内蒙古鑫华半导体科技有限公司10000吨/年高纯电子级多晶硅产业集群项目(一期)
1、建设项目基本信息
企业基本信息
**** | 建设单位代码类型:|
****0105MABMQKDB6L | 建设单位法人:田新 |
牛克选 | 建设单位所在行政区划:**自治区**市**区 |
**自治区**市**区阿木尔南街19号 |
建设项目基本信息
****10000吨/年高纯电子级多晶硅产业集群项目(一期) | 项目代码:|
建设性质: | |
2021版本:081-电子元件及电子专用材料制造 | 行业类别(国民经济代码):C3985-C3985-电子专用材料制造 |
建设地点: | **自治区**市**区 **自治区**市**区阿木尔南街19号 |
经度:111.75285 纬度: 40.71634 | ****机关:****环境局 |
环评批复时间: | 2022-08-09 |
呼环政批字〔2022〕175号 | 本工程排污许可证编号:**** |
2024-01-18 | 项目实际总投资(万元):283000 |
11347 | 运营单位名称:**** |
****0105MABMQKDB6L | 验收监测(调查)报告编制机构名称:内****公司 |
****0105MA13NHUK88 | 验收监测单位:**华成****公司 |
****0114MA01T65C26 | 竣工时间:2024-05-30 |
调试结束时间: | |
2024-10-17 | 验收报告公开结束时间:2024-11-14 |
验收报告公开载体: | https://www.js-eia.cn/project/detail?type=6 proid=fd****484c92dbddd80b7ed03a3a0728 |
2、工程变动信息
项目性质
** | 实际建设情况:** |
\ | 是否属于重大变动:|
规模
本工程主要产品为电子级多晶硅(10000t/a),副产电子级二氯二氢硅(500t/a)、电子级三氯氢硅(3000t/a)、电子级四氯化硅(3000t/a) | 实际建设情况:年产电子级高纯多晶硅10000吨。 |
本项目为一期工程。电子级二氯二氢硅(特气)500吨、电子级三氯氢硅(特气)3000吨、电子级四氯化硅3000吨等留作二期建设。 | 是否属于重大变动:|
生产工艺
1、氢气制备 (1)电解制氢 脱盐水用加水泵送入原料水箱,经补水泵加入碱液系统。碱液系统将气液处理器与水碱箱连接在一起,配制碱液时,启动循环泵,使碱箱中的去离子水形成循环,再由水碱箱的投料口加入固态氢氧化钾,配制成30%的氢氧化钾溶液。 系统需要补碱时,由经加水泵将配制好的电解液注入碱液过滤器除去机械杂质,再用循环泵打入电解槽,形成闭环系统。电解槽为压滤式双极性串联结构,电解液在电解槽内直流电的作用下分解,在电极表面析出氢气与氧气,经各自通道分别进入气液系统。以脱盐水为基准,电解反应转化率为67.7%。 电解槽产出氢气和碱液混合物一起通过极框上阴极侧的出气孔流过氢气道,从中间负极框流出,汇集后送入气液分离器。分离出氢气导入氢气洗涤冷却器进一步洗涤,并利用循环冷却水间接冷却,然后再进入气水分离器,最终经氢气薄膜调节阀排出,装入储罐备用。 (2)氢气纯化 来自氢气储罐的氢气首先进入气水分离器滤除游离水,经排水阀定期自动排出,除游离水后的氢气送入脱氧器。脱氧器内装有常温即可催化反应进行的高效催化剂,氧和氢经催化剂作用生成水,氧气被去除。 催化反应产生的水被氢气带出脱氧器,进入冷却器后利用循环冷却水间接冷却,不凝气随氢气进入气水分离器,分离出游离水经排水阀定期自动排出,分离出氢气送入干燥器。残留水蒸气在干燥器内被分子筛吸附,高纯度氢气再经过滤器滤尘后流出纯化系统,经氢气压缩机压缩通过管道送氯氢化反应系统和还原系统使用。 2、氯化氢制备 (1)盐酸解析 将浓度31%盐酸打入预热器中,利用间接蒸汽预热至60℃,再与浓度40%的氯化钙溶液混合,然后送入解析塔上部。盐酸和氯化钙混合溶液靠重力沿填料表面下降,与来自再沸器的含氯化氢、水蒸气混和气体在解析塔内进行连续逆流接触传质、传热,从而使上升混合气体中氯化氢含量不断增加,在塔顶得到含饱和水的HCl气体,由管道送入氯化氢脱水系统。塔釜产生的恒沸酸与氯化钙的混合液进入再沸器,利用间接蒸汽加热至120℃,产生含氯化氢、水蒸气混和气体进入解析塔内继续进行传质、传热。塔釜最终产生的稀氯化钙溶液去蒸发器,利用间接蒸汽蒸发提浓后回用。盐酸解析过程加入浓度40%的氯化钙溶液作为共沸助剂,解析效率可达99.5%。 (2)氯化氢脱水 含饱和水的氯化氢气体首先进入一级冷凝器,用循环冷却水间接冷却至40℃左右,去除其中大部分的水蒸气。含氯化氢的一次冷凝液回流至解析塔顶部,一级冷凝后的氯化氢气体再进入二级冷凝器,用乙二醇为冷媒,间接冷冻脱水除去残留的水蒸气。含氯化氢的二次冷凝液回流至解析塔顶部,二级冷凝后的氯化氢气体先经除雾器去除夹带的细小水雾,再由浓硫酸干燥塔干燥,得到干燥的氯化氢,再经氯化氢压缩机压缩至0.2MPa,送至氯氢化反应器。塔内硫酸浓度经检测达到80%后,即为废硫酸,由干燥塔塔底排出。 3、硅粉备料 原料硅粉采用人工破袋,放料至仓泵,利用氮气气力输送至高压进料罐中,在高压进料罐利用间接蒸汽进行预热至120℃,再经重力流入低压进料罐,在回流氢气保护氛围下向氯氢化反应器内送料。 4、冷氢化 (1)氯氢化 预热后的硅粉在低压进料罐与催化剂氯化铜混合,再用氢气从氯氢化反应器顶部送入,解析、干燥后的氯化氢由密闭管道从氯氢化反应器底部进入,三氯氢硅精馏提纯产生的四氯化硅与电解制得的氢气在氢气压缩机出口处混合,通过密闭管道送入氯氢化反应器。原料升温采用梯级加热,145℃以下时回收系统余热并采用蒸汽间接加热,545℃以下时回收系统余热并采用电加热。氯氢化反应器内硅粉、氢气、氯化氢、四氯化硅在温度为535℃并存有催化剂条件下发生氯氢化反应,反应时间45s。氯氢化反应过程,氯化氢和硅粉投加摩尔比为3∶1,氯化氢过量加入,以硅粉为基准,氯氢化反应转化率为91.3%。 反应完成的混合气体夹带少量硅粉自反应器顶部流出,经旋风分离器和过滤器除尘后,由洗涤塔塔釜部通入,与冷凝回流的三氯氢硅液体逆流接触,进一步去除粉尘。洗涤塔顶混合气体依次经空冷、乙二醇制冷、氟利昂制冷三级冷凝器冷凝,冷凝下三氯氢硅混合料液送入合成产品罐,未被冷凝的氢气经换热后进入循环氢压缩机,经压缩后回流进入氯氢化系统中。 (2)粗分 合成产品罐中的三氯氢硅混合液经换热后进入粗分塔进行分离,利用二氯二氢硅、三氯氢硅、四氯化硅不同组分的沸点差异,通过间接蒸汽加热精馏。粗分塔塔顶分离出轻组分经冷凝器利用循环冷却水间接冷凝后,得到含量≥98%三氯氢硅送往提纯系统,塔釜重组分四氯化硅经汽化塔汽化后返回氯氢化工序循环使用。 (3)渣浆处理系统 来自冷氢化洗涤塔渣浆和汽化塔渣浆,主要含四氯化硅,少量三氯氢硅、聚氯硅烷、金属氯化物和硅粉。首先将渣浆输送至转鼓过滤器,过滤出硅粉、高沸物等排入水解罐。转鼓清液送至脱轻精馏塔,通过间接蒸汽加热,在70℃、0.15MPa条件下分离轻组分经冷凝后进入粗分塔。重组分进入高沸反应器,通入氯化氢后发生裂解反应。氯氢化反应重组分Si2Cl6和HCl投加摩尔比为1∶1.2,以HCl为基准,反应转化率为65.0%。 高沸反应器出口混合气经冷凝后进入脱高精馏塔,在70℃、0.15MPa条件下分离提纯,塔顶混合气经冷凝后进入粗分塔。塔釜料液返回高沸反应器继续裂解反应,未能被裂解的高沸物排入水解罐。 来自转鼓过滤器的硅粉、高沸物和高沸反应器的高沸物进入水解罐内,加入熟石灰和新水后进行水解。水解反应四氯化硅、三氯氢硅、二氯二氢硅等氯硅烷和熟石灰投加摩尔比均为1∶1.4,熟石灰过量加入,以四氯化硅、三氯氢硅、二氯二氢硅为基准,水解反应转化率均能够达到99 .0%以上,氯化氢回收率为60.0%。 5、三氯氢硅提纯 (1)精馏提纯 粗分后的三氯氢硅首先送入Ⅰ级脱轻塔,利用间接蒸汽加热,塔顶操作压力为0.30MPa,操作温度为60.4℃,塔釜操作压力为0.30MPa,操作温度为74.8℃。大部分低沸点杂质随同二氯二氢硅在塔顶馏出,经冷凝器冷凝后进二氯二氢硅中间罐;所有高沸点杂质则随同三氯氢硅由塔釜排出,并进入Ⅰ级脱高塔。 Ⅰ级脱高塔利用间接蒸汽加热,塔顶操作压力为0.45MPa,操作温度为91.2℃,塔釜操作压力为0.45MPa,操作温度为92.5℃。塔顶馏出三氯氢硅,经冷凝器冷凝后送入Ⅱ级脱轻塔;塔釜排出四氯化硅及高沸点杂质,送二氯二氢硅反应器进行反歧化。 脱高塔所得化学级三氯氢硅经再精制得电子级产品。为此,将脱高塔塔顶三氯氢硅产品再经2个塔,进一步脱除高、低沸物杂质。 Ⅰ级脱高后的三氯氢硅送入Ⅱ级脱轻塔,利用间接蒸汽加热,塔顶操作压力为0.13MPa,操作温度为57.9℃,塔釜操作压力为0.13MPa,操作温度为59.3℃。塔釜排出三氯氢硅后,进入Ⅱ级脱高塔;塔顶蒸出带有全部轻组份杂质及少量三氯氢硅,经冷凝器冷凝后返回Ⅰ级脱轻塔。 Ⅱ级脱高塔利用间接蒸汽加热,塔顶操作压力为0.33MPa,操作温度为81.1℃;塔釜操作压力为0.33MPa,操作温度为82.5℃。塔釜排出高沸点杂质及部分三氯氢硅,返回Ⅰ级脱高塔;塔顶采出馏分经吸附塔吸附除杂,初步去除其中的B、P杂质,经冷凝器冷凝后送络合精馏塔进行络合除杂。 (2)络合精馏 Ⅰ级脱高、吸附除杂后的三氯氢硅送入络合精馏塔,络合剂苯甲醛通过管道补入塔内,与三氯氢硅充分混合,将三氯氢硅中的硼、磷等杂质络合。利用间接蒸汽加热,使塔釜温度控制在60~80℃,塔顶精馏出三氯氢硅经冷凝器冷凝后为电子级三氯硅烷,进入中间产品罐待用。 塔釜高沸物送入苯甲醛分离精馏塔,利用间接蒸汽加热,使塔釜温度控制在180℃,塔顶馏出苯甲醛蒸汽经冷凝器冷凝后返回络合精馏塔。 络合剂苯甲醛与三氯氢硅混合后,苯甲醛占比为5~10%,以较小比例在络合精馏塔和苯甲醛分离精馏塔中循环使用。络合精馏塔采用大回流比、高效新型填料形成的**论板数,且苯甲醛与三氯氢硅沸点本身差异较大,所以能够将苯甲醛和三氯氢硅分离。企业通过ASPEN计算验证,络合精馏塔塔顶出口苯甲醛的含量为Trace,代表理论计算结果趋于0,在实际生产无法检测出。 (3)反歧化 反歧化反应即归中反应,即同种元素的不同化合物发生氧化还原反应,该元素的化合价向中间靠拢的反应。来自Ⅰ级脱轻塔塔顶馏出的二氯二氢硅与来自Ⅰ级脱高塔的四氯化硅混合后进入装有催化树脂二氯二氢硅反应器,利用间接蒸汽加热,反应温度60℃、反应压力0.6MPa,反应时间2h。反歧化反应四氯化硅和二氯二氢硅投加摩尔比为1∶1,以二氯二氢硅为基准,反应转化率为96.5%。 反应产物主要为三氯氢硅,含极少量未反应的二氯二氢硅以及过量的四氯化硅等,经冷凝器冷凝后返回冷氢化粗分工序。 6、还原 (1)还原 经提纯后的电子级三氯氢硅首先送入三氯氢硅汽化器,利用间接蒸汽通过夹套加热至145~160℃,再和纯化后的氢气混合,由喷嘴进入还原炉。还原炉安装有硅芯,采用电加热至1080℃,三氯氢硅被氢气还原成晶体硅沉积于硅芯表面,使硅棒直径不断长大,直至达到规定的尺寸。还原反应三氯氢硅和氢气投加摩尔比为4∶1,反应过程将产生氢气,炉内氢气始终处于过量状态,并起到保护作用。以三氯氢硅为基准,还原反应转化率为84.0%。 还原反应结束后,利用氢气和循环冷却水间接换热分级对还原炉进行降温,开炉卸出多晶硅棒并安装硅芯,多晶硅棒送整理车间进行破碎、酸洗、包装。 (2)清洗 还原炉生产周期为156h,结束后通H2将炉内剩余气体送入还原尾气回收系统。生产周期结束后需对还原炉内进行清洗,在清洗开始时,向钟罩内部充一定量的氮气,以避免钟罩内的释放氢气产生闪爆。由于无定形硅在80℃左右与碱液反应较活泼,故使用5~10%氢氧化钠溶液可将钟罩彻底清洗干净,最后用脱盐水漂洗、冲洗,完成清洗过程,碱液进碱液循环池循环使用。 清洗结束后,用温度为80~90℃的10万级洁净压缩空气烘干钟罩,再将钟罩冷吹至常温,通过连续吹风,完成对钟罩的干燥过程。 7、 产品整理、硅芯制备 (1)切割、破碎 从还原工序送来的硅棒运至准备间,放置在洁净工作台上,工作台表面为专用塑料板设防震措施,采用专用金属榔头对U型多晶硅棒两端敲击去除石墨头。根据市场需求,用锯床、脉冲破碎机、颚式破碎机,将去石墨头的多晶硅棒切割、破碎成符合客户要求的棒状、块状、粒状多晶硅和厂内用硅芯料。 (2)酸洗 切割、破碎后的棒状、块状、粒状多晶硅或硅芯料先采用盐酸及过氧化氢溶解硅料表面的微量活泼金属、金属氧化物、氢氧化物和部分盐类,然后利用氢氟酸和硝酸对产品表面进行腐蚀处理,最后经高纯水洗净,送入烘干箱烘干后包装待售,硅芯料用于厂内硅芯制备。 (3)硅芯制备 酸洗后的硅芯料采用人工带清洁手套放入硅芯拉制炉内的基座夹头中,取4个籽晶分别放入4个石墨夹头中,关闭炉门及放气阀,开启真空泵抽真空。当真空度显示为10Pa以下时,关闭真空并充入氩气形成保护气氛。炉内真空达到0.03MPa时,可关闭充气阀,送**频加热电源。通过高频予加热将籽晶一小部分熔化,熔化液滴将硅芯料引红熔化,然后将籽晶与硅熔体熔接在一起,并以适当的速度提拉从而制备成符合规格的硅芯。 硅芯拉制完毕,关闭高频加热电源,并用循环冷却水间接冷却3~5min至常温,启动真空泵抽出氩气。当真空度显示为10Pa时,打开放气阀将空气放入炉内。当炉内压力平衡后,打开炉门取硅芯,用硅芯磨锥机、硅芯钻孔机加工,然后放入硅芯储存槽待用。 8、尾气回收及电子级特气生产 三氯氢硅制备多晶硅的过程中,反应生成氯化氢、四氯化硅。其中有60%的三氯氢硅没有参与反应。氢气主要是保护作用,大部分氢气未参与反应。本项目采用干法回收系统,还原产生的尾气通过冷凝、压缩、吸收、解析和吸附等过程,分离出氢气、氯化氢、四氯化硅、三氯氢硅和二氯二氢硅。 (1)冷却压缩 还原尾气首先进入硅粉过滤器,硅粉过滤器内设置有高精度滤芯,过滤精度≤4μm,可将还原尾气中夹带的硅粉全部过滤。去除硅粉后的还原尾气先经换热器与入炉氢气间接换热进行初步降温,然后再经冷却器冷却,将四氯化硅、三氯氢硅、二氯二氢硅冷凝为液体分离出来,送三氯氢硅精馏塔。不凝气进入氢气压缩机压缩,压缩气压力0.9MPa、100℃,送氯化氢吸收塔。 (2)解析吸附 被氢气压缩机压缩后的气体,组分为氢气90%、三氯氢硅8%、二氯二氢硅2%、氯化氢0.2%,依次经过二氧化碳制冷、乙二醇制冷冷却后,温度降至-60℃左右,进入氯化氢吸收塔底部。氯化氢解析塔解析出的混合液组分为三氯氢硅60%、四氯化硅35%、二氯二氢硅5%,一部分作为吸收液进入氯化氢吸收塔塔顶,吸收冷却压缩后还原尾气中的氯化氢,得到的99.9%氢气送氢气吸收塔。塔釜混合液组分为三氯氢硅59.9%、四氯化硅34.9%、二氯二氢硅4.9%、氯化氢0.3%,与还原尾气冷却下来的四氯化硅、三氯氢硅、二氯二氢硅冷凝液混合后进入氯化氢解析塔。 氯化氢吸收塔混合液和还原尾气冷却液混合后进入氯化氢解析塔,塔顶分离出氯化氢气体经冷凝后,氯化氢气体用HCl压缩机压缩送至冷氢化车间使用,冷凝液回流到氯化氢解析塔。塔底三氯氢硅、四氯化硅、二氯二氢硅混合液依次经过循环冷却水间接冷却、乙二醇制冷冷却后,一部分作为吸收液进入氯化氢吸收塔,另一部分送往Ⅰ级精馏塔进行精馏提纯,作吸收液和去精馏提纯的混合液比例为2:1。 来自氯化氢吸收塔的含量99.9%氢气经换热后进入氢气吸附塔,经活性炭吸附后的氢气纯度达99.9999%,一部分经过氢气加热器、利用蒸汽加热后作为再生气进入吸附塔,另一部分送还原车间。 (3)精馏提纯 由还原尾气分离出的三氯氢硅、二氯二氢硅和四氯化硅混合气,基本不含杂质,因此采用两个塔单独精馏分离,回收三氯氢硅、二氯二氢硅和四氯化硅。 来自氯化氢解析塔塔底经冷却后的四氯化硅、三氯氢硅、二氯二氢硅混合冷凝液进入Ⅰ级精馏塔进行分离,利用间接蒸汽加热,操作压力为0.45MPa,操作温度为90℃。Ⅰ级精馏塔塔釜排出四氯化硅,送往四氯化硅提纯塔进一步精制生产电子级四氯化硅。 塔顶分离出粗三氯氢硅经冷凝后进入Ⅱ级精馏塔进行分离,利用间接蒸汽加热,塔顶操作压力为0.30MPa,操作温度为70℃。Ⅱ级精馏塔塔釜排出三氯氢硅,送往三氯氢硅提纯塔进一步精制生产电子级三氯氢硅。塔顶分离出含二氯二氢硅气体,经冷却后送往二氯二氢硅提纯塔进一步精制生产电子级二氯二氢硅。 Ⅰ级精馏塔塔釜排出的四氯化硅进入四氯化硅提纯塔,利用间接蒸汽加热,操作压力为0.45MPa,操作温度为90℃。塔釜产出电子级四氯化硅纯度达99.99%,送入四氯化硅产品罐中待售。塔顶混合气经二氧化碳制冷冷凝后,冷凝液进入三氯氢硅提纯塔。 Ⅱ级精馏塔塔釜排出的三氯氢硅进入三氯氢硅提纯塔,利用间接蒸汽加热,操作压力为0.30MPa,操作温度为70℃。塔釜产出电子级三氯氢硅纯度达99.99%,送入三氯氢硅产品罐中待售。塔顶混合气经二氧化碳制冷冷凝后,冷凝液进入二氯二氢硅提纯塔。 Ⅱ级精馏塔塔顶排出的二氯二氢硅经乙二醇制冷冷凝后进入二氯二氢硅提纯塔,利用间接蒸汽加热,操作压力为0.1MPa,操作温度为40℃。塔釜产出电子级二氯二氢硅纯度达99.99%,送入二氯二氢硅产品罐中待售。塔顶混合气经乙二醇制冷冷凝后,冷凝液返回进入氯化氢吸收塔。 9、 抽样检测 经酸洗后的多晶硅检测料送入实验楼。根据检测需要,进行实验前的准备,包括试剂的配制、仪器的开启等。然后对试样进行稳定、定容等预处理,再进行切割、破碎、酸化、消解等前处理。最后按照检测项目各仪器室进行分析、测定。 | 实际建设情况:一、氢气制备 1.电解制氢 脱盐水用加水泵送入原料水箱,经补水泵加入碱液系统。碱液系统将气液处理器与水碱箱连接在一起,配制碱液时,启动循环泵,使碱箱中的去离子水形成循环,再由水碱箱的投料口加入固态氢氧化钾,配制成30%的氢氧化钾溶液。 系统需要补碱时,由经加水泵将配制好的电解液注入碱液过滤器除去机械杂质,再用循环泵打入电解槽,形成闭环系统。电解槽为压滤式双极性串联结构,电解液在电解槽内直流电的作用下分解,在电极表面析出氢气与氧气,经各自通道分别进入气液系统。以脱盐水为基准,电解反应转化率为67.7%。 电解槽产出氢气和碱液混合物一起通过极框上阴极侧的出气孔流过氢气道,从中间负极框流出,汇集后送入气液分离器。分离出氢气导入氢气洗涤冷却器进一步洗涤,并利用循环冷却水间接冷却,然后再进入气水分离器,最终经氢气薄膜调节阀排出,通过管道进入氢气纯化工序。 2.氢气纯化 来自制氢装置的氢气首先进入气水分离器滤除游离水,经排水阀定期自动排出,除游离水后的氢气送入脱氧器。脱氧器内装有常温即可催化反应进行的高效催化剂,氧和氢经催化剂作用生成水,氧气被去除。 催化反应产生的水被氢气带出脱氧器,进入冷却器后利用循环冷却水间接冷却,不凝气随氢气进入气水分离器,分离出游离水经排水阀定期自动排出,分离出氢气送入干燥器。残留水蒸气在干燥器内被分子筛吸附,高纯度氢气再经过滤器滤尘后流出纯化系统,送入氢气储罐暂存。 二、氯化氢制备 本项目不设置盐酸解析装置,由******公司采用管道提供氯化氢气体。 三、硅粉备料 原料硅粉经槽罐车运输到厂,利用氮气气力输送至硅粉料仓、高压进料罐中,在高压进料罐利用间接蒸汽进行预热至120℃,再经重力流入低压进料罐,在回流氢气保护氛围下向氯氢化反应器内送料。 本工序产生的废气污染源主要为预热废气和进料废气,主要污染物为颗粒物落料废气、预热废气和进料废气均经密闭管道收集后送1台袋式除尘器处理,通过1根43m高排气筒排放。 四、冷氢化 1.氯氢化 预热后的硅粉在低压进料罐与催化剂氯化铜混合,再用氢气从氯氢化反应器顶部送入,解析、干燥后的氯化氢由密闭管道从氯氢化反应器底部进入,三氯氢硅精馏提纯产生的四氯化硅与电解制得的氢气在氢气压缩机出口处混合,通过密闭管道送入氯氢化反应器。原料升温采用梯级加热,145℃以下时回收系统余热并采用蒸汽间接加热,545℃以下时回收系统余热并采用电加热。氯氢化反应器内硅粉、氢气、氯化氢、四氯化硅在温度为535℃并存有催化剂条件下发生氯氢化反应,反应时间45s。氯氢化反应过程,氯化氢和硅粉投加摩尔比为3∶1,氯化氢过量加入,以硅粉为基准,氯氢化反应转化率为91.3%。 反应完成的混合气体夹带少量硅粉自反应器顶部流出,经旋风分离器和过滤器除尘后,由洗涤塔塔釜部通入,与冷凝回流的三氯氢硅液体逆流接触,进一步去除粉尘。洗涤塔顶混合气体依次经空冷、乙二醇制冷、氟利昂制冷三级冷凝器冷凝,冷凝下三氯氢硅混合料液送入合成产品罐,未被冷凝的氢气经换热后进入循环氢压缩机,经压缩后回流进入氯氢化系统中。 2.粗分 合成产品罐中的三氯氢硅混合液经换热后进入粗分塔进行分离,利用二氯二氢硅、三氯氢硅、四氯化硅不同组分的沸点差异,通过间接蒸汽加热精馏。粗分塔塔顶分离出轻组分经冷凝器利用循环冷却水间接冷凝后,得到含量≥98%三氯氢硅送往提纯系统,塔釜重组分四氯化硅经汽化塔汽化后返回氯氢化工序循环使用。 3.渣浆高沸处理系统 来自冷氢化洗涤塔渣浆和净化脱重塔渣浆,主要含四氯化硅,少量三氯氢硅、聚氯硅烷、金属氯化物和硅粉。首先将渣浆输送至转鼓过滤器,过滤出硅粉等固相进一步干燥,将氯硅烷分离,废固集中收集外委处理。氯硅烷送至脱高沸塔,轻组分回氢化粗分塔分离后作为氢化系统原料,重组分高沸分离后送鑫环高沸反应器裂解反应。高沸裂解反应重组分Si2Cl6和HCl投加摩尔比为1∶1.2,以HCl为基准,反应转化率为65.0%。 本工序产生的废气污染源主要为脱高沸塔不凝气和转鼓滤下固体蒸发不凝气不凝气主要污染物为二氯二氢硅、三氯氢硅、氢气,送至废气处理装置,使用石灰乳喷淋中和后放空,产生钙盐进行絮凝沉降分离,洗****处理站处理。 五、三氯氢硅提纯 1.氢化料精馏系统 ⑴合成1级塔 自冷氢化的产品粗三氯氢硅经除硼吸附后,首先进入合成1级塔,合成1级塔为隔板塔。通过合成1级塔分离后,合成1级塔的塔底采出高沸送至氢化装置,侧线采出提纯的三氯氢硅作为合成2级塔原料,塔顶气经过水冷器冷凝后,变成液态氯硅烷,进入高位回流罐,再通过回流泵输送,一部分作为塔顶回流,一部分作为低沸物采出,送至反歧化分离塔。 ⑵合成2级塔 合成1级塔侧线采出进入合成2级塔,通过合成2级塔分离后,合成2级塔的塔底采出高沸送至氢化装置,塔顶气作为1塔再沸器热源后,变成液态氯硅烷,进入回流罐,再通过回流泵输送,一部分作为塔顶回流,一部分作为合成3级塔原料。 ⑶合成3级塔 合成2级塔塔顶采出进入合成3级塔,通过合成3级塔分离后,合成3级塔的塔底采出高沸送至反歧化吸附塔,经除硼后返回原料罐,塔顶气经过水冷器冷凝后,变成液态氯硅烷,进入回流罐,再通过回流泵输送,一部分作为塔顶回流,一部分作为合成4级塔原料。 ⑷合成4级塔 合成3级塔塔顶采出进入合成4级塔,通过合成4级塔分离后,合成4级塔的塔底采出作为合成5级塔原料,塔顶气作为合成3级塔再沸器热源后,变成液态氯硅烷,进入回流罐,再通过回流泵输送,一部分作为塔顶回流,一部分作为低沸物采出,送至反歧化分离塔。 ⑸合成5级塔 合成4级塔塔底采出进入合成5级塔,通过合成5级塔分离后,合成5级塔的塔底采出高沸送至至反歧化吸附塔,经除硼后返回原料罐,塔顶气作为经过水冷器冷凝后,变成液态氯硅烷,进入回流罐,再通过回流泵输送,一部分作为塔顶回流,一部分作为氢化三氯氢硅精馏的产品送至罐区。 2.还原料精馏系统 ⑴回收1级塔 来自尾气回收的氯硅烷进入回收1级塔,塔底采出含有少量硅粉、重杂的四氯化硅,送至渣浆高沸;侧线液相采出四氯化硅,一部分作为反歧化原料,送至反歧化反应器,一部分作为四氯化硅产品送至罐区或氢化储罐;塔顶气作为回收2塔再沸器热源后,变成液态氯硅烷,进入高位回流罐,再通过回流泵输送,一部分作为塔顶回流,一部分作为回收2级塔原料。 ⑵回收2级塔 回收1级塔塔顶采出进入回收2级塔,塔底采出送至氢化装置,侧线采出部分高纯三氯氢硅,送至罐区作为回收料供还原。塔顶气经水冷器冷凝后,变成液态氯硅烷,进入回流罐,再通过回流泵输送,一部分作为塔顶回流,一部分二氯二轻硅送至反歧化分离单元。 3.反歧化系统 来自合成1级塔、合成4级塔塔顶采出的低沸物以及反歧化反应器出口的氯硅烷混合进入反歧化分离塔,反歧化分离塔的塔底采出送至罐区或氢化装置,侧线采出部分三氯氢硅与合成3级塔釜采、合成5级塔釜采、合成6级塔釜采氯硅烷混合后至吸附塔,吸附后送至罐区。塔顶气经水冷器冷凝后,变成液态氯硅烷,进入回流罐,再通过回流泵输送,一部分作为塔顶回流,一部分二氯二氢硅与回收1级塔顶采二氯二氢硅混合后,再与来自回收1级塔侧采的的四氯化硅按一定比例混合后,经冷却至合适温度后进入反歧化反应器,在反应器内树脂作用下发生反应,将二氯二氢硅和四氯化硅转化为三氯氢硅;反歧化反应器出料进入反歧化后缓冲罐,经泵送至反歧化分离塔。 六、还原 1.还原 经提纯后的电子级三氯氢硅首先送入三氯氢硅汽化器,利用间接蒸汽通过夹套加热至145~160℃,再和纯化后的氢气混合,由喷嘴进入还原炉。还原炉安装有硅芯,采用电加热至1080℃,三氯氢硅被氢气还原成晶体硅沉积于硅芯表面,使硅棒直径不断长大,直至达到规定的尺寸。还原反应三氯氢硅和氢气投加摩尔比为4∶1,反应过程将产生氢气,炉内氢气始终处于过量状态,并起到保护作用。以三氯氢硅为基准,还原反应转化率为84.0%。 还原反应结束后,利用氢气和循环冷却水间接换热分级对还原炉进行降温,开炉卸出多晶硅棒并安装硅芯,多晶硅棒送整理车间进行破碎、酸洗、包装。 2.清洗 还原炉生产周期为156h,结束后通H2将炉内剩余气体送入还原尾气回收系统。生产周期结束后需对还原炉内进行清洗,在清洗开始时,向钟罩内部充一定量的氮气,以避免钟罩内的释放氢气产生闪爆。由于无定形硅在80℃左右与碱液反应较活泼,故使用5~10%氢氧化钠溶液可将钟罩彻底清洗干净,最后用脱盐水漂洗、冲洗,完成清洗过程,碱液进碱液循环池循环使用。 清洗结束后,用温度为80~90℃的10万级洁净压缩空气烘干钟罩,再将钟罩冷吹至常温,通过连续吹风,完成对钟罩的干燥过程。 七、产品整理、硅芯制备 1.切割、破碎 从还原工序送来的硅棒运至准备间,放置在洁净工作台上,工作台表面为专用塑料板设防震措施,采用专用金属榔头对U型多晶硅棒两端敲击去除石墨头。根据市场需求,用锯床、脉冲破碎机、颚式破碎机,将去石墨头的多晶硅棒切割、破碎成符合客户要求的棒状、块状、粒状多晶硅和厂内用硅芯料。 2.酸洗 切割、破碎后的棒状、块状、粒状多晶硅或硅芯料先采用盐酸、氢氟酸和硝酸对产品表面进行腐蚀处理,最后经高纯水洗净,送入烘干箱烘干后包装待售,硅芯料用于厂内硅芯制备。 3.硅芯制备 酸洗后的硅芯料采用人工带清洁手套放入硅芯拉制炉内的基座夹头中,取5个籽晶分别放入5个石墨夹头中,关闭炉门及放气阀,开启真空泵抽真空。当真空度显示为10Pa以下时,关闭真空并充入氩气形成保护气氛。炉内真空达到1kPa时,可关闭充气阀,送**频加热电源。通过高频加热母料至熔化,然后将籽晶与硅熔体熔接在一起,并以适当的速度提拉从而制备成符合规格的硅芯。 硅芯拉制完毕,关闭高频加热电源,冷却至常温,打开泄压阀。当炉内压力平衡后,打开炉门取硅芯,用硅芯磨锥机、硅芯钻孔机加工,硅芯再进行清洗后待用。 八、尾气回收 三氯氢硅制备多晶硅的过程中,反应生成氯化氢、四氯化硅。尾气回收装置先进的流程组合及控制方案充分保证了产品纯度并满足高质量多晶硅生产的要求,相对常规工艺此技术更加节能。本项目采用干法回收系统,还原产生的尾气通过冷凝、压缩、吸收、解析和吸附等过程,分离出氢气、氯化氢、四氯化硅、三氯氢硅和二氯二氢硅。本项目尾气回收装置,主要由还原尾气冷却、氢气压缩、氯化氢吸收、氯化氢解析、氢气吸附等工序组成; (一)冷却压缩 1.还原尾气冷却 还原尾气经过过滤除去硅粉后,依次经过两级热量回收换热器、循环水冷却、7℃水冷却、氟利昂冷却,绝大部分氯硅烷冷凝后进入低压氯硅烷冷凝液罐,经热交换器回收压缩机后氢气、还原尾气热量后送入解析塔,不凝气被还原尾气复热后送入氢气压缩机压缩。 2.氢气压缩 还原尾气冷却分离出的不凝气,先进入尾气压缩机前缓冲罐,经缓冲后进入尾气压缩机压缩,压缩气经尾气压缩机后缓冲罐,冷却后送至HCL吸收塔。 本工序产生的噪声污染源主要为氢气压缩机,采取氢气压缩机安装在符合隔振设计要求的混凝土基座上,并布置在尾气回收车间内的降噪措施。固体废物污染源为过滤器废硅粉,全部采用包装袋收集,暂存于仓库内,外售工业硅企业回收利用。 (二)解析吸附 1.氯化氢吸收 被尾气压缩机压缩后的尾气,依次经过换热、冷却后,气相自塔底部进入HCL吸收塔,液相进入高压氯硅烷冷凝液罐收集后送至低压氯硅烷凝液罐。经解析塔脱出HCL后的氯硅烷(贫液)经过多级冷却后作为吸收液自塔顶进入吸收塔。利用氯硅烷(贫液)吸收尾气中HCL气体,HCL吸收塔顶回收氢气与压缩机后尾气热交换复热后进入吸附塔。 2.氯化氢解析及汽提 来自HCL吸收塔釜的氯硅烷(富液)经氯硅烷热交换器、HCL解析塔进料预热器被HCL解析塔塔釜的氯硅烷(贫液)加热后进入HCL解析塔,来自还原尾气冷却工序的氯硅烷冷凝液同时进入解析塔。 HCL解析塔顶气相经循环水、氟利昂冷却后,气相经热交换复热后送至冷氢化装置,冷凝液送至氯化氢回流罐,一部分回流至HCL吸收塔塔顶,一部分送至罐区。 来自HCL解析塔釜的氯硅烷(贫液)与来自HCL吸收塔塔釜的氯硅烷(富液)换热冷却后,大部分贫液继续经循环水冷却、与氯硅烷(富液)换热、氟利昂冷却后,作为吸收液自塔顶进入吸收塔;其余氯硅烷经泵增压后送至精馏装置。 3.氢气吸附工序 来自吸收塔的氢气经过复热后进入吸附塔,利用活性炭作为吸附剂,经吸附后的氢气纯度达99.9999%(wt%)。吸附后的回收氢气少部分经换热后作为再生气进入吸附塔吹扫,大部分作为产品氢气进入回收氢气缓冲罐,经与还原尾气换热后送至还原装置,多余的氢气送至冷氢化装置回收利用。 4.再生气回收工序 含有H2、HCl、氯硅烷的吸附塔的高温再生气经与反吹氢气换热冷却后,与来自冷氢化、精馏、罐区等装置的含氢尾气混合,经冷冻水冷却后送至再生气压缩机吸入罐,经再生气压缩机压缩后送至再生气压缩机排出罐。压缩后的再生气经热交换、氟利昂冷却至后,液相送至再生气凝液缓冲罐收集后,排至罐区;气相经与压缩后的再生气换热后送至冷氢化装置回收利用。 九、抽样检测 经酸洗后的多晶硅检测料送入整理装置三楼检测室。根据检测需要,进行实验前的准备,包括试剂的配制、仪器的开启等。然后对试样进行稳定、定容等预处理,再进行切割、破碎、酸化、消解等前处理。最后按照检测项目各仪器室进行分析、测定。 |
变更情况1 环评建设内容:**还原厂车间1座,地上2层钢混结构,占地面积4200m2,主要设备为44台多晶硅还原炉 实际建设情况:**还原厂车间1座,地上2层钢混结构,占地面积4200m2,主要设备为26台多晶硅还原炉 变更原因:设备改进,单台设备产能增加 变更情况2 环评建设内容:**盐酸解析车间1座,地上1层钢混结构,占地面积1900 m2,主要包括盐酸解析、氯化氢脱水工序 实际建设情况:******公司****公司管道直接供给氯化氢气体 变更原因:优化**配置,减少**浪费 变更情况3 环评建设内容:**精馏车间1座,地上1层钢混结构,占地面积3500 m2,主要安装脱轻塔、脱重塔、络合精馏塔等设备,用于三氯氢硅的提纯 实际建设情况:**精馏车间1座,地上1层钢混结构,占地面积3500 m2,主要安装合成塔、回收塔等设备,用于三氯氢硅的提纯 变更原因:优化工艺、取消络合精馏塔 ,不再使用苯甲酚,杜绝VOC | 是否属于重大变动:|
环保设施或环保措施
环评要求: 1、氢气制备 (1)电解制氢 本工序产生的废气污染源主要为氢氧化钾投料废气,主要污染物为颗粒物。固态氢氧化钾外购后直接配制碱液,不在厂内储存。碱液配制后在碱液罐内储存待用,一般配制周期较长,故投料废气间歇产生。氢氧化钾采用人工破袋,投料时控制落料高度,且碱液配制在封闭式电解车间内进行,能够对投料无组织废气的排放起到一定的抑制作用。电解阳极产生的氧气,不属于污染物,直接放空。 废水污染源主要为水碱箱定期排放废水,主要污染物为氢氧化钾,****处理站处理。噪声污染源主要为电解槽、补水泵、循环泵等,采取将泵类安装在符合隔振设计要求的混凝土基座上,电解槽和泵类均布置在电解车间内的降噪措施。固体废物污染源主要为过滤杂质和废隔膜,过滤杂质全部经专用容器收集,送危废暂存库暂存后,交有资质的单位处置;废隔膜由生产厂家回收。 (2)氢气纯化 本工序产生的废水污染源主要为气水分离废水,主要污染物为SS,****处理站处理。噪声污染源主要为氢气压缩机,采取将氢气压缩机安装在符合隔振设计要求的混凝土基座上,并布置在电解车间内的降噪措施。固体废物污染源主要为废催化剂和废分子筛,废催化剂和废分子筛全部由生产厂家回收。 2、氯化氢制备 (1)盐酸解析 本工序产生的固体废物污染源主要为解析残渣,全部经专用容器收集,送危废暂存库暂存后,交有资质的单位处置。 (2)氯化氢脱水 本工序产生的废水污染源主要为冷凝废水,主要污染物为氯化氢,****处理站处理。噪声污染源主要为氯化氢压缩机,采取将氯化氢压缩机安装在符合隔振设计要求的混凝土基座上,并布置在盐酸解析车间内的降噪措施。固体废物污染源主要为废硫酸,全部经专用容器收集,送危废暂存库暂存后,交有资质的单位处置。 3、硅粉备料 本工序产生的废气污染源主要为落料废气、预热废气和进料废气,主要污染物为颗粒物,本项目将仓泵受料口布置在封闭式操作间内,操作间内上方布置集气罩,采用负压引风,将落料粉尘引入密闭废气管道。预热废气经高压进料罐配置的过滤器过滤后由排气口排出。落料废气、预热废气和进料废气均经密闭管道收集后送1台袋式除尘器处理,通过1根15m高排气筒排放。 噪声污染源主要为仓泵,采取将仓泵安装在符合隔振设计要求的混凝土基座上,并布置在冷氢化车间内的降噪措施。 4、冷氢化 (1)氯氢化 本工序产生的废气污染源主要为氯氢化反应器置换废气,成分为氢气和少量氯化氢、二氯二氢硅、三氯氢硅、四氯化硅,主要污染物为氯化氢、二氯二氢硅、三氯氢硅、四氯化硅等,经密闭管道引入全厂废气处理系统处理。干燥后的氯化氢含少量硫酸雾,在氯氢化反应器内高温条件消耗少量催化剂氯化铜,释放出氯化氢并析出盐结晶。 噪声污染源主要为风机、循环氢压缩机,采取循环氢压缩机安装在符合隔振设计要求的混凝土基座上,风机加装消音器,风机、循环氢压缩机均布置在氯氢化车间内的降噪措施。固体废物污染源主要为旋风分离器、过滤器收集的废硅粉,全部采用包装袋收集,暂存于仓库内,外售工业硅企业回收利用。洗涤塔渣浆送厂区内渣浆处理系统处理。 (2)粗分 本工序产生的废气污染源主要为粗分不凝气,主要污染物为二氯二氢硅、三氯氢硅、四氯化硅等,经密闭管道引入全厂废气处理系统处理。汽化渣浆送厂区内渣浆处理系统处理。 (3)渣浆处理系统 本工序产生的废气污染源主要为脱轻不凝气、高沸反应不凝气、脱高不凝气和水解废气,脱轻不凝气、高沸反应不凝气、脱高不凝气主要污染物为二氯二氢硅、三氯氢硅、四氯化硅等,水解废气成分为氢气、氯化氢、二氯二氢硅、三氯氢硅、四氯化硅,主要污染物为氯化氢、二氯二氢硅、三氯氢硅、四氯化硅等,均经密闭管道引入全厂废气处理系统处理。废水污染源主要为水解废水,主要污染物为硅酸钙、氯化钙、氢氧化钙、SS等,****处理站处理。 5、 三氯氢硅提纯 (1)精馏提纯 本工序产生的废气污染源主要为各精馏塔冷凝不凝气,主要污染物为二氯二氢硅、三氯氢硅、四氯化硅等,经密闭管道引入全厂废气处理系统处理。固体废物污染源主要为废吸附剂,全部经专用容器收集,送危废暂存库暂存后,交有资质的单位处置。 (2)络合精馏 本工序产生的废气污染源主要为络合精馏不凝气、苯甲醛分离精馏不凝气,络合精馏不凝气主要污染物为三氯氢硅等,苯甲醛分离精馏不凝气主要污染物为三氯氢硅、苯甲醛等,全部经密闭管道引入全厂废气处理系统处理。固体废物污染源主要为苯甲醛分离精馏塔釜底残渣,全部经专用容器收集,送危废暂存库暂存后,交有资质的单位处置。 (3)反歧化 本工序产生的废气污染源主要为冷凝不凝气,主要污染物为二氯二氢硅、三氯氢硅、四氯化硅等,经密闭管道引入全厂废气处理系统处理。固体废物污染源主要为废树脂催化剂,全部经专用容器收集,送危废暂存库暂存后,交有资质的单位处置。 6、还原 本工序产生的废气污染源主要为还原炉置换废气,成分为氮气、氢气、氯化氢、二氯二氢硅、三氯氢硅、四氯化硅,主要污染物为氯化氢、二氯二氢硅、三氯氢硅、四氯化硅等,经密闭管道引入全厂废气处理系统处理。还原尾气进入还原尾气回收及电子级特气生产。 (2)清洗 本工序产生的废水污染源主要为清洗废水和碱液循环池定期排水,主要污染物均为氢氧化钠、硅酸钠、SS,****处理站处理。 7、 产品整理、硅芯制备 (1)切割、破碎 本工序产生的废气污染源主要为切割废气、破碎废气、筛分废气,主要污染物为颗粒物,本项目将锯床、脉冲破碎机、颚式破碎机、筛分机均布置在封闭式操作间内,操作间内上方布置集气罩,采用负压引风,将切割粉尘、破碎粉尘、筛分粉尘引入密闭废气管道送整理车间粉尘处理系统,经1台袋式除尘器处理,通过1根15m高排气筒排放。噪声污染源主要为锯床、脉冲破碎机、颚式破碎机、筛分机,采取脉冲破碎机、颚式破碎机、筛分机安装在符合隔振设计要求的混凝土基座上,锯床、脉冲破碎机、颚式破碎机、筛分机均布置在整理车间内的降噪措施。固体废物污染源主要为废石墨头,废石墨头全部采用包装袋收集,暂存于仓库内,由生产厂家回收。 (2)酸洗 本工序产生的废气污染源主要为酸洗废气,主要污染物为氯化氢、氢氟酸、硝酸和氮氧化物等,经酸洗机连接的密闭管道引入三级碱喷淋塔处理,通过1根35m高排气筒排放。废水污染源主要为清洗废水,主要污染物为氢氟酸、硝酸、SS,****处理站处理。噪声污染源主要为包装机,采取包装机布置在整理车间内的降噪措施。固体废物污染源主要为酸洗废酸,全部经专用容器收集,送危废暂存库暂存后,交有资质的单位处置。 (3)硅芯制备 本工序产生的废气污染源主要为磨锥、钻孔加工废气,硅芯磨锥机、硅芯钻孔机均布置在封闭式操作间内,操作间内上方布置集气罩,采用负压引风,将加工粉尘引入密闭废气管道送整理车间粉尘处理系统处理。真空泵抽出空气或氩气均不属于污染物,直接放空。 噪声污染源为真空泵、硅芯磨锥机、硅芯钻孔机,采取将泵类安装在符合隔振设计要求的混凝土基座上,硅芯磨锥机、硅芯钻孔机和泵类均布置在整理车间内的降噪措施。 8、 尾气回收及电子级特气生产 (1)冷却压缩 本工序产生的噪声污染源主要为氢气压缩机,采取氢气压缩机安装在符合隔振设计要求的混凝土基座上,并布置在尾气回收车间内的降噪措施。固体废物污染源为过滤器废硅粉,全部采用包装袋收集,暂存于仓库内,外售工业硅企业回收利用。 (2)解析吸附 本工序产生的噪声污染源主要为氯化氢压缩机,采取氯化氢压缩机安装在符合隔振设计要求的混凝土基座上,并布置在尾气回收车间内的降噪措施。固体废物污染源为废活性炭,全部经专用容器收集,送危废暂存库暂存后,交有资质的单位处置。 (3)精馏提纯 本工序产生的废气污染源主要为Ⅰ级精馏不凝气、Ⅱ级精馏不凝气、四氯化硅提纯不凝气、三氯氢硅提纯不凝气、二氯二氢硅提纯不凝气,主要污染物为氯化氢、二氯二氢硅、三氯氢硅、四氯化硅等,均经密闭管道引入全厂废气处理系统处理。 9、 抽样检测 本工序废气污染源主要为检测过程中切割废气、破碎废气、研磨废气、酸性废气、有机废气等试验废气,主要污染物为颗粒物、氯化氢、硝酸、氢氟酸等,均通过通风厨或移动式集气罩收集,经风机引入1套碱喷淋吸收塔+活性炭处理,再通过实验楼楼顶设置的1根7m高排气筒排放,排放高度为15m。废水污染源主要为酸性废水、有机废水、试样冲洗废水、不含重金属试剂的器皿清洗废水等试验废水,经实验楼内建设的污水一体化处理装置处理。固体废物污染源主要为含重金属实验废液、含重金属试剂的实验材料清洗废液、检测废弃样品、有机废液等试验废物,全部经专用容器收集,送办公生活区建设的危废暂存间暂存后,交有资质的单位处置。 批复要求: 2.做好大气污染防治工作。项目各生产车间均进行封闭,硅粉备料工序和硅棒切割、破碎、筛分、打磨、钻孔等工序产生的废气经集气罩收集后通过袋式除尘器处理,工艺废气及储罐呼吸废气经密闭管道引入全厂废气处理系统(深冷+水洗+碱洗)处理,酸洗废气经密闭管道引入三级碱喷淋塔处理,抽样检测实验废气经通风厨或移动式集气罩收集后通过碱喷淋吸收塔+活性炭处理,以上废气中颗粒物、氯化氢、硫酸雾、非甲烷总烃、氟化物、氮氧化物排放满足《大气污染物综合排放标准》(GB16297-1996)表2新污染源大气污染物排放限值二级标准后由符合规定的排气筒排放;厂区粉尘无组织排放须满足《大气污染物综合排放标准》(GB 16297-1996)表2无组织监控浓度限值;食堂油烟经油烟净化装置处理,满足《饮食业油烟排放标准》(GB18483-2001)后通过屋顶排气筒排放。 实施节能技术改造,建立能源管理制度,实现温室气体排放不新增。 3.加强水环境保护。项目生****处理站处理,生活污水经化粪池处理,以上废水须满足《污水综合排放标准》(GB8978-1996)三****处理厂收水水质标准以及溶解性总固体≤2000mg/L****园区含氟化物污水****处理厂处理。项目各生产车间、库房、危废暂存间等区域须做好防渗措施。 4.严格控制噪声环境影响。厂界噪声须满足《工业企业厂界环境噪声排放标准》(GB12348-2008)中3类标准要求。 5.加强固废管理理,优先进行综合利用,不可利用的固废须合理处置。废硅粉、废石墨头、废实验样品外运综合利用;电解槽废隔膜、氢气纯化产生的废催化剂和废分子筛、脱盐水纯水制备产生的废树脂和废反渗透膜、制氮产生的废分子筛等由厂家更换回收;生活垃圾由环卫部门处置;污水处理站污泥按照相关规定进行固废属性鉴别,若属于危险废物则交有资质单位转运处置,若属于一般固废则运至指定地点填埋处置;:制氢过滤杂质、解析残渣、废酸、废吸附剂、釜底残渣、反歧化废催化剂、废活性炭、实验废物、含重金属的实验废液及清洗废水、废机油等危险废物分类暂存于厂区危废暂存库,交有资质的单位转运处置。项目须在厂区内配套建设足够容量的一般固废临时贮存库和危险废物临时贮存库,严格按照《一般工业固体废物贮存、处置场污染控制标准》(GB18599-2020)和《危险废物贮存污染控制标准》(GB18597-2001)及修改单要求进行管理。 | 实际建设情况:一、废气治理措施 1.制氢装置投料废气 本项目电解制氢需配制碱液,固态氢氧化钾外购后直接配制,不在厂内储存。碱液配制后在碱液罐内储存待用,一般配制周期较长,故投料废气间歇产生,废气主要污染因子为颗粒物,碱液配置在封闭式制氢装置内进行,对外界无影响 2.硅粉备料废气 原料硅粉在预热和上料过程,均会有粉尘废气产生。本项目通过槽罐车运输硅粉到氢化装置,利用氮气通过密闭管道将硅粉送至硅粉料仓预热废气和上料废气一起经1台袋式除尘器处理,通过1根43m高排气筒排放。 3.工艺废气 全厂工艺废气主要来自冷氢化、三氯氢硅提纯、还原、尾气回收、渣浆处理过程,大部分废气为各工序精馏塔配套的冷凝器不凝气,还包括渣浆处理水解废气、氯氢化反应器置换废气、还原炉置换废气等。 废气中主要污染物为HCl、SiH2Cl2、SiHCl3、SiCl4,目前SiH2Cl2、SiHCl3、SiCl4无大气排放标准。由于SiH2Cl2、SiHCl3、SiCl4等氯硅烷类极易与H2O反应生成HCl,故污染因子均折算成HCl分析。氯硅烷类与水反应方程如下:(取消络合精馏塔,不涉及络合精馏) SiHCl3 + 2H2O → SiO2 + 3HCl + H2 SiH2Cl2 + 2H2O → SiO2 + 2HCl + 2H2 SiCl4 + 2H2O → SiO2 + 4HCl 各储罐的顶部设单向定压换气阀2套,其中1套定向吸气,在储罐压力下降时吸进空气以避免储罐负压;另1套为定向呼气,在储罐内压力升高时排出罐内气体。本工程在储罐呼气口处连接密闭废气管道,通过负压将储罐呼吸废气引入全厂生产工艺废气处理系统进行处理,工艺废气及储罐呼吸废气采用首先采用深冷回收氯硅烷,然后再根据气体成分返回冷氢化利用或去废气洗涤装置。 在多晶硅生产过程中,SiHCl3是多晶硅气相沉积还原炉内的主要反应原料之一,对这部分废气的有效回收是提高系统氯元素、硅元素以及氢元素利用率的关键环节之一,可减少系统元素的损失,降低生产成本。此类含氯硅烷为主的废气主要通过深冷回收工艺进行回收。 在生产过程中,废气中含有微量的氯硅烷,根据氯硅烷易水解的特性,采用3级碱洗的治理措施。采用3级氢氧化钙溶液雾状喷淋,使SiH2Cl2、SiHCl3、SiCl4等氯硅烷发生水解反应,最终生成二氧化硅和CaCl2、H2,****处理站处理。其主要的反应方程式如下: SiHCl3 + 3H2O → H2SiO3 + 3HCl + H2↑ SiCl4 + 3H2O → H2SiO3 + 4HCl H2SiO3 → SiO2↓+ H2O 2HCl + Ca(OH)2 → CaCl2 + 2H2O 设置3台三级碱液喷淋塔(1用2备)。全厂工艺尾气(约3800Nm3/h)通过全厂工艺管道进入尾气缓冲罐,经过缓冲后进入尾气洗涤塔,经过三级碱洗后由40m高排气筒排放。在塔内经循环泵加压后的稀碱液通过喷嘴进行三级雾化喷淋洗涤。经过洗涤的废气再进入尾气液封槽液封后经阻火器达标排放,主要成份为氯化氢、少量氮气、氢气。通过尾气洗涤液循环泵将尾气洗涤液储槽中的碱液进行循环输送至尾气洗涤塔进行喷淋。当喷淋液pH下降至弱碱性时,及时补充新鲜碱液。 4.整理粉尘废气 从还原系统制得的多晶硅棒,需按照客户要求用锯床、脉冲破碎机、颚式破碎机切割、破碎棒状、块状、粒状多晶硅。硅芯制备也需用硅芯磨锥机、硅芯钻孔机加工。切割、破碎、筛分、打磨、钻孔都将产生粉尘废气。本项目生产电子级多晶硅,对产品纯度要求较高。为保证整理车间洁净,将锯床、脉冲破碎机、颚式破碎机、筛分机、硅芯磨锥机、硅芯钻孔机均布置在封闭式操作间内,操作间内上方布置集气罩,采用负压引风,将切割粉尘、破碎粉尘、筛分粉尘引入密闭废气管道送整理车间粉尘处理系统,厂房为为高纯洁净环境,经袋式除尘器处理后,返回空调风系统循环使用,废气不外排。 5.酸洗废气 本项目多晶硅酸洗废气经酸洗机连接的密闭管道引入三级碱喷淋塔(四塔串联)处理,通过1根35m高排气筒排放。 6.抽样检测实验废气 原环评时设计的实验楼不再建设,仅在整理装置三楼设置1个检测分析间,用于整理车间的分析检测,其它检测项目依托******公司****中心。 整理车间分析检测间配制、试样预处理、检测化验过程中将产生少量酸性废气,抽样检测试样制备切割、破碎、研磨过程将产生粉尘废气,检测过程均在通风厨或移动式集气罩下进行,颗粒物、HCl、NOx、氟化物等均通过通风厨或移动式集气罩收集,经风机引入1套碱喷淋吸收塔+活性炭处理,再通过楼顶设置的1根35m高排气筒排放。 7.石灰落料废气 全厂工艺废气处理的碱洗过程均采用石灰浆作为吸收液,石灰浆通过外购石灰进行调配。石灰采用槽罐汽车运输入厂通过氮气送入石灰料仓,配浆时直接密闭管道接入石灰池内进行配置。酸性废气处理、试验废气处理的碱洗过程均采用袋装片状氢氧化钠配置吸收液。投料过程将产生落料粉尘。采用人工破袋,投料时控制落料高度,且浆配置在封闭式厂房内进行。 8.食堂油烟 本项目在办公生活区内设置食堂1座,灶头数5个。本项目在食堂设置油烟净化器1套,烟气引至沿食堂专用烟道在楼顶排放,满足《饮食业油烟排放标准》(试行)(GB 18483- 2001)最高允许排放浓度标准要求。 二、废水治理措施 1.生产废水 本工程产生的废水主要为生产废水和生活污水。生产废水包括脱盐水及高纯水制备、循环冷却水系统产生的废水,以及电解制氢工序水碱箱定期排放废水、氢气纯化工序气水分离废水、还原工序清洗废水和碱液循环池定期排水、酸洗工序清洗废水、抽样检测废水、酸洗废气处理废水、实验室废气处理废水、全厂工艺废气处理废水、地面冲洗废水。 生产废水量共计157m3/h,生产工艺废水****处理站处理后,排入开发区生产废水管网,最****处理厂处理。 ****处理站一座,设计总处理能力125m3/h,设计操作弹性50~120%。包括:低盐水预处理单元(设计处理量110m3/h)、高盐水预处理单元(设计处理量15m3/h)、MVR蒸发结晶单元(设计处理量15m3/h)。低盐废水包括低盐废水预处理与膜处理系统(膜处理系统二期建设,届时可实现废水零排放)。工艺流程简述如下: ⑴低盐水预处理单元: 装置产生的酸性废水及其他低盐废水通过加石灰乳中和、换热后,满足排放标准进入废水外排水池,通过市政管网****处理厂。 ⑵高盐水预处理单元: 装置高盐废水进入本系统高盐水高效沉淀池,在澄清池中投加化学药剂,主要为混凝剂(聚合硫酸铁)、助凝剂(PAM)及石灰乳等,充分反应后经过斜板澄清池进入中间水池,再去往气浮池和多介质过滤器等过滤措施进行固液分离,高盐水预处理清液去往浓盐水蒸发结晶系统。 ⑶蒸发结晶单元: 本项目MVR工艺简介: 高盐水预处理单元排出的浓盐水进入蒸发进料罐,在进料罐中经加药调节后通过进料泵送入板式换热器,换热至温度接近沸点后送入脱气塔。在脱气塔中去除氧和其它不凝气,通过除氧还可减轻浓盐水对蒸发器的腐蚀。经加药、预热和除氧后的浓盐水进入蒸发器盐水槽,并和循环盐水进行混合。循环盐水从蒸发器底部用循环泵送至蒸发器顶部溢流箱,在换热管内被壳侧的蒸汽加热部分汽化,完成降膜蒸发过程。蒸发过程产生的二次蒸汽经机械蒸汽压缩机升温升压提高蒸汽品质后进入蒸发器壳侧,作为蒸发系统的热源。蒸汽冷凝的产品水与料液换热后去往产品水池送出界区回用。高盐水MVR蒸发系统采用盐种防垢法降膜蒸发工艺,保障高盐水蒸发系统的长周期稳定运行。 高盐水蒸发系统排出的浓盐水经输送泵送至结晶进料罐,通过进料泵送入结晶循环泵出口处,与结晶器循环浆料进行混合,进入结晶加热器。结晶器由外供蒸汽供热,闪蒸产生的二次蒸汽经冷凝器冷凝成蒸馏液,经换热后作为产品水送出界区回用。结晶系统产生的浓盐浆经过离心脱水机分离出氯化钠盐。浓缩母液去往结片机产出结晶混合杂盐。 2.生活污水 本工程生活污水产生量为6.6m3/h,经化粪池预处理后,排入开发区生活污水管网,最****处理厂处理。 3.事故废水 为保证事故情况下,事故废水不会对土壤及地下水环境产生影响,本工程设置环境风险事故水污染防控三级防控系统,防止环境风险事故造成水污染。 第一级防控系统由装置区围堰、罐区防火堤和区内事故水池组成,收集一般事故泄漏的物料,防止轻微事故泄漏造成的水环境污染;装置区围堰高度不小于15cm,宽度不超过150mm围堰和导流设施,并设置清污、雨污切换系统;在罐区界区设置防火堤,防火堤内设置混凝土地坪并作防腐防渗处理,防火堤外设置切换阀门。罐区整体外围设置1个围堰。其中仅有1个为四氯化硅储罐,在围堰内单独再设置1个围堰,剩下的7个均为三氯氢硅储罐(同种物料,无需再设置防火隔堤)。一级防控措施构筑生产过程中环境安全第一层防控网,在轻微事故时利用围堤控制泄漏物料的转移,防止泄漏物料及事故废水外排造成污染。罐区围堤高度固定顶罐不应小于罐组内1个最大储罐的容积。第二级防控系统由装置区、罐区雨水收集池组成,将较大生产事故泄漏于装置区围堤、罐区围堤外的物料或水通过雨水收集池收集,回收物****处理站****园区污水处理厂处理,防止较大生产事故泄漏物料和污染消防水造成的环境污染;事故后清洗雨水收集池,清洗水****处理站处理。 第三级防控系统为污水处理前的污水收集与事故水池。多余的废水通过厂区管网自流至事故水池,随后通过配套水泵送入本项目污水站再处理。作为事故状态下的储存与调控手段,防止重大事故泄漏物料和污染消防水造成的环境污染。发生重大的火灾、爆炸事故时,消防水及其携带的物料通过第一级、第二级防控系统进入第三级防控系统,之后****处理站处理。事故处理完毕后,重点清洗污水收集与储存池,清****处理站处理。事故水池容积为4000m3,钢混结构,池底垫层使用10公分厚标号为C20的混凝土浇筑+池底板使用100公分厚标号为C35的混凝土浇筑+水池壁使用标号为C35的混凝土一体浇注完成,浇筑厚度450mm。池内壁表面及外露部分用1:2防水砂浆分层抹面,防水砂浆内掺5%防水剂,,实验抗渗等级P8,满足渗透系数不大于1×10-7cm/s的等效黏土防渗层要求。1座4000m3事故水池能够满足全厂1次消防事故水水量的要求。 4.初期雨水 本工程实行雨污分流制。厂区道路边及硬化场地边缘设雨水沟,初期雨水经收****处理站处理,****园区污水管网,最****处理厂。未受污染的清净雨水进入雨水监测****园区雨水管道。 三、噪声治理措施 本工程噪声污染源主要为电解槽、补水泵、循环泵、氢气压缩机、氯化氢压缩机、风机、循环氢压缩机、锯床、破碎机、筛分机、真空泵、硅芯磨锥机、硅芯钻孔机、包装机、氢气压缩机、氯化氢压缩机、其他各类风机及其他泵类,产噪声级值为85~95dB(A)。采取将补水泵、循环泵、氢气压缩机、氯化氢压缩机、循环氢压缩机、破碎机、筛分机、真空泵安装在符合隔振设计要求的混凝土基座上的减振降噪措施,各类风机加装消声器,电解槽、补水泵、循环泵、氢气压缩机、氯化氢压缩机、风机、循环氢压缩机、锯床、破碎机、筛分机、真空泵、硅芯磨锥机、硅芯钻孔机、包装机、氢气压缩机、氯化氢压缩机、其他各类风机及其他泵类均布置在厂房内。经采取噪声控制措施后,产噪设备排放声级值为60~80dB(A)。 四、固废治理措施 本项目产生的固体废物主要为过滤杂质、废隔膜、氢气纯化废催化剂、氢气纯化废分子筛、氯氢化后除尘废硅粉、废吸附剂、反歧化废树脂催化剂、废石墨头、酸洗废酸、尾气回收过滤废硅粉、氢气吸附废活性炭、废消耗品、含重金属实验废液、含重金属试剂的实验材料清洗废液、废弃样品、污泥、粉尘废气处理废硅粉、废离子交换树脂、废反渗透膜、废机油和生活垃圾。 氢气制备过程过滤杂质产生量为0.85t/a,主要成分为KOH。根据《国家危险废物名录》(2021版),过滤杂质属危险废物,废物类别为HW35废碱,废物代码261-059-35。全部经置于防渗漏的专用容器内,暂存于生产厂区建设的危废暂存库,交有危险废物资质的单位处置。 电解槽运行一定时期将产生废隔膜,主要成分为KOH、树脂。类比同类多晶硅企业,采用KOH作为电解液制氢产生的废隔膜属于一般工业固废,废物代码900-999-99。废隔膜产生量10t/a,由有资质单位回收利用/处置,不在厂内暂存。 氢气纯化过程脱氧器内将产生废催化剂,主要成分为钯、氧化铝。类比同类制氢企业,氢气纯化采用的废催化剂属于一般工业固废,废物代码900-999-99。废催化剂产生量0.18t/3a,由资质单位回收利用/处置,不在厂内暂存。 氢气纯化过程干燥器内将产生废分子筛,主要成分为硅、铝等。类比同类制氢企业,氢气纯化采用的废分子筛属于一般工业固废,废物代码900-999-99。根据设计资料,废分子筛产生量0.6t/3a,由资质单位回收利用/处置,不在厂内暂存。 氯氢化后的混合气体经旋风分离器和过滤器除尘过程废硅粉产生量为577.94t/a,主要成分为Si、CuCl2。类比同类多晶硅企业,废硅粉属于一般工业固废,废物代码900-999-66。全部采用包装袋收集,暂存于仓库内,外售工业硅企业回收利用。 三氯氢硅精馏提纯过程吸附塔将产生废吸附剂,主要成分为B、P、树脂等。根据《国家危险废物名录》(2021版),废吸附剂属危险废物,废物类别为HW49其他废物,废物代码900-041-49。废吸附剂产生量为1t/a,全部经置于防渗漏的专用容器内,暂存于生产厂区建设的危废暂存库,交有危险废物资质的单位处置。 反歧化过程中在二氯二氢硅反应器内将产生废催化剂,主要成分为SiH2Cl2、SiHCl3、SiCl4、树脂等。根据《国家危险废物名录》(2021版),废催化剂属危险废物,废物类别为HW50废催化剂,废物代码900-048-50。废催化剂产生量10t/a,全部经置于防渗漏的专用容器内,暂存于生产厂区建设的危废暂存库,交有危险废物资质的单位处置。 产品整理过程首先需对U型多晶硅棒两端敲击去除石墨头,主要成分为Si、石墨。类比同类多晶硅企业,废石墨头属于一般工业固废,废物代码900-999-99。废石墨头产生量48t/a,全部采用包装袋收集,暂存于仓库内,由资质单位回收利用或处置。 多晶硅及硅芯酸洗过程废酸产生量为4000t/a,主要成分为HF、HNO3等。根据《国家危险废物名录》(2021版),酸洗废酸属危险废物,废物类别为HW34废酸,废物代码900-300-34。全部经置于防渗漏的1个50m3专用废酸储罐内,定期交有危险废物资质的单位处置。 尾气回收过滤过程废硅粉产生量为86.59t/a,主要成分为Si。类比同类多晶硅企业,废硅粉属于一般工业固废,废物代码900-999-66。全部采用包装袋收集,暂存于仓库内,外售工业硅企业回收利用。 尾气回收得到H2经换热后进入氢气吸附塔,氢气吸附塔采用活性炭填料,因此会产生废活性炭,主要成分为C,因吸附或沾染部分HCl、SiH2Cl2、SiHCl3、SiCl4,根据《国家危险废物名录》(2021版),属危险废物,废物类别为HW49其他废物,废物代码900-041-49。废活性炭产生量16.90t/a,仅检修报废时产生。全部经置于防渗漏的专用容器内,检修产生后交有危险废物资质的单位处置。 抽样检测过程会产生废消耗品,主要为口罩、手套、防护服等;含重金属实验废液,主要成分为铬、银、铅、镍、镉、砷;含重金属试剂的实验材料清洗废液,主要成分为铬、银、铅、镍、镉、砷。根据《国家危险废物名录》(2021版),检测过程产生的废消耗品、含重金属实验废液、含重金属试剂的实验材料清洗废液均属危险废物,废物类别为HW49 其他废物,废物代码900-047-49。废消耗品产生量为0.50t/a,含重金属实验废液产生量为2t/a,含重金属试剂的实验材料清洗废液10t/a,全部经置于防渗漏的专用容器内,暂存于危废暂存间,交有危险废物资质的单位处置。 抽样检测过程会产生废弃样品,主要为未参与试验检测的废多晶硅,属于一般工业固废,废物代码900-999-99。废多晶硅产生量为1.20t/a,全部采用包装袋收集,暂存于仓库内,外售工业硅企业回收利用。 ****处理站运行过程会产生一定量的污泥,主要成分为CaSiO3、CaF2、Cu、Si及含Al、Fe的絮凝剂。污泥产生量4000t/a。本项目工业生产废水仅通过物化方式处理,我公司已将污泥成分送至有危险废物鉴定资质的单位进行鉴定,按照《危险废物鉴别技术规范》(HJ/T298)、《危险废物鉴别标准》(GB5085.1~6)等国家规定的危险废物鉴别标准和鉴别方法鉴定出该污泥属于一般固体废物。 MVR产生的杂盐验收阶段未产出,达产后产生量约5000t/a,鉴定正在进行中。因此,暂按危险废物从严管理,放置于危废暂存间。在本项目正式运营后,企业需按照《危险废物鉴别技术规范》(HJ/T298)、《危险废物鉴别标准》(GB5085.1~6)等国家规定的危险废物鉴别标准和鉴别方法予以认定判定。 含硅粉尘处理废气处理过程废硅粉产生量为35.46t/a,主要成分为Si。类比同类多晶硅企业,废硅粉属于一般工业固废,废物代码900-999-66。全部采用包装袋收集,暂存于仓库内,外售工业硅企业回收利用。 脱盐水和高纯水制备过程将产生废离子交换树脂主要成分为树脂,废反渗透膜主要成分为醋酸纤维素、聚酰胺。类比同类企业,废离子交换树脂和废反渗透膜均属于一般工业固废,废物代码900-999-66。废离子交换树脂产生量0.30t/a,废反渗透膜产生量0.40t/a,均由资质单位回收利用/处置,不在厂内暂存。 日常检修、维护过程将产生废机油。根据《国家危险废物名录》(2021版),废机油属危险废物,废物类别为HW08废矿物油与含矿物油废物,废物代码900-214-08。废机油产生量8.60t/a,全部经置于防渗漏的专用容器内,送主厂区危废暂存间贮存,交有危险废物资质的单位处置。 本劳动定员为400人,生活垃圾产生量为105.60t/a。本项目办公生活区、生产区指定地点设置垃圾箱,由当地环卫部门定期清运。 |
变更情况1 环评建设内容:采用负压引风,将切割粉尘、破碎粉尘、筛分粉尘引入密闭废气管道送整理车间粉尘处理系统,经1台袋式除尘器处理,通过1根15m高排气筒排放 实际建设情况:产品整理废气排放口(DA005)取消,气体不排放,返回系统循环空调风使用 变更原因:整体洁净厂房,杜绝产品污染;减少污染外排。 变更情况2 环评建设内容:生产厂区内建1****处理站,钢混结构,占地面积4000 m2,采用中和+二级化学沉淀+超滤工艺,经处理后废水****处理厂 实际建设情况: 变更原因:生产厂区内建1****处理站,钢混结构,占地面积4000m2,内部设置2套废水处理装置: ⑴高盐水采用预处理(中和+化学沉淀)+MVR蒸发处理工艺,处理后废水不外排; ⑵低盐废水采用“中和+絮凝沉淀+膜处理(二期建设)”处理工艺,处理后废水****处理厂。 变更情况3 环评建设内容:生产厂区建1座260m2的危废暂存间 实际建设情况:生产厂区建2座危废暂存间,面积为39m2×2 变更原因:厂区面积较小,减少贮存量 变更情况4 环评建设内容:酸洗废酸置于防渗漏的专用容器内,暂存于生产厂区建设的危废暂存库 实际建设情况:生产区805装置内,**1个废酸储罐,并设置围堰、防腐等措施 变更原因:减少液体危险废物的转运 | 是否属于重大变动:|
其他
一、地下水污染防控: 1 源头控制 (1)禁止任何废水排入地下水中。 (2)将现有的厂房采取整体分区防渗,全厂根据不同区域潜在的地下水污染风险性大小划分为:重点污染防渗区、一般污染防渗区和简单污染防渗区。 (3)在拟建位置可能发生泄漏的装置上下游布设地下水污染跟踪监测井,进行地下水污染监测,发现泄漏及时切断泄露源,减小向地下水中的泄露时间和泄露量。 (4)厂区液体输送管网和污水输送管网应采用明管敷设,并置于管廊。 (5)雨污分流,将污染区初期雨水与非污染区雨水(含污染区后期雨水)分别收集,分开处理。 2、 防渗区域划分及技术要求 为防止废水的跑、冒、滴、漏以及原料、危险废物等物料产生渗滤液污染土壤和地下水,本评价依据《环境影响评价技术导则》(HJ610-2016),提出采取地下水分区防渗措施。本项目分三个防渗区域,分别为重点防渗区、一般防渗区、简单防渗区。 (1)重点防渗区 重点防渗区主要为制氢车间、盐酸解析车间、冷氢化车间、精馏车间、气体回收车间、特气生产车间、还原车间、整理车间、生产区库房、变电站、危废暂存库、危废暂存间等。防渗要求达到厚度不小于6m,渗透系数不大于1×10-7cm/s的等效黏土防渗层;或参照《危险废物填埋污染控制标准》(GB 18598-2019)中采用铺设2mm**度聚乙烯膜防渗,渗透系数小于等于10-10cm/s。 (2)一般防渗区 一****分站、脱盐水站、多功能物质库、实验楼等。防渗要求达到厚度不小于1.5m,渗透系数小于1×10-7cm/s的等效黏土层的防渗效果。 (3)简单防渗区 简单防渗区为综合楼、餐厅、中央控制室、值班宿舍、活动室及绿化以外的其他区域,采取防渗混凝土做一般地面硬化。 二、环境风险防范 1、事故废水 (1)事故废水三级防控措施 按****集团公司企业标准《事故状态下水体污染的预防与控制技术要求》(Q/SY1190-2009)要求,本项目设置环境风险事故水污染防控三级防控系统,防止环境风险事故造成水污染。 第一级防控系统由装置区围堰、罐区防火堤和区内事故水池组成,收集一般事故泄漏的物料,防止轻微事故泄漏造成的水环境污染;装置区围堰高度不小于15cm,宽度不超过150mm围堰和导流设施,并设置清污、雨污切换系统;在罐区界区设置防火堤,防火堤内设置混凝土地坪并作防腐防渗处理,防火堤外设置切换阀门。一级防控措施构筑生产过程中环境安全第一层防控网,在轻微事故时利用围堤控制泄漏物料的转移,防止泄漏物料及事故废水外排造成污染。罐区围堤高度固定顶罐不应小于罐组内1个最大储罐的容积。 第二级防控系统由装置区、罐区雨水收集池组成,将较大生产事故泄漏于装置区围堤、罐区围堤外的物料或水通过雨水收集池收集,回收物****处理站****园区污水处理厂处理,防止较大生产事故泄漏物料和污染消防水造成的环境污染;事故后清洗雨水收集池,清洗水****处理站处理。 第三级防控系统为污水处理前的污水收集与储存池。作为事故状态下的储存与调控手段,防止重大事故泄漏物料和污染消防水造成的环境污染。 发生重大的火灾、爆炸事故时,消防水及其携带的物料通过第一级、第二级防控系统进入第三级防控系统,之后****处理站处理。 事故处理完毕后,重点清洗污水收集与储存池,清****处理站处理。 2、环境风险应急预案 制定环境应急预案并定期演练,严格落实报告提出的防护措施,建立完善环境风险防范体系。 | 实际建设情况:一、地下水污染防控: (一)地下水污染控制措施 1车间地面防渗 ⑴地面混凝土浇筑 车间地面浇筑用混凝土中水泥强度不低于32.5MPa,强度满足《普通混凝土力学性能试验方法标准》(GB/T50081-2002)有关规定,含泥量、粗细骨料等均满足《地下工程防水技术规范》(GB50108-2008)相关要求,基层混凝土水灰比控制在0.50以下,强度达到C25以上,混凝土配合比设计对泌水有所控制,整体浇筑采用高强度水泥或早强型水泥,采用低水灰比的干硬性混凝土,掺加混凝土外加剂和掺和料,混凝土整体抗渗等级整体为P10、P8,渗透系数小于10-10cm/s。 ⑵地面防渗材料 氢化装置:地面防水/防腐采用1.5mm厚聚氨酯涂层、40mm厚花岗岩板并使用环氧胶泥做结合层的施工做法。 清理基层→涂刷底层涂料(特殊部位进行处理)→防水层施工→待固化→弹线→标高控制点→洒水湿润→环氧胶泥材料配→铺环氧胶泥结合层→排版试铺→铺花岗岩面板并调整→勾缝→清洗、成品保护。 罐区:地面采用大面积混凝土振桥振捣,依据侧模标高和弹设在墙体上的水平控制线,达到振捣密实、上表面整平、布满原浆且粗骨料被挤压沉实到混凝土中下部为止。根据设计要求耐磨地面采用200mm厚C20混凝土随打随压光,面层为耐磨面层,采用通用性防水材料,通用性的新型聚合物水泥基防水材料是由丙烯酸乳液和助剂组成的液料与由特种水泥、级配砂及特殊矿物质粉末组成的粉料按特定比例组合而成双组份防水材料,防水等级较高,车间地面整体渗透系数小于10-10cm/s。 化学品库/危废暂存间:地面防水采用单层1.5mm厚聚氨酯防水涂料+50mmC30抗渗混凝土+2mm环氧砂浆施工的做法。 精馏、尾气回收:围堰、排水沟、集水坑、地坪垫层抗渗隔离层采用1.5mm厚聚氨酯防水涂料做法;地坑防水采用20mm厚防水砂浆+1mm厚水泥基渗透结晶型防水涂料做法。 整理装置:采用1.5mm厚聚氨酯防水涂料+耐酸砖环氧胶泥铺彻灌缝防腐做法。 (二)事故水池防渗 ****处理站主体工程由中化二建承建,******公司实施监理。****公司施工组织报告,工程监理单位编制的工程监理资料等了解项目建设情况,水处理工程于2023年2月18日开工建设,2023年5月进行调试,2024年6月进行试生产。厂区污水处理工程建设时间与主体工程同步建设,同步试运行,严格执行了“三同时”制度。 池体构筑物主要施工工序:基坑开挖验槽→卵石、碎石垫层→基础垫层→混凝土垫层→池底板→池壁→池顶板→池周围土方回填→池内壁水泥砂浆→装修→钢梯栏杆。 各构筑物采用防水砼,砼强度等级为C35,抗渗标号为P8,掺一定比例的混凝土外加剂,提高砼的防渗抗裂性能。 1、池底 垫层用混凝土由冀****公司,垫层使用10公分厚标号为C20的混凝土浇筑完成,混凝土试块在荷载值441.4KN下,抗压强度达到19.6Mpa,垫层试样由施工单位送至至**自****研究院,经检测混凝土抗渗强度符合GBJ82-1985、JGJ55-2000、GB5009-2002标准,实验抗渗等级P8,满足防渗要求。混凝土配比为水泥:沙子:石子:水=1:2.56:3.84:0.71,抗压强度达到13.6MPa,符合标准JGJ55-2000,满足水体构筑物抗压标准。 池底板使用70公分厚标号为C30的混凝土浇筑完成,混凝土试样由施工单位送至至**自****研究院,经检测混凝土抗渗强度符合GBJ82-1985、JGJ55-2000、GB5009-2002标准,实验抗渗达到P8, 满足防渗要求。。 2、池壁 水池壁使用标号为C35的混凝土一体浇注完成,浇筑厚度450mm。池内壁表面及外露部分用1:2防水砂浆分层抹面,防水砂浆内掺5%防水剂。 2023年5月,建设单位联合施工单位、监理单位进行池体试水实验,试水时间72h。池内首先灌至1/3高水位,经24h试水后,未发现渗漏现象,后灌至2/3高水位,24h试水后,再灌满全池,均未发现渗漏现象。。 (三)管道防泄漏措施 管****处理站,生产废水通过管道输送至污水站废水处理系统,将压力表安装在给水入口处,并将其他立管接口处封堵,开始向管内注水,待管道充满水后,开始缓慢加压,压力升至0.4Mpa时,管道及接口处未发现渗漏,继续加压至0.6Mpa时,停止加压,稳压1h,压力下降0.02Mpa,然后泄压入口表压力为0.46Mpa,观察2h,入口处表压力为0.445Mpa,压降值为0.005Mpa,检查管道及各个连接处,不渗不漏,压力试验合格。 (四)化粪池防渗 水泥砂浆施工工艺流程:地板、池壁基层处理→冲洗湿润→刷素水泥→抹底层砂浆→素水泥浆→抹面层砂浆→抹水泥砂浆→养护。 化粪池所用的砌体为普通烧结砖,强度MU10。水泥砂浆为普通硅酸盐水泥,水泥等级为为32.5,由水泥砂浆采用分层涂抹,涂抹后压实,抹平并进行表面压光。水泥砂浆涂抹完成后进行湿养,养护时间为15天。 (五)罐区地面防渗 砂浆车间地面采用大面积混凝土采用振桥振捣,依据侧模标高和弹设在墙体上的水平控制线,达到振捣密实、上表面整平、布满原浆且粗骨料被挤压沉实到混凝土中下部为止。根据设计要求耐磨地面采用200mm厚C20混凝土随打随压光,面层为耐磨面层,采用通用性防水材料,通用性的新型聚合物水泥基防水材料是由丙烯酸乳液和助剂组成的液料与由特种水泥、级配砂及特殊矿物质粉末组成的粉料按特定比例组合而成双组份防水材料,防水等级较高,车间地面整体渗透系数小于10-10cm/s。 (六)危废暂存间防渗及废酸储罐 1.危废暂存间 地面防水采用单层1.5mm厚聚氨酯防水涂料+50mmC30抗渗混凝土+2mm环氧砂浆施工的做法,然后做2-4mm厚环氧树脂防腐,库内设30cm高墙裙作为围堰。,在地面与围堰施工过程注意地面与墙体接缝处的严密衔接(均采取防渗措施,保证防渗渗透系数≤10-10cm/s)。危废暂存间(液)设置围堰和2个积液坑,将其分隔成2个贮存区域,分别存放废酸、废油。地面设置1%坡度,确保2个区域的废液分别流向各自的积液坑。积液坑尺寸为0.6×0.6×0.6m,积液坑粘贴防腐砖,并铺填干砂用于吸收泄漏的液体。 2.废酸储罐 805整理装置一楼设置酸洗废酸储罐1个(50m3),酸洗工段产生的废酸不再送危废暂存间,由管道送至废酸储罐,废酸储罐周边设置设置围堰、导流槽、收集池,底部采用抗渗混凝土浇筑后,表面粘贴耐酸砖,放置废酸储罐的车间外部设置地埋式截流槽。 (七)地下水监测井建设情况 厂区范围内设置三口地下水监测井,地下水监测井孔径210mm,井径110mm,井深15.5m。管材为pvc-u,按照《地下水监测井建设规范》(DZ/T0270-2014)和《地下水环境监测技术规范》(HJ 164-2020)要求开展施工。 二、环境风险防范 (一)风险防范措施 1、事故性废水排放风险整体防范措施 ⑴本项目事故性废水排放环境污染三级防控体系 为防止发生物料泄漏等风险事故时,泄漏物料以及事故废水外排对周围环境产生影响,本项目在生产厂区设置事故废水环境污染三级防控体系:一级防控措施将污染物控制在生产车间、装置区、罐区;二级防控措施将污染物控制在排水系统事故应急池;三级防控措施将污染物控制在厂内,确保生产非正常状态下不发生污染事件。本项目的事故废水环境污染三级防控措施具体如下: 一级防控措施(围堰) 第一级防控系统由装置区围堰、罐区围堤和区内污水收集池组成,收集一般事故泄漏的物料,防止轻微事故泄漏造成的水环境污染;装置区设置围堰高度1.5m,配套导流设施,并设置清污、雨污切换系统;在罐区界区设置围堰,围堰内设置混凝土地坪,围堰外设置切换阀门。一级防控措施构筑生产过程中环境安全第一层防控网,在轻微事故时利用围堤控制泄漏物料的转移,防止泄漏物料及事故废水外排造成污染。 二级防控措施(事故应急池) 当发生较大事故,无法利用装置和罐区围堰控制泄漏物料和事故废水时,本项目设置厂内事故应急池做为二级防控措施,切断污染物与外部的通道,把泄漏物料和事故废水导入事故应急池,将污染控制在厂内,防止较大生产事故时泄漏物料和污染消防水外排造成污染。 ⑵事故废水及泄漏物料收集处理措施 厂区设置事故排污管道,在生产装置和罐区围堰外设置切换阀门。轻微事故时把泄漏物料和事故消防水经污水管道导入厂区污水处理系统处理;较大或重大事故时,利用排污管道作为转输系统,将生产装置和罐区围堰收集的事故消防废水、可能受污染的雨水和事故泄漏物料导入事故池。 事故状态下本工程收集的事故消防废水、可能受污染的雨水和事故泄漏物料全部进入事故池暂时存放,然后分批次委托有资质的单位安全处置;一旦发生较大或重大事故时,各生产车间将立即停产,不再产生各类生产废水等,减少事故水量。 2、事故水池 消防废水的转移:当某一物料储罐发生泄漏或火灾的情况下,通过高压泵将泡沫喷到泄漏储罐上;同时启动冷却水自动喷淋系统,消防栓对周围罐体进行降温,这时产生的消防废水主要为消防泡沫和冷却喷淋废水。消防废水首先贮存在围堰内;事故状态结束后,围堰内的消防水逐渐转移至事故池。 前期雨水的储存:本项目的前期雨水主要指生产车间、储罐区和三废处理区域的前期雨水,即在降雨前15分钟所产生的雨水,通过车间、罐区和污水处理区设置的围堰收集后,导入厂区设置的3个初期雨水收集池,随后通过各自配备的水泵送至污水站再处理。 厂区内建设有有效容积4000m3事故水池1座,工艺装置区事故排放的污水由废水管道收集后暂存于事故水池,事故水池底由下至上依次为素土夯实+250mm砂夹石+100公分厚标号为C20混凝土作为垫层+池底板使用100公分厚标号为C35的混凝土作为池底板+厚度450mm的C35的混凝土一体浇注池壁,池内壁表面及外露部分用1:2防水砂浆分层抹面,防水砂浆内掺5%防水剂。,实验抗渗等级P8,防渗效果能够满足渗透系数小于1.0×10-10cm/s。 3、罐区围堰 参照《石油化工企业设计防火规范》(GB50160-2008)第5.3.7条低温常压储罐应设围堰,各有毒有害物料储存区必须设置隔水围堰。项目按照储存物质性质对储罐区储罐进行分区分格,储罐区主要为原料储罐区,仅有1个储罐为四氯化硅储罐,设置单独的围堰;其余7个储罐均为三氯氢硅储罐,整体设置1个围堰。围堰西侧和东侧各设置2个排污阀和1个水封井,通过管道送入初期雨水池。防止污染介质外流扩散造成水体、土壤的大面积环境污染。 4、危废暂存间风险防范 危废暂存间(液)设置围堰和2个积液坑,将其分隔成2个贮存区域,分别存放废酸、废油。地面设置1%坡度,确保2个区域的废液分别流向各自的积液坑。积液坑尺寸为0.6×0.6×0.6m,积液坑粘贴防腐砖,并铺填干砂用于吸收泄漏的液体。四周墙壁设置30cm高的墙裙,墙裙与地面自流平采取防渗措施,保证防渗渗透系数≤10-10cm/s。 5、应急预案 根据《中华人民**国环境保护法》、《企业事业单位突发环境事件应急预案备案管理办法》、《突发环境事件应急管理办法》等法律、法规有关规定,建立健全环境安全应急体系,确保在发生突发环境事件时,各项应急工作能够高效有序地快速启动,避免和最大限度地减轻突发环境事件对环境造成的损失和危害,结合公司实际情况,制定了《****突发环境事件应急预案》,并在当地环境保护主管部门取得备案文件。 (二)排污口规范化、监测设施及在线装置 1.废气排污口规范化要求 按照《固定源废气监测技术规范》(HJ/T 397-2007)在排气筒位置设置了采样口,并按照要求搭建了采样平台。 2.废水排放口 生产区及生活区废水排放口均设置了取样点,并按照规定设置了警示标牌。 (三)污染源在线监测 ****工业废水排口水污染源在线监测系统于2024年7月22日安装完成,****公司**哈富****公司进行在线设备的安装、调试检测及验收工作。 2024年8月14日完成漂移、示值误差等调试检测; 2024年9月10日完成720小时无故障运行调试; 2024年9月13日完成验收比对监测; 2024年9月26日邀请专家成立8人验收组对工业废水排口在线监测系统进行验收。设备的安装、调试、比对等均符合《水污染源在线监测系统安装技术规范》(HJ353-2019)和《水污染源在线监测系统验收技术规范》(HJ354-2019)中要求。验收结论为通过。验收资料已装订成册并提交环保部门备案。 |
\ | 是否属于重大变动:|
3、污染物排放量
0 | 642.08 | 0 | 0 | 0 | 642.08 | 642.08 | |
0 | 111 | 0 | 0 | 0 | 111 | 111 | |
0 | 11 | 0 | 0 | 0 | 11 | 11 | |
0 | 0 | 0 | 0 | 0 | 0 | 0 | |
0 | 0 | 0 | 0 | 0 | 0 | 0 | |
0 | 15347.2 | 0 | 0 | 0 | 15347.2 | 15347.2 | / |
0 | 0 | 0 | 0 | 0 | 0 | 0 | / |
0 | 6.43 | 0 | 0 | 0 | 6.43 | 6.43 | / |
0 | 0 | 0 | 0 | 0 | 0 | 0 | / |
0 | 0 | 0 | 0 | 0 | 0 | 0 | / |
4、环境保护设施落实情况
表1 水污染治理设施
1 | 生产区废水排放口 | 《污水综合排放标准》(GB 8978-1996)表4三级标准;****处理厂纳管水质要求 | 生产过程产生低盐废水及高盐废水,装置产生的酸性废水及其他低盐废水通过加石灰乳中和、换热后,满足排放标准进入废水外排水池,通过市政管网****处理厂。装置高盐废水进入本系统高盐水高效沉淀池,在澄清池中投加化学药剂充分反应后经过斜板澄清池进入中间水池,再去往气浮池和多介质过滤器等过滤措施进行固液分离,高盐水预处理清液去往浓盐水蒸发结晶系统。 | 验收期间废水出水pH值范围为7.4~7.9,其他监测因子最高浓度分别为CODcr 94mg/L、BOD5 23.5mg/L、总磷 0.5mg/L、总氮21.9mg/L、氨氮 9.11mg/L、SS 48mg/L、氟化物 1.41mg/L、石油类0.35mg/L,以上污染物排放浓度均满足《污水综合排放标准》(GB 8978-1996)表4三级标准,同时需****处理厂纳管水质要求。 | |
2 | 生活区污水排放口 | 《污水综合排放标准》(GB 8978-1996)表4三级标准,同时需****处理厂纳管水质要求。 | 化粪池 | 验收期间废水出水pH值范围为7.0~7.9,其他监测因子最高浓度分别为CODcr 117mg/L、BOD5 52.7mg/L、总磷0.62mg/L、总氮22.7mg/L、氨氮9.28 mg/L、SS 59 mg/L,以上污染物排放浓度均满足《污水综合排放标准》(GB 8978-1996)表4三级标准,同时需****处理厂纳管水质要求。 |
表2 大气污染治理设施
1 | 工艺废气及储罐呼吸废气排气筒 | 《大气污染物综合排放标准》(GB 16297-1996) | 三级碱液喷淋塔(1用2备) | HCl最高排放速率4.15×10-3kg/h、最高排放浓度1.6mg/m3,颗粒物最高排放速率9.44×10-3kg/h、最高排放浓度3.6mg/m3,监测值均低于《大气污染物综合排放标准》(GB 16297-1996)表2 HCl最高允许排放速率(40m)2.6kg/h及最高允许排放浓度100mg/m3限值要求,颗粒物最高允许排放速率(40m)39kg/h及最高允许排放浓度120mg/m3限值要求。 | |
2 | 酸洗废气排放口 | 《大气污染物综合排放标准》(GB 16297-1996) | 四级串联碱喷淋塔处理,通过1根35m高排气筒排放。 | 氟化物最高排放速率7.79×10-3kg/h、最高排放浓度0.28~0.41mg/m3,NOx最高排放速率0.812kg/h、最高排放浓度43mg/m3,监测值均低于《大气污染物综合排放标准》(GB 16297-1996)表2氟化物最高允许排放速率(35m)0.795kg/h及最高允许排放浓度9mg/m3,NOx最高允许排放速率(35m)5.95kg/h及最高允许排放浓度240mg/m3限值要求。 | |
3 | 实验室抽样检测废气排放口 | 《大气污染物综合排放标准》(GB 16297-1996) | 1套碱喷淋吸收塔+活性炭处理,再通过楼顶设置的1根35m高排气筒 | 颗粒物最高排放速率0.024kg/h、最高排放浓度3.1mg/m3,HCl最高排放速率7.84×10-3kg/h、最高排放浓度1.0mg/m3,NOx最高排放速率0.364kg/h、最高排放浓度44mg/m3,氟化物最高排放速率2.88×10-3kg/h、最高排放浓度0.35mg/m3,以上污染物监测值均低于《大气污染物综合排放标准》(GB 16297-1996)表2 颗粒物最高允许排放速率(35m)31kg/h及最高允许排放浓度120mg/m3,HCl最高允许排放速率(35m)2kg/h及最高允许排放浓度100mg/m3、NOx最高允许排放速率(35m)5.95kg/h及最高允许排放浓度240mg/m3,氟化物最高允许排放速率(35m)0.795kg/h及最高允许排放浓度9mg/m3限值要求。 | |
4 | 原料制备废气排放口 | 《大气污染物综合排放标准》(GB 16297-1996) | 经1台袋式除尘器处理,通过1根43m高排气筒排放。 | 颗粒物最高排放速率1.94×10-3kg/h、最高排放浓度4.6mg/m3,监测值均低于《大气污染物综合排放标准》(GB 16297-1996)表2颗粒物最高允许排放速率(43m)48kg/h及最高允许排放浓度120mg/m3限值要求。 | |
5 | 食堂油烟 | 《饮食业油烟排放标准》(试行)(GB 18483- 2001)大型食堂 | 设置1套油烟净化装置 | 食堂油烟净化装置出口油烟最高排放浓度为0.9mg/m3,浓度满足《饮食业油烟排放标准》(试行)(GB 18483- 2001)大型食堂油烟最高允许排放浓度2mg/m3限值要求。 |
表3 噪声治理设施
1 | 风机 水泵等 | 《工业企业厂界环境噪声排放标准》(GB12348-2008) | 高噪声设备放置于混凝土基座减振降噪措施。 | 验收期间厂界西北侧昼间最大噪声值为50.6dB(A),夜间45.4dB(A),监测结果均低于《工业企业厂界环境噪声排放标准》(GB12348-2008)厂界外声环境功能区类别3类标准昼间65dB(A),夜间55dB(A)限值要求,道路一侧厂界(东、南侧)昼间最大噪声值55.7dB(A),夜间47.8dB(A),监测结果均低于《工业企业厂界环境噪声排放标准》(GB12348-2008)厂界外声环境功能区类别4类标准昼间70dB(A),夜间55dB(A)限值要求。 |
表4 地下水污染治理设施
1 | 1 源头控制 (1)禁止任何废水排入地下水中。 (2)将现有的厂房采取整体分区防渗,全厂根据不同区域潜在的地下水污染风险性大小划分为:重点污染防渗区、一般污染防渗区和简单污染防渗区。 (3)在拟建位置可能发生泄漏的装置上下游布设地下水污染跟踪监测井,进行地下水污染监测,发现泄漏及时切断泄露源,减小向地下水中的泄露时间和泄露量。 (4)厂区液体输送管网和污水输送管网应采用明管敷设,并置于管廊。 (5)雨污分流,将污染区初期雨水与非污染区雨水(含污染区后期雨水)分别收集,分开处理。 2、 防渗区域划分及技术要求 为防止废水的跑、冒、滴、漏以及原料、危险废物等物料产生渗滤液污染土壤和地下水,本评价依据《环境影响评价技术导则》(HJ610-2016),提出采取地下水分区防渗措施。本项目分三个防渗区域,分别为重点防渗区、一般防渗区、简单防渗区。 (1)重点防渗区 重点防渗区主要为制氢车间、盐酸解析车间、冷氢化车间、精馏车间、气体回收车间、特气生产车间、还原车间、整理车间、生产区库房、变电站、危废暂存库、危废暂存间等。防渗要求达到厚度不小于6m,渗透系数不大于1×10-7cm/s的等效黏土防渗层;或参照《危险废物填埋污染控制标准》(GB 18598-2019)中采用铺设2mm**度聚乙烯膜防渗,渗透系数小于等于10-10cm/s。 (2)一般防渗区 一****分站、脱盐水站、多功能物质库、实验楼等。防渗要求达到厚度不小于1.5m,渗透系数小于1×10-7cm/s的等效黏土层的防渗效果。 (3)简单防渗区 简单防渗区为综合楼、餐厅、中央控制室、值班宿舍、活动室及绿化以外的其他区域,采取防渗混凝土做一般地面硬化。 | 化学品库/危废暂存间:地面防水采用单层1.5mm厚聚氨酯防水涂料+50mmC30抗渗混凝土+2mm环氧砂浆施工的做法,渗透系数小于10-10cm/s;事故水池等水工构筑物池底板使用70公分厚标号为C30的混凝土浇筑完成,混凝土试样由施工单位送至至**自****研究院,经检测混凝土抗渗强度符合GBJ82-1985、JGJ55-2000、GB5009-2002标准,实验抗渗达到P8,渗透系数小于10-10cm/s。 |
表5 固废治理设施
1 | 加强固废管理理,优先进行综合利用,不可利用的固废须合理处置。废硅粉、废石墨头、废实验样品外运综合利用;电解槽废隔膜、氢气纯化产生的废催化剂和废分子筛、脱盐水纯水制备产生的废树脂和废反渗透膜、制氮产生的废分子筛等由厂家更换回收;生活垃圾由环卫部门处置;污水处理站污泥按照相关规定进行固废属性鉴别,若属于危险废物则交有资质单位转运处置,若属于一般固废则运至指定地点填埋处置;:制氢过滤杂质、解析残渣、废酸、废吸附剂、釜底残渣、反歧化废催化剂、废活性炭、实验废物、含重金属的实验废液及清洗废水、废机油等危险废物分类暂存于厂区危废暂存库,交有资质的单位转运处置。项目须在厂区内配套建设足够容量的一般固废临时贮存库和危险废物临时贮存库,严格按照《一般工业固体废物贮存、处置场污染控制标准》(GB18599-2020)和《危险废物贮存污染控制标准》(GB18597-2001)及修改单要求进行管理。 | 4.固废 (1)一般工业固废 电解制氢装置电解槽废隔膜、氢气纯化装置废催化剂及废分子筛、产品整理废石墨头、脱盐及高纯水装置产生的废离子交换树脂及废反渗透膜等由厂家回收或委外处置;废气回收过滤装置的废硅粉、抽样检测废弃样品、除尘器收集的废硅粉等外售工业硅企业回收利用;污水处理装置污泥经压****填埋场处理 (2)危险废物 电解制氢装置碱液过滤器过滤杂质、吸附塔废吸附剂、二氯二氢硅反应器废催化剂、酸洗机酸洗废液、氢气吸附法废活性炭、抽样检测废消耗品实验废液 实验材料清洗废液、废机油等属于危险废物,交由有资质单位回收。蒸发装置产生的杂盐未进行属性鉴定,暂按危险废物管理。 ⑶生活垃圾 统一交由环卫部门处置。 |
表6 生态保护设施
1 | 厂区绿化充分贯彻因地制宜、有利生产、保障安全、美化环境、节约用地、经济合理的原则,根据厂区的总图布置、生产特点、管网布局、消防安全、环境特征,以及当地的土壤情况、气候条件、植物习性等因素,合理选择抗污、净化、减噪或滞尘能力强的绿化植物。 | 生产区由于防火要求,均进行地面硬化或铺设石子,不设置绿化,仅在事故水池处进行绿化,绿化面积约930m2。 |
表7 风险设施
1 | 1、事故废水 (1)事故废水三级防控措施 按****集团公司企业标准《事故状态下水体污染的预防与控制技术要求》(Q/SY1190-2009)要求,本项目设置环境风险事故水污染防控三级防控系统,防止环境风险事故造成水污染。 第一级防控系统由装置区围堰、罐区防火堤和区内事故水池组成,收集一般事故泄漏的物料,防止轻微事故泄漏造成的水环境污染;装置区围堰高度不小于15cm,宽度不超过150mm围堰和导流设施,并设置清污、雨污切换系统;在罐区界区设置防火堤,防火堤内设置混凝土地坪并作防腐防渗处理,防火堤外设置切换阀门。一级防控措施构筑生产过程中环境安全第一层防控网,在轻微事故时利用围堤控制泄漏物料的转移,防止泄漏物料及事故废水外排造成污染。罐区围堤高度固定顶罐不应小于罐组内1个最大储罐的容积。 第二级防控系统由装置区、罐区雨水收集池组成,将较大生产事故泄漏于装置区围堤、罐区围堤外的物料或水通过雨水收集池收集,回收物****处理站****园区污水处理厂处理,防止较大生产事故泄漏物料和污染消防水造成的环境污染;事故后清洗雨水收集池,清洗水****处理站处理。 第三级防控系统为污水处理前的污水收集与储存池。作为事故状态下的储存与调控手段,防止重大事故泄漏物料和污染消防水造成的环境污染。 发生重大的火灾、爆炸事故时,消防水及其携带的物料通过第一级、第二级防控系统进入第三级防控系统,之后****处理站处理。 事故处理完毕后,重点清洗污水收集与储存池,清****处理站处理。 2、环境风险应急预案 制定环境应急预案并定期演练,严格落实报告提出的防护措施,建立完善环境风险防范体系。 | 1、事故废水 (1)事故废水三级防控措施 按****集团公司企业标准《事故状态下水体污染的预防与控制技术要求》(Q/SY1190-2009)要求,本项目设置环境风险事故水污染防控三级防控系统,防止环境风险事故造成水污染。 第一级防控系统由装置区围堰、罐区防火堤和区内事故水池组成,收集一般事故泄漏的物料,防止轻微事故泄漏造成的水环境污染;装置区围堰高度不小于15cm,宽度不超过150mm围堰和导流设施,并设置清污、雨污切换系统;在罐区界区设置防火堤,防火堤内设置混凝土地坪并作防腐防渗处理,防火堤外设置切换阀门。一级防控措施构筑生产过程中环境安全第一层防控网,在轻微事故时利用围堤控制泄漏物料的转移,防止泄漏物料及事故废水外排造成污染。罐区围堤高度固定顶罐不应小于罐组内1个最大储罐的容积。 第二级防控系统由装置区、罐区雨水收集池组成,将较大生产事故泄漏于装置区围堤、罐区围堤外的物料或水通过雨水收集池收集,回收物****处理站****园区污水处理厂处理,防止较大生产事故泄漏物料和污染消防水造成的环境污染;事故后清洗雨水收集池,清洗水****处理站处理。 第三级防控系统为污水处理前的污水收集与储存池。作为事故状态下的储存与调控手段,防止重大事故泄漏物料和污染消防水造成的环境污染。 发生重大的火灾、爆炸事故时,消防水及其携带的物料通过第一级、第二级防控系统进入第三级防控系统,之后****处理站处理。 事故处理完毕后,重点清洗污水收集与储存池,清****处理站处理。 2、环境风险应急预案 制定环境应急预案并定期演练,严格落实报告提出的防护措施,建立完善环境风险防范体系。 |
5、环境保护对策措施落实情况
依托工程
******公司现有厂房及生产设施全部由**市下设的青城国资负责拆除后,交付****使用,不涉及与本项目相关的利旧工程和依托工程。 | 验收阶段落实情况:与环评一致 |
/ |
环保搬迁
\ | 验收阶段落实情况:\ |
/ |
区域削减
\ | 验收阶段落实情况:\ |
/ |
生态恢复、补偿或管理
\ | 验收阶段落实情况:\ |
/ |
功能置换
\ | 验收阶段落实情况:\ |
/ |
其他
\ | 验收阶段落实情况:\ |
/ |
6、工程建设对项目周边环境的影响
/ |
/ |
/ |
/ |
/ |
/ |
7、验收结论
1 | 未按环境影响报告书(表)及其审批部门审批决定要求建设或落实环境保护设施,或者环境保护设施未能与主体工程同时投产使用 |
2 | 污染物排放不符合国家和地方相关标准、环境影响报告书(表)及其审批部门审批决定或者主要污染物总量指标控制要求 |
3 | 环境影响报告书(表)经批准后,该建设项目的性质、规模、地点、采用的生产工艺或者防治污染、防止生态破坏的措施发生重大变动,建设单位未重新报批环境影响报告书(表)或环境影响报告书(表)未经批准 |
4 | 建设过程中造成重大环境污染未治理完成,或者造成重大生态破坏未恢复 |
5 | 纳入排污许可管理的建设项目,无证排污或不按证排污 |
6 | 分期建设、分期投入生产或者使用的建设项目,其环境保护设施防治环境污染和生态破坏的能力不能满足主体工程需要 |
7 | 建设单位因该建设项目违反国家和地方环境保护法律法规受到处罚,被责令改正,尚未改正完成 |
8 | 验收报告的基础资料数据明显不实,内容存在重大缺项、遗漏,或者验收结论不明确、不合理 |
9 | 其他环境保护法律法规规章等规定不得通过环境保护验收 |
不存在上述情况 | |
验收结论 | 合格 |
招标导航更多>>
工程建筑
交通运输
环保绿化
医疗卫生
仪器仪表
水利水电
能源化工
弱电安防
办公文教
通讯电子
机械设备
农林牧渔
市政基建
政府部门
换一批
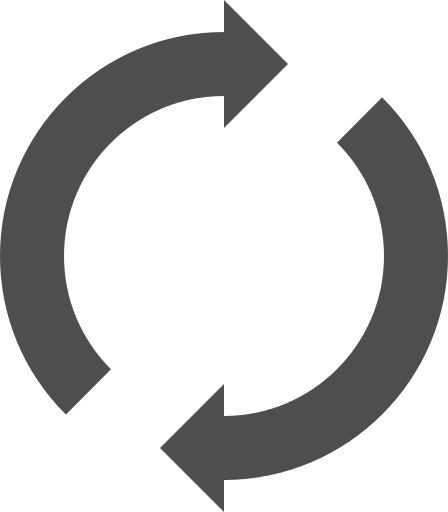