年产12万台/套汽车内外饰(含座椅)和年产24万台套汽车橡胶制品生产项目
1、建设项目基本信息
企业基本信息
**** | 建设单位代码类型:|
****0804MA49N01124 | 建设单位法人:李建军 |
张正杰 | 建设单位所在行政区划:****门市**区 |
**市**区至信大道汽车零部件产业园2-2888号 |
建设项目基本信息
年产12万台/套汽车内外饰(含座椅)和年产24万台套汽车橡胶制品生产项目 | 项目代码:|
建设性质: | |
2021版本:071-汽车整车制造;汽车用发动机制造;改装汽车制造;低速汽车制造;电车制造;汽车车身、挂车制造;汽车零部件及配件制造 | 行业类别(国民经济代码):C3670-C3670-汽车零部件及配件制造 |
建设地点: | ****门市**区 至信大道汽车零部件产业园2-2888号 |
经度:112.16733 纬度: 30.90707 | ****机关:****环境局 |
环评批复时间: | 2022-11-29 |
荆环审〔2022〕88号 | 本工程排污许可证编号:**** |
2024-04-26 | 项目实际总投资(万元):54681.88 |
3007.685 | 运营单位名称:**** |
****0804MA49N01124 | 验收监测(调查)报告编制机构名称:******公司 |
****0802MA48PJGR2C | 验收监测单位:******公司 |
****0804MA49M9F88N | 竣工时间:2023-12-15 |
2023-12-22 | 调试结束时间:2024-06-06 |
2024-08-29 | 验收报告公开结束时间:2024-09-27 |
验收报告公开载体: | http://hplsx.com/portal.php?mod=view aid=149 |
2、工程变动信息
项目性质
** | 实际建设情况:** |
无 | 是否属于重大变动:|
规模
年产12万台/套汽车内外饰(含座椅)和年产24万台套汽车橡胶制品生产项目 | 实际建设情况:年产12万台/套汽车内外饰(含座椅)和年产24万台套汽车橡胶制品生产项目 |
无 | 是否属于重大变动:|
生产工艺
1、北厂座椅车间发泡生产线:座椅发泡:首先使用专用清模工具,对模具型腔及分型面进行清理;然后使用专用喷枪,将脱模剂均匀喷涂于已清理干净的模腔内,防止产品粘模;根据嵌件规格将对应的嵌件放入正确的模腔内;混料设备按生产计划和配料单进行A料配制,把B料抽入储料罐,备用于发泡生产;使用高压发泡机及高精度混合枪头,按照设定比例将混料黑白料,浇注于指定模腔内、保压、熟化;然后起模进行自检互检;使用机械开孔机或真空开孔机对出模的产品进行开孔处理;之后使用自动喷码机或日期章进行产品喷码;依据修补标准对产品进行修补;检验员对产品进行终检,之后产品进入后熟化区进行熟化。 /2、北厂外饰车间注塑生产线:注塑工艺按照产品单元化,操作少人化,经济实用的原则进行规划,注塑机设备系统,将储料斗中的原料通过吸料风机输送至注塑机干燥料筒,(注塑机和料桶由软管连接)进行干燥,然后通过加热线圈加热,使原料熔融。原料熔化后在外动力油马达作用下驱动旋转的螺杆,沿着螺槽向前输送并压实;物料在外加热和螺杆剪切的双重作用下逐渐地塑化、熔融和均化;当螺杆旋转时,物料在螺槽摩擦力及剪切力的作用下把已熔融的物料推到螺杆的头部,与此同时,螺杆在物料的反作用力的作用下,以高压高速,将储料室的熔融料通过喷嘴注射到模具的型腔中,过程中模具通过模温机进行预热;型腔中的熔料经过保压、冷水机冷却、固化定型后,模具在合模机构的作用下,开启模具,并通过顶出装置把定型好的制件从模具顶出,然后通过三轴机械手/六轴机器人将产品从注塑机中取出,并进行自动剪胶口,对于合格的产品人工放入工装车,运输到产品存储区。 3、北厂外饰车间涂装生产线: (1)上件:项目所需喷涂注塑件进入上件区进行上件。 (2)表面预处理: a.预脱脂和脱脂:脱脂分预脱脂及脱脂两部分,脱脂主要是用酸性溶液靠皂化、乳化作用或浸透溶解除去塑料件表面的油污,其后水洗的主要作用是清洗工件表面带出来的脱脂剂。预脱脂用于除去零部件产品油污,采用喷淋方式,喷淋时间为90s,脱脂用于除去油污,采用喷淋方式,喷淋时间为120s。预脱脂液及脱脂液温度均为50~60℃。预脱脂及脱脂槽均需定期换槽液,产生脱脂废液(W1)经管道排****处理站脱脂废液预处理系统。 b.水洗(三级水洗+纯水洗):为了冲洗干净车身表面残留的脱脂剂在脱脂后设三级水洗(水洗1、水洗2、水洗3)及一级纯水洗工序。三道水洗均为喷淋水洗,采用常温工业水喷淋60s,纯水洗利用喷淋管进行喷淋水洗,生产中纯水喷淋后废水流向3#水洗槽用于水洗3后向2#水洗槽溢流用于水洗2,2#水洗槽液向1#水洗槽保持溢流用于水洗1,1#水洗槽溢流水排出。1#槽槽液每周更新一次,2#槽槽液每两周更新一次,3#槽槽液每两周更新一次,产生脱脂废水(W2),主要污染物为COD、SS、总氮、石油类等。纯水制备工程中产生的浓水(W8)。 c.吹水:为去除内外饰零部件表面水分,利用风吹对内外饰零部件进行自动吹水,再人工进行**吹水。生产人员进涂装室需除静电,并定期对工作服进行清洗及地面清扫,产生洗衣及清扫废水(W3)。 d.水分烘干:将内外饰零部件的表面水分烘干,烘干温度75-85℃。烘干方式为间接加热,采用天然气燃烧加热产生的热风对流循环,该工序烘干废气主要污染物是水蒸气,故本次环评不做分析。该工序产生燃烧天然气废气(G1-1)。 e.强冷(风冷):经过烘干后的塑件会通过风冷室降温到室温,进而便于进行后道工段。 f.火焰处理:合格的塑件经输送链输送至车间的喷涂区域,在输送过程中完成自然冷却,经过观察室进入火焰处理室,该室用天然气燃烧火焰烧工件表面,火焰温度的为1000~2500℃,空气稍过量以使燃烧完全,处理时间需短,火焰处理可使型料表面层分子局部氧化,产生-COOH、-CO等极性基团,以增加塑料件的表面性能、提高塑料表面的浸润性和附着力,还可消除塑料表面的毛刺。本过程采用机器人自动控制完成,产生燃气废气(G1-2)。 (3)喷涂:喷涂件设计时需涂装3道涂层,分别为底漆、色漆、清漆,设置调漆室、喷漆室、流平室、烘干室和强冷室等组成一条喷漆线。项目调漆过程在集中供漆系统完成。将各种油漆与稀释剂、固化剂调和后,输送至各喷漆室喷枪处使用。喷漆工段按底漆喷漆、流平→色漆喷漆、流平→面漆喷漆、流平→清漆烘干等工序依次完成涂装。 本项目采用干式喷漆室3C1B,各步骤具体操作如下: a.调漆 在喷漆之前应首先完成调漆工作,本项目调漆在专门的调漆间内自动完成,采用电动柱塞泵将漆料打入调配罐进行调制,室内空调送风。调漆采用漆料、稀释剂、固化剂进行调制。在更换颜色时,对调漆系统、漆料输送系统及喷枪均需要进行清洗。 调漆车间有调漆废气(G1-16)产生采用活性炭吸附处理,同时还有废油漆桶(S5)、废活性炭产生(S3)、空调循环冷却水(W4)。 b.喷涂 工艺原理:本项目底漆喷涂、色漆喷涂均采用旋杯式静电喷涂机器人进行喷涂,清漆采用喷枪或旋杯式静电喷涂机器人进行喷涂。自动静电旋杯涂装是应用一个具有锐利边缘的金属杯高速旋转产生的离心力使涂料雾化,旋杯上带有负高压静电荷,在其杯口边缘产生充分的电晕放电,**料被送到旋转内壁,受离心力作用便向四周扩散而形成均匀的薄膜状态,沿旋杯口切线方向流动,涂料受到强电场力的分裂作用进一步雾化成为涂料微粒,与此同时,涂料微粒亦获得了负电荷,成为负离子状涂料粒子,在电场力和离心力的作用下,涂料粒子呈弧状迅速向接地良好的工件表面吸附,于是涂料便均匀而牢固地吸附在工件的表面上。项目在密闭喷漆间内由机器人依次完成内外饰零部件喷涂。机器人喷涂完成后由人工进行检查,并在漏喷处进行补喷,喷涂过程中产生会产生喷漆废气(G1-3、G1-5、G1-7)。 密闭喷漆间均采用上送风下抽风的水旋喷漆室,喷漆室工作时产生含甲苯、二甲苯、非甲烷总烃和漆雾等废气,漆雾与水充分接触而被水吸收,净化效率90%以上。经水旋喷漆室处理后的喷漆室废气,采取玻璃纤维过滤棉进一步过滤漆雾后,和流平室废气汇合送至一套RTO焚烧装置处理,净化效率95%,净化后经DA008排气筒排放。产生漆渣沉淀池废气(G1-17)、RTO焚烧炉天然气燃烧废气(G1-18)、涂装废水(W6)、油漆渣(S1)、废过滤棉(S4)、废蓄热陶瓷体(S8)。 c.流平 每一层漆料喷涂结束后,被喷涂的车身在密闭的、具有一定空气流速的流平室内停,底漆和色漆停留10min,清漆停留15min,主要目的是将湿漆工件表面的溶剂挥发一部分,起到表干的作用,从而保证了漆膜的平整度和**度,并保证后续喷涂的质量。流平室与喷漆室为一体结构,流平过程挥发的有机废气纳入喷漆室废气处理系统一并处理。该工序产生流平废气(G1-4、G1-6、G1-8)。 d.烘干 清漆喷涂后的车身经滑橇转移烘干,烘干温度为80~90℃,烘干时间45min。加热方式为间接加热,采用天然气燃烧产生的热风对流循环,该工序产生烘干废气(G1-9)及燃天然气废气(G1-10)。 e.强冷(风冷) 经过烘干后的塑件会通过风冷室降温到室温,进而便于进行后道工段。该工序产生强冷废气(G1-11)。 (4)精修 因各种原因影响,涂件表面难免有些小颗粒、脏点、流痕等影响外观质量的缺陷,设置精修工段消除这些缺陷,使涂件表面更美观。精修是零部件清漆彻底干燥后进行的作业份,包括打磨和点修补两个工位。打磨采用砂纸人工打磨,如有流痕,先用刨刀刨平,再用砂纸打磨。该工序产生精修废气(G1-12)、打磨砂纸及废擦拭材料(S9)。 (5)补漆喷涂及烘干 对于喷漆质量较好但是有细微瑕疵的车辆在补漆房中进行清漆点补,涂装车间共设有1个补漆房。点补漆采用人工喷涂,天然气加热烘干,产生补漆废气(G1-13)、烘干废气(G1-14)、燃气废气(G1-15)。 (6)喷枪及调漆间油桶换色清洗 喷枪换色清洗在涂装线体内进行,清洗过程产生的少量挥发性有机废气(G1-19)通过喷漆室配套的rto焚烧炉废气处理措施处理后由排气筒DA008排放。调漆间油漆桶清洗过程产生的少量挥发性有机废气(G1-20)通过调漆室配套的活性炭废气处理措施处理后由排气筒DA008排放。清洗工程产生废清洗剂(溶剂型)(S10)经工作区配套的回收装置收集后作危废处理。 (7)滑撬清洗(制具清洗) 在喷涂过程中,挂架上会喷上油漆,此工序就是清洗挂架上的残留油漆。对滑撬进行清洗,滑撬清洗废水(W5)为连续排放。 4、南厂内饰车间注塑生产线:注塑工艺按照产品单元化,操作少人化,经济实用的原则进行规划,注塑机设备系统,将储料斗中的原料通过吸料风机输送至注塑机干燥料筒,(注塑机和料桶由软管连接)进行干燥,然后通过加热线圈加热,使原料熔融。原料熔化后在外动力油马达作用下驱动旋转的螺杆,沿着螺槽向前输送并压实;物料在外加热和螺杆剪切的双重作用下逐渐地塑化、熔融和均化;当螺杆旋转时,物料在螺槽摩擦力及剪切力的作用下把已熔融的物料推到螺杆的头部,与此同时,螺杆在物料的反作用力的作用下,以高压高速,将储料室的熔融料通过喷嘴注射到模具的型腔中,过程中模具通过模温机进行预热;型腔中的熔料经过保压、冷水机冷却、固化定型后,模具在合模机构的作用下,开启模具,并通过顶出装置把定型好的制件从模具顶出,然后通过三轴机械手/六轴机器人将产品从注塑机中取出,并进行自动剪胶口,对于合格的产品人工放入工装车,运输到产品存储区。 5、南厂内饰车间门板手喷生产线: 工艺流程及产污节点 预处理→人手上件(满足节拍)→自动静电除尘(满足节拍)→人工喷漆(90秒)→流平(5分钟)→烘烤(85±5℃,恒温30分钟)→自然冷却(>15分钟)→人手下件(满足节拍)。 (1)预处理 南厂内饰车间门板手喷线门板件预处理脱脂依托北厂外饰车间涂装生产线进行,脱脂后的门板件返回南厂内饰车间门板手喷线。该过程产生脱脂废液(W1)、脱脂废水(W2)。 (2)人手上件 输送链支撑立柱采用100*100mm型钢方通,以12mm厚码板与地面用M16的膨胀螺丝固定。人员上件工位上配LED照明,照度为500LUX。为方便人手上件和下件,吊挂工件包络面最下面离地高为400mm,并在上件/下件区位的合适位置设急停开关1个,急停开关带安全盖。 (3)自动静电除尘 室体采用1.5mm厚的无花镀锌板拆制而成;配合悬挂输送链,室体长度(依工件行进方向)为2500mm,采用吹尘风刀,安装于除尘室内两侧,吹扫工件表面浮尘。经预处理后的门板件含尘量极小,底部吸风。除尘室正面壁板上、离地面1.2米高配8mm厚钢化玻璃观察窗,玻璃窗高为1。 (4)人工喷涂(色漆、清漆) 调漆间完成手喷漆调配。产生调漆废气G3-6,废油漆桶S5。 喷涂室采用干式结构,配4组过滤小车,每组小车配指针式压差装置,每组过滤小车配6个过滤箱。顶部送风,侧面吸风。顶部送风层过滤器配指针式压差计,以方便动态查看过滤器的堵塞情况。室体顶部送风,喷涂位风速0.4—0.6m/s,喷房为5米宽(依工件行进方向),顶部中间位设180°旋转机构,可将行进中的工件在10秒内旋转180°。产生喷涂废气G3-1、G3-3。S3废活性炭、S4废过滤棉。 (5)流平 立墙采用容重120K双面夹心岩棉板,厚度50mm,双面厚度0.426mm彩钢板,防火等级A1级。每一层漆料喷涂结束后,被喷涂的车身在密闭的、具有一定空气流速的流平室内停,色漆和清漆各停留5min,主要目的是将湿漆工件表面的溶剂挥发一部分,起到表干的作用,从而保证了漆膜的平整度和**度,并保证后续喷涂的质量。流平室与喷漆室为一体结构,流平过程挥发的有机废气纳入喷漆室废气处理系统一并处理。产生流平废气G3-2、G3-4。 (6)烘干 门板件烘干采用电加热炉,电热管加热。加热管集中安装于“风管”中,炉体支撑采用100*100mm型材方通,炉体框架采用10#槽钢等型材制作或加强。炉内运风上送下吸,热风循环直接加热。烘烤温度:85±5℃,恒温30分钟,炉内排废气与活性炭废气处理装置对接。产生烘干废气G3-5、废活性炭S3。 (7)自然冷却 烘干后门板件自然冷却15分钟。 (8)人手下件 冷却至室温后手工下件存放。 6、南厂内饰车间植绒生产线 (1)上件 将待植绒件移至操作平台。 (2)人工擦洗 采用人工抹布蘸涂擦洗液的方法对植绒件表面的灰尘、油脂等杂质进行擦洗。产生废抹布(S6)。 (3)喷胶 将表面处理好的待植绒件进行喷胶处理,喷胶使用水基胶和底涂剂(固化剂)按一定比例混合。上胶采用压送式,空气使用量200—300L/min,胶水喷出量350ml/min。喷胶室保持微负压做到对挥发气体的有效收集,同时闲置的喷枪放置于盛有水的桶中。产生涂胶废气(G2-1)、喷枪放置废水(W7)。 (4)植绒 利用高压静电感应技术原理,对绒毛施加静电,绒毛可按照要求飞往产品表面,植绒过程中无飞扬的绒毛飞出植绒舱,避免影响车间环境,能够完成绒毛的收集。产生植绒废气(G2-2)、废绒毛(S12)。 (5)烘干 采用电加热炉对植绒后的汽车零部件在植绒烘箱中进行烘干。产生烘干废气(G2-3)。 (6)清绒 使用吸绒机对烘干后的零部件进行清绒,去除多余绒毛,使表面绒毛附着更加均匀。产清绒废气(G2-4)、废绒毛(S12)。 7、南厂座椅车间生产线 (1)地毯成型:自动上料加热,网链输送毯坯至下模,人工辅助挂料,模具合模,模压成型,二次动作冲切,人工取件并将半成品放置到余料清理工作台,清理模具,准备铺放下一张面料,主操作手将大边余料投入垃圾车,副操作手辅助余料清理工序,清理冲切后余料,钉装搭扣,将附件按照要求摆放后,使用热熔胶机打胶,将附件按照压痕粘接至地毯背部制定位置,将成品放置成品工装车。粘接工艺主要会产生挥发性有机物, (2)顶棚成型:自动上料加热,网链抛送毯坯至下模,人工辅助挂料,模具合模,模压成型,人工取件并将半成品放置周转工装中,模压后产品放置水切割工装胎具上进行水切割,清理水切割后余料,将附件按照要求摆放后,使用热熔胶机打胶,将附件按照压痕粘接至地毯背部制定位置,背部装订搭扣,将成品放置成品工装车。 (3)包覆生产线 工件采用传送带输送至各个工序,采用人工或半自动化包覆作业方式进行定位、压合、包边、包角、活化;喷胶房采用密闭空间设计,人工/机器人使用喷枪对骨架和蒙皮进行胶水喷涂,喷胶房排烟口使用过滤网棉进行废气过滤。过滤后的废气含有挥发性有机物,采用活性炭吸收+催化燃烧(RCO)处理后经排气筒排放。 8、南厂橡胶车间生产线 (1)炼胶工艺流程: 项目采用开炼、薄通的方法对购入的合成橡胶(EPDM)进行混炼。将胶料加到辊筒上,由于两个辊筒以不同的线速度相对回转,胶料在被辊筒挤压的同时,在摩擦力和粘附力的作用下,被拉入辊隙中(保证辊距在1mm以下),形成楔形端面的胶条。在辊隙中由于速度梯度和辊筒温度的作用致使胶料受到强烈的碾压、撕裂,同时伴随着橡胶分子链的氧化断裂作用。在胶料不断被拉入辊隙的过程为使配合剂尽快混入橡胶中,在辊缝上端应保留一定的堆积胶。当加入配合剂时,由于堆积胶的不断翻转和更替,便把配合剂带进堆积胶的皱纹沟中,并进而带入辊缝中,配合剂混入胶料。 从辊隙中排出的胶片不包辊而直接落在接料盘上,等胶料全都通过辊距后,再将胶料返回到辊距上方重新通过辊距,这样反复数次,直至达到要求的可塑度为止,放入模具成型冷却后检验入库完成炼胶作业。 (3)(橡胶)密封条制品生产工艺流程: 成型的胶条经检具后送入锯切机中根据不同密封条所需要的长度进行裁断,裁断后的密封条收尾进行接合然后检验入库。部分完成接合后的密封条需进行角部喷涂,采用人工喷漆后晾干检验入库。 (4)(橡胶)减震制品生产工艺流程 将加工完成的密封条及其它组件进行组装,完成各类总成产品检验入库。 | 实际建设情况:1、北厂座椅车间发泡生产线:座椅发泡:首先使用专用清模工具,对模具型腔及分型面进行清理;然后使用专用喷枪,将脱模剂均匀喷涂于已清理干净的模腔内,防止产品粘模;根据嵌件规格将对应的嵌件放入正确的模腔内;混料设备按生产计划和配料单进行A料配制,把B料抽入储料罐,备用于发泡生产;使用高压发泡机及高精度混合枪头,按照设定比例将混料黑白料,浇注于指定模腔内、保压、熟化;然后起模进行自检互检;使用机械开孔机或真空开孔机对出模的产品进行开孔处理;之后使用自动喷码机或日期章进行产品喷码;依据修补标准对产品进行修补;检验员对产品进行终检,之后产品进入后熟化区进行熟化。 /2、北厂外饰车间注塑生产线:注塑工艺按照产品单元化,操作少人化,经济实用的原则进行规划,注塑机设备系统,将储料斗中的原料通过吸料风机输送至注塑机干燥料筒,(注塑机和料桶由软管连接)进行干燥,然后通过加热线圈加热,使原料熔融。原料熔化后在外动力油马达作用下驱动旋转的螺杆,沿着螺槽向前输送并压实;物料在外加热和螺杆剪切的双重作用下逐渐地塑化、熔融和均化;当螺杆旋转时,物料在螺槽摩擦力及剪切力的作用下把已熔融的物料推到螺杆的头部,与此同时,螺杆在物料的反作用力的作用下,以高压高速,将储料室的熔融料通过喷嘴注射到模具的型腔中,过程中模具通过模温机进行预热;型腔中的熔料经过保压、冷水机冷却、固化定型后,模具在合模机构的作用下,开启模具,并通过顶出装置把定型好的制件从模具顶出,然后通过三轴机械手/六轴机器人将产品从注塑机中取出,并进行自动剪胶口,对于合格的产品人工放入工装车,运输到产品存储区。 3、北厂外饰车间涂装生产线: (1)上件:项目所需喷涂注塑件进入上件区进行上件。 (2)表面预处理: a.预脱脂和脱脂:脱脂分预脱脂及脱脂两部分,脱脂主要是用酸性溶液靠皂化、乳化作用或浸透溶解除去塑料件表面的油污,其后水洗的主要作用是清洗工件表面带出来的脱脂剂。预脱脂用于除去零部件产品油污,采用喷淋方式,喷淋时间为90s,脱脂用于除去油污,采用喷淋方式,喷淋时间为120s。预脱脂液及脱脂液温度均为50~60℃。预脱脂及脱脂槽均需定期换槽液,产生脱脂废液(W1)经管道排****处理站脱脂废液预处理系统。 b.水洗(三级水洗+纯水洗):为了冲洗干净车身表面残留的脱脂剂在脱脂后设三级水洗(水洗1、水洗2、水洗3)及一级纯水洗工序。三道水洗均为喷淋水洗,采用常温工业水喷淋60s,纯水洗利用喷淋管进行喷淋水洗,生产中纯水喷淋后废水流向3#水洗槽用于水洗3后向2#水洗槽溢流用于水洗2,2#水洗槽液向1#水洗槽保持溢流用于水洗1,1#水洗槽溢流水排出。1#槽槽液每周更新一次,2#槽槽液每两周更新一次,3#槽槽液每两周更新一次,产生脱脂废水(W2),主要污染物为COD、SS、总氮、石油类等。纯水制备工程中产生的浓水(W8)。 c.吹水:为去除内外饰零部件表面水分,利用风吹对内外饰零部件进行自动吹水,再人工进行**吹水。生产人员进涂装室需除静电,并定期对工作服进行清洗及地面清扫,产生洗衣及清扫废水(W3)。 d.水分烘干:将内外饰零部件的表面水分烘干,烘干温度75-85℃。烘干方式为间接加热,采用天然气燃烧加热产生的热风对流循环,该工序烘干废气主要污染物是水蒸气,故本次环评不做分析。该工序产生燃烧天然气废气(G1-1)。 e.强冷(风冷):经过烘干后的塑件会通过风冷室降温到室温,进而便于进行后道工段。 f.火焰处理:合格的塑件经输送链输送至车间的喷涂区域,在输送过程中完成自然冷却,经过观察室进入火焰处理室,该室用天然气燃烧火焰烧工件表面,火焰温度的为1000~2500℃,空气稍过量以使燃烧完全,处理时间需短,火焰处理可使型料表面层分子局部氧化,产生-COOH、-CO等极性基团,以增加塑料件的表面性能、提高塑料表面的浸润性和附着力,还可消除塑料表面的毛刺。本过程采用机器人自动控制完成,产生燃气废气(G1-2)。 (3)喷涂:喷涂件设计时需涂装3道涂层,分别为底漆、色漆、清漆,设置调漆室、喷漆室、流平室、烘干室和强冷室等组成一条喷漆线。项目调漆过程在集中供漆系统完成。将各种油漆与稀释剂、固化剂调和后,输送至各喷漆室喷枪处使用。喷漆工段按底漆喷漆、流平→色漆喷漆、流平→面漆喷漆、流平→清漆烘干等工序依次完成涂装。 本项目采用干式喷漆室3C1B,各步骤具体操作如下: a.调漆 在喷漆之前应首先完成调漆工作,本项目调漆在专门的调漆间内自动完成,采用电动柱塞泵将漆料打入调配罐进行调制,室内空调送风。调漆采用漆料、稀释剂、固化剂进行调制。在更换颜色时,对调漆系统、漆料输送系统及喷枪均需要进行清洗。 调漆车间有调漆废气(G1-16)产生采用活性炭吸附处理,同时还有废油漆桶(S5)、废活性炭产生(S3)、空调循环冷却水(W4)。 b.喷涂 工艺原理:本项目底漆喷涂、色漆喷涂均采用旋杯式静电喷涂机器人进行喷涂,清漆采用喷枪或旋杯式静电喷涂机器人进行喷涂。自动静电旋杯涂装是应用一个具有锐利边缘的金属杯高速旋转产生的离心力使涂料雾化,旋杯上带有负高压静电荷,在其杯口边缘产生充分的电晕放电,**料被送到旋转内壁,受离心力作用便向四周扩散而形成均匀的薄膜状态,沿旋杯口切线方向流动,涂料受到强电场力的分裂作用进一步雾化成为涂料微粒,与此同时,涂料微粒亦获得了负电荷,成为负离子状涂料粒子,在电场力和离心力的作用下,涂料粒子呈弧状迅速向接地良好的工件表面吸附,于是涂料便均匀而牢固地吸附在工件的表面上。项目在密闭喷漆间内由机器人依次完成内外饰零部件喷涂。机器人喷涂完成后由人工进行检查,并在漏喷处进行补喷,喷涂过程中产生会产生喷漆废气(G1-3、G1-5、G1-7)。 密闭喷漆间均采用上送风下抽风的水旋喷漆室,喷漆室工作时产生含甲苯、二甲苯、非甲烷总烃和漆雾等废气,漆雾与水充分接触而被水吸收,净化效率90%以上。经水旋喷漆室处理后的喷漆室废气,采取玻璃纤维过滤棉进一步过滤漆雾后,和流平室废气汇合送至一套RTO焚烧装置处理,净化效率95%,净化后经DA008排气筒排放。产生漆渣沉淀池废气(G1-17)、RTO焚烧炉天然气燃烧废气(G1-18)、涂装废水(W6)、油漆渣(S1)、废过滤棉(S4)、废蓄热陶瓷体(S8)。 c.流平 每一层漆料喷涂结束后,被喷涂的车身在密闭的、具有一定空气流速的流平室内停,底漆和色漆停留10min,清漆停留15min,主要目的是将湿漆工件表面的溶剂挥发一部分,起到表干的作用,从而保证了漆膜的平整度和**度,并保证后续喷涂的质量。流平室与喷漆室为一体结构,流平过程挥发的有机废气纳入喷漆室废气处理系统一并处理。该工序产生流平废气(G1-4、G1-6、G1-8)。 d.烘干 清漆喷涂后的车身经滑橇转移烘干,烘干温度为80~90℃,烘干时间45min。加热方式为间接加热,采用天然气燃烧产生的热风对流循环,该工序产生烘干废气(G1-9)及燃天然气废气(G1-10)。 e.强冷(风冷) 经过烘干后的塑件会通过风冷室降温到室温,进而便于进行后道工段。该工序产生强冷废气(G1-11)。 (4)精修 因各种原因影响,涂件表面难免有些小颗粒、脏点、流痕等影响外观质量的缺陷,设置精修工段消除这些缺陷,使涂件表面更美观。精修是零部件清漆彻底干燥后进行的作业份,包括打磨和点修补两个工位。打磨采用砂纸人工打磨,如有流痕,先用刨刀刨平,再用砂纸打磨。该工序产生精修废气(G1-12)、打磨砂纸及废擦拭材料(S9)。 (5)补漆喷涂及烘干 对于喷漆质量较好但是有细微瑕疵的车辆在补漆房中进行清漆点补,涂装车间共设有1个补漆房。点补漆采用人工喷涂,天然气加热烘干,产生补漆废气(G1-13)、烘干废气(G1-14)、燃气废气(G1-15)。 (6)喷枪及调漆间油桶换色清洗 喷枪换色清洗在涂装线体内进行,清洗过程产生的少量挥发性有机废气(G1-19)通过喷漆室配套的rto焚烧炉废气处理措施处理后由排气筒DA008排放。调漆间油漆桶清洗过程产生的少量挥发性有机废气(G1-20)通过调漆室配套的活性炭废气处理措施处理后由排气筒DA008排放。清洗工程产生废清洗剂(溶剂型)(S10)经工作区配套的回收装置收集后作危废处理。 (7)滑撬清洗(制具清洗) 在喷涂过程中,挂架上会喷上油漆,此工序就是清洗挂架上的残留油漆。对滑撬进行清洗,滑撬清洗废水(W5)为连续排放。 4、南厂内饰车间注塑生产线:注塑工艺按照产品单元化,操作少人化,经济实用的原则进行规划,注塑机设备系统,将储料斗中的原料通过吸料风机输送至注塑机干燥料筒,(注塑机和料桶由软管连接)进行干燥,然后通过加热线圈加热,使原料熔融。原料熔化后在外动力油马达作用下驱动旋转的螺杆,沿着螺槽向前输送并压实;物料在外加热和螺杆剪切的双重作用下逐渐地塑化、熔融和均化;当螺杆旋转时,物料在螺槽摩擦力及剪切力的作用下把已熔融的物料推到螺杆的头部,与此同时,螺杆在物料的反作用力的作用下,以高压高速,将储料室的熔融料通过喷嘴注射到模具的型腔中,过程中模具通过模温机进行预热;型腔中的熔料经过保压、冷水机冷却、固化定型后,模具在合模机构的作用下,开启模具,并通过顶出装置把定型好的制件从模具顶出,然后通过三轴机械手/六轴机器人将产品从注塑机中取出,并进行自动剪胶口,对于合格的产品人工放入工装车,运输到产品存储区。 5、南厂内饰车间门板手喷生产线: 工艺流程及产污节点 预处理→人手上件(满足节拍)→自动静电除尘(满足节拍)→人工喷漆(90秒)→流平(5分钟)→烘烤(85±5℃,恒温30分钟)→自然冷却(>15分钟)→人手下件(满足节拍)。 (1)预处理 南厂内饰车间门板手喷线门板件预处理脱脂依托北厂外饰车间涂装生产线进行,脱脂后的门板件返回南厂内饰车间门板手喷线。该过程产生脱脂废液(W1)、脱脂废水(W2)。 (2)人手上件 输送链支撑立柱采用100*100mm型钢方通,以12mm厚码板与地面用M16的膨胀螺丝固定。人员上件工位上配LED照明,照度为500LUX。为方便人手上件和下件,吊挂工件包络面最下面离地高为400mm,并在上件/下件区位的合适位置设急停开关1个,急停开关带安全盖。 (3)自动静电除尘 室体采用1.5mm厚的无花镀锌板拆制而成;配合悬挂输送链,室体长度(依工件行进方向)为2500mm,采用吹尘风刀,安装于除尘室内两侧,吹扫工件表面浮尘。经预处理后的门板件含尘量极小,底部吸风。除尘室正面壁板上、离地面1.2米高配8mm厚钢化玻璃观察窗,玻璃窗高为1。 (4)人工喷涂(色漆、清漆) 调漆间完成手喷漆调配。产生调漆废气G3-6,废油漆桶S5。 喷涂室采用干式结构,配4组过滤小车,每组小车配指针式压差装置,每组过滤小车配6个过滤箱。顶部送风,侧面吸风。顶部送风层过滤器配指针式压差计,以方便动态查看过滤器的堵塞情况。室体顶部送风,喷涂位风速0.4—0.6m/s,喷房为5米宽(依工件行进方向),顶部中间位设180°旋转机构,可将行进中的工件在10秒内旋转180°。产生喷涂废气G3-1、G3-3。S3废活性炭、S4废过滤棉。 (5)流平 立墙采用容重120K双面夹心岩棉板,厚度50mm,双面厚度0.426mm彩钢板,防火等级A1级。每一层漆料喷涂结束后,被喷涂的车身在密闭的、具有一定空气流速的流平室内停,色漆和清漆各停留5min,主要目的是将湿漆工件表面的溶剂挥发一部分,起到表干的作用,从而保证了漆膜的平整度和**度,并保证后续喷涂的质量。流平室与喷漆室为一体结构,流平过程挥发的有机废气纳入喷漆室废气处理系统一并处理。产生流平废气G3-2、G3-4。 (6)烘干 门板件烘干采用电加热炉,电热管加热。加热管集中安装于“风管”中,炉体支撑采用100*100mm型材方通,炉体框架采用10#槽钢等型材制作或加强。炉内运风上送下吸,热风循环直接加热。烘烤温度:85±5℃,恒温30分钟,炉内排废气与活性炭废气处理装置对接。产生烘干废气G3-5、废活性炭S3。 (7)自然冷却 烘干后门板件自然冷却15分钟。 (8)人手下件 冷却至室温后手工下件存放。 6、南厂内饰车间植绒生产线 (1)上件 将待植绒件移至操作平台。 (2)人工擦洗 采用人工抹布蘸涂擦洗液的方法对植绒件表面的灰尘、油脂等杂质进行擦洗。产生废抹布(S6)。 (3)喷胶 将表面处理好的待植绒件进行喷胶处理,喷胶使用水基胶和底涂剂(固化剂)按一定比例混合。上胶采用压送式,空气使用量200—300L/min,胶水喷出量350ml/min。喷胶室保持微负压做到对挥发气体的有效收集,同时闲置的喷枪放置于盛有水的桶中。产生涂胶废气(G2-1)、喷枪放置废水(W7)。 (4)植绒 利用高压静电感应技术原理,对绒毛施加静电,绒毛可按照要求飞往产品表面,植绒过程中无飞扬的绒毛飞出植绒舱,避免影响车间环境,能够完成绒毛的收集。产生植绒废气(G2-2)、废绒毛(S12)。 (5)烘干 采用电加热炉对植绒后的汽车零部件在植绒烘箱中进行烘干。产生烘干废气(G2-3)。 (6)清绒 使用吸绒机对烘干后的零部件进行清绒,去除多余绒毛,使表面绒毛附着更加均匀。产清绒废气(G2-4)、废绒毛(S12)。 7、南厂座椅车间生产线 (1)地毯成型:自动上料加热,网链输送毯坯至下模,人工辅助挂料,模具合模,模压成型,二次动作冲切,人工取件并将半成品放置到余料清理工作台,清理模具,准备铺放下一张面料,主操作手将大边余料投入垃圾车,副操作手辅助余料清理工序,清理冲切后余料,钉装搭扣,将附件按照要求摆放后,使用热熔胶机打胶,将附件按照压痕粘接至地毯背部制定位置,将成品放置成品工装车。粘接工艺主要会产生挥发性有机物, (2)顶棚成型:自动上料加热,网链抛送毯坯至下模,人工辅助挂料,模具合模,模压成型,人工取件并将半成品放置周转工装中,模压后产品放置水切割工装胎具上进行水切割,清理水切割后余料,将附件按照要求摆放后,使用热熔胶机打胶,将附件按照压痕粘接至地毯背部制定位置,背部装订搭扣,将成品放置成品工装车。 (3)包覆生产线 工件采用传送带输送至各个工序,采用人工或半自动化包覆作业方式进行定位、压合、包边、包角、活化;喷胶房采用密闭空间设计,人工/机器人使用喷枪对骨架和蒙皮进行胶水喷涂,喷胶房排烟口使用过滤网棉进行废气过滤。过滤后的废气含有挥发性有机物,采用活性炭吸收+催化燃烧(RCO)处理后经排气筒排放。 8、南厂橡胶车间生产线 (1)炼胶工艺流程: 项目采用开炼、薄通的方法对购入的合成橡胶(EPDM)进行混炼。将胶料加到辊筒上,由于两个辊筒以不同的线速度相对回转,胶料在被辊筒挤压的同时,在摩擦力和粘附力的作用下,被拉入辊隙中(保证辊距在1mm以下),形成楔形端面的胶条。在辊隙中由于速度梯度和辊筒温度的作用致使胶料受到强烈的碾压、撕裂,同时伴随着橡胶分子链的氧化断裂作用。在胶料不断被拉入辊隙的过程为使配合剂尽快混入橡胶中,在辊缝上端应保留一定的堆积胶。当加入配合剂时,由于堆积胶的不断翻转和更替,便把配合剂带进堆积胶的皱纹沟中,并进而带入辊缝中,配合剂混入胶料。 从辊隙中排出的胶片不包辊而直接落在接料盘上,等胶料全都通过辊距后,再将胶料返回到辊距上方重新通过辊距,这样反复数次,直至达到要求的可塑度为止,放入模具成型冷却后检验入库完成炼胶作业。 (3)(橡胶)密封条制品生产工艺流程: 成型的胶条经检具后送入锯切机中根据不同密封条所需要的长度进行裁断,裁断后的密封条收尾进行接合然后检验入库。部分完成接合后的密封条需进行角部喷涂,采用人工喷漆后晾干检验入库。 (4)(橡胶)减震制品生产工艺流程 将加工完成的密封条及其它组件进行组装,完成各类总成产品检验入库。 |
无 | 是否属于重大变动:|
环保设施或环保措施
(一)严格落实废气污染防治措施。运营期北厂外饰车间喷涂废气主要含有挥发性有机物,采用水旋柜+过滤棉+RTO燃烧处理后经高27米排气筒(DA001)排放;清漆固化炉1#、清漆固化炉2#、水份烘干炉、返修(补漆)烘干炉天然气燃烧采用低氮燃烧技术,废气分别经高17米排气筒(DA009、DA012、DA013、DA014)排放;漆渣池废气含挥发性有机物,经活性炭吸附后经高15米排气筒(DA015)排放;注塑废气、北厂座椅车间发泡废气主要含有挥发性有机物,经滤棉+活性炭+RCO炉处理后分别经高21米排气筒(DA002、DA003)排放。 运营期南厂座椅车间发泡废气主要含有挥发性有机物,经过滤棉+活性炭浓缩+RCO 炉处理后经高21米排气筒(DA004)排放;焊接废气颗粒物经滤筒过滤后经高15米排气筒(DA005)排放;热熔粘接废气含挥发性有机物,经UV光解+活性炭过滤后经15米高排气筒(DA006)排放。内饰车间注塑废气含有挥发性有机废气,经干式过滤器+活性炭浓缩+催化燃烧后经15米排气筒(DA007)放;门板手喷涂生产线废气含挥发性有机物,经过滤棉+活性炭吸附处理后经15米高排气筒(DA010)排放;植绒废气经布袋除尘+活性炭吸附处理后经15米排气筒(DA011)排放。橡胶件加工废气含有颗粒物和挥发性有机物,经干式过滤+等离子体+活性炭过滤后经15米高排气筒(DA008)排放。 DA001、DA005、DA010、DA011、DA015执行《大气污染物综合排放标准》(GB16297-1996)表2二级标准限值;DA002、DA003、DA004、DA006、DA007、DA008执行《合成树脂工业污染物排放标准》(GB31572-2015)表5标准限值;DA009、DA012、DA013、DA014执行《锅炉大气污染物排放标准》(GB13271-2014)表3大气污染物特别标准限值;厂内执行《挥发性有机物无组织排放控制标准》(GB37822-2019)特别排放限值;厂界执行《大气污染物综合排放标准》(GB16297-1996)表2二级标准。 按照《重污染天气重点行业应急减排措施制定技术指南》制定重污染天气应急预案,依法报备,按预案文件规定适时启动运行。 按《重点行业应急减排措施制定技术指南(2020年修订版)》对工业涂装业B级企业的要求优化项目工艺设计、污染防治措施及应急减排措施。 建设项目所排污染物国家标准已规定特别排放限值的一律执行,目前国家排放标准中暂未规定特别排放限值的,待相应排放标准修订或修改后,建设项目需执行相应特别排放限值,执行时间与排放标准实施时间或标准修改单发布时间同步。 项目建成后,你公司主要大气污染物挥发性有机物、二氧化硫、氮氧化物、颗粒物年排放总量不得超过35.395吨、0.335吨、2.697吨、6.121吨。 (二)严格落实各类废水污染防治措施。 项目污水委托****污水处理站预处****处理厂协议约定的污染物浓度限值后,****处理厂深度处理达到《****处理厂污染物排放标准》(GB18918-2002)一级A标准后排入新埠河。 项目建成后,公司水主要污染物化学需氧量、氨氮、年排放总量不得超过5.606吨、0.56吨。 因项目污水委托****处理,公司排水总量、水主要污染物排放总量纳入****排污许可监管。 (三)严格落实噪声污染防治措施。通过选用低噪声设备、对高噪声设备采取减震、消声、隔声等措施,确保营运期厂界噪声达到《工业企业厂界环境噪声排放标准》(GB12348-2008)南厂东厂界执行4类标准,其它厂界执行3类标准。 (四)严格落实固体废物处置措施。根据国家和地方的有关规定,按照“减量化、**化、无害化”原则,对固体废物进行分类收集、综合利用和处置,确保不造成二次污染。 危险废物按照《危险废物收集贮存运输技术规范》(HJ2025-2012)和《危险废物贮存污染控制标准》(CB18597-2001)及其修改单的要求进行管理,收集时根据危险废物的种类、数量、危险特性、物理形态、运输要求等因素选择合适的包装形式,集中到危险废物仓库暂存。 项目建成后,全厂固体废物产生量1083.489吨/年,其中危险废物413.189吨/年,一般固体废物670.3吨/年。危险废物主要有HW06(900-402-06)废溶剂型清洗溶剂(14.363吨/年),HW08(900-217-08)废润滑油(1.5吨/年),HW12(900-252-12)油漆渣(130.028吨/年)、打磨砂纸及废擦拭材料(2吨/年),HW49(900-041-49)废活性炭(237.08吨/年)、废过滤材料(1吨/年)、废油漆桶(8.5吨/年)、含油抹布及手套(2.2吨/年)、废蓄热陶瓷体(3吨/年)等,按危险废物管理要求收集暂存后委托有资质的单位处置。 (五)严格落实各项风险控制措施。严格落实环境风险防范各项措施。建立健全环境风险防控体系和事故排放污染物收集系统。落实环境风险防范措施,加大环境风险监控力度,及时监控,防止污染扩散。制定环境风险应急防范预案,按照《企业事业单位突发环境事件应急预案备案管理办法(试行)》(环发〔2015〕4号)的管理要求进行备案。完善环境风险事故预防、应急处理设施建设和物资储备,加强职工培训,定期开展环境风险应急防范预案演练。 (六)根据该项目环境影响报告书分析,项目无需设置大气防护距离。项目卫生防护距离、安全距离的设置及管理****门市****委员会、****管理局确认后执行。 (七)在项目的建设和营运过程中,应建立畅通的公众参与平台,加强与周边公众的沟通,及时解决公众担忧和提出的环境问题,满足公众合理的环境保护要求,定期发布企业环境信息,并主动接受社会监督。 | 实际建设情况:1、废水 项目实施后,厂区废水采用雨污分流,清污分流,分质处理的整体原则。全厂废水可以分为生活污水和生产废水两类。生活污水主要来自员工的日常生活、住宿及食堂等,生产废水主要来自各生产车间及冷却循环水系统排水、纯水系统浓盐水等清排水。各车间及道路雨水经管网收集后排入来龙河。 项目厂区被**路分为南北两个部分,北厂生产废水来自北厂外饰车间涂装线零部件清洗废水、涂装线喷涂漆雾处理废水、配套纯水制备系统排放浓水,北厂外饰车间废水****处理站处理,脱脂废液至涂装废液预处理系统处理后同脱脂废水、洗衣及清扫废水、洗衣及清扫废水、涂装喷淋废水至涂装废水预处理系统(混凝沉淀工艺)再经生化处理系统(水解酸化+生物接触氧化+沉淀工艺)处理达标后同涂装喷淋废水、涂装喷淋废水由长城整车厂区西部工业污水总排口经市政工业污水****处理厂。 项目北厂生活办公废水****处理站处理达标后由长城整车厂区西部污水排放****处理厂。 项目南厂橡胶车间废水主要为泡胶池里面的水性隔离剂,每月一换,换下的废水由吨桶收集,置于厂房外东北角,定期由有资质单位转运处理。南厂内饰车间门板手喷线喷枪清洗水和南厂内饰车间植绒线喷枪放置废水用桶盛装作为危废,当收集桶满后由有资质单位转运至精工联合危废暂存间,定期由有资质单位转运处理。南厂生产废水由多介质过滤器预处理后暂存于水切污水池,再由厂区罐车定期运至****处理站处理,运至北厂外饰车间同涂装线废水****处理站****处理厂工业废水纳管标准相关要求。****处理厂处理达《****处理厂污染物排放标准》(GB18918-2002)一级A标准后排入新埠河。 项目南厂生活废水经南厂化粪池处理后由南厂生活污水排口进市政****处理厂处理后排入新埠河。 2、废气 项目分为南厂区、北厂区:南厂内饰车间注塑废气中非甲烷总烃经活性炭吸附后通过高15米排气筒DA002排放;南厂内饰车间门板手喷生产线废气中颗粒物、非甲烷总烃、甲苯、二甲苯经活性炭箱处理后通过高15米排气筒DA010排放;南厂内饰车间植绒生产线废气中颗粒物、非甲烷总烃经UV光氧+活性炭吸附后通过高15米排气筒DA009排放;南厂座椅车间焊接废气中颗粒物与发泡废气中非甲烷总烃经催化燃烧(RCO)+活性炭吸附后通过高15米排气筒DA003排放;南厂座椅车间粘接废气中非甲烷总烃经滤筒除尘器后通过高17米排气筒DA005排放;南厂橡胶车间废气中颗粒物、甲苯、二甲苯、非甲烷总烃、二硫化碳经低温等离子+活性炭吸附处理后通过高15米排气筒DA007排放。 北厂座椅车间发泡废气中非甲烷总烃经催化燃烧(RCO)+活性炭吸附处理后通过高21米排气筒DA006排放;北厂外饰车间注塑废气中非甲烷总烃经活性炭吸附处理后通过高21米排气筒DA001排放;北厂外饰车间涂装废气中颗粒物、非甲烷总烃、二甲苯、甲苯、二氧化硫、氮氧化物经RT0+活性炭吸附处理后通过高27米排气筒DA008排放;北厂外饰车间涂装线清漆固化炉燃气1#废气中颗粒物、二氧化硫、氮氧化物经高17米排气筒DA012直排;北厂外饰车间涂装线清漆固化炉燃气2#废气中颗粒物、二氧化硫、氮氧化物经高17米排气筒DA013直排;北厂外饰车间涂装线水分烘干炉燃气中颗粒物、二氧化硫、氮氧化物经高17米排气筒DA014直排;北厂外饰车间涂装线返修烘干炉燃气中颗粒物、二氧化硫、氮氧化物经高17米排气筒DA015直排;北厂外饰车间涂装线漆渣沉淀池废气中颗粒物、二氧化硫、氮氧化物经高15米排气筒DA011直排。 3、噪声 项目主要噪声源为生产线设备运行以及风机、各种泵等运行时产生的噪声的一些机械传动设备,噪声源强约75~105dB(A),选用低噪声、振动小的设备,设备基础安装减振器,冲压线全封闭等降噪措施,降低噪声影响。 4、固(液)体废物 建设项目产生的固体废物包括一般工业固体废物、危险固体废物和生活垃圾等。 (1)一般工业固废:本项目南厂、北厂分别设置一般固废暂存间,采取防扬散、防流失、防渗漏“三防”措施,并设置标识标牌。营运期产生的一般固体废物****公司综合利用。企业在委托第三方运输、利用、处置工业固体废物时,对受托方的主体资格和技术能力进行核实,依法签订书面合同,在合同中约定污染防治要求。 (2)危险废物:本项目南厂、北厂产生****公司转运至精工联合危废暂存间,定期交由有资质单位处置。设置的危废间采取防风、防晒、防雨、防渗、防腐等防治措施,并按照《危险废物识别标志设置技术规范》(HJ 1276-2022)规范设置标识标牌。危险废物间内暂存符合《危险废物贮存污染控制标准》(GB18597-2023)要求,危险****公司进行转运处置,转移危险废物按照《危险废物转移管理办法》******部交通运输部部令第23号)要求执行。 (3)其他一般固废:项目营运期生活垃圾集中收集后交由环卫部门统一收集处理。 5、初期雨水收集处理措施 为减轻生产区雨季产生的初期雨水对受纳水体来龙河水质的影响,建设单位设置单独的收集系统进行收集处理。对北厂外饰车间涂装生产线、南厂内饰车间门板手喷所在区域道路雨水管网单独收集,能够有效降低初期雨水对受纳水体来龙河的影响;加强环境监测,初期雨水收集池配备水泵将收集的污水分批次导入污水处理系统调节水池,经处理达标后回用或外排入城市污水管网;加强环境管理,禁止员工向雨水口倾倒垃圾、严禁管道混接和乱接等。 6、地下水污染防治措施 地下水污染防治措施按照“源头控制,分区防治,污染监控,应急响应”原则进行设计。 7、土壤污染防治措施 根据本项目的特点,建设单位采取如下的措施以防止运营期对区域土壤环境造成污染: (1)工程措施 ①项目在运行过程中,应加大对北厂外饰车间涂装生产线废气、南厂内饰车间门板手喷生产线废气的治理力度,确保RTO炉、活性炭箱正常运行,进一步减少甲苯、二甲苯及非甲烷总烃的排放量。 ②严格用水和废水的管理,强调节约用水,防止污水“跑、冒、滴、漏”,污水管道连接均采用胶粘硬连接方式,以避免渗漏。 ③北厂外饰车间涂装生产线、南厂内饰车间门板手喷生产线及油漆库、危险废物暂存间等重点防渗区地面做防渗漏处理,地面涂覆环氧树脂防渗;生产现场及危废暂存间的设备、容器设置防渗漏托盘,防止液体原料或液态危废发生泄漏。 ④设置风险事故应急池,对北厂外饰车间涂装生产线、南厂内饰车间门板手喷生产线事故状态下的消防废水进行收集,防治由于消防废水的下渗对土壤环境造成影响。 (2)管理措施 ①建设单位要加强内部管理,将土壤污染防治纳入项目环境风险防控体系,严格依法依规建设和运行污染治理设施,确保重点污染物稳定达标排放;另外,提供企业员工污染隐患和环境风险防范意识,并定期开展培训。 ②建设单位设置专门管理制度,加强对原辅材料及危险废物的规范化管理,定期巡查维护环保设施的运行情况,及时处理非正常运行情况; ③建设单位应当按照环境保护主管部门的规定和监测规范,对其用地及周边土壤环境每年至少开展一次监测,监测结果如实向环保主管部门备案; ④建立相应制度,对运行期项目可能造成的土壤污染问题承担相应的责任并进行修复,将其列入企业内部的环保管理规定中。 8、环境风险 根据现场调查,本项目环境风险防范措施落实情况如下: ①生产车间:生产车间地坪均进行了地面硬化,对厂房实行分区防渗,划分为重点防渗区、一般防渗区和简单防渗区,并按照防渗要求进行了防渗处理。项目于南厂再内饰与座椅车间之间建设238m3,****园区内)80m3水池;北厂依托长城整车事故池。 ②危险废物暂存间:危险废物暂存间设置环形沟和集水槽,危废暂存区四面墙体、环形沟和集水槽做好防渗防漏处理。 ③化学品储存间:化学品储存间设置环形沟和集水槽,库房四面墙体、环形沟和集水槽做好防渗防漏处理。 ④警示标识:设置了物流名称和危险标识、风险事故应急撤离路线指示牌和风向标。 9、规范化排污口、监测设施及在线监测装置 项目废水、废气排放口及固废暂存场所的设置符合的要求,废水、废气排放口及固废暂存场所均设置了规范的标识标牌,废气排气筒均设置了采样平台及监测采样口,采样口的设置符合《污染源技术规范》要求。 本项目南厂生活污水通过化粪池沉淀后排入市政管网,南厂生产废水收集后运至****处理站与北厂生产废水一****处理站处****处理厂处理达标后排入新埠河。 |
(1)本项目排气筒编号在进行排污申报系统填报后,由于系统问题,排气筒编号产生变化,但未涉及污染物种类的变化。(2)初期雨水池:北厂外饰车间初期雨水收集池依托****整车厂区初期雨水收集池;因场地受限,南厂在现有基础上没有空地建设初期雨水收集池,因此南厂依托曼德北厂初期雨水收集池。 (3)事故应急池:北厂依托****整车厂区事故应急池;南厂在座椅车间与内饰车间空地已238m3并依托曼德北厂区80m3事故池。 (4)危废暂存间:南厂北厂分别建设一般固废暂存间;北厂南厂危废暂存于厂房临时暂存点,****园区内精工联合危废仓库暂存,收集到一定量后交由有资质单位处理。 | 是否属于重大变动:|
其他
无 | 实际建设情况:无 |
无 | 是否属于重大变动:|
3、污染物排放量
0 | 0 | 0 | 0 | 0 | 0 | 0 | |
0 | 0 | 0 | 0 | 0 | 0 | 0 | |
0 | 0 | 0 | 0 | 0 | 0 | 0 | |
0 | 0 | 0 | 0 | 0 | 0 | 0 | |
0 | 0 | 0 | 0 | 0 | 0 | 0 | |
0 | 0 | 0 | 0 | 0 | 0 | 0 | / |
0 | 0.121 | 0.335 | 0 | 0 | 0.121 | 0.121 | / |
0 | 1.765 | 2.679 | 0 | 0 | 1.765 | 1.765 | / |
0 | 5.475 | 6.121 | 0 | 0 | 5.475 | 5.475 | / |
0 | 12.62 | 35.395 | 0 | 0 | 12.62 | 12.62 | / |
4、环境保护设施落实情况
表1 水污染治理设施
1 | 化粪池 | 《****处理厂纳管标准》 | 南厂生活废水经南厂化粪池处理后由南厂生活污水排口进市政****处理厂处理后排入新埠河。 | 生活污水排放口DW001监测结果:pH值的排放浓度为7.5-8.2;动植物油的排放浓度为0.06Lmg/L;化学需氧量的排放浓度为55-56mg/L;五日生化需氧量的排放浓度为18.3-18.9mg/L;氨氮的排放浓度为6.81-9.42mg/L;悬浮物的排放浓度为24mg/L;总磷的排放浓度为0.05-0.06mg/L;总氮的排放浓度为17.5-18.6mg/L。 | |
2 | ****处理站 | 《****处理厂纳管标准》 | 项目厂区被**路分为南北两个部分,北厂生产废水来自北厂外饰车间涂装线零部件清洗废水、涂装线喷涂漆雾处理废水、配套纯水制备系统排放浓水,北厂外饰车间废水****处理站处理,脱脂废液至涂装废液预处理系统处理后同脱脂废水、洗衣及清扫废水、洗衣及清扫废水、涂装喷淋废水至涂装废水预处理系统(混凝沉淀工艺)再经生化处理系统(水解酸化+生物接触氧化+沉淀工艺)处理达标后同涂装喷淋废水、涂装喷淋废水由长城整车厂区西部工业污水总排口经市政工业污水****处理厂。 项目北厂生活办公废水****处理站处理达标后由长城整车厂区西部污水排放****处理厂。 项目南厂橡胶车间废水主要为泡胶池里面的水性隔离剂,每月一换,换下的废水由吨桶收集,置于厂房外东北角,定期由有资质单位转运处理。南厂内饰车间门板手喷线喷枪清洗水和南厂内饰车间植绒线喷枪放置废水用桶盛装作为危废,当收集桶满后暂存于南厂临时危废暂存间,定期由有资质单位转运处理。南厂生产废水由多介质过滤器预处理后暂存于水切污水池,再由厂区罐车定期运至****处理站处理,运至北厂外饰车间同涂装线废水****处理站****处理厂工业废水纳管标准相关要求。****处理厂处理达《****处理厂污染物排放标准》(GB18918-2002)一级A标准后排入新埠河。 | ****处理站的监测报告,满足纳管标准的要求。 |
表2 大气污染治理设施
1 | DA001 | 《大气污染物综合排放标准》(GB16297-1996)表2 | 北厂外饰车间注塑废气中非甲烷总烃经活性炭吸附处理后通过高21米排气筒DA001排放 | 验收监测结果满足要求 | |
2 | DA002 | 《大气污染物综合排放标准》(GB16297-1996)表2 | 南厂内饰车间注塑废气中非甲烷总烃经活性炭吸附后通过高15米排气筒DA002排放 | 验收监测结果满足要求 | |
3 | DA003 | 《合成树脂工业污染物排放标准》(GB31572-2015)表5 | 南厂座椅车间焊接废气中颗粒物与发泡废气中非甲烷总烃经催化燃烧(RCO)+活性炭吸附后通过高15米排气筒DA003排放 | 验收监测满足要求 | |
4 | DA005 | 《大气污染物综合排放标准》(GB16297-1996)表2 | 南厂座椅车间粘接废气中非甲烷总烃经滤筒除尘器后通过高17米排气筒DA005排放 | 验收监测满足要求 | |
5 | DA006 | 《合成树脂工业污染物排放标准》(GB31572-2015)表5 | 北厂座椅车间发泡废气中非甲烷总烃经催化燃烧(RCO)+活性炭吸附处理后通过高21米排气筒DA006排放; | 验收监测满足要求 | |
6 | DA007 | 颗粒物执行《大气污染物综合排放标准》(GB16297-1996)表2;甲苯、二甲苯、挥发性有机物执行《表面涂装(汽车制造业)挥发性有机化合物排放标准》(DB42/1539-2019);臭气浓度执行《恶臭污染物排放标准》(GB14554-93)。 | 南厂橡胶车间废气中颗粒物、甲苯、二甲苯、非甲烷总烃、二硫化碳经低温等离子+活性炭吸附处理后通过高15米排气筒DA007排放 | 验收监测满足要求 | |
7 | DA008 | 甲苯、二甲苯、挥发性有机物执行《表面涂装(汽车制造业)挥发性有机化合物排放标准》(DB42/1539-2019);颗粒物、二氧化硫、氮氧化物执行《表面涂装(汽车制造业)挥发性有机化合物排放标准》(DB42/1539-2019)。 | 北厂外饰车间涂装废气中颗粒物、非甲烷总烃、二甲苯、甲苯、二氧化硫、氮氧化物经RT0+活性炭吸附处理后通过高27米排气筒DA008排放; | 验收监测满足要求 | |
8 | DA009 | 颗粒物执行《大气污染物综合排放标准》(GB16297-1996)表2二级标准;挥发性有机物执行《表面涂装(汽车制造业)挥发性有机化合物排放标准》(DB42/1539-2019) | 南厂内饰车间植绒生产线废气中颗粒物、非甲烷总烃经UV光氧+活性炭吸附后通过高15米排气筒DA009排放 | 验收监测满足要求 | |
9 | DA010 | 颗粒物、挥发性有机物、甲苯、二甲苯执行《大气污染物综合排放标准》(GB16297-1996)表2二级标准 | 南厂内饰车间门板手喷生产线废气中颗粒物、非甲烷总烃、甲苯、二甲苯经活性炭箱处理后通过高15米排气筒DA010排放 | 验收监测满足要求 | |
10 | DA011 | 颗粒物执行《大气污染物综合排放标准》(GB16297-1996)表2二级标准;甲苯、二甲苯、挥发性有机物执行《表面涂装(汽车制造业)挥发性有机化合物排放标准》(DB42/1539-2019)。 | 北厂外饰车间涂装线漆渣沉淀池废气中甲苯、二甲苯、挥发性有机物经活性炭箱处理后经高15米排气筒DA011排放 | 验收监测满足要求 | |
11 | DA012 | 颗粒物、氮氧化物、二氧化硫执行《锅炉大气污染物排放标准》(GB13271-2014)表3大气污染物特别标准限值 | 北厂外饰车间涂装线清漆固化炉燃气1#废气中颗粒物、二氧化硫、氮氧化物经高17米排气筒DA012直排 | 验收监测满足要求 | |
12 | DA013 | 颗粒物、二氧化硫、氮氧化物执行《锅炉大气污染物排放标准》(GB13271-2014)表3大气污染物特别标准限值 | 北厂外饰车间涂装线清漆固化炉燃气2#废气中颗粒物、二氧化硫、氮氧化物经高17米排气筒DA013直排 | 验收监测满足要求 | |
13 | DA014 | 颗粒物、二氧化硫、氮氧化物执行《锅炉大气污染物排放标准》(GB13271-2014)表3大气污染物特别标准限值 | 北厂外饰车间涂装线水分烘干炉燃气中颗粒物、二氧化硫、氮氧化物经高17米排气筒DA014直排 | 验收监测满足要求 | |
14 | DA015 | 颗粒物、氮氧化物、二氧化硫执行《锅炉大气污染物排放标准》(GB13271-2014)表3大气污染物特别标准限值 | 北厂外饰车间涂装线返修烘干炉燃气中颗粒物、二氧化硫、氮氧化物经高17米排气筒DA015直排 | 验收监测满足要求 |
表3 噪声治理设施
1 | 选用低噪声、振动小的设备,设备基础安装减振器,冲压线全封闭等降噪措施,降低噪声影响。 | 南厂厂界东侧噪声执行《工业企业厂界环境噪声排放标准》GB12348-2008表1中4类;南厂厂界南、西、北侧噪声执行《工业企业厂界环境噪声排放标准》GB12348-2008表1中3类 | 项目主要噪声源为生产线设备运行以及风机、各种泵等运行时产生的噪声的一些机械传动设备,噪声源强约75~105dB(A),选用低噪声、振动小的设备,设备基础安装减振器,冲压线全封闭等降噪措施,降低噪声影响。 | 验收监测满足要求 | |
2 | 选用低噪声、振动小的设备,设备基础安装减振器,冲压线全封闭等降噪措施,降低噪声影响。 | 北厂厂界东、南、西、北噪声执行《工业企业厂界环境噪声排放标准》GB12348-2008表1中3类 | 项目主要噪声源为生产线设备运行以及风机、各种泵等运行时产生的噪声的一些机械传动设备,噪声源强约75~105dB(A),选用低噪声、振动小的设备,设备基础安装减振器,冲压线全封闭等降噪措施,降低噪声影响。 | 验收监测满足要求 |
表4 地下水污染治理设施
表5 固废治理设施
1 | (四)严格落实固体废物处置措施。根据国家和地方的有关规定,按照“减量化、**化、无害化”原则,对固体废物进行分类收集、综合利用和处置,确保不造成二次污染。 危险废物按照《危险废物收集贮存运输技术规范》(HJ2025-2012)和《危险废物贮存污染控制标准》(CB18597-2001)及其修改单的要求进行管理,收集时根据危险废物的种类、数量、危险特性、物理形态、运输要求等因素选择合适的包装形式,集中到危险废物仓库暂存。 项目建成后,全厂固体废物产生量1083.489吨/年,其中危险废物413.189吨/年,一般固体废物670.3吨/年。危险废物主要有HW06(900-402-06)废溶剂型清洗溶剂(14.363吨/年),HW08(900-217-08)废润滑油(1.5吨/年),HW12(900-252-12)油漆渣(130.028吨/年)、打磨砂纸及废擦拭材料(2吨/年),HW49(900-041-49)废活性炭(237.08吨/年)、废过滤材料(1吨/年)、废油漆桶(8.5吨/年)、含油抹布及手套(2.2吨/年)、废蓄热陶瓷体(3吨/年)等,按危险废物管理要求收集暂存后委托有资质的单位处置。 | 建设项目产生的固体废物包括一般工业固体废物、危险固体废物和生活垃圾等。 (1)一般工业固废:本项目南厂、北厂分别设置一般固废暂存间,采取防扬散、防流失、防渗漏“三防”措施,并设置标识标牌。营运期产生的一般固体废物****公司综合利用。企业在委托第三方运输、利用、处置工业固体废物时,对受托方的主体资格和技术能力进行核实,依法签订书面合同,在合同中约定污染防治要求。 (2)危险废物:本项目南厂、北厂产生的危险废物转运至精工联合危废暂存间,定期交由有资质单位处置。设置的危废间采取防风、防晒、防雨、防渗、防腐等防治措施,并按照《危险废物识别标志设置技术规范》(HJ 1276-2022)规范设置标识标牌。危险废物间内暂存符合《危险废物贮存污染控制标准》(GB18597-2023)要求,危险****公司进行转运处置,转移危险废物按照《危险废物转移管理办法》******部交通运输部部令第23号)要求执行。 (3)其他一般固废:项目营运期生活垃圾集中收集后交由环卫部门统一收集处理。 |
表6 生态保护设施
表7 风险设施
1 | 项目位于**汽车及零部件产业园,环境风险评价等级为三级。本项目主要危险物质为危险废物、油漆、稀释剂、清洗溶剂等。主要危险单元为危险废物暂存库、储调漆间、原材料库。项目存在的环境风险主要为火灾爆炸等引起的伴生/次生污染物排放、危险物****处理站发生故障引起污染物事故排放等。 项目设置“三级防控”的环境风险防控体系。将事故状态下泄漏的物料、消防废水、污染雨水等均进行收集后进入厂区事故应急池内,做到不影响厂区外环境。经过分析,项目在严格落实环评提出各项措施和要求的前提下,本项目的环境风险在可接受范围内。 | 根据现场调查,本项目环境风险防范措施落实情况如下: ①生产车间:生产车间地坪均进行了地面硬化,对厂房实行分区防渗,划分为重点防渗区、一般防渗区和简单防渗区,并按照防渗要求进行了防渗处理。项目于南厂再内饰与座椅车间之间建设238m3,****园区内)80m3水池;北厂依托长城整车事故池。 ②危险废物暂存间:危险废物暂存间设置环形沟和集水槽,危废暂存区四面墙体、环形沟和集水槽做好防渗防漏处理。 ③化学品储存间:化学品储存间设置环形沟和集水槽,库房四面墙体、环形沟和集水槽做好防渗防漏处理。 ④警示标识:设置了物流名称和危险标识、风险事故应急撤离路线指示牌和风向标。 |
5、环境保护对策措施落实情况
依托工程
(二)严格落实各类废水污染防治措施。 项目污水委托****污水处理站预处****处理厂协议约定的污染物浓度限值后,****处理厂深度处理达到《****处理厂污染物排放标准》(GB18918-2002)一级A标准后排入新埠河。 项目建成后,公司水主要污染物化学需氧量、氨氮、年排放总量不得超过5.606吨、0.56吨。 因项目污水委托****处理,公司排水总量、水主要污染物排放总量纳入****排污许可监管。 | 验收阶段落实情况:项目北厂生产废水来自北厂外饰车间涂装线零部件清洗废水、涂装线喷涂漆雾处理废水、配套纯水制备系统排放浓水,北厂外饰车间废水依托****污水处理站处理,脱脂废液至涂装废液预处理系统处理后同脱脂废水、洗衣及清扫废水、洗衣及清扫废水、涂装喷淋废水至涂装废水预处理系统(混凝沉淀工艺)再经生化处理系统(水解酸化+生物接触氧化+沉淀工艺)处理达标后同涂装喷淋废水、涂装喷淋废水由****厂区西部工业污水总排口经市政工业污水****处理厂。 项目北厂生活办公废水依托****污水处理站处理达标后由****厂区西部污水排放****处理厂。 项目南厂橡胶车间废水主要为泡胶池里面的水性隔离剂,每月一换,换下的废水由吨桶收集,置于厂房外东北角,定期由有资质单位转运处理。南厂内饰车间门板手喷线喷枪清洗水和南厂内饰车间植绒线喷枪放置废水用桶盛装作为危废,当收集桶满后由有资质单位转运至精工联合危废暂存间,定期由有资质单位转运处理。南厂生产废水由多介质过滤器预处理后暂存于水切污水池,再由厂区罐车定期运至****污水处理站处理,运至北厂外饰车间同涂装线废水依托****污水处理站****处理厂工业废水纳管标准相关要求。****处理厂处理达《****处理厂污染物排放标准》(GB18918-2002)一级A标准后排入新埠河。 项目南厂生活废水经南厂化粪池处理后由南厂生活污水排口进市政****处理厂处理后排入新埠河。 |
/ |
环保搬迁
无 | 验收阶段落实情况:无 |
/ |
区域削减
无 | 验收阶段落实情况:无 |
/ |
生态恢复、补偿或管理
无 | 验收阶段落实情况:无 |
/ |
功能置换
无 | 验收阶段落实情况:无 |
/ |
其他
无 | 验收阶段落实情况:无 |
/ |
6、工程建设对项目周边环境的影响
/ |
/ |
/ |
/ |
/ |
/ |
7、验收结论
1 | 未按环境影响报告书(表)及其审批部门审批决定要求建设或落实环境保护设施,或者环境保护设施未能与主体工程同时投产使用 |
2 | 污染物排放不符合国家和地方相关标准、环境影响报告书(表)及其审批部门审批决定或者主要污染物总量指标控制要求 |
3 | 环境影响报告书(表)经批准后,该建设项目的性质、规模、地点、采用的生产工艺或者防治污染、防止生态破坏的措施发生重大变动,建设单位未重新报批环境影响报告书(表)或环境影响报告书(表)未经批准 |
4 | 建设过程中造成重大环境污染未治理完成,或者造成重大生态破坏未恢复 |
5 | 纳入排污许可管理的建设项目,无证排污或不按证排污 |
6 | 分期建设、分期投入生产或者使用的建设项目,其环境保护设施防治环境污染和生态破坏的能力不能满足主体工程需要 |
7 | 建设单位因该建设项目违反国家和地方环境保护法律法规受到处罚,被责令改正,尚未改正完成 |
8 | 验收报告的基础资料数据明显不实,内容存在重大缺项、遗漏,或者验收结论不明确、不合理 |
9 | 其他环境保护法律法规规章等规定不得通过环境保护验收 |
不存在上述情况 | |
验收结论 | 合格 |
招标导航更多>>
工程建筑
交通运输
环保绿化
医疗卫生
仪器仪表
水利水电
能源化工
弱电安防
办公文教
通讯电子
机械设备
农林牧渔
市政基建
政府部门
换一批
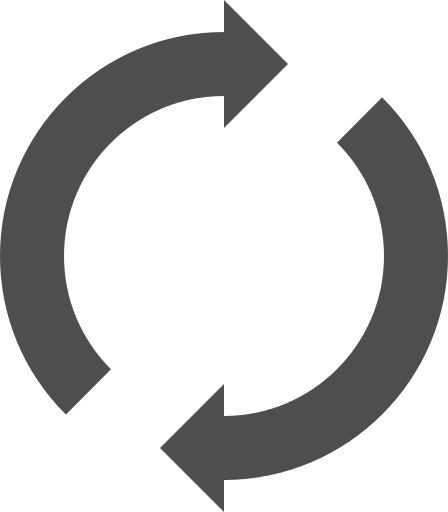