新甾醇项目一期
1、建设项目基本信息
企业基本信息
**** | 建设单位代码类型:|
913********168390M | 建设单位法人:李新发 |
周正华 | 建设单位所在行政区划:**省**市**区 |
****开发区东三路以西,康兴路以南 |
建设项目基本信息
新甾醇项目一期 | 项目代码:|
建设性质: | |
2021版本:024-其他食品制造 | 行业类别(国民经济代码):C1495-C1495-食品及饲料添加剂制造 |
建设地点: | **省**市**区 ****开发区东三路以西,康兴路以南 |
经度:118.01666 纬度: 47.001666 | ****机关:****环境局 |
环评批复时间: | 2020-09-29 |
垦审批环字〔2020〕075号 | 本工程排污许可证编号:**** |
2017-12-27 | 项目实际总投资(万元):20000 |
160 | 运营单位名称:**** |
913********168390M | 验收监测(调查)报告编制机构名称:**** |
913********168390M | 验收监测单位:******公司 |
****0502MA3EMBNCXA | 竣工时间:2024-08-13 |
2024-08-13 | 调试结束时间:2024-11-13 |
2024-09-29 | 验收报告公开结束时间:2024-10-31 |
验收报告公开载体: | http://xinfapharma.com |
2、工程变动信息
项目性质
** | 实际建设情况:** |
无 | 是否属于重大变动:|
规模
维生素E醋酸酯粉(DL-α-生育酚乙酸酯)30000t/a,亚硫酸钠9147.46t/a | 实际建设情况:维生素E醋酸酯粉(DL-α-生育酚乙酸酯)30000t/a,亚硫酸钠9147.46t/a,乙酸钠溶液(25%)10771t/a |
变化,维生素E乙酸酯合成中,使用乙酸酐作为乙酰化试剂,同时副产乙酸。生产中通过加水,生成乙酸溶液后,通过分层与产品分离,进一步蒸馏得到约35—42%乙酸溶液。此处原环评****处理站。 现用30%液碱,将该乙酸溶液中和至中性,得到约25%浓度的乙酸钠溶液。符合《维生素副产乙酸钠溶液》(T/CPCIF 0082—2021)标准后,作为副产品销售,主要用于污水处理。这样污染物排放量减少,更利于环境。 | 是否属于重大变动:|
生产工艺
SM1(去氢芳樟醇)工段:打开炔化釜进料阀,将乙炔和液氨组成的氨乙炔压缩液体通过车间冷凝至28~30℃,压力为2.0~3.0MPa,进入1号醇化釜中,SM和氢氧化钾水溶液(含量47.5%,预先采用氢氧化钾固体和水调配)通过加压泵进入1号醇化釜中,混合30min后,溢流进入2号醇化釜,保温反应2.5h后,溢流到3号醇化釜,保温1h,然后进入缓冲罐,缓冲罐物料通过换热器(冷量回收蒸发器)气化过量氨乙炔后回收冷量,气化的气体通过气液分离器和换热器回气柜;液体进入闪蒸塔,在温度30~60℃,压力为0.1~0.5MPa****回收部分氨乙炔,底部液体进入氨回收塔,在温度50~90℃,常压下继续回收氨乙炔,再次回收完毕氨乙炔的物料进入洗涤塔,在20~30℃,常压下用水洗涤,下层水排出碳酸钾水溶液,油层转料至精馏塔,在110~150℃,压力为-0.093MPa下,精馏除去乙炔、氨和水,得去氢产品。 SM2工段:将去氢芳樟醇通过计量泵转入釜内。通过计量泵将IPM和回收IPM加入釜内,氮气置换三次。升温至110℃,保温2.5h后取样检测,去氢芳樟醇含量少于0.5%,说明反应完全。以冷水为冷媒进行降温,物料降温至20℃后进入刮膜蒸发器,蒸出并回收IPM泵入IPM大槽套用,蒸余液泵入滴加罐中,在0-5℃下滴入重排釜。甲醇、回收甲醇、20%氢氧化钠配成溶液,泵入重排釜中。反应30min后,通过流量计将1%硫酸溶液滴入重排釜中调pH为7-8,中和溶液保温搅拌,泵入SM2反应液高位槽后分层,油层进入产品塔精馏塔,底温110℃下减压精馏,回收IPM泵入IPM大槽套用,回收AC泵入AC大槽,检测合格后套用至IPM工序。产品泵入产品釜,脱重液检测后打回反应釜套用。水相蒸馏,回收甲醇套用至氢氧化钠醇溶液配制工序中,水相去污水站。 SM2氢化反应:通过进料泵将 SM2泵入计量槽,经计量槽泵入高压釜内。密闭压力釜,氮气置换三次,釜内真空度为-0.09MPa,通入氢气至压力2.0MPa。开启搅拌(转速120r/min),升温至120℃反应过程中补加氢气,直至压力不变为止。反应结束后以循环水为冷媒进行降温,温度降为30℃,将剩余气体空排。氢化液上出口出料,通过隔膜泵泵入快速过滤器过滤。滤饼去焚烧,滤液泵入蒸馏釜,釜底温温度130-140℃,釜顶温度100-110℃下减压蒸馏(真空度-0.09MPa),回收氢化SM2产品,釜底残渣为固废。 SC反应:乙炔和液氨组成的混合气体从气柜进入压缩机,从压缩机出来的乙炔和液氨组成的氨乙炔压缩液体再经过三级冷凝,冷凝至28~30℃,压力为2.0~3.0MPa,打开炔化釜进料阀,进入1号醇化釜中,氢化SM2通过计量泵进入管线与氨乙炔混合后进入1号醇化釜中,开启搅拌(转速85r/min),夹套以60℃热水为热源升温至30℃,混合30min后,溢出进2号醇化釜,取样检测,原料含量少于0.5%后进入冷量回收蒸发器。气化的气体通过换热器回气柜回收氨气和乙炔。气化后液****回收部分氨乙炔。底部液体泵入洗涤塔,加入洗涤水洗涤。水相泵入氨回收塔,回收氨气回收后水相进入水相大槽。油相通过刮膜蒸发器蒸水,蒸出水进入水相大槽,釜底液进入精馏塔,温度120-130℃下精馏,馏份通过冷凝器降温回收前馏分,检测后进入洗涤工序。温度130-140℃下精馏,得到产品,釜底残渣收集检测后进入洗涤工序。 SM3氢化反应:通过进料泵将SM3泵入计量槽,经计量槽泵入高压釜内。密闭压力釜,置换氮气三次,釜内真空度为-0.09MPa,通入氢气至压力2.0MPa。开启搅拌,升温至120℃,反应过程中补加氢气,直至压力不变为止。反应结束后以循环水为冷媒进行降温,温度降为30℃,将剩余气体空排。氢化液上出口出料,通过隔膜泵泵入快速过滤器过滤,滤饼去焚烧炉。滤液泵入蒸馏釜,釜底温度130-140℃,釜顶温度110-120℃下减压蒸馏(真空度-0.09MPa),回收氢化SM3产品,釜底残渣作为固废处理。 IP反应:乙炔和液氨组成的混合气体从气柜进入压缩机,从压缩机出来的乙炔和液氨组成的氨乙炔压缩液体再经过过三级冷凝,冷凝至28~30℃,压力为2.0~3.0MPa,打开炔化釜进料阀,进入1号醇化釜中,氢化SM3通过计量泵进入管线与氨乙炔混合后进入1号醇化釜中,夹套以60℃热水为热源升温至30℃,混合30min后,溢出进2号醇化釜,取样检测,原料含量少于0.5%后进入冷量回收蒸发器。气体通过换热器回气柜回收氨气和乙炔。液****回收部分氨乙炔,底部液体泵入洗涤塔,从水相大槽加入套用洗涤水洗涤。水相进入氨回收塔,回收氨气,回收后水相进入水相大槽。油相泵入刮膜蒸发器蒸水,蒸出水进入水相大槽。釜底液进入产品蒸馏塔。前馏分打回洗涤釜,产品进入产品储罐,釜底残渣去焚烧炉。 CZ反应:通过进料泵将IP泵入IP计量槽,通过计量槽泵入高压釜内。将乙醇泵入高压釜,密闭高压釜,置换氮气三次,釜内真空度为-0.09MPa,通入氢气至压力2.0MPa。开启搅拌,升温至120℃,反应约8h,反应过程中补加氢气,直至压力不变为止。反应结束后以15℃~20℃循环水为冷媒进行降温至30℃,将剩余气体空排。氢化液通过隔膜泵泵入快速过滤器过滤,滤饼去焚烧炉,滤液泵入精馏塔,塔底温度150℃,塔顶温度130℃下减压精馏(真空度-0.09MPa),回收CZ产品,釜底料打回过滤器重新过滤,回收乙醇套用。 磺化工艺:开启搅拌,从对二甲苯储罐泵入对二甲苯至反应釜中,在30-35℃温度下自浓硫酸暂存罐通过转料泵泵入硫酸,加完硫酸后将混合液缓慢升温至120℃左右,保温2小时。反应液进入蒸馏釜,蒸汽通过管道到冷凝器冷凝回流至合成分水器,去污水站。真空-0.8MPa下蒸出合格产品,通过中转泵转入中转罐,釜底残渣为固废。 中和工艺:从碱液储罐中通过转料泵向中和釜内加入液碱,加入液碱的同时从磺化液中转罐中通过计量转料泵向中和釜缓慢加入二甲基苯磺酸,搅拌下蒸去水分,水分进入储水罐,套用至碱熔工序。合格后的物料直接通过放料口直接放入碱熔反应釜。 酸化工艺:离心母液通过进料泵转入酸化合成釜中。在50~80℃温度下通入二氧化硫进行反应,调至PH=6后分层。水相进入蒸馏釜,蒸馏后进入套用水罐,釜底盐溶液进入制盐工序。有机相通过转料泵转入酸化产品罐中,再经转料泵转入精馏塔。前馏分打回酸化合成釜,产品对二甲基苯酚转入储罐,釜底残渣去焚烧炉。 氢化工艺:反应釜氮气置换。向反应釜中加入甲醇、催化剂、三甲基苯醌。通入氢气,控制压力0.2MPa。升温至55℃保温反应。持续通入氢气,维持压力0.2-0.3Mpa。反应结束后,降温至室温,氮气置换。压滤,滤饼套用。滤液进入暂存罐。进入单效蒸发器(多效)进行浓缩,回收甲醇去储罐套用。浓缩液进入浓缩液暂存罐。浓缩液喷雾干燥。得产品。 缩合工段:来自罐区的溶剂、盐酸通过计量罐投入缩合反应釜中,通过投料仓将HQ、CAT投入缩合反应釜中,氮气保护下,升温至40~50℃,保温30min后开通过计量罐滴加CZ,滴毕,40~50℃保温3小时。上述反应液转至洗涤釜,用纯化水洗涤2次,静置分掉水层,二次洗水套用至一次洗涤。一次洗涤水转至催化剂脱色釜,加入活性炭脱色,脱色温度40~50℃,脱色时间30min,保温完毕后,进行压滤,压滤出的废活性炭送焚烧炉焚烧,滤液转至蒸馏釜减压蒸干回收CAT进行套用;蒸馏出水进蒸出水罐,用片碱中和后,送蒸发器进行蒸馏回收水套用。洗涤后油层减压精馏,蒸馏温度60~100℃,真空度0.09Mpa,回收溶剂,回收的溶剂进行套用;蒸余物料转至酯化釜。 酯化工段:向酯化釜中投入锌粉,通过计量罐向酯化釜中投入乙酸酐、生育酚粗品,氮气保护下,升温至115~135℃,保温3~4h。反应完毕后,物料通过离心泵转至醋酐回收釜,减压蒸馏回收乙酸,蒸馏温度不超过145℃,真空度-0.09MPa,蒸馏完毕后进入稀释釜,通过计量罐加入溶剂油,搅拌后进入过滤器,过滤出醋酸锌,滤液转至洗涤工序。滤液用纯化水洗涤一次,洗涤时间15min,静置分掉水层;加入60%甲醇洗涤一次,洗涤15min,静置分掉水层;再用纯化水洗涤一次,洗涤15min,静置分掉水层;洗涤温度25~35℃。酯化一次洗涤水送蒸发器进行蒸馏回收水和醋酸锌,回收水套用至一次酯化洗涤工段,酯化二次、三次洗涤水送甲醇精馏装置进行精馏回收水套用至三次洗涤水中,回收甲醇水套用至60%甲醇水配制中,废液去污水站处理。油层减压回收溶剂油套用至稀释釜中,控制温度135℃,得生育酚乙酸酯粗品。 制盐工序:将回收粗品盐溶于反应釜中,在温度为33.4℃搅拌溶解,过滤,去掉滤饼,为固废。滤液进入醇洗釜中,缓慢加入乙醇,使亚硫酸钠重结晶,结晶物为副产物亚硫酸钠。乙醇水蒸馏回收乙醇和水套用。 | 实际建设情况:SM1(去氢芳樟醇)工段:打开炔化釜进料阀,将乙炔和液氨组成的氨乙炔压缩液体通过车间冷凝至28~30℃,压力为2.0~3.0MPa,进入1号醇化釜中,SM和氢氧化钾水溶液(含量47.5%,预先采用氢氧化钾固体和水调配)通过加压泵进入1号醇化釜中,混合30min后,溢流进入2号及3号醇化釜,再次保温约1h,然后进入缓冲罐,缓冲罐至冷量闪蒸管线上加热水把催化剂浓度进行稀释。缓冲罐物料通过换热器(冷量回收蒸发器)气化过量氨乙炔后回收冷量,气化的气体通过气液分离器和换热器回气柜;液体进入闪蒸塔,在温度50-70℃,压力为3-5kpa****回收部分氨乙炔,回收完毕氨乙炔的物料经分水器分出水层和油层,油层进入洗涤塔,在60-80℃常压下用蒸汽冷凝水洗涤,下层排出稀碱水溶液,油层转料至精馏塔,在110~150℃,压力为-0.093MPa下,精馏脱轻除去SM(甲基庚烯酮),产品塔得去氢产品。 SM2工段:将去氢芳樟醇通过计量罐转入釜内。通过计量泵将新IPM和回收IPM加入釜内,氮气置换三次。关闭所有阀门,升温至95-105℃,然后开始泵加催化剂,泵加2.5h,维持反应温度在105-115℃之间,然后取样检测,去氢芳樟醇含量少于0.5%,说明反应完全。以循环水为冷媒进行降温,物料降温至60℃以下后进入反应液大罐,然后将反应液转至降膜蒸发器,蒸出并回收IPM泵入IPM大槽套用,蒸余液转至刮膜蒸发器,在70-90℃,真空-80—90kpa条件下回收DMK,回收的DMK一部分去配制催化剂,剩余部分打至IPM车间裂解制备IPM,脱完DMK后SM2粗品泵至加氢车间或者在甲醇催化剂中异构化后酸中和得到假性紫罗兰酮供其他项目使用。 SM2氢化反应:通过进料泵将 SM2泵入计量槽,经计量槽泵入高压釜内。首次加氢反应一并将加氢催化剂加入到反应釜中,密闭压力釜,氮气置换三次,氢气置换三次,将釜中氧含量置换到0.5%以下,通入氢气至压力1.5-2.0MPa。开启搅拌,将搅拌开到最大,先升温至70℃进行加氢反应,在70℃下加氢反应不动时,再将釜温升温至110-120℃反应过程中补加氢气,直至压力不变为止,此时取样测样,当SM2加氢中间体残留1%以下时视为反应合格,反应结束后以循环水为冷媒进行降温,温度降为30℃,将剩余气体空排。氢化液上出口出料,通过隔膜泵泵入快速过滤器过滤。滤液泵入SM2脱轻、成品塔进行提纯,脱轻塔釜温度120-140℃,成品塔釜底温温度130-140℃,脱轻塔顶温度100-110℃,成品塔塔顶温度120-130℃蒸出LJZ产品(真空1-2kpa),釜底残渣为固废。 SC反应:乙炔和液氨组成的混合气体从气柜进入压缩机,从压缩机出来的乙炔和液氨组成的氨乙炔压缩液体再经过三级冷凝,冷凝至28~30℃,压力为2.0~3.0MPa,打开炔化釜进料阀,进入1号醇化釜中,醇化釜中充满氨乙炔后开启搅拌(转速85r/min),将提前配制好的1#cat用计量泵泵至1号醇化釜,泵加cat一小时后再将氢化SM2通过计量泵进入1号醇化釜,混合30min后,然后依次溢出进2号醇化釜、3号醇化釜,取样检测,原料含量少于5%后进入冷量回收蒸发器。气化的气体通过换热器回气柜回收氨气和乙炔。剩余液****回收部分氨乙炔。从闪蒸塔出来的反应液经分水器进行连续分层,上层油相汇集到油相大罐中,然后通过泵将油相泵入洗涤塔,加入洗涤水洗涤。水相泵入氨回收塔,回收氨气回收后水相进入水相大槽。油相通过刮膜蒸发器蒸水,蒸出水进入水相大槽,刮膜脱水液进入精馏塔,温度120-130℃下精馏分别进行脱轻、脱重,脱轻塔中馏份通过冷凝器降温回收前馏分,检测后再回套至原料进行炔化反应。脱轻塔釜液泵至成品塔温度130-160℃下精馏,得到产品SC,釜底残渣收集检测后进入洗涤工序。 SM3氢化反应:通过进料泵将SM3泵入高压釜内。首次投料将加氢催化剂一并投入到反应釜中,密闭压力釜,置换氮气三次,氢气置换三次,检测釜中氧含量在0.5%以下视为置换合格,通入氢气至压力1.5-2.0MPa。开启搅拌,先将反应温度升至70℃进行加氢反应,当加氢流量不再变化,釜中压力不再下降时,将反应温度升温至110-120℃,反应过程中补加氢气,直至压力不变为止。反应结束后以循环水为冷媒进行降温,温度降为60℃以下出料,将剩余气体空排。氢化液上出口出料,通过隔膜泵泵入快速过滤器过滤,过滤后的催化剂通过氮气正吹反吹,再通过原料液及加氢液反冲至反应釜中套用。滤液泵入脱轻塔及成品塔提纯,脱轻塔釜底温度140-160℃,釜顶温度120-140℃下减压蒸馏回收轻组分,脱轻塔釜料转移至成品塔,控制成品塔釜温度150-170℃,塔顶温度130-150℃,压力1kpa以下(绝压),精馏出氢化SM3(FAT)产品,釜底残渣作为固废处理。 IP反应:乙炔和液氨组成的混合气体从气柜进入压缩机,从压缩机出来的乙炔和液氨组成的氨乙炔压缩气体再经过过三级冷凝,冷凝至28~30℃,压力为2.0~3.0MPa,打开炔化釜进料阀,进入1号醇化釜中,开启醇化釜搅拌,氨乙炔加压液化循环一段时间后,通过计量泵开始泵入1#cat,泵加1h后开始将氢化SM3通过计量泵进入1号醇化釜中,在釜中停留时间约30min后,反应液依次溢出进2号,3号醇化釜,从缓冲罐后闪蒸管处取样检测(样品要用热水洗涤至中性送检),原料含量少于5%后进入冷量回收蒸发器。气体通过换热器回气柜回收氨气和乙炔。液****回收部分氨乙炔,闪蒸毕的反应液通过分水器分出上层油相,将油相通过转料泵泵入洗涤塔,用蒸汽冷凝水大罐的热水进行洗涤。水相进入氨回收塔,回收氨气,回收后水相进入水相大槽。油相泵入刮膜蒸发器蒸水,蒸出水进入水相大槽。刮膜底液用乙醇稀释后去做加氢反应制备CZ。 CZ反应:通过进料泵将IP泵入IP计量槽,通过计量槽泵入高压釜内,首次投料将加氢催化剂一并投入到加氢釜中。将乙醇泵入高压釜,密闭高压釜,置换氮气三次,氢气置换三次,将釜中氧含量置换至0.5%以下,通入氢气至压力1.5-2.0MPa。开启搅拌,升温至70-90℃,反应约8h,反应过程中补加氢气,直至压力不变为止。取样检测IP含量降至0.5%以下视为反合格,反应结束后以循环水为冷媒进行降温至50℃以下,将剩余气体空排。静置一段时间后氢化液通过隔膜泵泵入快速过滤器过滤,滤饼通过氮气反吹、正吹,加氢液正洗、反洗将带出的催化剂再次返回到加氢反应釜中,滤液泵入精馏塔,塔底温度150-180℃,塔顶温度130-150℃下减压精馏(真空度500pa以下,绝压),回收CZ产品,釜底料打回过滤器重新过滤,回收乙醇套用。 磺化工艺:开启搅拌,从对二甲苯储罐泵入对二甲苯至反应釜中,在30-35℃温度下自浓硫酸暂存罐通过转料泵泵入硫酸,加完硫酸后将混合液缓慢升温至120℃左右,保温2小时。蒸汽通过管道到冷凝器冷凝回流至合成分水器,去污水站。真空-0.8MPa下蒸出溶剂对二甲苯,套用至下一批次,釜底为产品,通过中转泵转入中转罐。 中和工艺:从碱液储罐中通过转料泵向中和釜内加入液碱,加入液碱的同时从磺化液中转罐中通过计量转料泵向中和釜缓慢加入二甲基苯磺酸,搅拌下蒸去水分,水分进入储水罐,打至污水站处理。合格后的物料直接通过放料口直接放入碱熔反应釜。 酸化工艺:离心母液通过进料泵转入酸化合成釜中。在50~80℃温度下通入二氧化硫进行反应,调至PH=6后分层。水相进入水相暂存罐,套用至碱熔工序。有机相通过转料泵转入酸化产品罐中,再经转料泵转入精馏塔。前馏分打回酸化合成釜,产品对二甲基苯酚转入储罐,釜底残渣去焚烧炉。 氢化工艺:反应釜氮气置换。向反应釜中加入甲醇、催化剂、三甲基苯醌。通入氢气,控制压力0.2MPa。升温至55℃保温反应。持续通入氢气,维持压力0.2-0.3Mpa。反应结束后,降温至室温,氮气置换。压滤,滤饼套用。滤液进入暂存罐。 缩合工段:将来自氢化工序的甲醇、三甲基氢醌转入蒸馏釜中,升温至65℃,开始蒸馏甲醇,冷凝器有凝液流出到蒸馏釜分层罐中,持续升温蒸馏,蒸馏过程中向蒸馏釜中转入YQ。继续升温蒸馏,此时冷凝液为YQ甲醇混合液,混合液进入分层罐中,甲醇在下层自动流至甲醇罐套用至氢化工序,YQ在上层,随着液位上升,回流至蒸馏釜中。待釜内温度开始上升,且分层罐中液位无明显变化时,则蒸馏结束。 开启蒸馏釜底阀,开启缩合釜HQ进料阀门,将HQ放入下方蒸馏釜中。向缩合釜中加入EN、氯化锌。开始升温,待温度升高至80℃时,开启盐酸、CZ转料泵,开始向釜内滴加盐酸、CZ。滴加过程维持1小时,滴加过程中维持釜内温度90℃。反应过程中YQ和水蒸出,冷凝后流至缩合釜分层罐中,在分层罐中分层,水在下层,分出至缩合分层水相中转罐,用泵转至界外废水罐;YQ在上层,随着液位上升回流至缩合釜中。滴加结束后保温蒸水5小时,保温结束后将物料转入缩合物料中转罐暂存。 酯化工段:将缩合物料中转罐内温度降温至60℃,开启打料泵,将物料转入酯化混合器中,同时开启醋酐转料泵,将醋酐转入酯化混合器中,使两种物料相互混合反应后流入酯化接收釜。将反应完全的酯化液转入过滤釜中,持续搅拌物料进行过滤后转至酯化过滤液分层罐。分层罐中液体分层,下层水相放入酯化脱色水相接收罐,后续进入XK18工序回收XK18催化剂和醋酸;上层有机相进入轻相缓冲罐中。进入洗涤混合器水洗后继续分层,水相套用至活性炭配制,有机相转入萃取塔再次水洗后进入油相暂存罐暂存,水相用作洗涤混合器用水。油相减压蒸馏回收溶剂,得到粗品生育酚乙酸酯粗品。生育酚乙酸酯粗品进入精馏塔精馏得到VE乙酸酯,重组分进入薄膜蒸发器,进入短程蒸发器,经短程蒸发器后得到生育酚乙酸酯。维生素副产乙酸钠溶液回收,将醋酸水溶液加入中和釜中,加入液碱混合得乙酸钠溶液 制盐工序:将回收粗品盐溶于反应釜中,在温度为33.4℃搅拌溶解,过滤,去掉滤饼,为固废。滤液进入接收罐中,再进入浓缩设备进行蒸馏,蒸馏水套用,高温过滤得到无水亚硫酸钠重结晶,结晶物为副产物无水亚硫酸钠。蒸馏水套用。 |
根据生产部门提供的资料,在本工段的生产过程中,根据现场实际情况优化调整,通过工艺分析,未新增污染物种类,最终核算污染物排放量未增加 | 是否属于重大变动:|
环保设施或环保措施
废气(1)甲醇制氢装置废气为脱碳过程产生废气G1-1,主要成份为二氧化碳、二甲醚、甲烷、甲醇等,引至锅炉焚烧处置。(2)电石库有组织废气颗粒物依托新柠项目废气处理设施;(3)侧链(异植物醇)生产废气:氢气废气经水喷淋处理后经25m排气筒p1排放,有机废气依托新柠项目废气处理装置处理后引至焚烧炉焚烧处置;(4)主环生产废气:氢气经风机引入7#二级碱喷淋碱洗塔吸收处理,25m高排气筒P2排放,有机废气引至二级喷淋水洗塔处理后引至锅炉焚烧处置;(5)合成工段产生废气:含HCl有机废气通过深冷+碱喷淋+除雾器+活性炭吸附处理后经25m排气筒P3排放,含氢有机废气经风机引入8#二级水喷淋水洗塔吸收处理,25m排气筒P4高空排放。有机废气经冷凝+二级喷淋水洗塔吸收处理后引至锅炉焚烧处置,混料含尘废气经布袋除尘器处理后经25m排气筒P5排放。 固体废物:压滤机滤饼(S2-2)回用于酸洗水中和工段;侧链(异植物醇):IPM工段(S3-1)、氢化509(S5-1、S5-2)、SM工段(S6-1)SM1工段(S7-1)、SM2工段(S8-1)、SM2氢化工段(S9-1、S9-2)、SC工段(S10-1)、SM3工段(S11-1)、SM3氢化工段(S12-1)、IP工段(S13-1)、SZ工段(S14-1);主环生产:磺化工段(S15-1)、酸化工段(S18-1、S18-2)、甲基化工段(S19-1)、氧化工段(S20-1)、氢化工段(S21-1)、合成(S22-1、S22-1-1)等危险废物暂存于厂区现有危废间,其中废催化剂回收再生,其他送至新厂区固废焚烧炉焚烧处理。 | 实际建设情况:废气(1)甲醇制氢装置废气为脱碳过程产生废气:引至RTO装置焚烧(2)电石库有组织废气:经集气罩收集、布袋除尘器处理后,最终通过1根28m高的排气筒排放(3)侧链(异植物醇)生产废气:氢气经冷凝器冷却回收后直排;其他废气、有机废气经膜吸收、水喷淋、冷凝回收等处理后,最终引至RTO装置焚烧(4)主环生产废气:氢气经冷凝器冷却回收后直排,废气、有机废气经水喷淋、冷凝回收等处理后,最终引至RTO装置焚烧,主环甲基化气化废气经PSA吸附后尾气引入熔盐炉焚烧(5)合成工段产生废气:经风机引入一套冷凝+二级喷淋碱洗塔吸收处理,引至RTO装置焚烧;注:混料含尘废气已在喷粉工序已验收完成,本次不在验收范围。 固体废物:压滤机滤饼(S2-2)部分回用于酸洗水中和工段,部分当作建材用于厂区建设,其余外售侧链(异植物醇):IPM工段(S3-1)、SM工段(S6-1)SM1工段(S7-1)、SM2氢化工段(S9-1)、SC工段(S10-1)、SM3氢化工段(S12-1)、SZ工段(S14-1);主环生产:磺化工段(S15-1)、甲基化工段(S19-1)、氧化工段(S20-1)、氢化工段(S21-1)、合成(S22-1),S1废机油、S2废机油桶、S3废导热油、S4化验室固废等危险废物暂存于厂区现有危废间,其中S1废机油、S2废机油桶、S3废导热油、S4化验室固废、废催化剂委托有资质单位处理,其他送至新厂区固废焚烧炉焚烧处理。 |
环评中提及的(1)电石库有组织废气颗粒物依托新柠项目废气处理设施变为经集气罩收集、布袋除尘器处理后,最终通过1根28m高的排气筒排放,不再依托新柠项目废气处理设施,但**的废气处理设施未变化; 环评中提及的(2)侧链(异植物醇)生产废气:氢气废气经水喷淋处理后经25m排气筒p1排放,有机废气依托新柠项目废气处理装置处理后引至焚烧炉焚烧处置变为氢气经冷凝器冷却回收后直排;其他废气、有机废气经膜吸收、水喷淋、冷凝回收等处理后,最终引至RTO装置焚烧;因氢气不属于污染物,现场出于对安全因素考虑,氢气经冷凝器冷却回收后直排;不再依托新柠项目废气处理设施,但**的有机废气处理设施不会影响处理效果的弱化或降低; 环评中提及的(3)主环生产废气:氢气经风机引入7#二级碱喷淋碱洗塔吸收处理,25m高排气筒P2排放,有机废气引至二级喷淋水洗塔处理后引至锅炉焚烧处置变为氢气经冷凝器冷却回收后直排,氢气经冷凝器冷却回收后直排,其他废气、有机废气经水喷淋、冷凝回收等处理后,最终引至RTO装置焚烧,主环甲基化气化废气经PSA吸附后尾气引入熔盐炉焚烧;因氢气不属于污染物,现场出于对安全因素考虑,氢气经冷凝器冷却回收后直排;有机废气废气处理方式发生变化(经水喷淋、冷凝回收等处理后,最终引至RTO装置焚烧)属于污染防治措施强化或改进,这样处理效率更高,外排废气含量降低,使废气排放浓度降低,更利于环境。 环评中提及的(4)合成工段产生废气:含HCl有机废气通过深冷+碱喷淋+除雾器+活性炭吸附处理后经25m排气筒P3排放,含氢有机废气经风机引入8#二级水喷淋水洗塔吸收处理,25m排气筒P4高空排放。有机废气经冷凝+二级喷淋水洗塔吸收处理后引至锅炉焚烧处置变为经风机引入一套冷凝+二级喷淋碱洗塔吸收处理,引至RTO装置焚烧,属于污染防治措施强化或改进,这样处理效率更高,外排废气含量降低,使废气排放浓度降低,更利于环境。环评中提及的压滤机滤饼(S2-2)部分回用于酸洗水中和工段,部分当作建材用于厂区建设,其余外售。环评中提及的废催化剂回收再生变为剂委托有资质单位处理,危废环评预测量5635.2825t/a,验收阶段核算量:3216.06t/a。符合《关于进一步加强建设项目固体废物环境管理的通知》(鲁环办函[2016]141号)要求。 | 是否属于重大变动:|
其他
无 | 实际建设情况:无 |
无 | 是否属于重大变动:|
3、污染物排放量
0 | 0 | 0 | 0 | 0 | 0 | 0 | |
0 | 15.27 | 119.606 | 0 | 0 | 15.27 | 15.27 | |
0 | 0.76 | 11.961 | 0 | 0 | 0.76 | 0.76 | |
0 | 0 | 0 | 0 | 0 | 0 | 0 | |
0 | 5.73 | 27.908 | 0 | 0 | 5.73 | 5.73 | |
0 | 0 | 0 | 0 | 0 | 0 | 0 | / |
0 | 0 | 35.77 | 0 | 0 | 0 | 0 | / |
0 | 0 | 110.068 | 0 | 0 | 0 | 0 | / |
0 | 0.108 | 6.824 | 0 | 0 | 0.108 | 0.108 | / |
0 | 11.52 | 93.588 | 0 | 0 | 11.52 | 11.52 | / |
4、环境保护设施落实情况
表1 水污染治理设施
1 | ****处理站 | 《污水综合排放标准》(GB8978-1996)三级等级标准①****开发区污水处理厂进水水质要求② | ****处理站 | 手工及在线监测 |
表2 大气污染治理设施
1 | RTO装置焚烧(依托)、膜吸收、喷淋设施、冷凝回收 | **省《挥发性有机物排放标准 第7部分:其他行业(DB37/ 2801.7-2019)《大气污染物综合排放标准》(GB16297-1996),**省《区域性大气污染物综合排放标准》(DB37/2376-2019),《恶臭污染物排放标准》(GB 14554-1993表2排放限值(27 kg/h)。 | 各工段先经过(膜吸收、喷淋设施、冷凝回收)等预处理后进入RTO装置焚烧 | 手工及在线监测 | |
2 | 脉冲式布袋除尘器 | **省《区域性大气污染物综合排放标准》(DB37/2376-2019) | 经集气罩收集、脉冲式布袋除尘器处理后,最终通过1根28m高的排气筒排放。 | 手工监测 |
表3 噪声治理设施
1 | 隔声、减振措施 | 《工业企业厂界环境噪声排放标准》(GB12348-2008) | 本项目选用低噪声设备,安装减震垫,经厂房的屏蔽以及距离衰减等措施 | 手工监测 |
表4 地下水污染治理设施
表5 固废治理设施
表6 生态保护设施
表7 风险设施
5、环境保护对策措施落实情况
依托工程
****处理站、锅炉焚烧装置、部分配套公用设施 | 验收阶段落实情况:****处理站、RTO焚烧装置、部分配套公用设施 |
/ |
环保搬迁
无 | 验收阶段落实情况:无 |
/ |
区域削减
无 | 验收阶段落实情况:无 |
/ |
生态恢复、补偿或管理
无 | 验收阶段落实情况:无 |
/ |
功能置换
无 | 验收阶段落实情况:无 |
/ |
其他
无 | 验收阶段落实情况:无 |
/ |
6、工程建设对项目周边环境的影响
/ |
/ |
/ |
/ |
/ |
/ |
7、验收结论
1 | 未按环境影响报告书(表)及其审批部门审批决定要求建设或落实环境保护设施,或者环境保护设施未能与主体工程同时投产使用 |
2 | 污染物排放不符合国家和地方相关标准、环境影响报告书(表)及其审批部门审批决定或者主要污染物总量指标控制要求 |
3 | 环境影响报告书(表)经批准后,该建设项目的性质、规模、地点、采用的生产工艺或者防治污染、防止生态破坏的措施发生重大变动,建设单位未重新报批环境影响报告书(表)或环境影响报告书(表)未经批准 |
4 | 建设过程中造成重大环境污染未治理完成,或者造成重大生态破坏未恢复 |
5 | 纳入排污许可管理的建设项目,无证排污或不按证排污 |
6 | 分期建设、分期投入生产或者使用的建设项目,其环境保护设施防治环境污染和生态破坏的能力不能满足主体工程需要 |
7 | 建设单位因该建设项目违反国家和地方环境保护法律法规受到处罚,被责令改正,尚未改正完成 |
8 | 验收报告的基础资料数据明显不实,内容存在重大缺项、遗漏,或者验收结论不明确、不合理 |
9 | 其他环境保护法律法规规章等规定不得通过环境保护验收 |
不存在上述情况 | |
验收结论 | 合格 |
招标导航更多>>
工程建筑
交通运输
环保绿化
医疗卫生
仪器仪表
水利水电
能源化工
弱电安防
办公文教
通讯电子
机械设备
农林牧渔
市政基建
政府部门
换一批
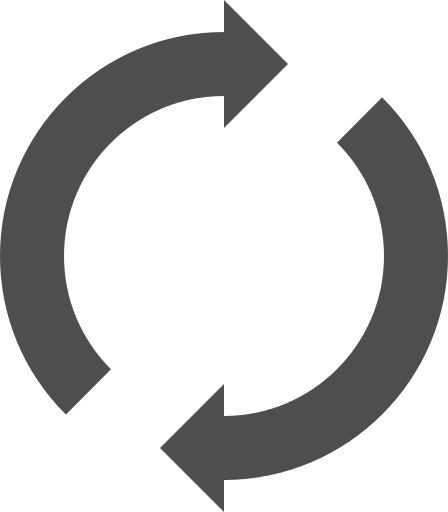