统一信息编码:****
根据生产需要,现寻求一种溶剂型铝合金清洗剂,用于铝合金零件加工过程的表面清洗(清洗剂要求为国产化产品),如有相关产品,需提供供应商资质证明材料、2L样品、产品安全技术说明书、产品指标测试报告(需第三方检测报告)、报价单,资格证明材料、样品、产品安全技术说明书于12月1日前提供, 产品指标测试报告、报价单于12月13日前提供。****公司章。联系人刘莹181****3656
清洗剂使用场景、性能指标及供应商资质要求分别如下:
一、清洗剂使用场景
用于LY12、2024、LF21、2A12等牌号的国产及进口铝合金薄板/型材材料及零件清洗,薄板:LY12规格0.3~7mm,2024规格0.3~6.0mm,2A12规格0.5~5mm,LF21规格规格1.0~5.0mm,型材: XC111-1~XC615-3等L型、T型、Z型等截面型材,清洗适用于以下场景:
1、原材料清洗:
① 薄板原材料薄膜去除后板材在环境中接触的灰尘,搬运过程中的手套残留的油污或者其他脏污。
② 薄板及型材原材料表面自带成排分布的油墨标记,如2024-AMS-QQ-A-250/5板材的红色油墨印记,2024-AMS-QQ-A-250/4浓重的黑色油墨标印,LY12材料及其他2024材料常规的黑色油墨标印。
2、零件加工过程中清洗:
① 加工过程中在零件上用记号笔做的标记;
② 打磨后残留在零件上的铝粉;
③ 模具清洁不到位成形后残留在零件上的灰尘、脏污。
④ 拿放零件的手套不干净沾染的油污(如化猪油、壳牌润滑油等)、脏污、灰尘等。
⑤ 数控设备加工后残留在零件上的切削液(如辛辛那提切削液等)
⑥ 零件放置于环境中的灰尘等。
二、清洗剂性能测试要求
2.1 鉴定试验要求
清洗剂需按表1进行全项目鉴定试验,要求如下:
表1 清洗剂鉴定试验要求
清洗剂类型 | 清洗对象 | 安全环保性能 | 理化性能 | 漆层兼容性能 | |||||||||||||
气味 | 闪点 | 挥发性有机物含量 | 毒性 | 卤素含量 | 重金属含量 | 非挥发残留物 | 铜片腐蚀 | 缝隙腐蚀 | 全浸腐蚀 | 氢脆 腐蚀 | 应力腐蚀 | 镉层腐蚀 | 增氢量 | 漆层软化 | 漆层结合力 | ||
溶剂型 | 金属 | √ | √ | √ | √ | √ | √ | √ | √ | √ | √ | √ | √ | √ | ○ | × | × |
注:“√”为需鉴定的试验项目,“×”为不需鉴定的试验项目。清洗对象不包含钛合金时,“○”可不进行。 |
2.2 供应商鉴定试验
结合清洗剂的类型以及清洗用途,厂家应按照表1试验项目,提供有CMA资质的第三方测试机构出具的报告,具体的试验方法见章节3。
3 安全型清洗剂的鉴定试验及要求
3.1 不同类型的清洗剂需鉴定的试验项目见表1,鉴定内容包括安全环保性能、理化性能、涂层兼容性能和现场使用性能。
3.2 安全环保性能
3.2.1 气味
按ASTM D 1296进行试验,清洗剂的气味应为低或无残留。
3.2.2 闪点
按照GB/T 261进行闪点测试,清洗剂的闪点应不低于60℃。
3.2.3 挥发性有机物含量(VOCs)
按照GB/T 23986进行VOCs测试,清洗剂的VOCs应不高于60 mg/m3。
3.2.4 毒性
清洗剂不应有致癌性,当按照生产商推荐的方法使用时,不应对人体健康产生不良影响。
采用气相色谱/质谱法测试清洗剂中按发性有机化合物的致癌组分,清洗剂中任何致癌组分的质量或体积百分比大于0.1%为有致癌性。
3.2.5 卤素含量
采用IC法(离子色谱分析)测试卤素含量,检测下限10ppm。采用IC法测试用于钛合金热处理的清洗剂,不应检出卤素(F、Cl、Br、I)。如其他特殊专业有要求,按特殊专业要求执行。
3.2.6 重金属含量
使用ICP光谱仪测试重金属铅、镍、镉、汞、砷、六价铬和铬的含量,提供含实测值的报告。
3.3 理化性能
3.3.1 非挥发残留物
准备一个125mL的干净的蒸发皿,在110℃±2℃的烘箱中烘干,并在干燥器中冷却,精确称量。重复该过程,直到两次称量结果的差值在0.1mg之内。向称量好的蒸发皿内加入100mL清洗剂,并加热,待溶液蒸干后,将蒸发皿放回烘箱中,重复110℃±2℃烘干、在干燥器中冷却、精确称量的过程,直到两次称量结果的差值在0.1mg之内。清洗剂溶液蒸干后称得的质量与加入清洗剂前蒸发皿的质量之差即为清洗剂中非挥发性残留物含量。非挥发残留物≤5mg/100mL。
3.3.2 铜片腐蚀
按GB/T 5096进行测试,试验温度为38℃±2℃,试验浸泡时间为24h。铜片腐蚀等级不高于1b 级。
3.3.3 缝隙腐蚀
3.3.3.1 试验材料及溶液
3.3.3.1.1 试验材料采用2024-T3(包铝)、2024-T3 (裸铝)、7075-T6 (包铝)和7075-T6 (裸铝)四种铝合金。
3.3.3.1.2 试验溶液为去离子水或蒸馏水和清洗剂。
3.3.3.2 试样制备
3.3.3.2.1 采用尺寸为50mm×100mm×(1~4)mm 的试样,试样上端中间部位可有φ3mm 的安装孔。2024-T3(包铝)和7075-T6(包铝)试样表面不需进行表面处理,2024-T3(裸铝)和7075-T6(裸铝)试样进行硫硼酸阳极氧化(封闭处理)或铬酸阳极化(封闭处理)。裸铝试样可由包铝试样打磨获得,每个单面打磨去除的厚度应大于2 倍包铝层厚度。
3.3.3.2.2 每次试验准备两套夹层试样对,两套夹层试样对的试验溶液分别为清洗剂和电导率不超过0.50mS/m的去离子水或蒸馏水(作为空白对照组)。每套夹层试样对包含4 个夹层试样对,每个夹层试样对由相同材料和相同表面处理状态的两片试样组成。所有试样用无水乙醇或丙酮清洗,干燥,放入干燥器中待用。
3.3.3.2.3 夹层试样对按如下方法制备: 将分析用快速或中速定量滤纸裁成25mm×75mm的长方形,将滤纸置于试样对的一片试样上。用滴管将试验溶液滴到滤纸上,使滤纸浸满试验溶液,将试样对的第二片试样放到滤纸上,形成夹层,每对夹层用长度不超过25mm,宽度不超过20mm的4条耐溶剂胶带固定,胶带粘在夹层对两个长边和两个短边的中间位置,即制得一个夹层试样对。
3.3.3.3 试验程序
3.3.3.3.1 对所有试样对进行干燥和潮湿的交替试验,每个夹层试样对应水平放置,不允许堆积。先将夹层试样对放到38℃±2℃的烘箱中保持8h,再放入38℃±2℃、相对湿度为95%~100%的调温调湿箱中保持16h,如此循环四次。然后将试样对依次放入38℃±2℃的烘箱中8h,38℃±2℃、相对湿度为95%~100%的调温调湿箱中64h。
3.3.3.3.2 试验结束后,试样用无水乙醇或丙酮清洗,用毛刷轻轻刷试样表面,再用无水乙醇或丙酮清洗,干燥,用10 倍放大镜检查每对试样变色和腐蚀情况。
3.3.3.4 清洗剂测试要求:不超过去离子水或蒸馏水的影响,清洗剂润湿的滤纸接触的铝合金表面允许轻微变色。
3.3.4 全浸腐蚀
按HB 20542中4.5.5节规定进行试验,技术指标要求见表2。
表2 全浸腐蚀技术指标
序号 | 试板材料 | 质量变化不超过(mg/cm2﹒24h) |
1 | LY12-CZ和7075-T6 | 0.04 |
2 | Ti-6Al-4V | 0.04 |
3 | 45#和30CrMnSiA | 0.04 |
4 | GH4169 | 0.04 |
3.3.5 氢脆腐蚀
按ASTM F519中A5.3.1规定(选择1a.2型试件进行试验时):应当按照表A5.1内的规定施加应力,试样应在整个试验期间(150h)浸入清洗剂中。清洗剂不应使试样产生脆性断裂。
3.3.6 应力腐蚀
按照HB 20542中4.5.10节进行试验,钛合金试样在500倍显微镜下观察无任何裂纹。
3.3.7 增氢量
将一个试样从中间剖开(以避免不同批次材料的氢含量差异影响实验数据准确性),1半在清洗剂中浸泡30分钟,另外1半原始试样不进行浸泡。按HB 5297.23进行增氢量测试,浸渍后试片的增氢量不能超过25mg/l(ppm)。试片材料为TC4或Ti-6Al-4V,尺寸大约为76×150×1.0-2.5mm,数量为1片。
3.3.8 镉层腐蚀
按HB 20542中4.5.6节进行试验,镀镉层质量变化不超过0.20mg/cm2﹒24h。
3.5 现场使用性能
3.5.1 现场清洗的验证对象应包含实际接触的材料和零件种类以及油污种类,具体按第一条所列的使用场景。
3.5.2 按产品说明进行使用,不允许清洗剂在零件表面自然挥发,需在清洗剂挥发前用新抹布擦干,清洗剂应能使清洗表面去除相应的污染物,当用目视检查时,零件应没有脏物、腐蚀、油、油脂和外来残余物。
3.5.3 使用干净的擦布测试其去除污染物的擦拭次数或时间,擦拭一个来回算做一次。
2.具有独立承担民事责任的能力,遵守国家相关法律、法规,企业征信良好;营业执照规定的经营范围应包含拟承制产品或服务。
3.从事该品类的研制/生产时间不得少于3年。
4.企业财务状况良好,连续亏损不得超过3年。
5.具备满足与拟申请承担任务的质量管理水**质量保证能力,建立满足顾客要求的质量体系(GJB、ISO、AS、EN等均可),并取得通过第三方认证的有效证书。
6.遵守国家相关法律、法规,企业征信良好;近3年经营活动中没有违法记录和重大的法律纠纷。
7.具备危险品生产许可证、经营许可证(适用于危险品制造商),具备危险品运输条件(获得相应资质或者承诺委托拥有资质的单位运输)。
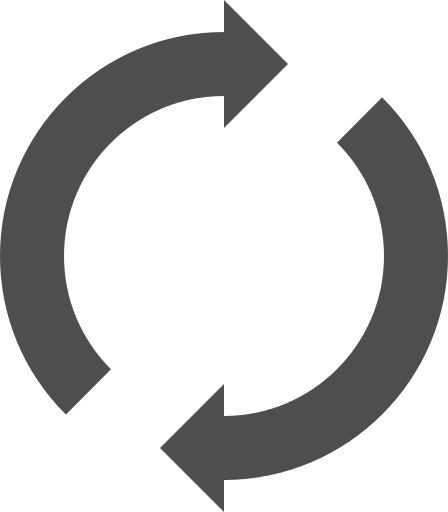