********化****中心平台设备更新项目 —增材制造系统采购项目(国债项目)招标项目的潜在供应商应在线上获取招标文件,并于2024年12月25日 09时30分(**时间)前递交投标文件。
品目1:搅拌摩擦增材制造设备 1套 国产
1、总体参数
★1.1目标材料:铝合金、镁合金等轻质合金材料。
1.2 设备主要构成
▲1.2.1设备主机:采用一体式结构,整体刚性好,操作便捷。
▲1.2.2控制系统:采用搅拌摩擦固相增材专用控制系统。
▲1.2.3智慧采集系统:可对增材中主轴、棒料推进轴的扭矩和压力、温度进行检测和数据采集,并无线传输至接收模块。
1.2.4批量上料系统:配置棒料仓,手动放置棒料进≥10mm*10mm*300mm棒料仓,棒料仓自动进行批量上料。
1.2.5视频监视系统:远程观察增材状态。
▲1.2.6冷却系统:实现固相制造工具在线冷却,提高工具寿命和产品成型质量。
▲1.2.7安全防护系统:设备四周配备钣金防护罩,各轴设置电气限位和机械限位等。
1.2.8气氛工装要求:增材基板尺寸≥350*300mm; 增材区域≥200*200*100mm。
1.3 设备各轴定义
1) X轴—横梁沿床身导轨直线运动;
2) Y轴—溜板沿横梁左右运动;
3) Z轴—滑枕沿溜板上下运动;
4)Z1轴—顶料机构上下运动;
5) Sp轴—主轴旋转运动。
1.4设备功能要求
★1.4.1设备配备无线数据采集系统,采集模块位于增材刀柄上,可在主轴旋转过程中直接检测增材区域力、扭矩、温度,并无线传输至接收模块,进行实时显示,数据准确、可靠。其参数指标如下:
1)≥2路高频温度0~1400℃,采集频率1~128 Hz;
2)压力-5~+45 kN,采集频率1~1024 Hz;
3)扭矩-150~+150Nm,采集频率1~1024 Hz;
4)**抗力-30~30 kN,采集频率1~1024 Hz;
5)压力、扭矩检测精度不低于0.5%。
6)系统可同时输出0~3V模拟量和数字量信号,数字量信号可通过上位机显示。
★1.4.2设备需具备批量上料功能,能够实现≥10mm轻质铝合金棒料从棒料仓自动上料,上料过程中无需人工参与。料箱集成在机头上,预留人工上料口,方便人工批量对料仓进行装载棒料,单次连续送料≥6根。
★1.4.3设备的冷却系统在转速不低于 2000 r/min,可持续运行24h,累计冷却部件寿命≥500h。
1.4.4电气部分
▲1)满足搅拌摩擦固相增材加工需求,系统操作便捷、宜人化程度好。
2)全密封空调电柜,使数控系统及轴功率模块具有良好的工作环境。
▲3)内嵌式操作台,配有可移动式电子手轮,具有轴选择、快速进给、手动方向、急停和使能等功能,可以对增材层高进行手动精细微调,方便操作者使用,最小调节量0.001mm。
▲4)控制系统具有超程报警、过载保护及其他报警及保护功能;
5)系统能实现可靠机、电、气连接和控制。
▲6)设备主轴采用电主轴,结构紧凑。
1.4.5视频监视系统
▲1)设备需配备视频监视系统可远程观察增材状态,视频监控系统具备可扩展功能和接口,方便客户对屏幕进行扩展。
▲2)视频监视系统采集频率≥50Hz;
3)视频分辨率:不低于1920 × 1080。
1.5设备总体参数指标要求
▲1.5.1主轴最大转速:≥2000rpm
▲1.5.2主轴额定功率:≥12kw
1.5.3主轴额定扭矩:120Nm
▲1.5.4 Z1轴最大推力:≥3T
1.5.5工作台尺寸(长×宽):400×400mm
▲1.5.6 X轴行程:≥300mm
▲1.5.7 Y轴行程:≥300mm
▲1.5.8 Z轴行程:≥300mm
1.5.9 Z1轴行程:≥350mm
1.5.10主轴端面到工作台距离:90~390mm
1.5.11适用棒料截面尺寸:10±0.1 □代表横截面
1.5.12适用棒料长度:300(0,-1)mm
1.5.13适用棒料直线度:0.3mm
1.5.14分层厚度:0.2~2mm
1.5.15可增材最大区域:≥300×300×300mm
1.5.16设备外形尺寸(长×宽×高):≤1400×1700×3000mm
▲1.5.17 X轴定位精度:≤0.03mm/全程
▲1.5.18 Y轴定位精度:≤0.03mm/全程
▲1.5.19 Z轴定位精度:≤0.03mm/全程
1.5.20 X轴重复定位精度:≤0.02mm/全程
1.5.21 Y轴重复定位精度:≤0.02mm/全程
1.5.12 Z轴重复定位精度:≤0.02mm/全程
2、设备依据相关标准
GB/T9061-1988 金属切削机床 通用技术条件;
GB/T15760-1995 金属切削机床 安全防护技术条件;
GB/T5226.1-1996 工业机械电气设备 第一部分 通用技术条件;
JB/T10051-1999 金属切削机床液压系统通用技术条件;
JB/T8356.1-1996 机床包装技术条件;
GB/T17421.2-2000机床检测通则 第2部分:数控轴线的定位精度和重复定位精度的确定;
JB/T 13589.1-2018 ****中心 第1部分:**固定式机床精度检验。
3、设备安全防护
(1)系统具备软件限位、电气限位、硬限位等安全防护功能;
(2)设备X/Y轴配备铠甲防护罩,对导轨丝杠进行防护;
(3)设备配备全防护钣金,整体美观,防护性好。
4、设备使用条件
(1) 电网标准:(交流三相五线)电压380V±10%,频率50Hz±2%;
(2)设备应可靠接地,具备漏电保护功能;
(3)环境温度:-10℃ ~45℃;
(4)相对湿度:≤ 85%。
品目1:增材制造涡流阵列检测系统 1套 国产
设备总体参数:
1.1涡流阵列检测主机
★(1)≥16通道阵列涡流检测;无方向性焊缝检测;独特的裂纹测深功能;非等幅相位/幅度报警功能;阻抗平面图、时基扫描图显示、时基叠合显示、阵列涡流扫描二(B/C)、三维成像显示功能;高清晰度、高灵敏度;操作简单,具备中、英文操作界面(任选);C-扫描视图的数据采集,可快速有效地检测缺陷和定位;支持管材壁厚减薄测量、表面缺陷检测及深度测量、金属材料表面涂层及镀层厚度测量、各类金属材质、硬度分选,可测电导率;多种滤波方式;可预设专用工艺参数;数据存储方式多样;具多频检测组态分析功能;支持视频涡流检测功能:同步获取被检对象表面的涡流检测信号和视频图像信号。
▲(2) 频率范围: 64Hz~5MHz;频率: ≥4个;阻抗平面: ≥8个;
(3)高通滤波: 0~500Hz;低通滤波: 10Hz~10KHz;数字滤波: 1~100;
(4)前置增益: 10~35dB;驱动: 8级;幅度和相位测量: 自动/手动;相位: 0~359度;增益: 0~90dB,最小步进 0.5 dB;
(5)同屏显示: 阻抗平面图、时基扫描曲线、B/C扫成像、时基叠合显示;
(6)报警类型: 半幅相报警 / 幅相报警 / 方框报警;滤波方式: 高通/低通/数字滤波;
(7)平衡方式: 数字式电子平衡。
(8)涡流检测探头1套(10个,含涡流阵列探头1个,电导率探头1个);
★(9)磁记忆检测功能:对工件表面漏磁场法向分量进行扫描检测 ,便可确定应力集中区域;不需要对被检测表面做任何处理;不需要对被检测对象专门充磁;原来不知道的应力集中和金属缺陷的位置可在检测过程中确定;操作简单,可预设专用工艺参数;数据存储方式多样。可用于铁磁性金属构件的应力集中及疲劳裂纹检测;通道数:≥8个检测通道;
▲ (10)磁记忆检测显示模式: 时基/阴影/数字/叠合;信号显示: S值/K值;磁记忆数据校准方式: 仪器探头/大地磁场;测长时钟选择:内/外时钟;步距: 1~256mm;增益: 0~90dB,最小步进 0.5 dB;数字滤波: 1~100;报警方式: HP值过“零”报警(门限10~1000)/K值报警(1~500);背景抑制: 关/加S1/减S1;
1.2主机其他性能指标:笔记本电脑配置不低于(CPU:i5,内存:8G,硬盘:512GB,显示:14.0英寸);数据接口: USB、网络;工作温度范围: -20℃ ~ +55℃;储存温度范围:-20℃ ~ +50℃;
▲1.3自动化丝材涡流检测系统:自动化检测可适应Ф0.1~2mm丝材规格范围,对于不大于直径18mm的棒材能够进行手动检测。
1.4丝材检测机械装置包括丝材定心校直轮组(前后两组),涡流检测装置、张紧装置、导向轮及编码测速轮组、放线盘、收线盘轮轴等组成;放线盘安装在控制柜上方部的左侧边上;张紧装置安装在放线盘侧;丝材校直装置安装在出线盘右侧;导向轮组安装在校直装置两侧;涡流检测装置安装在两组矫直轮组中间。涡流检测主机含涡流线圈探头和穿过式磁饱和器,磁饱和器由三爪定心、导套、定心套组成。可根据棒材规格大小更换不同探头和导套等;丝材可适应Ф0.1~2mm规格范围。压轮装置保证检测****检测中心。手动升降系统可精确调整压轮精度,保证不同规格线径都可以进行调整。丝材从放线盘出来,经过导线轮,穿过矫直装置,进入涡流检测装置,出来后进过定心轮组和张紧轮组后,由收线轮盘将丝材重新盘卷完成。探头座高低可根据工件规格大小通过升降装置升降探头座,****中心高一致。需提供机械系统三维数模图,总装图、部装图和二维CAD图纸。
1.5电控系统:控制系统使用PLC作整个过程控制,所有元器件和触控屏均采用正规厂商产品。自动探伤模式下,探伤可以自动运行,无需人工控制。电控系统配有自动手动切换功能,可以随时切换到手动模式。整套系统配置有安全紧急开关。交货时需提供电路原理图、接线图和程序代码。
1.6报告处理系统:探伤报告自动生成,可以方便查询历史探伤记录,可以记录检验报告、导出检验报告到相应格式(如:pdf等)并能方便存储备查;报警及打标装置:缺陷信号声光报警提示,不同颜色的喷标装置可分别对缺陷有效标记,喷标精度±25mm。
1.7设备尺寸: ≥长1500mm,≥宽1000mm,≥高1500mm。
品目2:增材制造超声相控阵检测系统 1套 国产
1.设备总体参数:
1.1 主机
★(1)超声相控阵检测主机1套:至少具有64通道,并能至少同时激励16通道,并支持PR功能;仪器应符合EN12668的要求;至少具有4组TOFD通道,支持同时进行PAUT及TOFD的联合检测,主机可供系统集成使用,电脑端配套软件作为检测数据采集和分析;
(2)超声相控阵检测主机PAUT通道发射电压不低于115V,UT通道不低于190V;具有完整的PAUT系统校准功能,每条波束应能独立进行校准;至少具有2轴编码功能;仪器应为无风扇设计,以满足现场高尘环境的使用要求;
(3)具有TCG功能并支持TCG及DAC的转换;数据传输速率不低于30MB/S;声束数量不低于1024;脉冲重复频率不低于20KHz;
(4)仪器使用温度能够达到40°C;仪器设计至少应符合IP65环境评级;脉冲宽度至少在30ns-1000ns(步距为2.5ns);
▲(5)闸门要求:每个通道至少有4个独立的闸门,1个界面触发闸门,2个报警缺陷闸门,1个底波缺陷跟踪闸门,每个闸门可分别在整个显示范围内调节起始、宽度和门槛值。每个闸门有自己的特定颜色,便于识别。每个通道的界面闸门和缺陷闸门均可存储尖峰振幅和TOF数据;
▲(6)为了增加检测效率,仪器至少支持4台并联,可以扩大脉冲重复频率;
(7)仪器相控阵接口为IPEX接口,常规超声接口为Lemo 00接口;
(8)仪器具有网线接口、I/O接口、报警输出接口等常用接口;
▲(9)仪器具有多种开发模式,可以开放模拟信号的底层数据,供以后科研开发使用,利用仪器提供的底层数据,可以自行编写A扫描、B扫描、S扫描以及C扫描等显示;
▲(10)仪器应具有表面自适应功能,可以检测复杂表面形状的工件,将界面波和底波可以计算显示为平直的形状,便于分析;
▲(11)免费提供数据二次开发的SDK开发包和机械控制的SDK开发包;
▲(12)SNR信噪比分析功能;
▲(13)C扫描融合功能,可以将多个C扫数据融合在一起;
▲(14)FFT计算,傅里叶变换;
▲(15)可以导入自行创建的TCG曲线,从而可以创建符合DGS的缺陷放大和定量功能;
▲(16)条件性A扫描数据记录,减少数据存储量;
▲(17)自动缺陷辨别模式;
(18)离线闸门调整;
(19)离线C扫描重构;
(20)离线TOFD直通波拉直和去除;
(21)数据文件融合
★1.2相控阵整合型仪器设备控制及数据分析软件1套:
数据采集、控制及数据分析软件适用于Win7,Win8,Win10等PC操作系统;软件支持二次开发,可使用C++等程序开发软件,实现实时修改设置参数、读取检测原始数据等功能;控制及数据分析软件应能免费进行版本更新;控制及数据分析软件应能设计高级聚焦法则并应用于仪器端,例如矩阵探头和TRL一发一收探头;控制及数据分析软件能基于PC端进行数据分析及报告出具;控制及数据分析软件在数据分析时,应具有软增益、直通波同步、直通波去除、多视图同时显示及调整、焊缝轮廓添加、SAFT、视图融合等分析功能。软件支持多国语言,至少包含中文、英语;软件可通过网络对便携式采集设备进行控制,实现参数设置、数据采集等功能;
★1.3探头
轻合金增材制造产品用1个楔块和超声探头3个(其中含1个水浸相控阵探头,1个相控阵探头,1个30MHz水浸超声探头),电脑1台,参数不低于此配置CPU: core ultra7 -155h;显卡:集成显卡;线程:22;内存:32gb;硬盘:1tb固态; 14.5英寸 2560*1600。
1.4自动化超声波检测装置1套
★(1)探伤方法:采用完全水浸法。
(2)直径1.5-20mm ,长度≥300mm的自动超声波探伤。
(3)设备主要指标:检测对象:铜棒/铝棒直径:1.5-20mm,长度:300mm;棒料温度:不高于50℃;
(4)检测工件要求:弯曲度:1.5mm/m(长度方向矫直);圆度及倒角:无外翻及毛刺;粗糙度:无氧化皮、Ra≤3.2;
(5)检测部位温度:常温;检测盲区:棒料两端头≤30mm;设备尺寸: 长≥1500mm,≥宽1000mm,高≥1700mm。
(6)设备工作环境:交流电源:220V±15% 50Hz;环境温度:5℃ - 60℃;最大湿度:90%;耦**:采用自来水。
(7)设备主要组成:设备主要由工件定位机构、探头扫查行车(X 轴)、探头盒旋转机构(R 轴)、操作台、电气控制器等组成,其中机械部分主要材料为不锈钢。工件定位机构:棒材两端采用三爪卡盘,一端为三轮定心机构,另一端为随动轴,尾端可以根据工件长度进行移动,保证满足不同长度、不同直径的棒材稳定定位。探头扫查行车(X 轴):可控制行进速度和步进距离,螺距应小于探头所覆盖的宽度并保证其有效声束宽度在探测过程中覆盖于旋转和移动速度,保证满足本方案产品参数中提到的棒材规格探伤要求。探头盒旋转机构(R 轴):探头在探头盒旋转机构里延棒材外径360度旋转一圈后步进(按探头的扫查范围选择步进距离)。检测水箱:超声波检测需要水做耦合剂。做到了自动化,并安装了限位开关、过载/短路保护器、多种防尘罩等,保障设备长期稳定运行。设备的关键电气部件:PLC和电气元件、电机、驱动器、电器元件低故障率可靠性高。提供机械装置三维数模图、总装图和零件CAD图,电气系统提供电气原理图、接线图和PLC程序代码。
品目3:增材制造机器视觉智能检测系统 1套 国产
1.设备总体参数:
★1.1检测用3D激光轮廓传感器1个:激光线轮廓点数≥3200个,Z方向线性度(+/-% of MR)为0.01,X方向分辨率(轮廓线数据间隔)为8.8 ~ 11.8 μm,Z方向重复性 (μm)为0.52,安装净距离(CD) (mm)为40,测量范围(MR)(mm)为26,视野 (FOV) (mm)为28 - 37。扫描速度1.3 KHz,数据接口为Gigabit Ethernet(1000Mbit/s),兼容Fast Ethernet(100Mbit/s),数字I/O为12-pin M12接口提供供电和I/O,3路差分信号输入(Line 0/3/6),1路差分信号输出(Line 1),1路RS-232,支持通讯协议。可以通过图像识别和分类功能对图像进行自动处理。通过训练模型和算法,软件可以识别和分类不同的尺寸公差测量、复杂形状检测、表面质量缺陷等;图形界面和开源SDK(软件开发包)实现参数设置和三维数据实时可视化。提供开源SDK、驱动以及支持标准工业协议方便与用户应用、第三方图像处理软件和PLC集成。该系统含有授权卡1个、显示器网络线缆和供电线缆(各1个),需提供软件代码。
1.2检测用3D相机智能视觉控制器1个;处理器参数配置不低于:i7-4790及以上;内存:16G;电源750W,最高至1200W,4个PCI扩展槽,至少支持2个硬盘,控制器至少集成4路IO接口,并可独立定义输入输出,2路及以上以太网接口,控制器集成后支持通讯协议EtherNet/IPT,PROFINET,SLMP等基本协议接口。
★1.3检测用3D激光立体相机1个:配置不低于:分辨率:3072 × 2048@RGB图,1440 × 1080@深度图,深度图检测精度:X,Y:0.5 ****@1.2 m;1 mm@1 m,Z:0.2 ****@1.2 m; 0.4 mm@2 m;该检测用系统含有:3D激光振镜立体相机控制器套包1个、电源及线缆1个、显示器1个、授权加密狗2个、开发软件1个,具有通讯功能;检测用3D相机智能视觉控制器参数配置不低于:处理器:i7-8700及以上;内存:16G;硬盘:128G+2THDD,支持PCIE扩展槽,支持8路光耦隔离输入,支持8路及以上等光耦隔离输出,6个及以上千兆网接口,8个及以上usb接口,2路全功能RS232,支持RS485和RS422切换,控制器支持24v供电模式,需提供软件代码。
★1.4检测用4K线扫相机1个,配置不低于:4K千兆网口彩色线阵相机4096像素千兆以太网口工业线阵,采用4096 × 2线CMOS Sensor,像元尺寸7um,动态范围是72dB,像素位深支持8bit、12bit,相机输出功率小于6W,相机噪声≤8.5,工作温度范围在-10~65℃,相机重量小于280g,相机接口M42,相机可调节增益范围1x to 8x,行业SEE参数标准:30 nJ / cm2,NEE行业参数标准:12 pJ/cm2,防光晕Anti-blooming:100 x Saturation,积分非线性Integral non-Linearity:1.5 % DN,支持行触发、帧触发以及行+帧触发等多种外触发模式,支持多相机同步采集。使用千兆以太网接口传输图像,可快速实时传输数据,行频最高可达12.5kHz支持图像无损压缩、脉冲宽度控制曝光,支持手动调节 Gamma校正、平场校正、LUT、黑电平调节等支持双向 I/O 接线 兼容 GigE Vision V2.0 协议及 GenICam 标准,该检测用系统含有线扫镜头镜头1个、成品线缆1个、视觉控制器1个、报警灯1个、显示器1个、线扫光源1个、授权卡2个、AI开发软件1个和具有通讯功能,需提供软件代码但AI算子除外。
▲1.5开发人员需熟练使用以下全部软件语言及框架:开发语言:c# ,c++ ,Python;容器相关:docker ,docker-compose,Kubernetes;框架相关:python 的相关库,python transformers,pytorch 套件,Vscode,前端框架 vue ,后端框架 .net8,深度学习需要安装 pytorch gpu版;环境依赖:Docker: 承载标注工具和模型训练环境;Ultralytics 镜像: 深度学习框架及模型库;LabelStudio 镜像: 数据标注工具;SQLServer数据库: 用于存储和管理数据;NVidia CUDA;Tool: 用于GPU加速计算;OnnxRuntime: 用于模型推理和优化;zlibwapi.dll: 结合OnnxRuntime使用,进行压缩和解压操作,训练脚本及模型优化开发,验收时需提供软件二次开发代码;通过训练模型和算法,具备检测0.01mm宽0.5mm长划痕、0.01mm凹坑及缺陷的能力,开发团队有可以演示的检测瑕疵异物的AI算法软件,不低于三种形式的应用。传统算法及深度学习算法检测准确率99%及以上,深度学习算法检测节拍均保证在每次检测200毫秒以内完成,深度学习模型性能调试:素材训练达到400轮次时候,具备项目需求的性能,可以达到90%正确率。
▲1.6零件视觉检测辅助自动化机电装置1套,设备尺寸:长≥1500mm,宽≥1000mm,高≥1600mm。
▲1.7自动化检测装置含伺服驱动机构,含有相机装置高精度直线行走和工件高精度回转运动机构,以保证测试精度和稳定性,提高测试效率。
1.8机械装置包括工作台、丝杠行走装置,工件转动装置和工件夹紧装置等组成;可控制相机装置的直线行进速度和步进距离,应小于相机视野所覆盖的宽度并保证其有效视野。在探测过程中可控制工件夹紧装置的旋转速度和步进转角,保证满足本方案产品参数中提到的工件规格检测要求。提供不低于3个参考测试用件。
1.9电气控制系统使用PLC作整个过程控制,所有电控系统控制器、元器件、触控屏均采用正规厂商产品。自控系统所有控制集中在一个电控面板上,操作直观简单。
1.10整套系统配置有安全紧急开关,提供机械三维数模图,电气部分提供电气柜电气接线图。
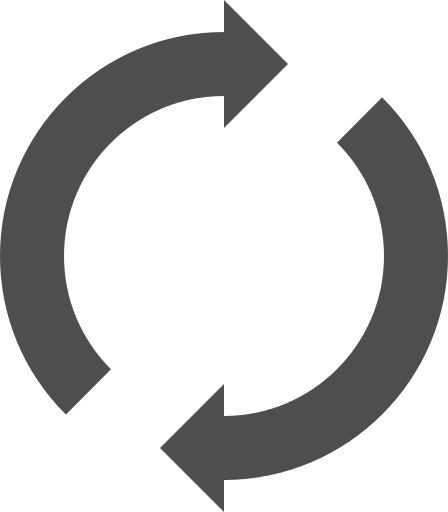