一汽解放传动事业部车桥基地建设项目暨重型换代桥技术升级(一期)
1、建设项目基本信息
企业基本信息
**** | 建设单位代码类型:|
912********131661N | 建设单位法人:倪牟淳 |
白亚林 | 建设单位所在行政区划:**省长****开发区 |
**省长****开发区****工业园 |
建设项目基本信息
****事业部车桥基地建设项目暨重型换代桥技术升级(一期) | 项目代码:|
建设性质: | |
2021版本:071-汽车整车制造;汽车用发动机制造;改装汽车制造;低速汽车制造;电车制造;汽车车身、挂车制造;汽车零部件及配件制造 | 行业类别(国民经济代码):C3670-C3670-汽车零部件及配件制造 |
建设地点: | **省长****开发区 ****工业园南侧 |
经度:125.12409 纬度: 43.83961 | ****机关:****环境局 |
环评批复时间: | 2021-07-23 |
长环建(表)(告知)〔2021〕10号 | 本工程排污许可证编号:**** |
2024-05-21 | 项目实际总投资(万元):98986 |
1515 | 运营单位名称:**** |
912********131661N | 验收监测(调查)报告编制机构名称:**** |
912********131661N | 验收监测单位:**** |
912********067642A | 竣工时间:2024-05-30 |
调试结束时间: | |
2024-10-31 | 验收报告公开结束时间:2024-11-29 |
验收报告公开载体: | https://gongshi.****.com/h5public-detail?id=422067 |
2、工程变动信息
项目性质
本项目为**(迁建)项目 | 实际建设情况:与环评及批复一致 |
无 | 是否属于重大变动:|
规模
项目****中心工业园内的原轻微车桥联合厂房(现为车桥3号厂房),原轴齿1号厂房(现为变速箱2号厂房)并**车桥1号厂房、车桥2号厂房,****集团1号厂房、2号厂房、轻微车桥联合厂房及轴齿1号厂房设备进行搬迁。本项目**车桥1号厂房建筑面积为36680m2,主要包括装配车间;**车桥2号厂房建筑面积为29622m2,主要为后桥桥壳车间;基地机加车间。变速箱2号厂房利用原有面积21240m2,主要为桥齿车间及热处理车间。车桥3号厂房利用原有面积69114m2,主要为冲焊车间;前桥杂件车间;后桥桥壳车间;基地机加车间装配车间。本项目通过改造、淘汰落后生产线并新购入装备,将原有生产线进行重排,达到年产32万支中重型车驱动桥总成,16万支转向桥总成的产能。 | 实际建设情况:环评阶段原轴齿1号厂房变为速箱2号厂房,现更名为4号厂房,厂房名称与环评阶段不一致,建设内容与环评一致 |
厂房名称与环评阶段不一致,建设内容与环评一致 | 是否属于重大变动:|
生产工艺
1、冲焊车间 (1)冲压工段 工艺描述:→OP15拆跺上料(机器人R1)→OP30涂油铺膜(润滑)→OP40成形(4000T液压机)→OP50撕膜(人工)→OP55转运(机器人R2)→OP60清洗(清洗机)→OP70抛丸(抛丸机)→OP80铣直边和坡口(数控铣床)→OP90打毛刺码垛(铣床机器人R3) (2)焊接工段 工艺描述:本工段主要承担中后桥壳焊接总成的焊接、清理、修磨、校正及检测等任务。 OP10组对半壳(CO2半自动焊机)→OP20焊直****工作站)→OP30切豁口(****工作站)→OP40****工作站含CO2半自动焊机)→OP60铣面镗减速器****加工中心)→OP70组焊加强环****工作站)→OP80组焊后盖(外侧****工作站)→OP90焊接后盖(内侧****工作站)→OP100****工作站)→OP130锯两端(圆盘锯)→OP140焊轴头(摩擦焊)→OP150焊法兰定位****工作站)→OP160车飞边/焊缝(数控车床)→OP170组对制动法兰(CO2半自动焊机)→OP180焊制动法兰****工作站)→OP190****工作站)OP210****加工中心)→OP220试漏/补焊(试漏机)→OP230钻放气孔油孔(卧式数控钻床)→OP240组对支架/托板(CO2半自动焊机)→OP250焊支架/托板****工作站)→OP260补焊/****工作站)→OP280总成抛丸(抛丸机)→OP290清渣(CO2半自动焊机)→OP310在线检测(蓝光检测仪)→OP330最终检测下线(转运) 2、前桥杂件车间 本车间主要承担中重型前桥的前轴、转向节零件的机械加工、表面淬火、清洗等任务。 (1)转向节 工艺描述:OP10半精车轴颈、端面及锥体(卧式数控车)→OP20精车轴颈、端面及车螺纹(卧式数控车)→OP30淬火(淬火机)→OP40磨轴颈、端面(数控端面外圆磨床)→OP50钻法兰螺栓孔以及螺纹孔、镗定位孔;铣平面,钻攻螺纹孔,钻镗ABS孔,****中心)→OP70钻主销孔(卧式双面组合钻床)→OP80粗精镗主销孔,精铣内侧面,****加工中心)→OP90铣杆部端头螺纹平面(立式铣床)→OP100探伤退磁(荧光磁粉探伤机)→OP110铣法兰处圆弧面(组合机床)→OP120压装衬套(压装机)→OP130打毛刺→OP140清洗(清洗机)→OP150打标记(标记机)→OP160手动压装油封→OP170最终检验。 (2)前轴 工艺描述:将控制臂、****加工中心进行加工,加工后对工件表面的残留冷却液和切屑进行清洗。将机加后的控制臂、球销、球座和端盖在预装圆台上进行装配和旋压。预装后的总成放到回火炉中进行加热。将回火后的总成和大卡环、小卡环、防尘罩在终装圆台上进行再装配,并测量总成性能。将终装后的零部件在压装机上压入橡胶支撑。 3、后桥桥壳车间 本车间主要承担中/后桥壳总成、中桥减速器壳总成、差速器壳等零件的机加、清洗、工序间检测等生产任务。 (1)桥壳四线(后桥壳) 工艺描述:OP10粗镗孔、车端面、倒角(镗床)→OP20磨轴头轴径(数控磨床)→OP30车小法兰外圆端面及止口(数控车床)→OP40铣面精镗孔;钻大法兰孔及倒角、攻丝;****加工中心)→OP50钻小法兰孔及倒角、攻丝(数控卧钻)→OP60去毛刺(去毛刺机器人)→OP70清洗(清洗机)→OP80打标记(激光标记机)→OP90最终检查 (2)桥壳三线(中桥壳) 工艺描述:OP10磨轴头轴径(数控磨床)→OP20车小法兰外圆端面及止口(数控车床)→OP30铣面精镗孔;钻、镗定位销孔;钻大法兰孔及倒角、攻丝;铣钻支架、加工贯通轴孔;钻小法兰孔及倒角、****中心)→OP40去毛刺(机器人)→OP50清洗(清洗机)→OP60打标记(打标机)→OP70最终检查 (3)减壳二线(中减壳) 工艺描述:OP10铣法兰面、止口、凸台,钻、镗定位孔,钻螺纹底孔,攻丝,钻、铰定位销孔,****中心)→OP20打标记(激光标记机)→OP30装配(压装机、拧紧机)→OP40半精镗、精镗孔,半精铣、精铣平面,铣调整环螺纹,钻、镗差速锁孔,钻孔、****中心)→OP50清洗(清洗机)本次扩建新增除标室一处,仅对备件部分件进行除标处理,分为橡胶支撑除标和机加件除标,机加件采用机械打磨进行除标,橡胶支撑件采用激光加热磨平处理。 4、基地机加车间 本车间承担中/后桥壳总成、中桥减速器壳总成、转向节、前壳、齿轮壳等 零件的机加、清洗、工序间检测等生产任务。 (1)桥壳一线(后桥壳) OP10车小法兰外圆端面及止口(数控车床)→OP20镗孔、车大法兰面(组合机)→OP30钻孔大法兰孔(组合机)→OP40攻大法兰螺纹(摇臂钻)→OP50****加工中心)→OP60攻****加工中心)→OP70去毛 刺(机器人)→OP80清洗(清洗机)→OP90打标记(打标机)→OP100最终检查 (2)桥壳一线(中桥壳) OP10车小法兰外圆端面及止口(数控车床)→OP20镗孔、车大法兰面(组合机)→OP30加工定位销孔、****加工中心)→OP40钻大法兰孔(组合机)→OP50攻大法兰螺纹(摇臂钻)→OP60钻小法兰孔(组合机)→OP70攻小法兰螺纹(组合机)→OP80去毛刺(机器人)→OP90清洗(清洗机)→OP100打标记(打标机)→OP110最终检查 (3)转向节四线 OP10粗铣法兰面、钻孔、插补铣轴承孔,钻孔、精铣法兰平面、粗精镗轴承孔、钻铰ABS孔及定位销孔,****加工中心)→OP20粗精铣两耳外部平面,钻孔、粗精镗孔、铣螺纹,钻孔、****加工中心)→OP30粗精铣平面,钻孔、倒角、攻螺纹,粗精铣槽,****加工中心)→OP40铣平面,镗圆槽孔,锪螺栓孔平面,钻攻螺纹孔,****中心)→OP50手动去毛刺→OP60清洗(清洗机)→OP70打标记(打标机)。 (4)差壳一线 OP10打标(智能标记机)→OP20车端面、内孔、球面(立式数控车床)→OP30粗车轴径及端面(立式数控车床)→OP40钻孔、倒角、****中心)→OP50钻、镗十字轴孔,****加工中心)→OP60精车轴径及 端面(卧式数控车床)→OP70测量(综合量仪B4C)→OP80清洗(清洗机) 5、桥齿车间 本车间主要承担中重型桥主、从动锥齿轮的机械加工、清洗等任务,生产性质属大批量生产。 (1)主动锥齿轮 OP10****中心孔(外委)→OP20粗车(外委)→OP30精车(卧式数控车床)→OP40打标识(标识机)→OP50铣花键(数控花键铣床)→OP60铣槽(数控铣床)→OP70铣齿(数控铣齿机)→OP80清洗(清洗机)→OP90热处理(热处理车间进行)→OP100磨小轴颈及平面(数控端面外圆磨床)→OP110磨大轴颈及平面(数控端面外圆磨床)。 (2)从动锥齿轮 OP10粗车(外委)→OP20精车外圆(立式数控车床)→OP30精车内孔(立式数控车床)→OP40****中心)→OP50****加工中心)→OP60铣齿(数控铣齿机)→OP70打标识(标识机)→OP80清洗(清洗机)→OP90热处理(热处理车间进行)→OP100硬车外圆(立式数控车床)→OP110硬车内孔(立式数控车床)。 (3)主、从动锥齿轮配对 OP10粗配对(锥齿轮检验机)→OP20研齿(数控研齿机)→OP30清洗(清 洗机)→OP40精配对(数控检验机)→OP50打标识(激光标识机)。 6、热处理车间 本车间承担主/从动锥齿轮的渗碳、淬火、清洗、回火、退火、倒棱、抛丸、校直等热处理任务,生产性质为大批量生产。 (1)主动锥齿轮: OP10涂防渗涂料→OP20预氧化→OP30加热→OP40渗碳→OP50扩散→OP60降温→OP70淬火→OP80清洗→OP90回火→OP100退火→OP110齿端倒角→OP120强化抛丸→OP130校直→OP140螺纹清理。 (2)从动锥齿轮: OP10预氧化→OP20加热→OP30渗碳→OP40扩散→OP50降温→OP60压淬→OP70清洗→OP80回火→OP90强化抛丸。 7、装配车间 本工段主要承担转向桥总成、减速器总成、架套总成装配任务,包括外协件 存放、总成的试验及成品的储运等任务。 (1)装配工段 1)前桥总成装配: OP010打刻标牌(激光打标机)→OP020前轴上线(前桥装配线)→OP030装转向节→OP040调转向角(转向角测量设备)→OP050装上臂(电动拧紧机)→OP060装制制动器、动气室(KBK)→OP070拧制动气室、制动器螺栓→OP080装横拉杆总成→OP090装油封座圈及轮毂总成(KBK)→OP100轮毂内腔注脂(注油)(注脂机、注油机)→OP110检测ABS信号(ABS检测仪)→OP120装制动鼓(KBK)→OP130调刹车间隙→OP140调前束(前束调整仪)→OP150总成下线(天车)→OP160总成挂线喷漆。 2)中后桥总成装配: OP010备件→OP020桥壳上线定位、夹紧(AGV线)→OP030装装制动器总成,预拧螺栓(助力机械手)→OP040复拧制动器螺栓(机器人拧紧机)→OP050装凸轮轴→OP060压装油封座圈,内轴承内圈(压机)→OP070装轮毂总成及外侧轴承内圈(机器人)→OP080压装轮毂及轴承合件(压机)→OP090拧轴头锁紧螺母,测转动力矩(拧紧机)→OP100装制动鼓总成(助力机械手)→OP110装工艺轮辋,拧紧工艺螺母(拧紧机)→OP120调刹车间隙(充放气专机)→OP130调转桥壳合件(桁架机械手)→OP140桥壳翻转(翻转机)→OP150桥壳涂胶(涂胶机)→OP160装减速器总成(机器人)→OP170复拧减速器螺栓(拧紧机)→OP180桥壳翻转(翻转机)→OP190装贯通轴合件(压机)→OP200压装贯通轴油封、突缘(压机)→OP210拧突圆螺母(拧紧机)→OP220桥壳翻转(翻转机)→OP230轮毂端面涂胶→OP240装半轴(专机)→OP250拧半轴螺栓(拧紧机)。→OP260试差速锁信号试→OP270轮毂注油(加油机)→OP280桥总成试漏(试漏仪)→OP290拆卸工艺轮辋→OP300总成下线检测→OP310总成挂线喷漆。 3)减速器总成装配: 差速器分装线:OP1010被齿、差壳上线(机器人)→OP1020组装差速器合件(旋转工作台)→OP1030差速器合件上线(机器人)→OP1040测量行、半轴齿轮啮合间隙(间隙测量机)→OP1050更换半轴齿轮垫片(复测仪)→OP1060被齿上线(机器人)→OP1070拧紧被齿连接螺栓(四轴拧紧机)→OP1080压装差速器轴承(轴承压装机)→OP1090检测被齿跳动(被齿跳动检测机)→OP1100总成翻转90°,吊装下线(翻转机、KBK系统)减速器合装线:OP2010减壳、主齿上线(机器人)→OP2020测量S2值(S2测量机)→OP2030翻转/拆卸减壳轴承盖(翻转拆卸机)→OP2040动态测量主锥下轴承高度/轴承上线(轴承动态测量机)→(机器人)→OP2050压装主锥上下轴承外圈(压装机)→压装主锥导向轴承外圈→OP2060压装主锥导向轴承内圈(压装机)→压装主锥下轴承内圈→OP2070套装主锥并压装上轴承内圈(套装机)→OP2080测量主锥预紧力垫片(窜动测量机)→OP2090拆上轴承,放垫片(压测机)→测量主锥转动力矩→OP2100压装油封,突缘(压装检测机)→OP2110拧紧主锥螺母并测量转矩(拧测机)→OP2120主锥转矩不合格返修(压测机)→OP2130压铆主锥螺母(压铆机)→OP2140主锥总成翻转180°(翻转机)→OP2150差速器总成上线(KBK系统,智能葫芦)→OP2160预拧紧轴承盖螺栓(双轴坐标拧紧机)→OP2170调节齿侧间隙(齿侧间隙调整机)→OP2180人工调节齿侧间隙→OP2190拧紧轴承盖螺栓(双轴坐标拧紧机)→OP2200自动喷涂白丹粉(喷涂机)→OP2210总成运转试验(总成运转试验机)→OP2220装锁片→OP2230翻转180°→OP2240压装后侧齿轮轴承外圈(压装机)→OP2250测量输入轴轴承垫片厚度(高度测量机)→OP2260减壳涂胶(涂胶机)→OP2270轴承座H1检测,压装轴承外圈(轴承座深度测量压机)→OP2280压装主锥端盖(压装机)→OP2290窜动测量(窜动测量机)→OP2300装轴间差速锁→OP2310检测差速锁气密性(气密测试仪)→OP2320拧紧轴承座螺栓(机器人双轴拧紧机)→OP2330压装油封、突缘(压装检测机)→OP2340拧紧凸缘螺母并压铆(拧紧压铆机)→OP2350中桥减总转线(转线机械手)→OP2360中减总成运转试验(总成运转试验机)→OP2370安装轮间差速锁→OP2380检测差速锁气密性(气密测试仪)→OP2390减总自动下线(桁架机械手)→OP2400减总加载测试(加载测试台)。 转向桥总成:清洗前轴→前轴上线→装转向节→装上臂及左右臂→装横拉杆→吊制动器→拧制动器螺栓→装轮毂→调预紧力、检测ABS调轴承间隙→调刹车间隙→油嘴注油→调前束→挂桥→喷漆。 驱动桥总成:清洗桥壳→桥壳上线→吊减速器→装减速器→拧减速器螺栓→装后盖→拧后盖螺栓→装刹车缸及凸轮轴→装轮毂→调预紧力、检测ABS→装半轴→调整刹车间隙→装垫板→试漏→挂桥→喷漆→总成磨合。 (2)涂装工段 上件→预脱脂→沥水→脱脂→沥水→水洗→防锈水洗→沥水→吹水→水分烘干→强冷→防护→手工预喷底漆→自动喷底漆→检查补漆→闪干→补漆→自动喷面漆→检查补喷→晾干→面漆烘干→局部补喷→强冷→拆防护→下件 8、****中心 本车间承担临时维修件(设备、夹具)制造任务,承担设备备件制造任务, 承担汽车件临时迂回加工任务,承担新产品试制任务。 9、磨刀部 刀具周转、刃磨及装调,工量具、刀具储存与分发,废旧工具分类处理,机 电设备及工装运行维护修理。机电备件贮存管理,全厂动力管线维修。 ①刀具刃磨 从生产线收回用钝的刀具→清洗→拆卸→刃磨→检查→装调→暂存→分送各使用点。 ②设备维修 巡回检查/接故障报修→制订维修计划(巡检发现问题)→准备维修备件(计 划维修)→修理→试车→交验收。 | 实际建设情况:与环评阶段一致 |
无 | 是否属于重大变动:|
环保设施或环保措施
1.运营期废气 本项目冲焊工段、下料工段产生的颗粒物经集气装置收集后通过滤筒除尘器(效率90%)处理,处理后经15m排气筒排放,前桥杂件及热处理淬火工段产生的颗粒物及非甲烷总烃经15m排气筒直接排放,热处理工艺气体发生炉产生的二氧化硫、氮氧化物、颗粒物直接经15m高排气筒排放,以上工段产生的颗粒物、二氧化硫、氮氧化物、颗粒物及非甲烷总烃排放满足《大气污染物排放标准》GB16297-1996)中二级标准,对周围环境空气影响较小。 喷涂工艺烘干炉,产生的废气直接经15m排气筒排放,其中二氧化硫和氮氧化物满足《大气污染物排放标准》(GB16297-1996)中二级标准,烟尘满足《工业炉窑大气污染物排放标准》(GB9078-1996)中表2和表4要求,对周围环境空气影响较小。 喷涂过程中产生的非甲烷总烃经活性炭吸附后与烘干废气一同送至RTO焚烧处理,处理后的废气经不低于15m高排气筒排放,非甲烷总烃满足《大气污染物排放标准》(GB16297-1996)中二级标准。 食堂油烟经自建油烟净化器处理后通过高于楼顶的排气筒排放,排放浓度满足《饮食业油烟排放标准(试行)》(GB18483-2001)中大型标准限值,对周围环境空气影响较小。 本项目冲焊车间、热处理车间抛丸粉尘;空调预处理产生的二氧化硫、氮氧化物、颗粒物以无组织形式排放,排放标准需满足《大气污染物排放标准》(GB16297-1996)中二级标准,对周围环境空气影响较小。 热处理车间渗碳工序产生的非甲烷总烃厂区内浓度执行《挥发性有机物无组织排放控制标准》(GB37822-2019)特别排放限值要求,厂界执行《大气污染物排放标准》(GB16297-1996)。 2.运营期废水 拟建项目车桥3号厂房和变速箱2号厂房废清洗液、废乳化液收集后与生产废水,通过压力****园区污水处理站。**车间涂装废水输送至车间内生产废水收集池;**车间的废乳化液、废清洗液用槽车单机收集,送至生产废水收集池,生产废水收集池的生产废水定期用****园区污水处理站处理达到《污水综合排放标准》(GB8978-1996)中三级标准后排****处理厂。生活污水及循环冷却水直接经管网排****处理厂。 3.运营期噪声 拟建项目采用低噪声设备,对于声级值较大的设备等安放在室内,并设置单独的操作间。机械设备设置减震器,风机口安装消音器等。通过以上措施,拟建项目北侧均满足《工业企业厂界环境噪声排放标准》(GB12348-2008)中4类标准;东、南、西侧满足《工业企业厂界环境噪声排放标准》(GB12348-2008)中3类标准,对周围声环境影响较小。 4.运营期固体废物 本项目产生危险废物和一般固****园区现有危废暂存间及固废贮存间进行贮存,****公司回收,综合利用。含油污泥、废活性炭、含油废膜、废机油、废机油桶、含油纺织物、漆渣、含胶废物等废物,委托具有资质的危废处置单位安全处置。产生的****园区****处理站处置。本项目产生的一般生活垃圾由环卫部门统一收集处理。固体废物分类收集,分类处理;不产生二次污染。 | 实际建设情况:1.运营期废气 本项目冲焊工段、下料工段产生的颗粒物经集气装置收集后通过滤筒除尘器(效率90%)处理,处理后经15m排气筒排放,前桥杂件及热处理淬火工段产生的颗粒物及非甲烷总烃经15m排气筒直接排放,热处理工艺气体发生炉产生的二氧化硫、氮氧化物、颗粒物直接经15m高排气筒排放,以上工段产生的颗粒物、二氧化硫、氮氧化物、颗粒物及非甲烷总烃排放满足《大气污染物排放标准》GB16297-1996)中二级标准,对周围环境空气影响较小。 喷涂工艺烘干炉,车桥1号厂房产生的废气经24.5m高排气筒排放,车桥3号厂房产生的废气经15m高排气筒排放,其中二氧化硫和氮氧化物满足《大气污染物排放标准》(GB16297-1996)中二级标准,烟尘满足《工业炉窑大气污染物排放标准》(GB9078-1996)中表2和表4要求,对周围环境空气影响较小。 喷涂过程中产生的非甲烷总烃经活性炭吸附后与烘干废气一同送至RTO焚烧处理,车桥1号厂房处理后的废气经24.5m高排气筒排放,车桥3号厂房处理后的废气经15m高排气筒排放,非甲烷总烃满足《大气污染物排放标准》(GB16297-1996)中二级标准。 食堂油烟经自建油烟净化器处理后通过高于楼顶的排气筒排放,排放浓度满足《饮食业油烟排放标准(试行)》(GB18483-2001)中大型标准限值,对周围环境空气影响较小。 本项目冲焊车间、热处理车间抛丸粉尘;抛丸废气经设备自带除尘设备(去除效率 99%)处理后通过15m高排气筒排放,满足《大气污染物排放标准》(GB16297-1996)中二级标准。 空调预处理产生的二氧化硫、氮氧化物、颗粒物以无组织形式排放,排放标准需满足《大气污染物排放标准》(GB16297-1996)中二级标准,对周围环境空气影响较小。 热处理车间渗碳工序产生的非甲烷总烃厂区内浓度执行《挥发性有机物无组织排放控制标准》(GB37822-2019)特别排放限值要求,厂界执行《大气污染物排放标准》(GB16297-1996)。 2.运营期废水 车桥3号厂房和4号厂房废清洗液、废乳化液收集后与生产废水,通过压力****园区污水处理站。**车间涂装废水输送至车间内生产废水收集池;**车间的废乳化液、废清洗液用槽车单机收集,送至生产废水收集池,生产废水收集池的生产废水定期用****园区污水处理站处理达到《污水综合排放标准》(GB8978-1996)中三级标准后排****处理厂。生活污水及循环冷却水直接经管网排****处理厂。 3.运营期噪声 项目采用低噪声设备,对于声级值较大的设备等安放在室内,并设置单独的操作间。机械设备设置减震器,风机口安装消音器等。通过以上措施,拟建项目北侧均满足《工业企业厂界环境噪声排放标准》(GB12348-2008)中4类标准;东、南、西侧满足《工业企业厂界环境噪声排放标准》(GB12348-2008)中3类标准,对周围声环境影响较小。 4.运营期固体废物 本本项目产生****园区现有危废暂存间及车桥1号车间、车桥2号车间**危险废物暂存间暂存,一般****园区现有固废贮存间进行贮存,****公司回收,综合利用。含油污泥、废活性炭、含 油废膜、废机油、废机油桶、含油纺织物、漆渣、含 胶废物等废物,委托具有资质的危废处置单位安全处置。产生的****园区****处理站处置。本项目产生的一般生活垃圾由环卫部门统一收集处理。固体废物分类收集,分类处理 |
本项目环评阶段车桥1号厂房排气筒高度为15m,验收阶段实际建设排气筒高度为24.5m,排气筒高度高于环评阶段;环评阶段计划冲焊车间、热处理车间产生的抛丸废气为无组织排放,实际建设内容为有组织排放,对比环评时期排放方式有所变更;环评阶段项目产生****园区现有危废暂存间进行贮存,实际建设内容为车桥1号厂房、车桥2号厂房分别建设一处危废暂存间,对比环评时期多2处危废暂存间;环评阶段原轴齿1号厂房变更后为变速箱2号厂房,现更名为4号厂房,对比环评时期车间名称有所变更。 | 是否属于重大变动:|
其他
无 | 实际建设情况:无 |
无 | 是否属于重大变动:|
3、污染物排放量
0 | 0 | 0 | 0 | 0 | 0 | 0 | |
17.15 | 5.82 | 0 | 17.15 | 0 | 5.82 | -11.33 | |
2.23 | 0.62 | 0 | 2.23 | 0 | 0.62 | -1.61 | |
0 | 0 | 0 | 0 | 0 | 0 | 0 | |
0 | 0 | 0 | 0 | 0 | 0 | 0 | |
0 | 0 | 0 | 0 | 0 | 0 | 0 | / |
0 | 0 | 0 | 0 | 0 | 0 | 0 | / |
0 | 0 | 0 | 0 | 0 | 0 | 0 | / |
12.56 | 4.774 | 0 | 12.56 | 0 | 4.774 | -7.786 | / |
35.11 | 11.69 | 0 | 35.11 | 0 | 11.69 | -23.42 | / |
4、环境保护设施落实情况
表1 水污染治理设施
1 | 污水处理站 | 《污水综合排放标准》(GB8978-1996)中三级标准 | ****园区****处理站 | 2024年6月13日-6月18日,由********处理站废水进行检测,检测结果均满足《污水综合排放标准》(GB8978-1996)中三级标准 |
表2 大气污染治理设施
1 | 冲焊工段、下料工段颗粒物经集气装置 | 《大气污染物排放标准》 (GB16297-1996)中二级标准 | 冲焊工段产生的颗粒物经集气装置收集后通过滤筒除尘器(效率90%)处理,处理后经15m高排气筒排放 | 2024年6月6日-9日,委托****对颗粒物进行监测,检测结果满足《大气污染物排放标准》 (GB16297-1996)中二级标准 | |
2 | 活性碳吸附装置及RTO焚烧处理 | 《大气污染物排放标准》(GB16297-1996)中二级标准 | 喷涂过程中产生的非甲烷总烃经活性炭吸附后与烘干废气一同送至RTO焚烧处理,车桥1号厂房处理后的废气经24.5m高排气筒排放,车桥3号厂房处理后的废气经15m高排气筒排放 | 2024年6月6日-9日,委托****对非甲烷总烃进行监测,检测结果满足《大气污染物排放标准》 (GB16297-1996)中二级标准 | |
3 | 油烟净化装置 | 《饮食业油烟排放标准(试行)》(GB18483-2001)中大型标准限值 | 食堂油烟经自建油烟净化器处理后通过高于楼顶的排气筒排放 | 2024.9.13---2024.9.14,委托****对食堂油烟进行监测,排放浓度满足《饮食业油烟排放标准(试行)》(GB18483-2001)中大型标准限值 | |
4 | 抛丸设备自带除尘设备 | 《大气污染物排放标准》(GB16297-1996)中二级标准 | 冲焊车间、热处理车间抛丸粉尘;抛丸废气经设备自带除尘设备(去除效率 99%)处理后通过15m高排气筒排放 | 2024年6月6日-9日,委托****对非甲烷总烃进行监测,检测结果满足《大气污染物排放标准》 (GB16297-1996)中二级标准 |
表3 噪声治理设施
1 | 减震器、消音器等 | 项目北侧满足《工业企业厂界环境噪声排放标准》(GB12348-2008)中4类标准;东、南、西侧满足《工业企业厂界环境噪声排放标准》(GB12348-2008)中3类标准 | 项目采用低噪声设备,对于声级值较大的设备等安放在室内,并设置单独的操作间。机械设备设置减震器,风机口安装消音器等。 | 2024.6.13-14;2024.6.18-19****对项目厂界噪声进行了监测,项目北侧满足《工业企业厂界环境噪声排放标准》(GB12348-2008)中4类标准;东、南、西侧满足《工业企业厂界环境噪声排放标准》(GB12348-2008)中3类标准 |
表4 地下水污染治理设施
表5 固废治理设施
1 | 本项目产生危险废物和一般固****园区现有危废暂存间及固废贮存间进行贮存,****公司回收,综合利用。含油污泥、废活性炭、含油废膜、废机油、废机油桶、含油纺织物、漆渣、含胶废物等废物,委托具有资质的危废处置单位安全处置。产生的****园区****处理站处置。本项目产生的一般生活垃圾由环卫部门统一收集处理。固体废物分类收集,分类处理 | 本项目产生****园区现有危废暂存间及车桥1号车间、车桥2号车间**危险废物暂存间暂存,一般****园区现有固废贮存间进行贮存,****公司回收,综合利用。含油污泥、废活性炭、含 油废膜、废机油、废机油桶、含油纺织物、漆渣、含 胶废物等废物,委托具有资质的危废处置单位安全处置。产生的****园区****处理站处置。本项目产生的一般生活垃圾由环卫部门统一收集处理。固体废物分类收集,分类处理; |
表6 生态保护设施
表7 风险设施
5、环境保护对策措施落实情况
依托工程
车桥3号厂房和4号厂房废清洗液、废乳化液收集后与生产废水,通过压力****园区污水处理站。**车间涂装废水压力输送至车间内设置的地下式生产废水收集池;**车间的废清洗液、废乳化液用槽车单机收集,送至生产废水收集池,生产废水收集池的生产废水定期用****园区污水处理站处理达到《污水综合排放标准》(GB8978-1996)中三级标准后排****处理厂。 本项目产生危险废物和一般固****园区现有危废暂存间及固废贮存间进行贮存。 | 验收阶段落实情况:项目废清洗液、废乳化液收集后****园区****处理站处置。与环评阶段一致;本项目产生****园区现有危废暂存间及车桥1号车间、车桥2号车间**危险废物暂存间暂存,对比环评时期新增2座危废暂存间 |
/ |
环保搬迁
无 | 验收阶段落实情况:无 |
/ |
区域削减
无 | 验收阶段落实情况:无 |
/ |
生态恢复、补偿或管理
无 | 验收阶段落实情况:无 |
/ |
功能置换
无 | 验收阶段落实情况:无 |
/ |
其他
无 | 验收阶段落实情况:无 |
/ |
6、工程建设对项目周边环境的影响
/ |
/ |
/ |
/ |
/ |
/ |
7、验收结论
1 | 未按环境影响报告书(表)及其审批部门审批决定要求建设或落实环境保护设施,或者环境保护设施未能与主体工程同时投产使用 |
2 | 污染物排放不符合国家和地方相关标准、环境影响报告书(表)及其审批部门审批决定或者主要污染物总量指标控制要求 |
3 | 环境影响报告书(表)经批准后,该建设项目的性质、规模、地点、采用的生产工艺或者防治污染、防止生态破坏的措施发生重大变动,建设单位未重新报批环境影响报告书(表)或环境影响报告书(表)未经批准 |
4 | 建设过程中造成重大环境污染未治理完成,或者造成重大生态破坏未恢复 |
5 | 纳入排污许可管理的建设项目,无证排污或不按证排污 |
6 | 分期建设、分期投入生产或者使用的建设项目,其环境保护设施防治环境污染和生态破坏的能力不能满足主体工程需要 |
7 | 建设单位因该建设项目违反国家和地方环境保护法律法规受到处罚,被责令改正,尚未改正完成 |
8 | 验收报告的基础资料数据明显不实,内容存在重大缺项、遗漏,或者验收结论不明确、不合理 |
9 | 其他环境保护法律法规规章等规定不得通过环境保护验收 |
不存在上述情况 | |
验收结论 | 合格 |
招标导航更多>>
工程建筑
交通运输
环保绿化
医疗卫生
仪器仪表
水利水电
能源化工
弱电安防
办公文教
通讯电子
机械设备
农林牧渔
市政基建
政府部门
换一批
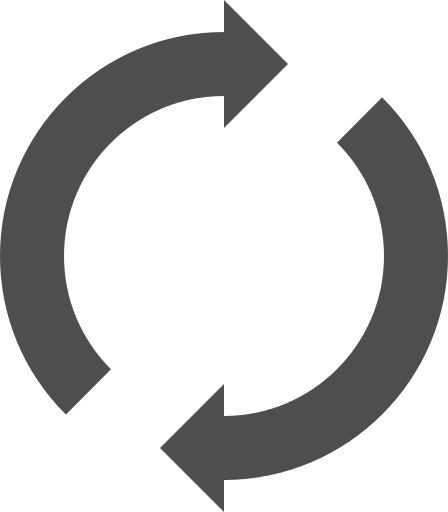