |
不涉及重大变动 | 是否属于重大变动:|
其他
一、根据环评单位现场调查,****工程部份已开工建设,至今未投入运营。你公司应严格按照报告书中所列建设项目的地点、规模、性质、采用生产工艺以及拟采取的环境保护措施建设和运行,确保对环境的不利影响能够得到缓解和控制,我局原则同意该报告书结论。你公司应全面落实报告书中提出的各项环境保护对策措施和本批复要求。 二、项目建设应重点做好以下工作 (一)项目应严格按照环评要求建设各种环保设施,确保与主体工程同步建设;加强环保设施的日常管理和维护,确保环保设施正常运转。 (二)严格按照环评报告书要求,落实大气污染物防治措施。本项目装置区低含硫不凝气/干气经火炬气回收装置处理脱硫净化后,经管道输送入全厂高压瓦斯系统作为燃料气使用;酸性水及富胺液进入酸性水及富胺液处理系统处理后的酸性气经中和反应器中和后尾气引至火炬系统焚烧放空;项目工艺加热炉、转化炉和蒸汽锅炉使用清洁能源作原料,采用低氮燃烧,废气排放应满足《锅炉大气污染物排放标准》(GB13271-2014)表3特别排放限值排放。 污水处理站设置2套废气处理装置,其中:1套为污水预处理段高浓度废气除臭系统,采用“碱洗+催化燃烧”工艺;1套为污水生化段低浓度废气除臭系统,采用“碱洗+生物除臭+活性炭吸附”工艺,废气排放应满足《石油炼制工业污染物排放标准》(GB31570-2015)表4标准、《**省固定污染源大气挥发性有机物排放标准》(DB51/2377-2017)和《恶臭污染物排放标准》(GB14554-93)相关要求。 根据环评报告书分析,分别以汽柴油加氢精制装置、****处理站边界向外分别划定200m、200m和100m卫生防护距离。****人民政府《关于实施100万吨/年汽柴油加氢精制装置和20000N m3/h制氢装置大气防护距离范围内居民搬迁的函》(大府函〔2019〕67号)要求落实,在项目实施前完成防护距离内的居民搬迁工作,今后在卫生防护距离内不得迁入人群居住、生活服务设施、学校、医院等敏感设施。 (三)严格按照环评报告书要求,落实废水治理措施。项目应进一步完善厂区“雨污分流、清污分流”的原则;加强初期雨水收集和处理;在生产过程应加强车间排口管理。产生的含硫酸性工艺废水和脱硫富胺液进入酸性水及富胺液处理系统处理,酸性****水厂内回用,溶剂再生塔塔底再生贫胺液循环使用;低含油工艺废水、公辅及环保设施排水和生活****处理站隔油生化处理;****处理站1座,最大处理能力350 m3/h,采用“调节罐→隔油池→一级气浮→二级气浮→A/O池→沉淀池”处理工艺,废水排放应满足《石油炼制工业污染物排放标准》(GB31570-2015)表2间接排放标准、《污水综合排放标准》(GB8978-1996)三级标准后进****处理厂处理达标排放。 (四)严格按照报告书要求,落实一般固废和危险废物污染防治措施。项目生产过程中产生的各类废催化剂、废保护剂、废吸附剂、废脱氯剂、废瓷球、脱硫固废、含油废渣、废碱渣、污水处理站油泥和废渣、罐底残渣属危险废物,应集中收集分类暂存,定期交由有危废处置资质的单位处置;产生的污油和分离废油集中收集暂存,用于老厂区燃料油装置作原料;产生的催化燃烧废催化剂由厂家回收处理;产生的办公生活垃圾分类收集后经环卫部门清运;落实危废暂存间“三防”措施,完善标识标牌。 (五)严格按照报告书要求,落实并优化噪声防治措施。通过优化布局,选用低噪声设备,采取加装消声器、基础减振等措施控制噪声污染,确保其满足《工业企业厂界环境噪声排放标准》(GB12348-2008)3类标准。 (六)落实和强化地下水污染防治措施。严格按照环评要求对厂区分为重点防渗区、一般防渗区、简单防渗区。其中生产装置区、污水处理站、事故应急池、雨水收集池、储罐区、变配电站等均为重点污染防治区,采取一种材料单独使用或多种材料结合使用的方法,以确保重点防渗效果。循环水站、锅炉房和气柜等为一般污染防治区,铺设钢筋混凝土加防渗剂的防渗地坪,切断污染地下水途径。厂区其余区域为简单防渗区,要求地面硬化处理。 (七)加强环境风险防范和应急管理,制定环境风险应急预案。制定切实有效的环境风险事故防范措施和环境风险事故应急预案,建立环境风险事故报警系统体系,并严格按照相关规定要求和落实本评价及安全评价报告中提出的环境风险防范措施及应急预案,预防因安全事故导致环境次生灾害。经常性加强环保设施、设备维护、保养,确保设施、设备稳定、正常运行;强化应急预案演练,确保预案、方案具有针对性、操作性,有效减少环境风险事故对环境造成的影响。 (八)认真落实报告书提出的环境管理和环境监测计划,对地下水和土壤加强环境监测,密切关注变化趋势,有效防范地下水和土壤环境污染。依法定期向公众发布环境信息,主动接受社会监督。在项目实施过程中,应建立畅通的公众参与平台,及时解决公众提出的合理环境诉求。 三、项目建设应依法取得相关部门行政许可手续后方可动工建设。 四、总量控制 严格按照项目环评报告书要求,落实企业“以新带老”实施后,全厂废气、废水不突破已批复总量指标。新增废气非甲烷****环保局《关于****100万吨/年汽柴油加氢精制装置和20000N m3/h制氢装置主要污染物排放总量替代方案的报告》(遂大环〔2019〕33 号)调剂解决。 五、项目建设必须严格按照《建设项目环境保护管理条例》(国务院第682号令)的要求,配套建设的环境保护设施与主体工程同时设计、同时施工、同时投产使用的环境保护“三同时”制度。纳入排污许可证管理的行业,必须按照国家排污许可证有关管理规定要求,申领排污许可证,不得无证排污和不按证排污。项目竣工后,建设单位应按相关规定对配套建设的环境保护设施组织竣工验收,并依法向社会公开验收报告。 项目环境影响评价文件经批准后,如工程的性质、规模、工艺、地点或者防治污染、防止生态破坏的措施发生重大变动的,建设单位应当重新报批环境影响评价文件,否则不得实施建设。自环评批复文件批准之日起,如工程超过5年未开工建设,环境影响评价文件应当报我局重新审核。 六、****环境局、****支队加强对该项目的“事中事后”和环境保护“三同时”监督检查及日常监督管理工作。 | 实际建设情况:一、根据环评单位现场调查,****工程部份已开工建设,至今未投入运营。你公司应严格按照报告书中所列建设项目的地点、规模、性质、采用生产工艺以及拟采取的环境保护措施建设和运行,确保对环境的不利影响能够得到缓解和控制,我局原则同意该报告书结论。你公司应全面落实报告书中提出的各项环境保护对策措施和本批复要求。 二、项目建设应重点做好以下工作 (一)项目应严格按照环评要求建设各种环保设施,确保与主体工程同步建设;加强环保设施的日常管理和维护,确保环保设施正常运转。 (二)严格按照环评报告书要求,落实大气污染物防治措施。本项目装置区低含硫不凝气/干气经火炬气回收装置处理脱硫净化后,经管道输送入全厂高压瓦斯系统作为燃料气使用;酸性水及富胺液进入酸性水及富胺液处理系统处理后的酸性气经中和反应器中和后尾气引至火炬系统焚烧放空;项目工艺加热炉、转化炉和蒸汽锅炉使用清洁能源作原料,采用低氮燃烧,废气排放应满足《锅炉大气污染物排放标准》(GB13271-2014)表3特别排放限值排放。 污水处理站设置2套废气处理装置,其中:1套为污水预处理段高浓度废气除臭系统,采用“碱洗+催化燃烧”工艺;1套为污水生化段低浓度废气除臭系统,采用“碱洗+生物除臭+活性炭吸附”工艺,废气排放应满足《石油炼制工业污染物排放标准》(GB31570-2015)表4标准、《**省固定污染源大气挥发性有机物排放标准》(DB51/2377-2017)和《恶臭污染物排放标准》(GB14554-93)相关要求。 根据环评报告书分析,分别以汽柴油加氢精制装置、****处理站边界向外分别划定200m、200m和100m卫生防护距离。****人民政府《关于实施100万吨/年汽柴油加氢精制装置和20000N m3/h制氢装置大气防护距离范围内居民搬迁的函》(大府函〔2019〕67号)要求落实,在项目实施前完成防护距离内的居民搬迁工作,今后在卫生防护距离内不得迁入人群居住、生活服务设施、学校、医院等敏感设施。 (三)严格按照环评报告书要求,落实废水治理措施。项目应进一步完善厂区“雨污分流、清污分流”的原则;加强初期雨水收集和处理;在生产过程应加强车间排口管理。产生的含硫酸性工艺废水和脱硫富胺液进入酸性水及富胺液处理系统处理,酸性****水厂内回用,溶剂再生塔塔底再生贫胺液循环使用;低含油工艺废水、公辅及环保设施排水和生活****处理站隔油生化处理;****处理站1座,最大处理能力350 m3/h,采用“调节罐→隔油池→一级气浮→二级气浮→A/O池→沉淀池”处理工艺,废水排放应满足《石油炼制工业污染物排放标准》(GB31570-2015)表2间接排放标准、《污水综合排放标准》(GB8978-1996)三级标准后进****处理厂处理达标排放。 (四)严格按照报告书要求,落实一般固废和危险废物污染防治措施。项目生产过程中产生的各类废催化剂、废保护剂、废吸附剂、废脱氯剂、废瓷球、脱硫固废、含油废渣、废碱渣、污水处理站油泥和废渣、罐底残渣属危险废物,应集中收集分类暂存,定期交由有危废处置资质的单位处置;产生的污油和分离废油集中收集暂存,用于老厂区燃料油装置作原料;产生的催化燃烧废催化剂由厂家回收处理;产生的办公生活垃圾分类收集后经环卫部门清运;落实危废暂存间“三防”措施,完善标识标牌。 (五)严格按照报告书要求,落实并优化噪声防治措施。通过优化布局,选用低噪声设备,采取加装消声器、基础减振等措施控制噪声污染,确保其满足《工业企业厂界环境噪声排放标准》(GB12348-2008)3类标准。 (六)落实和强化地下水污染防治措施。严格按照环评要求对厂区分为重点防渗区、一般防渗区、简单防渗区。其中生产装置区、污水处理站、事故应急池、雨水收集池、储罐区、变配电站等均为重点污染防治区,采取一种材料单独使用或多种材料结合使用的方法,以确保重点防渗效果。循环水站、锅炉房和气柜等为一般污染防治区,铺设钢筋混凝土加防渗剂的防渗地坪,切断污染地下水途径。厂区其余区域为简单防渗区,要求地面硬化处理。 (七)加强环境风险防范和应急管理,制定环境风险应急预案。制定切实有效的环境风险事故防范措施和环境风险事故应急预案,建立环境风险事故报警系统体系,并严格按照相关规定要求和落实本评价及安全评价报告中提出的环境风险防范措施及应急预案,预防因安全事故导致环境次生灾害。经常性加强环保设施、设备维护、保养,确保设施、设备稳定、正常运行;强化应急预案演练,确保预案、方案具有针对性、操作性,有效减少环境风险事故对环境造成的影响。 (八)认真落实报告书提出的环境管理和环境监测计划,对地下水和土壤加强环境监测,密切关注变化趋势,有效防范地下水和土壤环境污染。依法定期向公众发布环境信息,主动接受社会监督。在项目实施过程中,应建立畅通的公众参与平台,及时解决公众提出的合理环境诉求。 三、项目建设应依法取得相关部门行政许可手续后方可动工建设。 四、总量控制 严格按照项目环评报告书要求,落实企业“以新带老”实施后,全厂废气、废水不突破已批复总量指标。新增废气非甲烷****环保局《关于****100万吨/年汽柴油加氢精制装置和20000N m3/h制氢装置主要污染物排放总量替代方案的报告》(遂大环〔2019〕33 号)调剂解决。 五、项目建设必须严格按照《建设项目环境保护管理条例》(国务院第682号令)的要求,配套建设的环境保护设施与主体工程同时设计、同时施工、同时投产使用的环境保护“三同时”制度。纳入排污许可证管理的行业,必须按照国家排污许可证有关管理规定要求,申领排污许可证,不得无证排污和不按证排污。项目竣工后,建设单位应按相关规定对配套建设的环境保护设施组织竣工验收,并依法向社会公开验收报告。 项目环境影响评价文件经批准后,如工程的性质、规模、工艺、地点或者防治污染、防止生态破坏的措施发生重大变动的,建设单位应当重新报批环境影响评价文件,否则不得实施建设。自环评批复文件批准之日起,如工程超过5年未开工建设,环境影响评价文件应当报我局重新审核。 六、****环境局、****支队加强对该项目的“事中事后”和环境保护“三同时”监督检查及日常监督管理工作。 |
不涉及重大变动 | 是否属于重大变动:|
3、污染物排放量
0 | 0 | 0 | 0 | 0 | 0 | 0 | |
0 | 71.539 | 76.62 | 0 | 0 | 71.539 | 71.539 | |
0 | 0.667 | 3.34 | 0 | 0 | 0.667 | 0.667 | |
0 | 0 | 0 | 0 | 0 | 0 | 0 | |
0 | 0 | 0 | 0 | 0 | 0 | 0 | |
0 | 0 | 0 | 0 | 0 | 0 | 0 | / |
0 | 2.9065 | 40.8 | 0 | 0 | 2.906 | 2.906 | / |
0 | 86.8009 | 88.91 | 0 | 0 | 86.801 | 86.801 | / |
0 | 4.6996 | 14.66 | 0 | 0 | 4.7 | 4.7 | / |
0 | 4.3378 | 30.4 | 0 | 0 | 4.338 | 4.338 | / |
4、环境保护设施落实情况
表1 水污染治理设施
1 | 污水处理站 | 《石油炼制工业污染物排放标准》(GB31570-2015)表2间****处理厂设计要求 | 本项目各类废水,按其性质经过预处理后,最****处理站处理。污水处理站采用“调节罐→隔油池→一级气浮→二级气浮→A/O池→沉淀池”处理工艺,出水达《石油炼制工业污染物排放标准》(GB31570-2015)表2间****处理厂设计进水标准后经排****处理厂,****处理厂处理达标后排入郪江。 | 各项指标满足《石油炼制工业污染物排放标准》(GB31570-2015)表2间****处理厂设计进水标准要求 |
表2 大气污染治理设施
1 | 锅炉燃烧烟气 | 《锅炉大气污染物排放标准》(GB13271-2014)表3特别排放限值要求 | 项目**2台35t/h燃气锅炉,采用天然气及自产干气作为燃料,天然气为清洁能源,自产干气经脱硫处理,其燃烧废气中污染物浓度较低,污染物排放量少,同时采用低氮燃烧,该工艺为《排污许可证申请与核发技术规范 石化工业》(HJ853-2017)中锅炉烟气治理的可行技术,符合技术规范要求,其污染物排放可满足《锅炉大气污染物排放标准》(GB13271-2014)表3特别排放限值要求。 | 污染物排放可满足《锅炉大气污染物排放标准》(GB13271-2014)表3特别排放限值要求。 | |
2 | 工艺加热炉烟气 | 《石油炼制工业污染物排放标准》(GB31570-2015)表4特别排放限值要求 | 本项目汽柴油加氢精制装置设置1台加热炉和1台重沸炉,采用天然气和自产干气为燃料;制氢装置设置1台转化炉采用天然气和PSA尾气为燃料,天然气为清洁能源,自产干气经脱硫处理,其燃烧废气中污染物浓度较低,污染物排放量少,同时采用低氮燃烧,该工艺为《污染源源强核算技术指南 石油炼制工业》(HJ982-2018)和《排污许可证申请与核发技术规范 石化工业》(HJ853-2017)中工艺加热炉烟气治理的可行技术,符合技术规范要求,污染物排放可满足《石油炼制工业污染物排放标准》(GB31570-2015)表4特别排放限值要求。 | 各项废气排放满足《石油炼制工业污染物排放标准》(GB31570-2015)表4特别排放限值要求 | |
3 | 酸性气治理措施 | 《石油炼制工业污染物排放标准》(GB31570-2015)表4标准和《恶臭污染物排放标准》(GB14554-93)标准要求。 | 本项目硫磺回收装置硫磺回收单元采用克劳斯工艺回收酸性气中硫,制硫尾气经焚烧炉焚烧处理,尾气中残存的硫化氢及其它硫化物几乎完全转化成二氧化硫,焚烧后的高温烟气经余热回收和换热后温度降至360℃,再经碱洗处理后烟气通过80m高烟囱排放。因此,本项目酸性气处理工艺为“两级克劳斯硫回收+焚烧+碱洗”,为《污染源源强核算技术指南 石油炼制工业》(HJ982-2018)和《排污许可证申请与核发技术规范 石化工业》(HJ853-2017)中酸性气回收装置治理的可行技术,符合技术规范要求,且碱洗技术适用于执行特别排放限值的污染源。因此,本项目硫磺回收装置尾气污染物排放满足《石油炼制工业污染物排放标准》(GB31570-2015)表4标准和《恶臭污染物排放标准》(GB14554-93)标准要求。 | 废气污染物满足《石油炼制工业污染物排放标准》(GB31570-2015)表4标准和《恶臭污染物排放标准》(GB14554-93)标准要求。 | |
4 | 污水处理站废气治理措施 | 《**省固定污染源大气挥发性有机物排放标准》(DB51/2377-2017)和《恶臭污染物排放标准》(GB14554-93)标准要求 | ****处理站工艺特点,共设2套废气处理装置,其中1套为污水预处理段高浓度废气除臭系统,实际采用“碱洗+催化燃烧”工艺;1套为污水生化段低浓度废气除臭系统,采用“碱洗+生物除臭+活性炭吸附”工艺。 1、高浓度废气除臭系统 高浓度除臭系统为预处理段工艺的除臭,主要包括集水池、调节罐、隔油池、气浮池、浓缩罐和低温干化设备,集水池、隔油池和气浮池的池体上部加盖,调节罐、浓缩罐和低温干化设备密闭负压收集废气,废气通过管道输送至除臭单元,采用“碱洗+催化燃烧”工艺,设计风量为8000m3/h。2、低浓度废气除臭系统 低浓度除臭系统为生化段工艺的除臭,主要包括缺氧池、MBBR池、好氧池筑物的除臭,生化池的池体上部采取加盖收集废气,通过管道输送至除臭单元,采用“碱洗+生物除臭+活性炭吸附”工艺。 | 废气满足《**省固定污染源大气挥发性有机物排放标准》(DB51/2377-2017)和《恶臭污染物排放标准》(GB14554-93)标准要求 | |
5 | 危废间废气活性炭吸附装置 | 《**省固定污染源大气挥发性有机物排放标准》(DB51/2377-2017) | 危废间废气活性炭吸附装置处理后排放 | 挥发性有机物满足《**省固定污染源大气挥发性有机物排放标准》(DB51/2377-2017) |
表3 噪声治理设施
1 | 噪声防治措施 | 《工业企业厂界环境噪声排放标准》(GB12348-2008)3类标准要求 | 项目除了尽量选用低噪声的设备外,主要采取的降噪措施是针对设备采取消声、基础减振等措施,再通过利用距离衰减和厂区外绿化带阻隔,可使厂界噪声满足《工业企业厂界环境噪声排放标准》(GB12348-2008)3类标准要求。 | 厂界噪声满足《工业企业厂界环境噪声排放标准》(GB12348-2008)3类标准要求 |
表4 地下水污染治理设施
1 | 针对可能发生的地下水污染,地下水污染防治措施应按照“源头控制、末端防治、污染监控、应急响应”相结合的原则,从污染物的产生、入渗、扩散、应急响应全阶段进行控制。本厂区应以主动防渗漏措施为主,被动防渗漏措施为辅,人工防渗措施和自然防渗条件保护相结合,防止地下水受到污染。 根据项目可能泄漏的污染物的性质和生产单元的构筑方式,以及潜在的地下水污染源分类分析,将厂区划分为简单防渗区、一般防渗区和重点防渗区。 简单防渗区:指不会对地下水环境造成污染的区域。主要包括厂区的配电室、管控中心、消防泵站等。 一般防渗区:是指裸露于地面的生产功能单元,污染地下水环境的物料或污染物泄漏后,可及时发现和处理的区域。本项目所涉及的循环水站、锅炉房和气柜等单元。 重点防渗区:是指位于地下或半地下的生产功能单元,污染地下水环境的物料或污染物泄漏后,不易及时发现和处理的区域。包括生产装置区、污水处理站、事故应急池、雨水收集池及储罐区等单元。2019年编制的环评报告中防渗设计结构建议 防止地下水污染的被动控制措施即为地面防渗工程。环评提出厂区地下水污染防渗设计建议如下: 重点防渗区:环评要求采用防渗性能与厚度Mb≥6.0m,渗透系数K≤1×10-7cm/s粘土防渗层等效的刚性+柔性防渗措施,即车间地面:场平挖方材料及原始土层+土工布+2mmHDPE土工膜(K≤10-12cm/s)+土工布+防渗混凝土层12cm;罐区:罐区采用天然粘土填料层+土工布+2mm土工膜(K≤10-12cm/s)+土工布+砂垫层≥300mm+沥青砂绝缘层100mm+钢储罐底板;特殊污染防治区水池混凝土强度等级不低于C30,抗渗等级不低于P10,且水池内表面涂刷水泥基渗透结晶型防水涂料(渗透系数不大于1×10-12cm/s,结构厚度不小于300mm);车间内管线及其他设备内各种管线采用碳钢无缝管线连接,对于地下管线可按照素填土夯实+100mm厚C15混凝土垫层+长丝无纺布+2mm厚HDPE土工膜+长丝无纺布+砂垫层200mm+中粗砂垫层+回填至地面。 一般防渗区:采用防渗性能与厚度Mb≥1.5m,渗透系数K≤1×10-7cm/s粘土防渗层等效的厚度为12cm的P8混凝土防渗措施(其渗透系数大致为2.61×10-9cm/s)。车间地面:场平挖方材料及原始土层+防渗混凝土层12cm并采取相应防腐措施。除此之外,所有缝均应设止水带。 | ****公司100万吨/年汽柴油加氢精制装置和20000Nm3/h制氢装置项目最早于2013年施工建设,其隐蔽工程于2019年前即完成施工(环评报告2019年6月编制并取得环评批复)。项目施工期间没有开展施工期环境监理工作,由于保管不善等原因,目前没有保留有重点防渗区域施工记录及日志等资料。目前搜集的资料仅有部分重点防渗区域的施工设计资料,经过与环评报告及相关标准的比对,其满足重点防渗的要求。****公司确认并承诺重点防渗区施工是严格按照设计资料施工,重点防渗区满足《石油化工工程防渗技术规范》(GB/T50934-2013)等相关技术规范及行业标准规范要求。我公司承诺在日常运营工作中应做好以下工作内容: 1、应采取必要的技术手段和措施,定期对重点防渗区域定期进行泄漏检查,防止污染物泄漏污染地下水和土壤。 2、应按照《中国人民**国土壤污染防治法》(2019年1月1日起施行)、《**省土壤污染防治条例》(2023年7月1日起施行)、《重点监管单位土壤污染隐患排查指南(试行)》(公告 2021年 第1号)、《**省工矿用地土壤环境管理办法( 川环规〔2023〕7号)》等相关法律法规及技术规范和标准的要求,定期开展地下水和土壤的自行监测,编制隐患排查报告,并根据监测结果和分析结论采取相应的措施,以防治土壤和地下水污染。 |
表5 固废治理设施
1 | 严格按照报告书要求,落实一般固废和危险废物污染防治措施。项目生产过程中产生的各类废催化剂、废保护剂、废吸附剂、废脱氯剂、废瓷球、脱硫固废、含油废渣、废碱渣、污水处理站油泥和废渣、罐底残渣属危险废物,应集中收集分类暂存,定期交由有危废处置资质的单位处置;产生的污油和分离废油集中收集暂存,用于老厂区燃料油装置作原料;产生的催化燃烧废催化剂由厂家回收处理;产生的办公生活垃圾分类收集后经环卫部门清运;落实危废暂存间“三防”措施,完善标识标牌。项目固体废物包括:各类废催化剂、废保护剂、废吸附剂、废脱氯剂、废瓷球、脱硫固废、含油废渣、污水处理站污泥、罐底残渣、废油以及生活垃圾等。 | 项目固体废物包括:各类废催化剂、废保护剂、废吸附剂、废脱氯剂、废瓷球、脱硫固废、含油废渣、污水处理站污泥、罐底残渣、废油以及生活垃圾等。目前企业已经与******公司、**兴蓉****公司签订危废协议处置危险废物。设置危废间暂存间1处。 |
表6 生态保护设施
表7 风险设施
1 | 加强环境风险防范和应急管理,制定环境风险应急预案。制定切实有效的环境风险事故防范措施和环境风险事故应急预案,建立环境风险事故报警系统体系,并严格按照相关规定要求和落实本评价及安全评价报告中提出的环境风险防范措施及应急预案,预防因安全事故导致环境次生灾害。经常性加强环保设施、设备维护、保养,确保设施、设备稳定、正常运行;强化应急预案演练,确保预案、方案具有针对性、操作性,有效减少环境风险事故对环境造成的影响。 | ****于2023年9月修订了《****突发环境事件应急预案》(2023年版),****生态环境局备案(备案编号510923-2023-031-H)。同时,企业按照相关法律法规及应急预案的要求,至少每年开展一次环境风险应急演练工作(实际每年开展两次),****最近一次开展应急演练工作时间为2023年12月26日,相关应急演练开展资料见附件12。 根据项目环评报告及最新编制的应急预案报告,项目厂区采取的环境风险防范措施主要包括以下内容。环境风险防控措施 1、储罐区 为避免项目泄漏事故时,泄漏物料对周边地表水、地下水及土壤环境的污染:储罐区围堰:项目储罐区设置2.0m高围堰(原料油罐区有效总容积27000m3;汽油、柴油罐区有效总容积分别为10000m3)并进行防渗处理,可以有效防止液体原料泄漏对环境的影响。 生产装置区截流沟:项目生产车间为封闭状态,并设截流沟用于区内液体物料泄漏时的截留和确保不发生消防水外排事故,通过截流沟及时将泄漏液体引入事故应急池或应急接收槽,以避免泄漏物料对周围环境的影响。 事故废水收集及阻断设施:新厂区建设有1座20000m3事故应急池以及配套的事故废水收集及阻断设施,均可用于厂区泄漏物料的收集暂存,以避免周边地表水、地下水及土壤环境的污染。 综上,通过上述风险防范措施,可以有效的避免生产、储存及运输的过程中物料泄漏对周围地表水、地下水及土壤环境的污染。 2、消防废水 由项目消防水量为378L/s,按持续6小时消防用水量估算,则消防废水产生量为8165m3。为避免项目火灾事故时,项目消防废水未有效收集处理而直接入河而采取的措施如下所述。 事故应急设施:新厂区建设有1座20000m3事故应急池和1×4000m3污水罐为应急缓冲罐,用于对消防废水暂存,待火灾后,将消防废水****处理站处理后,****园区污水管网。事故废水收集及阻断设施:本企业设置雨水收集池(制氢装置区1座初期雨水收集池有效容积500m3、硫磺回收装置区初期雨水收集池1座有效容积280m3、全厂雨水监控池1座有效容积3000m3)、1座20000m3事故应急池和1个4000m3应急缓冲罐以及配套的事故废水收集及阻断设施,均可用于厂区泄漏物料的收集暂存,以避免对周边地表水、地下水及土壤环境的污染。 综上,通过上述风险防范措施,可以有效的避免生产、储存及运输的过程中物料泄漏对周边地表水、地下水及土壤环境的污染。 3、设计上采取的风险防范措施 (1)总图及平面布置 总图布置符合《石油化工企业设计防火规范》(GB50160-2008)等标准规范要求。设备按工艺流程顺序和同类设备适当集中相结合的方式进行布置。装置内的设备应布置紧凑和完整,以便满足经济、安全、方便操作和维修的要求。有明火的设备,远离可能泄漏可燃气体的工艺设备及储罐。可能散发可燃气体或有毒有害气体的工艺装置等危险性较大设备设施集中布置,且布置在人员集中场所及明火或散发火花地点的全年最小频率风向的上风侧。凡在开停工、检修过程中可能出现有害流体泄漏、漫流的设备区周围,均设围堰以及导液设施;处理腐蚀性介质的设备区应铺防腐地面。 (2)工艺和设备 ①工艺装置及辅助生产设施的压力容器、压力管道的设计及制造严格执行《工业金属管道设计规范》(GB50316-2008)及其它有关的标准规范。 ②对危险物料的安全控制是防火防爆最有效的措施之一,项目设计中从原料油的输入、加工直至产品的输出,所有易燃易爆物料始终处于密闭的设备和管道中,设备以及管线之间的连接处均采取了可靠的密封措施,防止介质泄漏。 ③为确保装置开停工及检修安全,在装置有关管道和设备上设置固定式或半固定式吹扫接头,在进出装置边界管道上设置切断阀和盲板。巡检人员配备便携式毒性气体检测报警仪,以便及时发现可能出现毒性气体泄漏。 ④为防止压力设备由于超压发生事故,在适当的位置安装泄压阀。在事故条件下可能处于真空状态下的设备,将采用可承受全真空的设备,在适当的位置安装充压设施。 ⑤项目设备和管道的防腐采用工艺防腐和材料抗腐两个方面的措施,解决设备和管道的腐蚀问题。 ⑥在工艺、设备设计过程中,充分考虑了脆性破裂、温差应力破坏、高温蠕变破坏、腐蚀破坏及密封泄漏等因素。根据介质、操作温度、压力和腐蚀情况,设计对装置中重要部位和设备的用材,按规范选择相应的防腐等级,以保证防腐蚀能力,确保设备安全及设备寿命。 (3)自动控制 本企业的控制系统有分散控制系统(DCS)、安全仪表系统(SIS)、压缩机组控制系统(CCS)和仪表及控制设备维护系统(AMS)。 ①各工艺装置及公用工程均采用集散型控制系统(DCS)进行过程控制,****中心控制室进行集中操作和管理。各单元的主要工艺检测和控制参数均引入DCS进行指示、调节、记录、报警等操作,各单元内的主要转动设备的运行状态均引入DCS进行显示。各工艺装置一般设相对独立的DCS控制站,但硫磺、酸性水、胺液再生三个单元按一个联合装置考虑共用1个(套)DCS控制站,污水处理站和锅炉房设独立的DCS控制站,其它公用工程各单元就近引入相邻的DCS控制站。 ②安全仪表保护系统(SIS)独立于DCS设置。各装置及关键设备根据不同的工艺过程的需要设置必要的安全仪表系统(SIS)。原则上全厂采用统一型号的控制系统。 ③油品储运设施采用计算机监控管理系统(SCADA系统),****中心控制室设有SCADA系统的监控站。 ④可燃和有毒气体检测系统(GDS)独立于DCS设置。****中心控制室设置GDS的控制站和操作站,对新厂区各工艺装置、罐区及公用工程各单元的可燃和有毒气体检测及报警进行集中管理。 ⑤汽柴油加氢精制装置采用汽轮机-离心压缩机组,需设计压缩机控制系统(CCS)。CCS与装置安全仪表系统SIS合二为一,不单设CCS。硫磺回收装置设独立的安全仪表系统SIS,其它装置的安全联锁相对简单,不设SIS,安全联锁功能在DCS上实现,但安全联锁控制必须完善齐全。 ⑥全厂自动控制方案采用单参数控制为主,根据具体工艺过程及生产要求,分别采用串级、前馈、分程、超驰、比值、顺序、三冲量等复杂控制。 ⑦设智能设备管理系统(AMS)实现对智能仪表(HART通讯协议)的信息集中管理。 ⑧设时钟同步系统(GPS)统一DCS/SIS/SCADA系统的时钟,DCS/SIS/SCADA应具有接受GPS时钟信号的功能和配置。 ⑨区域中心控制室各控制系统设置与全厂计算机信息和生产调度系统管理网相连的以太网通信接口、服务器,建立实时数据库,为全厂信息管理系统提供所需的实时数据和管理信息。 (4)消防及火灾报警系统 ①消防水系统:新厂区已建消防泵房设计消防水量400L/s,水压1.2MPa,消防水罐:2×5000m3。消防泵站设置两台5000m3钢质消防水罐,消防水罐补水来自厂区新鲜水管道,根据消防水罐的液位自动补水。设置两台电动消防水泵,两台柴油机消防水泵,四台水泵两开两备,消防水泵从消防水罐取水,输送至厂区消防用水点。消防水系统采用稳高压系统,平时消防管网压力由稳压装置将压力维持在0.7~0.9MPa之间;消防时用水量增大,管网压力下降至0.6MPa或接到消防报警信号时,依次自动启动消防泵,使管网压力达到1.2MPa,满足消防要求。 ②泡沫灭火系统:罐区设固定式泡沫灭火系统,就近设置3座泡沫站,每座泡沫站内设有1套平衡式泡沫比例混合装置,泡沫混合液最大供给量为64L/s,泡沫液储存量10m3。 ③消防站:****大队工业园区队,位于厂区附近500m范围内,消防站有消防车辆4部,实行24小时执勤,消防大队现有消防人员30名。****大队总队位于**县城文体路,距离企业约8公里,在园区消防力量不足的情况下能够在10分钟内增援。 ④火灾报警系统:全厂设有电话报警系统,生产区设有1套火灾报警系统,主控盘设置在控制室内,用于自动报警系统和手动报警按钮系统的报警信号显示。 |
5、环境保护对策措施落实情况
依托工程
由于老厂区汽油产品质量无法满足现行国家《车用汽油标准》(GB 17930-2016)要求,部分污染物排放也不能满足国家《石油炼制工业污染物排放标准》(GB31570-2015)相关要求,因此****老厂区目前部分设施处于停产状态。****原料部分来源于老厂区200万吨/年燃料油处理装置生产,部分为外购,外购的原料为燃料油,其成分、组成等与老厂区所提供的原料基本一致。 由于老厂区大部分设施处于停产状态,本项目为下游产品深加工,因此,目前本次验收期间本项目与老厂区之间的生产相对独立,不存在生产设施、原辅材料(部分来源于老厂区200万吨/年燃料油处理装置生产,部分为外购)、环保设施的依托关系。 由于目前企业来料、出料基本为公路运输(企业生产不稳定,原料来料量小,****原料部分为铁路运输,部分为公路运输,铁路卸料为负压,不涉及设置油气回收装置,环评报告要求铁路专线装卸区设置油气回收装置为汽油装车环节),故本项目依托老厂区的设施(含环保设施)仅为设置于老厂区与新厂区之间(厂区东南角)的公路装卸区。因此,本次竣工环境保护验收工作对其老厂区装卸区油气回收装置的进、出口挥发性有机物进行监测,并计算了挥发性有机物的去除效率。 | 验收阶段落实情况:由于老厂区汽油产品质量无法满足现行国家《车用汽油标准》(GB 17930-2016)要求,部分污染物排放也不能满足国家《石油炼制工业污染物排放标准》(GB31570-2015)相关要求,因此****老厂区目前部分设施处于停产状态。****原料部分来源于老厂区200万吨/年燃料油处理装置生产,部分为外购,外购的原料为燃料油,其成分、组成等与老厂区所提供的原料基本一致。 由于老厂区大部分设施处于停产状态,本项目为下游产品深加工,因此,目前本次验收期间本项目与老厂区之间的生产相对独立,不存在生产设施、原辅材料(部分来源于老厂区200万吨/年燃料油处理装置生产,部分为外购)、环保设施的依托关系。 由于目前企业来料、出料基本为公路运输(企业生产不稳定,原料来料量小,****原料部分为铁路运输,部分为公路运输,铁路卸料为负压,不涉及设置油气回收装置,环评报告要求铁路专线装卸区设置油气回收装置为汽油装车环节),故本项目依托老厂区的设施(含环保设施)仅为设置于老厂区与新厂区之间(厂区东南角)的公路装卸区。因此,本次竣工环境保护验收工作对其老厂区装卸区油气回收装置的进、出口挥发性有机物进行监测,并计算了挥发性有机物的去除效率。 |
/ |
环保搬迁
为了确保大气环境防护区域之外叠加后的短期浓度也符合环境质量标准,项目建成后全厂以最远垂直距离(456.55m)划定大气防护距离,****政府《关于项目大气防护距离范围内居民搬迁的函》(大府函[2019]67号):“大气防护距离内分布有**镇**二小区163户650人、**村居民54户162人,其中**二小区已纳****园区管委会负责搬迁(大工管委函[2018]50号),**村居民54户162****政府负责项目投产前完成搬迁工作”。企业承诺在大气防护距离内现有居民搬迁完成前不投入生产(川盛化[2019]62号) | 验收阶段落实情况:为了确保大气环境防护区域之外叠加后的短期浓度也符合环境质量标准,项目建成后全厂以最远垂直距离(456.55m)划定大气防护距离,****政府《关于项目大气防护距离范围内居民搬迁的函》(大府函[2019]67号):“大气防护距离内分布有**镇**二小区163户650人、**村居民54户162人,其中**二小区已纳****园区管委会负责搬迁(大工管委函[2018]50号),**村居民54户162****政府负责项目投产前完成搬迁工作”。企业承诺在大气防护距离内现有居民搬迁完成前不投入生产(川盛化[2019]62号),目前大气防护距离范围内居民已搬迁。 |
/ |
区域削减
/ | 验收阶段落实情况:/ |
/ |
生态恢复、补偿或管理
/ | 验收阶段落实情况:/ |
/ |
功能置换
/ | 验收阶段落实情况:/ |
/ |
其他
(一)项目应严格按照环评要求建设各种环保设施,确保与主体工程同步建设;加强环保设施的日常管理和维护,确保环保设施正常运转。 (二)严格按照环评报告书要求,落实大气污染物防治措施。本项目装置区低含硫不凝气/干气经火炬气回收装置处理脱硫净化后,经管道输送入全厂高压瓦斯系统作为燃料气使用;酸性水及富胺液进入酸性水及富胺液处理系统处理后的酸性气经中和反应器中和后尾气引至火炬系统焚烧放空;项目工艺加热炉、转化炉和蒸汽锅炉使用清洁能源作原料,采用低氮燃烧,废气排放应满足《锅炉大气污染物排放标准》(GB13271-2014)表3特别排放限值排放。 污水处理站设置2套废气处理装置,其中:1套为污水预处理段高浓度废气除臭系统,采用“碱洗+催化燃烧”工艺;1套为污水生化段低浓度废气除臭系统,采用“碱洗+生物除臭+活性炭吸附”工艺,废气排放应满足《石油炼制工业污染物排放标准》(GB31570-2015)表4标准、《**省固定污染源大气挥发性有机物排放标准》(DB51/2377-2017)和《恶臭污染物排放标准》(GB14554-93)相关要求。 根据环评报告书分析,分别以汽柴油加氢精制装置、****处理站边界向外分别划定200m、200m和100m卫生防护距离。****人民政府《关于实施100万吨/年汽柴油加氢精制装置和20000N m3/h制氢装置大气防护距离范围内居民搬迁的函》(大府函〔2019〕67号)要求落实,在项目实施前完成防护距离内的居民搬迁工作,今后在卫生防护距离内不得迁入人群居住、生活服务设施、学校、医院等敏感设施。 (三)严格按照环评报告书要求,落实废水治理措施。项目应进一步完善厂区“雨污分流、清污分流”的原则;加强初期雨水收集和处理;在生产过程应加强车间排口管理。产生的含硫酸性工艺废水和脱硫富胺液进入酸性水及富胺液处理系统处理,酸性****水厂内回用,溶剂再生塔塔底再生贫胺液循环使用;低含油工艺废水、公辅及环保设施排水和生活****处理站隔油生化处理;****处理站1座,最大处理能力350 m3/h,采用“调节罐→隔油池→一级气浮→二级气浮→A/O池→沉淀池”处理工艺,废水排放应满足《石油炼制工业污染物排放标准》(GB31570-2015)表2间接排放标准、《污水综合排放标准》(GB8978-1996)三级标准后进****处理厂处理达标排放。 (四)严格按照报告书要求,落实一般固废和危险废物污染防治措施。项目生产过程中产生的各类废催化剂、废保护剂、废吸附剂、废脱氯剂、废瓷球、脱硫固废、含油废渣、废碱渣、污水处理站油泥和废渣、罐底残渣属危险废物,应集中收集分类暂存,定期交由有危废处置资质的单位处置;产生的污油和分离废油集中收集暂存,用于老厂区燃料油装置作原料;产生的催化燃烧废催化剂由厂家回收处理;产生的办公生活垃圾分类收集后经环卫部门清运;落实危废暂存间“三防”措施,完善标识标牌。 (五)严格按照报告书要求,落实并优化噪声防治措施。通过优化布局,选用低噪声设备,采取加装消声器、基础减振等措施控制噪声污染,确保其满足《工业企业厂界环境噪声排放标准》(GB12348-2008)3类标准。 (六)落实和强化地下水污染防治措施。严格按照环评要求对厂区分为重点防渗区、一般防渗区、简单防渗区。其中生产装置区、污水处理站、事故应急池、雨水收集池、储罐区、变配电站等均为重点污染防治区,采取一种材料单独使用或多种材料结合使用的方法,以确保重点防渗效果。循环水站、锅炉房和气柜等为一般污染防治区,铺设钢筋混凝土加防渗剂的防渗地坪,切断污染地下水途径。厂区其余区域为简单防渗区,要求地面硬化处理。 (七)加强环境风险防范和应急管理,制定环境风险应急预案。制定切实有效的环境风险事故防范措施和环境风险事故应急预案,建立环境风险事故报警系统体系,并严格按照相关规定要求和落实本评价及安全评价报告中提出的环境风险防范措施及应急预案,预防因安全事故导致环境次生灾害。经常性加强环保设施、设备维护、保养,确保设施、设备稳定、正常运行;强化应急预案演练,确保预案、方案具有针对性、操作性,有效减少环境风险事故对环境造成的影响。 (八)认真落实报告书提出的环境管理和环境监测计划,对地下水和土壤加强环境监测,密切关注变化趋势,有效防范地下水和土壤环境污染。依法定期向公众发布环境信息,主动接受社会监督。在项目实施过程中,应建立畅通的公众参与平台,及时解决公众提出的合理环境诉求。 | 验收阶段落实情况:(一)项目应严格按照环评要求建设各种环保设施,确保与主体工程同步建设;加强环保设施的日常管理和维护,确保环保设施正常运转。 (二)严格按照环评报告书要求,落实大气污染物防治措施。本项目装置区低含硫不凝气/干气经火炬气回收装置处理脱硫净化后,经管道输送入全厂高压瓦斯系统作为燃料气使用;酸性水及富胺液进入酸性水及富胺液处理系统处理后的酸性气经中和反应器中和后尾气引至火炬系统焚烧放空;项目工艺加热炉、转化炉和蒸汽锅炉使用清洁能源作原料,采用低氮燃烧,废气排放应满足《锅炉大气污染物排放标准》(GB13271-2014)表3特别排放限值排放。 污水处理站设置2套废气处理装置,其中:1套为污水预处理段高浓度废气除臭系统,采用“碱洗+催化燃烧”工艺;1套为污水生化段低浓度废气除臭系统,采用“碱洗+生物除臭+活性炭吸附”工艺,废气排放应满足《石油炼制工业污染物排放标准》(GB31570-2015)表4标准、《**省固定污染源大气挥发性有机物排放标准》(DB51/2377-2017)和《恶臭污染物排放标准》(GB14554-93)相关要求。 根据环评报告书分析,分别以汽柴油加氢精制装置、****处理站边界向外分别划定200m、200m和100m卫生防护距离。****人民政府《关于实施100万吨/年汽柴油加氢精制装置和20000N m3/h制氢装置大气防护距离范围内居民搬迁的函》(大府函〔2019〕67号)要求落实,在项目实施前完成防护距离内的居民搬迁工作,今后在卫生防护距离内不得迁入人群居住、生活服务设施、学校、医院等敏感设施。 (三)严格按照环评报告书要求,落实废水治理措施。项目应进一步完善厂区“雨污分流、清污分流”的原则;加强初期雨水收集和处理;在生产过程应加强车间排口管理。产生的含硫酸性工艺废水和脱硫富胺液进入酸性水及富胺液处理系统处理,酸性****水厂内回用,溶剂再生塔塔底再生贫胺液循环使用;低含油工艺废水、公辅及环保设施排水和生活****处理站隔油生化处理;****处理站1座,最大处理能力350 m3/h,采用“调节罐→隔油池→一级气浮→二级气浮→A/O池→沉淀池”处理工艺,废水排放应满足《石油炼制工业污染物排放标准》(GB31570-2015)表2间接排放标准、《污水综合排放标准》(GB8978-1996)三级标准后进****处理厂处理达标排放。 (四)严格按照报告书要求,落实一般固废和危险废物污染防治措施。项目生产过程中产生的各类废催化剂、废保护剂、废吸附剂、废脱氯剂、废瓷球、脱硫固废、含油废渣、废碱渣、污水处理站油泥和废渣、罐底残渣属危险废物,应集中收集分类暂存,定期交由有危废处置资质的单位处置;产生的污油和分离废油集中收集暂存,用于老厂区燃料油装置作原料;产生的催化燃烧废催化剂由厂家回收处理;产生的办公生活垃圾分类收集后经环卫部门清运;落实危废暂存间“三防”措施,完善标识标牌。 (五)严格按照报告书要求,落实并优化噪声防治措施。通过优化布局,选用低噪声设备,采取加装消声器、基础减振等措施控制噪声污染,确保其满足《工业企业厂界环境噪声排放标准》(GB12348-2008)3类标准。 (六)落实和强化地下水污染防治措施。严格按照环评要求对厂区分为重点防渗区、一般防渗区、简单防渗区。其中生产装置区、污水处理站、事故应急池、雨水收集池、储罐区、变配电站等均为重点污染防治区,采取一种材料单独使用或多种材料结合使用的方法,以确保重点防渗效果。循环水站、锅炉房和气柜等为一般污染防治区,铺设钢筋混凝土加防渗剂的防渗地坪,切断污染地下水途径。厂区其余区域为简单防渗区,要求地面硬化处理。 (七)加强环境风险防范和应急管理,制定环境风险应急预案。制定切实有效的环境风险事故防范措施和环境风险事故应急预案,建立环境风险事故报警系统体系,并严格按照相关规定要求和落实本评价及安全评价报告中提出的环境风险防范措施及应急预案,预防因安全事故导致环境次生灾害。经常性加强环保设施、设备维护、保养,确保设施、设备稳定、正常运行;强化应急预案演练,确保预案、方案具有针对性、操作性,有效减少环境风险事故对环境造成的影响。 (八)认真落实报告书提出的环境管理和环境监测计划,对地下水和土壤加强环境监测,密切关注变化趋势,有效防范地下水和土壤环境污染。依法定期向公众发布环境信息,主动接受社会监督。在项目实施过程中,应建立畅通的公众参与平台,及时解决公众提出的合理环境诉求。 |
/ |
6、工程建设对项目周边环境的影响
/ |
/ |
/ |
/ |
/ |
/ |
7、验收结论
1 | 未按环境影响报告书(表)及其审批部门审批决定要求建设或落实环境保护设施,或者环境保护设施未能与主体工程同时投产使用 |
2 | 污染物排放不符合国家和地方相关标准、环境影响报告书(表)及其审批部门审批决定或者主要污染物总量指标控制要求 |
3 | 环境影响报告书(表)经批准后,该建设项目的性质、规模、地点、采用的生产工艺或者防治污染、防止生态破坏的措施发生重大变动,建设单位未重新报批环境影响报告书(表)或环境影响报告书(表)未经批准 |
4 | 建设过程中造成重大环境污染未治理完成,或者造成重大生态破坏未恢复 |
5 | 纳入排污许可管理的建设项目,无证排污或不按证排污 |
6 | 分期建设、分期投入生产或者使用的建设项目,其环境保护设施防治环境污染和生态破坏的能力不能满足主体工程需要 |
7 | 建设单位因该建设项目违反国家和地方环境保护法律法规受到处罚,被责令改正,尚未改正完成 |
8 | 验收报告的基础资料数据明显不实,内容存在重大缺项、遗漏,或者验收结论不明确、不合理 |
9 | 其他环境保护法律法规规章等规定不得通过环境保护验收 |
不存在上述情况 | |
验收结论 | 合格 |
招标导航更多>>
工程建筑
交通运输
环保绿化
医疗卫生
仪器仪表
水利水电
能源化工
弱电安防
办公文教
通讯电子
机械设备
农林牧渔
市政基建
政府部门
换一批
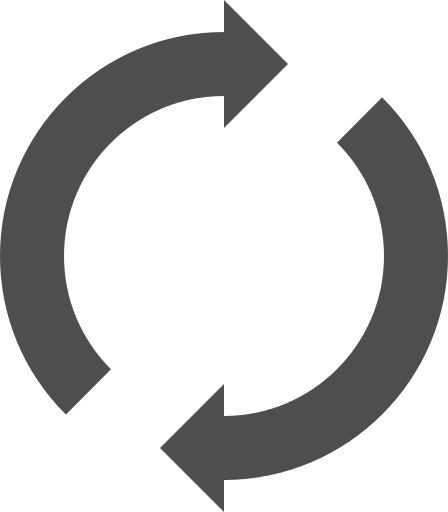