贵公司:
****2024.****.6二分公司生产需采购无缝钢管一批,详见下表清单及技术要求
采购清单:
序号 | 名称 | 规格型号 | 单位 | 数量 | 计 划 单 号 | 备注 |
1 | 无缝钢管 | Φ180×10mm 材质:L360Q | 米 | 4600 | 具体要求见技术规范书 | |
2 | 合计 |
钢管长度按照购方订货要求交货,要求至少 90%的钢管的长度为 11.0m~12.2m,其余应大于 8m。以上标的物数量按照需方项目工程实际需要大于等于上述数量供货,偏差不大于10米范围内,具体结算按实际供货数量按上述单价结算。
1.1无缝钢管主要技术参数及有关要求:详见第四章中技术规范书;
1)、供方应严格按照需方技术规范书要求和国家、部(专业)有关标准生产、检验和交货;
2)、无缝钢管的质量、规格和性能均严格相应按照附件技术规范书要求并相应按照国家相关标准及高于国家标准生产、检验和交货;
1.2询比内容:详见采购清单。
1.3交货地点:淮****公司仓库或需方指定地点。
1.4交货期要求:合同生效后45个日历日内报价人必须具备供货条件,在接到通知后3日历日内将全部钢材运抵指定地点。
1.5 报价范围:报价应包括本次询价范围内所需全部无缝钢管的包装费、运杂费(含运抵询价人工地现场卸货费)、保险费及询价人认为需要的其它费用等;
报价须知:
1、请贵单位于2024年 12月 16日14:00点前将报价文件上传至该电子采购平台(网址:http://cgpt.****.com),上述网站没有注册会员的单位请将报价文件盖章后在截止时间前扫描发至专用接收邮箱(****@163.com,邮件标题格式如下:物资名称+采购员+报价单位)。报价文件必须详细注明所报价产品型号规格、交货期、单价、总价(含13%增值税的交货价,包括但不限于设计费、包装费、运输费、卸货费、保险费、指导安装费、调试费、技术服务费、技术图纸资料费等其它一切费用)。
2、评审步骤:首先进行资格审查(详见附件一);其次进行符合性审查;最后进行评审(详见附件二)。
3、合同主要条款见附件三合同主要条款。
4、具体技术要求详见附件四技术标准和要求。
5、报价单位报价文件格式(详见附件五)。
6、报价时请注明制造标准及标准号。
7、所报产****公司设备配套合格使用。
8、
9、……
10、所有报价文件必须盖章后上传,否则视为无效报价。
联系人:谢旭东
联系电话:138****4822
地 址:**省**市**区井神路1号 邮 编:223200
****采供中心
2024年12月9日
附件一:资格审查程序
(一)本次资格审查采用合格制,各报价单位只有满足资格审查必要合格条件后,方可参加商务标的评审。
(二)评委按下表所列的资格审查必要合格条件,对各投选人递交的资格审查资料进行评审。
资格审查的合格条件
序号 | 资格审查必要合格条件 | 具体内容 | 备注 |
1 | 报价人必须具有独立法人资格(提供加载有统一社会信用代码的营业执照复印件,原件备查)) | 提供加盖公章的营业执照复印件 | 在我公司合格供应商目录的报价人可免予提供 |
2 | 报价人法定代表人授权委托书。 | 提供加盖公章的法定代表人授权委托书原件 | 在我公司合格供应商目录的报价人可免予提供 |
3 | 报价人2021年1月1日起至2023年12月31日止(以合同签订时间)具有单项合同销售金额达到人民币100万元及以上的钢材销售业绩合同5份。 | 提供加盖公章的合同复印件 | 在我公司合格供应商目录有类似业绩的报价人可免予提供 |
注:1、本次询价,报价人必须对询价的全部内容进行投标;否则,询价人不予接受。
2、本项目不接受联合体报价。
3、钢材制造商:****集团有限公司、****公司、******公司、****公司、****公司、****公司或相当于同档次质量品牌制造商,报价人如果是代理商,报价文件中必须提供相应制造商针对该批标的钢管材料可追溯的有效授权函。
注:以上材料必须提供,否则将导致废标。
附件二、评标办法及评分细则
详细评审和说明
本次询价,采取综合评估法进行详细评审,并采取打分的方法衡量报价文件是否最大限度地满足询价文件中规定的各项评价标准,满分为100分。评标委员会从以下几方面对报价文件进行详细评审和打分,并根据总得分高低进行排名,推荐中标候选人,详细评标办法如下:
1、报价价格的合理性,主要对报价价格进行评价(满分96分)
以经评审的各报价人的最终报价的平均值作为基准价,得满分96分。各报价人经评审的最终报价与基准相比每高1%扣1分,不足1%部份按内插法计算,小数点保留两位;各报价人经评审的最终报价低于基准价的不扣分(各报价人经评审的最终报价明显不合理的,****委员会初审后按无效投标予以否决处理)。
2 、技术业绩部分(满分2分)
2.1 .1报价人提供自2021年1月1日起至2023年12月31日止(以合同签订时间为准)具有单项合同销售金额(销售金额以合同对应的增值税发票金额合计累计值为准)达到人民币100万元及以上的与本次招标钢材相同或相近参数的销售业绩进行打分:提供5份及以上10个以下合格业绩的,得1分;提供10份及以上合格业绩的得2分。最高得2分。****公司钢材类合格供应商的业绩分满分)。
注:(1)、合同复印件和对应增值税发票复印件必须加盖公章(原件备查),否则不得分;(2)、必须同时提供合同复印件和对应增值税发票复印件,仅提供一项不得分。
3.3 商务部分(满分2分)
3.3.1售后服务好的(包括响应时间、服务内容等),得2分。****公司钢材类合格供应商的售后服务满分)。
4、对违反国家政策和利益的报价文件,****小组有权决定废标,并拒绝提供任何解释。
5、报价单必须加盖公章(未加盖公章视为无效报价)。
附件三:合同主要条款
****(以下简称需方)和 (此处填写供方单位名称) (以下简称供方)就(此处填写产品或钢材名称) 的设计、制造、供应、服务等事宜进行充分协商后一致同意签订本合同,下列文件是构成本合同的组成部分,均具有合同应有的法律效力,如有说法不一,以排列在前为准:
(一)本合同书及履行过程中双方协商一致签订的补充协议
(二)技术协议
(三)中标通知书
(四)招标文件(招标编号: )
(五)投标须知
(六)招标补充通知
(七)投标书澄清
(八)投标书(含投标函、报价表、投标方案等)
(九)构成合同的其它文件
本合同的具体条款如下:
一、供货范围及技术要求
(一)标的物:
(二)型号规格、数量;
二、技术及质量要求:
三、合同价格
(一)本合同总价为人民币万元(大写:元整)。
(二)本合同价格为含13%增值税的交货价,包括但不限于设计费、包装费、运输费、卸货费、保险费、指导安装费、调试费、技术服务费、技术图纸资料费等其它一切费用。
四、付款规定:
****银行汇票、承兑或电汇承付方式结算。
(一)合同生效后一周内需方收到供方开出的合同总价的10%的履约保函或履约保证金(履约保函或履约保证金的有效期到全部钢材运至需方现场并经安装调试正常运行168小时后或货到需方现场经需方初验合格后18个月[两者以先到为准])后,需方10个工作日内支付合同总价的 20 %,计人民币 万元(万元整)。
(二)本合同钢材全部运到需方现场,经需方初验全部合格后,需方再付合同总价的40% 计人民币万元(万元整)
(三);全部钢材安装调试完毕正常安全运行168小时全部验收合格或全部钢材到需方现场经需方初验合格后满6个月[两者以先到为准]、供方向需方提供合同总价的增值税专用发票(13%税率)后,需方向供方支付合同总价的30%,计人民币 万元( 万元整)。
(四)合同总价的10%作为质保金,待质保期满(质保期为全部钢材安装调试验收合格且正常运行168小时经需方验收合格后12个月或货到需方现场经需方初验合格后18个月内[两者以先到为准]),无质量问题,一次付清(无息)。有质量问题时,需方暂扣质保金直至供方修复好钢材缺陷并赔偿需方经济损失;有质量问题,一次性给需方造成经济损失达到合同总价的2.5%以上时或累计经济损失超过合同总价的5%时,需方不予支付质保金,供方同时须承担修复好钢材的责任,如质保金不能弥补给需方造成的经济损失,供方还应继续赔偿需方经济损失。
五、交货期和收货人、交货地点:
(一)本合同钢材交货时间:合同生效后 个日历日内供方必须具备供货条件,在接到需方通知后3日内将全部钢材运抵需方或需方书面形式指定地点 (如因需方原因需推迟交货期,则需方应提前以书面形式通知供方)。供方必须在需方书面形式通知后48小时内上门进行指导安装、调试等技术服务,如逾期不上门进行指导安装、调试等技术服务的,视为延期交付,按本合同第十条执行。
(二)交货地点:**省**市**区石塘镇盐矿所在地或需方指定地点。
(三)运输方式:供方送货上门;运费由供方承担,到达交货地点后负责卸货,由需方提供协助。
(四)收货人: 。
(五)合同履行地:**省**市**区华西路18号.
六、需方的权利和责任
(一)在合同交货期内,需方有权督促供方履行本合同的各项条款,督促供方保质、保量、按期交货。
(二)为了便于了解(此处填写产品或钢材名称) 的制造情况,在制造过程中,供方在项目试验前一周内应当通知需方,需方有权派员参加有关项目试验。
(三)供方按合同规定完成有关工作后,需方应按合同规定,及时向供方支付货款。
(四)在(此处填写产品或钢材名称) 制造过程中,需方根据需要有权派人到制造现场监造,包括材质、牌号、供应商、外协方等。
(五)在(此处填写产品或钢材名称) 制造后期,需方有权派人到供方现场,以便熟悉掌握有关组装工艺,供方需提供有关方便。
(六)如因需方原因推迟交货期,则需方以书面形式通知供方。
七、供方的权利和责任
(一)供方应按合同中明确的(此处填写产品或钢材名称) 供货范围,详细技术要求及供货资料,保质保量按期供货。
(二)供方所供的(此处填写产品或钢材名称) ,必须是确保整体性能优质的钢材,并保证全部钢材质量和性能。
(三)供方应按合同规定按时提供资料和图纸,并对其正确、可靠、成套、完整、清晰负责。出厂检验报告、合格证或质量证明文件应在随机文件中提供。
(四)供方所供钢材应切实做到不合格、不配套的钢材不准出厂。在质量保证期内,钢材因缺陷、制造、调试、材料、技术服务等问题产生故障,供方应在48小时内负责修复或更换全新的符合质量合格要求的(修复或更换的部分质保期重新计算),并赔偿由此造成的需方全部损失,如48小时内不能负责修复或更换全新的符合质量合格要求的钢材,需方有权退货,供方退还已付全部费用及利息,并赔偿由此造成的需方全部损失。质保期后,供方负责维修,维修及配件均以最优惠的价格供应。
(五)供方所供(此处填写产品或钢材名称) 应按合同有关规定进行包装,如因包装不善所产生的缺损,供方在确保交货期的前提下负责更换及补供,并承担因此而发生的费用。
(六)供方应按合同规定的交货期交货,若因运输途中造成产品缺损时,供方应及时増供缺损件,且交货期不予顺延。
(七)本合同质量保证期限为:全部钢材安装调试验收合格且正常运行168小时经需方验收合格后12个月或货到需方现场经需方初验合格后18个月内[两者以先到为准]。在质保期内,供方对钢材质量实行“三包”,即包修、包换、包退,费用由供方承担。
(八)货物交付(指供方将全部货物运到需方指定现场初验全部合格并经安装调试完毕正常安全运行168小时全部验收合格后,视为交付)给需方前的保险由供方负责,保险范围应包括但不限于供方装运的全部货物及运输过程中的第三者责任险。如交付给需方前发生与本合同有关的一切货物、设施损失损坏及人员伤亡等事故,责任由供方承担。
(九)与本合同有关的一切税费均由供方负担。
八、钢材验收:
(一)为确保本合同(此处填写产品或钢材名称) 的质量、性能及成套性,出厂前须按国家的有关标准和规定进行严格的检查或试验(需方有权参与出厂检验),确保钢材符合合同的要求。供方应保证产品是全新、未使用过的,完全符合合同规定的质量、规格和性能的要求,所提供的产品不侵犯任何第三方专利权且保证任何第三方不得对货物主张任何权利,如发生此类纠纷,由供方承担一切责任。给需方方造成损失的,还应当负责赔偿。供方并保证其产品经正确安装、正常运转和保养在其使用寿命内应具有良好的性能,如在产品的合格使用期内因产品的质量问题造成的财产损失和安全问题均由供方承担责任,给第三人和需方造成损失、损害的,供方应当承担一切法律责任和赔偿责任。
(二)初步检验为开箱检验,开箱检验包括对产品的型号规格、尺寸、数量、 外观质量、出厂日期、随机抽样检验产品质量等方面的检验,且开箱检验合格不代表需方对产品内在质量瑕疵的认可,初步检验合格后,货物的保管责任及货物的损坏或缺失等风险仍由供方承担。
启封、开箱初步检验时,需方应提前通知供方,供方得到通知后应在3天内到达现场。双方共同开箱检验,并做好检验记录。如供方未在规定时间到达现场,需方可单独开箱清点,缺损件应由供方负责。需方的检验确认并不免除供方因提供的钢材质量瑕疵而承担的责任。若供方提供的货物不符合本合同约定,需方有权要求供方提供符合合同约定的货物,且交货时间不予顺延。
(三)需方有权在本合同钢材质保期内对本合同钢材质量提出异议。
九、包装要求:
(一)供方按国家有关规定切实做好产品的包装,应标明收货单位、到站名称、箱号、毛重、外形尺寸等,如有特殊要求应标明记号。
(二)供方在装箱时应有严格按照装箱清单装箱。
(三)包装标准:
按照技术条件标准进行包装。
十、违约责任:
(一)供方应按本合同按期交付全部产品,如因供方原因造成产品延迟交付,每延迟一天,供方按每天( 此处填写金额为:合同总价的1%)赔偿需方损失。如供方延迟交付超过20天,需方有权解除合同,供方应退还需方已支付的全部款项并按合同总价款的20%承担违约责任。如违约金不能弥补给需方造成的经济损失,供方还应继续赔偿需方经济损失。如发生不可抗力,供方应当立刻通知需方。如延期30天,经双方协商无效,需方有权解除合同,供方应返还需方已支付的全部款项,并承担已付合****银行同期贷款利息计算)。
(二)在质量保证期内,在外部条件满足的情况下,其运行指标达不到规定技术要求,扣除质保金。一项以上(含一项)运行指标超过技术协议规定的最大偏离值,供方免费检修整改并赔偿全部经济损失。
(三)供方每延期一天支付履约保证金的,按合同总价的0.6%向需方支付违约金,如超过(此处填写:不超过交货期三分之一的天数)日,需方有权解除合同,供方向需方支付合同价款10%的违约金并且供方赔偿需方的损失。
(四)供方不能履行其在本合同项下任何一项义务的情况下,即构成违约,需方方有权从履约保证金中得到补偿。
(五)合同的任何一方没有履行或无故擅自更改本合同内容,应承担其相应违约责任;如因不可抗力致使合同任何一方不能履行或部分不能履行本合同有关条款方面产生的纠纷,双方在本合同中未有约定的,均按《中华人民**国民法典》有关规定执行。
十一、合同修改:
供、需方对合同正文、附件中的技术协议或其它附件条文需进行修改补充时,在协商一致后,签署补充协议书,合同双方法定代表人或委托代理人签字并加盖单位印章后即为生效。
十二、合同生效及其它:
(一)本合同及合同附件经需、供方法定代表人或委托代理人签字并加盖单位公章或单位合同专用章后即为生效。
(二)本合同正文一式陆份,需方执肆份,供方执贰份。
(三)供、需双方在履行本合同的过程中,如发生争议,应通过**协商解决,协商不成时,向需方********法院起诉。
(四)本合同货物在运输、卸货过程中的一切安全责任由供方承担;
(五)本合同签订后按买受人生产实际需要量,根据本合同单价采购和入账。
附件四:技术标准和要求
****
****公司无缝钢管(Φ180×10mm L360Q)
及相关服务
技术规范书
2024年12月
目 录
1 范围 3
2 一致性 3
4 术语和定义 5
6 制造要求 5
7 性能要求 7
9 外观检查 16
10 无损检验 17
11 标志和保护性涂层 17
13 记录保存 20
14 钢管装运 20
15 钢管堆放 21
16 管端保护 21
17 工厂资质和质量控制 22
本技术规格书规定采卤车间用无缝钢管的化学成分、显微组织、力学性能、静水压试验、几何尺寸、工艺质量、无损检测、工厂资质认证和质量控制等要求。
本技术规格书选用的钢管等级为 GB/T 9711-2017 PSL2 级产品.钢管钢级:GB/T 9711 L360Q
设计压力:8MPa;
钢管规格:Φ180×10mm;
本技术规格书适用于采卤车间更新原有无缝钢管的制造、采购及验收。
在本技术规格书中,数据以 SI 单位制表示。
下列文件对于本技术规格书的使用是不可缺少的,也是对 GB/T 9711 的补充。凡是注日期的引用文件,仅注日期的版本适用于本技术规格书。凡是不注日期的引用文件,其最新版本(包括任何修订内容)适用于本技术规格书。
GB/T 6394 金属平均晶粒度测定方法
GB/T 5777 无缝钢管超声波探伤检验方法
GB/T 7735 钢管涡流探伤检验方法
GB/T 9445 无损检测人员资格鉴定与认证
GB/T 12606 钢管漏磁探伤方法
GB/T 13298 金属显微组织检验方法
GB/T 13299 钢的显微组织评定方法
GB/T 10561 钢中非金属夹杂物含量的测定标准评级图显微检验法
GB/T 19001 质量管理体系要求
ISO 10893-2 钢管的无损检测 第 2 部分:无缝钢管和焊接(埋弧焊除外)钢管缺陷的自动涡流检测
ISO 10893-3 钢管的无损检测 第 3 部分:铁磁性无缝钢管和焊接(埋弧焊除外)钢管纵横向缺陷的全周向自动漏磁检测
ISO 10893-4 钢管的无损检测 第 4 部分:无缝钢管和焊接钢管表面缺陷的渗透检测
ISO 10893-5 钢管的无损检测 第 5 部分:铁磁性无缝钢管和焊接钢管表面缺陷的磁粉检测
ISO 10893-8 钢管的无损检测 第 8 部分:无缝钢管和焊接钢管分层缺陷的自动超声检测
ISO 10893-10 钢管的无损检测 第 10 部分:无缝钢管和焊接(埋弧焊除外)钢管纵横向缺陷的全周向自动超声检测
ISO 10893-12 钢管的无损检测 第 12 部分:无缝钢管和焊接(埋弧焊除外)钢管全周向超声波厚度检测
ASNT SNT-TC-1A 无损检测人员资格鉴定与认证推荐实施方法(Recommended practice for qualification of nondestructive examination personnel)
ASTM A370 钢产品力学性能试验的标准试验方法和定义(Standard test methods and definitions for mechanical testing of steel products)
ASTM E3 金相试样制备标准指南(Standard Guide for Preparation of Metallographic Specimens)
ASTM A435 钢板直射法超声检验规范(Standard specification for straight-beam ultrasonic examination of steel plates)
ASTM A578 特殊用途普通钢板和复合钢板直射法超声检验标准规范(Standard Specification for Straight-Beam Ultrasonic Examination of Plain and Clad Steel Plates for Special Applications)
ASTM A751 钢产品化学分析用标准试验方法、 作法和术语(Standard test methods,practices,and terminology for chemical analysis of steel products)
ASTM A1038 超声波接触阻抗法便携式硬度仪测试硬度的标准作法(Standard Practice for Portable Hardness Testing by the Ultrasonic Contact Impedance Method)
ASTM E94 射线检验标准指南(Standard Guide for Radiographic Examination)
ASTM E110 便携式硬度仪测试金属材料压痕硬度的标准方法(Standard Test Method for Indentation Hardness of Metallic Materials by Portable Hardness Testers)
ASTM E112 金属平均晶粒度的测定方法(Standard Test Methods for Determining Average Grain Size)
ASTM E45 钢中夹杂物含量评定的标准试验方法( Standard Test Methods for Determining the Inclusion Content of Steel)
ASTM E92 金属材料维氏硬度和努氏硬度标准试验方法(Standard Test Methods for Vickers Hardness and Knoop Hardness of Metallic Materials)
ASTM E1268 显微结构带状物等级或取向的评定方法( Standard Practice for Assessing the Degree of Banding or Orientation of Microstructures)
ASTM E165 液 体 渗 透 标 准 试 验 方 法 (Standard Practice for Liquid Penetrant Examination for General Industry)
ASTM E213 金属管超声检验标准作法(Standard Practice for Ultrasonic Testing of Metal Pipe and Tubing)
ASTM E273 焊管焊接焊接区超声检验标准作法(Standard Practice for Ultrasonic Testing of the Weld Zone of Welded Pipe and Tubing)
ASTM E709 磁粉检验标准指南 (Standard Guide for Magnetic Particle Testing)
GB/T 9711 界定的以及下列术语和定义适用于本文件。
4.1 校准
将仪器调整至一已知的基础基准,通常可向国家标准技术机构或相当机构溯源。
4.2 车载量
从制管厂发运的一节火车车厢所装载钢管的重量。
4.3 熔炼批
一次熔炼工艺一次循环所生产的金属。
4.4 熔炼分析
由钢材生产方报告的代表一熔炼批钢的化学成分分析。
4.5 标定
调整无损检测仪器至所选的对比标准值。
参见附录 A
钢管交货状态可为成型正火、正火状态或调质状态。
钢管不允许采用冷扩管。制造厂应根据本厂的技术设备,将先进的、成熟的钢管制造工艺报业主审查。制造无缝钢管用连铸坯、钢锭、轧坯不应有任何补焊,制管过程中
也不允许进行补焊。
6.2.1 无缝钢管用连铸坯、钢锭、轧坯应为吹氧转炉或电炉冶炼并经炉外精炼的细晶粒纯净镇静钢。钢管的晶粒度评定按 GB/T 6394(或 ASME E112)进行,管体晶粒度应为 7级或更细。钢中 A、B、C、D 类非金属夹杂物级别限制见表 1。
表 1 非金属夹杂物级别限定
A | B | C | D | ||||
薄 | 厚 | 薄 | 厚 | 薄 | 厚 | 薄 | 厚 |
≤2.0 | ≤2.0 | ≤2.0 | ≤2.0 | ≤2.0 | ≤2.0 | ≤2.0 | ≤2.0 |
6.2.2 制造无缝钢管用连铸坯、钢锭、轧坯不应有任何补焊,制管过程中也不允许进行补焊。不允许提供对接管。
钢管可进行热处理。
****制造厂(商)应建立并遵守文化程序,以保持所有钢管的炉批标识和试验批标识。该程序应能将任一根钢管追溯至相应的试验批和相关的化学成分和力学性能试验结果。
制造商应保持钢管表面清洁,钢管表面上应无油脂、过多的锈、腐蚀物等。钢管表面不得受 Cu、Sn、Pb、Zn 等低熔点金属污染。
6.6.1 制造商按本技术规格书生产无缝钢管之前,应提交制管工艺的详细说明(MPS 文件)供购方审查认可。
6.6.2 “购货合同”签订后,制造商如果对按 6.6.1 提交的文件有变动,应立即报告购方认可。如果不能按时报告并得到认可,则被视为拒绝执行合同的依据。
6.6.3 制造商提供的所有制造工艺文件需要得到购方或购方委托人的签字后方可认为有效,否则购方有权拒收制造商提供的所有产品。
钢管正式生产前应按附录 B 的要求进行首批检验及首批出证试验。首批检验及首批出证试验合格后,方可进行正式生产。
钢管应按附录 C 的规定进行钢管生产过程控制试验。
钢中 A、B、C、D 类非金属夹杂物级别限定如表 1 所示。钢管显微组织检验按 GB/T 13298 进行,晶粒度评定按 ASTM E112(或 GB/T 6394)或购方与制造商商定的其它方法进行,夹杂物级别按 ASTM E45 方法 A(或 GB/T 10561 方法 A)进行检验,或按购方与制造商协商的其它方法进行。
显微组织检验应在首批检验及首批出证试验、生产过程控制试验以及必要时进行,晶粒度、夹杂物检验应每 1 检验批进行 1 次。特殊情况下,由购方与制造商双方协商确定。
7.2.1 按本技术规格书供应的钢管的化学成分,产品分析结果应符合表2要求。如制造商选择推荐范围以外的其他化学成分,应经业主批准,并通过钢管评价试验和环焊工艺评定。
表 2 产品分析要求(wt. %)
元素 | 根据熔炼分析和产品分析 的最大质量分数(%) | 最大碳当量 a(%) | |
Cb | 0.20 | CEIIW | CEPcm |
Si | 0.45 | 0.38 | 0.20 |
Mnb | 1.40 | ||
P | 0.020 | ||
S | 0.010 | ||
V | 0.10 | ||
Nb | 0.05 | ||
Ti | 0.04 | ||
其它 d | c | ||
a 如果碳的质量分数大于0.12%,则CEIIW极限适用;如果碳的质量分数小于等于0.12%,则CEPcm 极限适用。 b 碳含量比规定最大质量分数每降低0.01%,则允许锰含量比规定最大质量分数增加0.05%,最大锰含量不得超过 1.65%。 c 除非另有协议,铜的最大含量为0.50%,镍的最大含量为0.30%,铬的最大含量为0.30%,钼的最大含量为0.15%。 |
7.2.2 元素分析
每炉钢管应进行1次熔炼分析和2次产品分析,并提供报告。产品分****制造厂选择,可从成品钢管或拉伸试样上截取。
化学成分分析方法应按照ASTM A751的规定进行。钢中化学成分应符合9.2.2的要求。每次要求的化学分析至少应包括下列元素:
a) 碳、锰、磷、硫、铬、铌、铜、钼、镍、硅、钛和钒;
b) 硼:如果硼的熔炼分析结果小于 0.0005%,那么在产品分析中就无需包括硼元素的分析,在碳当量计算中可将硼含量视为 0;
c) 除脱氧之外的其它目的,在炼钢时添加的其它合金元素。
7.2.3 碳当量
对于产品分析中碳的质量分数等于或小于0.12%的钢管,钢管碳当量CEPcm 应按公式
(1)计算确定。
CE = C + Si + Mn + Cu + Ni + Cr + Mo + V + 5B
(1)
下载Pcm
30 20
20 60 20
15 10
对于产品分析中碳的质量分数大于 0.12%的钢管,碳当量 CEIIW 应按公式(2)计算确定
CE = C + Mn + (Cr + Mo + V) + (Ni + Cu)
(2)
IIW 6 5 15
式中化学元素符号表示质量分数。
7.3.1 总则
样品应从钢管上截取。拉伸试验、CVN 冲击试验和硬度试验用样品的截取和相应试样的制备应按适用的引用标准规定。
各种试验用样品和试样应按 GB/T 9711 的适用位置截取。
对于本章规定的任何力学试验,任一试样显示出与该力学试验意图无关的机加工缺陷或材料缺欠,无论是在试验前还是在试验后发现的,该试样可报废,并用从同一根钢管上截取的另一试样代替。
7.3.2 拉伸性能
7.3.2.1 拉伸性能要求
屈服强度应为试样标距长度内产生 0.5 %总伸长(用引伸计测定)时所需的拉伸应力。当需记录或报告伸长率时,如采用板状试样,记录或报告中应注明试样的公称宽度;如采用圆棒试样,应注明直径和标距长度;如采用全截面试样亦应予以注明。
钢管的拉伸性能应符合表 3 的要求。
表 3 拉伸试验要求
钢级 | 屈服强度 Rt0.5 MPa | 抗拉强度a Rm MPa | 最大屈强比 Rt0.5/Rm | 标距长度为 50 mm的最小伸长率 Af,min | ||
最小 | 最大 | 最小 | 最大 | |||
% | ||||||
L360Q | 360 | 500 | 460 | 660 | 0.90 | a |
a 规定最小伸长率Af,min应按下列公式计算确定: A0.2 Af,min = C xc U 0.9 式中: C——采用国际单位制为 1940; Axc——适用的拉伸试样横截面积,mm2,按下列方法确定: ——对于圆棒试样,直径为 12.5mm和 8.9 mm的试样为 130 mm2;直径为 6.4 mm的试样为 65 mm2; ——对于全截面试样,取a)485 mm2 和b)采用钢管规定外径和规定壁厚计算的试样横截面积两者中的较小者,圆整到最接近的 10mm2; ——对于条形试样,取a)485 mm2 和b)采用试样规定宽度和钢管规定壁厚计算的试样横截面积两者中的较小者,圆整到最接近的 10 mm2; U——规定最小抗拉强度,MPa。 b 对于要求纵向拉伸试验的钢管,其最大屈服强度应≤495MPa。 |
7.3.2.2 拉伸试验方法
7.3.2.2.1 一般要求
拉伸试验应按 ASTM A370 进行。
对于管体试验,应测定屈服强度、抗拉强度、屈强比和断裂后的伸长率。应报告标距长度为 50 mm 的断裂后伸长率。对于标距长度小于 50mm 的试样,应按 ASTM A370将所测量的断裂后伸长率换算为 50mm 内的伸长率。
拉伸试样不得热压平、人工时效或热处理。
7.3.2.2.2 拉伸试样
代表钢管全壁厚的矩形试样应按ASTM A370和GB/T 9711的图5所示截取,横向试样应压平。也可使用由未经压平的样品加工的圆棒试样。横向拉伸试验用圆棒试样直径应为GB/T 9711的表21所给值,由制造厂选择可使用相邻较大直径试样除外。
7.3.3 夏比冲击韧性
7.3.3.1 夏比冲击韧性要求
应对管体横向进行-10℃夏比 V 型缺口冲击试验。钢管管体的夏比冲击吸收能量应满足表 4 的要求。
表 4 PSL2 钢管管体的 CVN 吸收功要求
位置 | 钢级 | 夏比冲击断面剪切率(SA%) | 夏比冲击吸收能量 (10mm×10mm×55mm),J | |
单个试样最小值 | 三个试样平均值 | |||
管体横向 | L360Q/X52 Q | ≥70 | ≥85 | 单个试样最小值≥45三个试样平均值≥60 |
注: 1) 使用小尺寸试样时,所要求的最低平均(三个试样一组)冲击功应是全尺寸试样要求值乘以小尺寸试样规定厚度与全尺寸试样规定厚度之比,并将计算结果圆整到最接近的焦耳值。 |
7.3.3.2 夏比冲击试验
7.3.3.2.1 试验方法
试样应按 ASTM A370 制备,除非订单上规定了按 ISO 148-1 和所要求的冲头半径
(2mm 或 8mm)。
7.3.3.2.2 试样
试样应按 ASTM A370 制备,除非订单上规定了按 ISO 148-1。试样的缺口轴线应垂直于钢管表面。
7.3.4 硬度试验
7.3.4.1 硬度试验方法
硬度试验用试样应从钢管端部截取,试样尽可能按照 ISO 377 的规定制备。钢管硬度测试位置如图 1 所示。
图 1 无缝钢管硬度测试位置
无缝钢管硬度试验应按照 ASTM E92(维氏硬度试验方法)或 ASTM E18(洛氏硬度试验方法)的规定进行,由制造厂选择。有争议时,应采用维氏硬度试验方法。
当外观检验发现有可疑的硬块时,根据所采用的方法使用便携式硬度试验设备及分别符合 ASTM A1038 或 ASTM E110 的方法,按 ASTM A370 的要求进行硬度试验。
7.3.4.2 硬度试验要求
钢管管体的最大允许硬度值≤250HV10。
7.3.5 复验
如果代表一批钢管的化学成分或力学性能不合格,应按照GB/T 9711 规定进行复验。
7.4.1 静水压试验要求
每根钢管应由制造商做静水压试验。试验过程中整个管体无泄漏,试验后目视无形状的变化和管壁鼓起。
试验压力至少不低于 7.4.3 的规定。
试验压力下的保持时间应不小于 10 s。当环向应力达到规定最小屈服强度的 95%时,试验压力保持时间应不小于 15s。所有静水压试验应记录试验压力与时间曲线,且该记录应提交购方检验代表检查。
7.4.2 静水压试验机的校验
为保证每根钢管能在要求的试验压力下进行静水压试验,每台试验机应配备能记录每根钢管试验压力和试验保持时间的记录仪,或配备自动连锁装置,以防止在未满足试
验要求(试验压力和保持时间)前将钢管判为已试压合格钢管。静水压试验记录或记录曲线应****制造厂内检查。试验压力测量装置应在试验前 4 个月内,采用静载荷压力校准仪或等效设备校验,以后至少每周校准一次,每次爆管后也应校准一次,校准压力表时应通知业主代表。
7.4.3 试验压力
7.4.3.1 除 7.4.3.2、7.4.3.3 规定允许外,以兆帕表示的平端钢管的静水压试验压力 P 应采用公式(2)计算确定,结果圆整至最接近的 0.1MPa:
式中:
P = 2St
下载D
(2)
S——环向应力,MPa,等于钢管规定最小屈服强度的 95%;
t——规定壁厚,mm; D——规定外径,mm。
7.4.3.2 如果在静水压试验中采用了产生轴向压应力的端面密封堵头,当规定试验压力产生的环向应力超过了规定最小屈服强度的 90%时,则静水压试验压力 P(用 MPa 表示)可采用公式(3)计算确定,计算结果圆整至最邻近的 0.1MPa。
S - é PR AR ù
下载ê A ú
P = ê p ú
(3)
式中:
2t Ap
S——环向应力,MPa,等于钢管规定最小屈服强度的 95%;
PR——端面密封工作油缸内压,MPa; AR——端面密封工作油缸横截面积,mm2; Ap——管壁横截面积,mm2;
Al——钢管内孔横截面积,mm2; D——钢管的规定外径,mm; t——钢管的规定壁厚,mm。
7.4.3.3 当环向应力至少为规定最小屈服强度的 95%时,经协商,可用最小允许壁厚 t min
代替规定壁厚 t,以确定要求的试验压力(见 7.4.3.1 或 7.4.3.2 中的适用者)。
7.4.4 同一规格的钢管应抽取一根钢管进行静水压爆破试验,实际爆破压力值不应低于按公称尺寸和母材抗拉强度最小值计算得出的理论爆破压力值,若能提供近 3 年内同规格钢管的静水压爆破试验报告,则可不进行爆破试验。
7.5.1 制造商应提供检查工艺和检查人员的资格,并提交按 GB/T 19001 要求制订的有关文件供审查使用。
7.5.2 购方将****工厂,作为生产期间有关检查和验收等事务的代表。
7.5.3 购方代表认为有必要时将进行审核检查,确认是否符合本技术规格书要求。
7.5.4 制造商应允许购方审查制造商在生产****控制所作的所有试验报告和试样。
7.5.5 如果购方发现试验方法和检查方法存在问题,有权拒绝接受钢管的最终检查结果,直到满足本技术规格书为止。
7.5.6 如果钢管内外表面上沾有油脂、腐蚀物和低熔点金属污染,则购方将不接收这些钢管。钢管上的油脂\低熔点金属污染等可采用购方认可的办法予以除去。在进行清除异物的作业中,要保留熔炼炉次和钢管的编号。
7.5.7 购方授权的检查代表有权拒收不符合本技术规格书的任何钢管。
7.5.8 购方检验要求见附录 E。
钢管的检验频次及试样要求应符合表 8 的规定。
表 8 PSL2 钢管的检验频次及试样要求
代号 | 试验种类和要求 | 交货试验 要求选择a | 试验频次 | ||
a | 熔炼分析 | M | 1 次/熔炼批 | ||
b | 产品分析 | M | 2 次/熔炼批 | ||
c | 拉伸试验 | M | 钢管应按下列规定组批进行试验: ——同一熔炼炉次; ——同一生产工艺; ——同一规格; —— 不多于 100 根钢管。 每1 检验批进行1 次试 验 | 每次取样数量 1 | |
d | 夏比(V 型缺口)冲击试验 | M | 3 | ||
e | 金相检验 | 管体晶粒度、夹杂 物检验 | M | 每检验批1次 | |
显微组织 | 必要时 | 必要时进行 | |||
f | 硬度试验 | M | 每检验批1次 | ||
g | 静水压试验 | M | 每根钢管 | ||
a M表示强制性项目。 |
应按照购方订货合同规定的外径和壁厚供货。
8.2.1 检验频次
对钢管直径的测量,每 10 根钢管应至少测量一次,若发现一根钢管直径超标,则应对同一检验批的所有钢管逐根进行测量。
8.2.2 测量方法
钢管直径一般测量钢管外径。管端直径在距离管端100 mm范围内测量,管体直径在钢管长度的中部测量。直径采用外卡规、测径规或其它能通过某一截面测量实际直径的装置测量,****制造厂选择采用测径卷尺测量。
8.2.3 管端直径及管体直径要求
钢管管端直径及管体外径偏差为±0.5%D,最大不超过±1.6mm。购方有特殊要求时,按照订货要求执行。
8.3.1 检验频次
对管端椭圆度的测量,每 10 根钢管应至少测量一次;对于管体椭圆度,每班测量二次,开始时测量一根,中间测量一根。若发现一根钢管椭圆度超标,则应对同一检验批的所有钢管逐根进行测量。
8.3.2 测量方法
管端不圆度在距离管端 100mm 范围内测量,管体椭圆度在钢管长度的中部测量。
8.3.3 不圆度要求
钢管不圆度偏差应符合表 5 要求,购方有特殊要求时,按照订货要求执行。
表 5 钢管椭圆度偏差要求
位置 | 管端 | 管体 |
允许偏差 | 1.0%D | 2.0%D |
8.4.1 检验频次
每根钢管均应测量壁厚,以确定是否符合规定的要求。
8.4.2 测量方法
壁厚测量应采用机械卡尺或经校准、具有相应精度的超声波测厚仪。发生争议时以机械卡尺测量的结果为准。机械卡尺与钢管内表面接触的触杆端头应为球面。
8.4.3 要求
无缝钢管壁厚偏差应符合表 6。购方有特殊要求时,按照订货要求执行。
表 6 钢管壁厚偏差要求
钢管类型 | 钢管壁厚 T mm | 壁厚偏差 a mm |
SMLS | 12.7/14.3 | -10%t~+12.5%t |
a 购方可以对整批交货钢管的平均壁厚偏差提出要求,以控制钢管整体重量。 |
8.5.1 检验频次
钢管应逐根进行称重。
8.5.2 钢管计算重量
钢管计算重量按公式(1)确定。
式中:
WL=Wpe×L (1)
WL——1根长度为L的钢管的计算重量,单位为千克(kg); L——钢管长度,单位为米(m);
Wpe——钢管单位长度重量,单位为千克每米(kg/m),Wpe=0.024 66(D-t)t,
D和t分别为钢管规定外径和壁厚,单位为mm。
8.5.3 钢管重量偏差
单倍尺钢管:-3.5 %~+10 %;
装车批量:-1.75 %,装车批的最小重量为 18144 kg。
8.6.1 检验频次
每根钢管均应进行长度测量。
8.6.2 长度要求
钢管长度按照购方订货要求交货,要求至少 90%的钢管的长度为 11.0m~12.2m,其余应大于 8m。购方有特殊要求时,按照订货要求执行。
8.7.1 检验频次
直度一般每 20 根钢管至少测量 1 次,若发现一根钢管直度超标,则应对当班生产的所有钢管逐根进行直度测量。
8.7.2 测量方法
测量部位为钢管可能存在的最大弯曲处。测量可采用一根拉紧的细绳或金属丝沿钢管侧表面从钢管一端拉至另一端,测量拉紧的细绳或金属丝与钢管侧表面的最大距离。
8.7.3 偏差要求
钢管全长直度偏差不得超过钢管长度的 0.2%,局部直度应小于 3.0 mm/m。
8.8.1 坡口加工
除购方订货合同另有规定外,钢管管端应开坡口,坡口形式为单 V 型坡口,坡口尺寸为 30°±2.5°。以钢管轴线的垂线为基准测量,钝边尺寸为 1.6±0.4mm。
应测量钢管管端切斜,切斜不应超过 1.6 mm。
8.8.2 管端内锥角
所有钢管管端的内外棱边上不应有毛刺。
为清除管端内毛刺所形成的内锥角应符合表7 要求,以钢管的纵向轴线为基准测量。
表 7 无缝钢管最大内锥角要求
钢管规定壁厚 mm | 最大内锥角 ° |
12.7/14.3 | 7.0 |
每根钢管均应进行外观检查,以检查表面缺陷。对钢管所有内、外表面都应进行外观检查。表面检查采用目视检查,允许采用其它经证实具有检测表面缺陷能力的检查方法代替目视检查。
外观检查应由进行过检查和评定表面缺欠培训的人员,在充足的光线条件下进行。
所有钢管的内外表面应清洁光滑,不应有重皮、裂纹、结疤、折叠、气泡、夹杂等对使用有害的缺陷存在。
管端25mm范围内及坡口面上不允许存在分层,扩展到钢管表面、坡口面上的分层均视为缺陷。有这种缺陷的钢管应切除,直到去除这种分层为止。
管体的分层验收限值应符合附录D中D.3.4.2.3的规定。
钢管管体不得有深度超过 1 mm 的凹坑。凹坑深度是指凹陷的最低点与钢管原始轮廓延伸部分之间的距离。
不允许采用扩管、锤击等方法进行凹坑修补。超标凹坑的处理按照附录 D 中 D.5
规定执行。
钢管上存在的任何方向长度大于 50 mm,且硬度值超过 35HRC,345HV10 或
327HBW 的硬块,应判不合格。对不合格硬块应切除或整根钢管拒收。
钢管管体上深度小于公称壁厚 10%的缺欠按照以下方法处理:所有“能引起应力集中”的缺陷,如尖缺口、凿痕及划痕等应全部磨光,其剩余壁厚不得小于最小允许壁厚。所有孤立的“不致引起应力集中”的缺欠,如圆底痕,不必修磨便可验收。
无损检验应符合附录 D 的规定。
11.1.1 总要求
符合本部分要求的钢管,应由制造厂作标志。制造厂应在生产之前提供标记方法的文件,供购方认可。
钢管上的标志应符合下述规定外,还应符合中国石油装备产品包装相关标准的要求。
11.1.2 标志位置
除非合同上规定了特定位置,否则标记应:
在钢管外表面上,按 11.1.4 所列的顺序,从距钢管一端 450 mm~760 mm 之间的一点开始。
在钢管内表面上,从距钢管一端至少 100mm 的一点开始。
11.1.3 标志方式
采用模板漆印方法作标志,合同另有规定的除外。所要求的标记应永久性地且清晰地标记。
11.1.4 标志内容
标志内容除了下列内容外,还可增加购方要求的其它标志内容。
——制造厂名称或标识;
——标准号;
——规定外径;
——规定厚度;
——钢管钢级/钢号;
——产品规范等级(PSL2);
——钢管类型(SMLS);
——炉号、试验批号和管号;
——水压试验压力;
——钢管长度;
——制造日期;
——客户检验代表的标识(如果有)。
业主批准接收的化学成份超出推荐范围要求的钢管,应在钢管内表面距管端 150mm
处喷上与字体等高,长度约 200mm 的白色标识带。
11.1.5 标志内容 如表 8 所示。
表 8 钢管钢级标识及符号
钢管钢级 | 标识及符号 |
L360Q | 绿色 |
11.1.6 兼容标准的标志
附加标志包括兼容标准的标志,按照购方要求,允许加在本技术规格书的标志后。
11.1.7 长度标志
钢管长度应以米(m)为单位,并精确到 0.01m,购方另有要求时除外。
11.1.8 涂层管标记
对于随后要涂层的钢管,如经协商,标记可在涂****加工厂进行。在这种情况下,应确保可追溯性,如采用唯一的编号(单个钢管或熔炼批)。
11.1.9 特殊要求
应在钢管内外表面同时做标志。如要求附加标志或要求在特殊位置做标志、或采用特殊方法做标志应经双方协商同意。
11.2.1 一般情况下,管子表面不需要涂层保护。
11.2.2 经购方要求,在潮湿或其它腐蚀性环境下需要长时间存放的钢管,表面应进行涂层保护。
11.2.3 如果涂敷临时保护涂层,则涂层后标记应清晰可辨。
11.2.4 制作标志和保护性涂层的材料,不得采用油性、石油脂类或沥青类材料。
制造厂应向购方提供产品质量证明书,质量证明书应注明产品的生产、取样、试验及检验均按要求进行并满足本技术规格书及由此形成的数据单的要求。
通过电子数据交换(EDI)传输系统以印刷文件或以电子文件使用的材料试验报告、质量证明书或类似文件应与****工厂印制的副本具有同等效力。
质量证明书应由制造商授权的代理人签名,并在装货发运之前提交购方,证明书包括书面质量证明书和电子版质量证明书。质量证明书副本数量由购方和制造商在签定订货合同时协商决定。
制造厂应向购方提供至少包括下列内容的质量证明书:
——钢坯供应状态;
——钢管生产依据技术条件编号;
****规格及数量;
——材料的炉号/批号;
——材料的化学成分和碳当量;
——力学性能试验数据;
——最低静水压试验压力和稳压时间;
——无损检验的方法和结果;
——热处理的类型和温度(如果有的话);
——其它补充试验结果。
与质量证明书同时应提供该批交货钢管的详细清单,内容至少应包括每根钢管的管号、规格、炉号/批号、长度、重量、总长、总重等。
工厂应按照其质量管理体系要求,记录和保管全部文件、记录和证书。本技术条件要求保存的试验和检验记录见表 9。****制造厂保存,****制造厂购买之日起五年内,如购方有要求,制造厂应向购方提供这些记录:
a) 如经协商,其它方法的无损检验;
b) 无损检验人员资质;
c) 附录或订单中规定的任何其它试验的记录。
表9 保存的记录要求
化学性能 | 熔炼分析 |
产品分析 | |
力学性能试验 | 拉伸试验 |
夏比冲击试验 | |
硬度试验 | |
其它试验 | |
静水压试验 | 静水压试验机自动记录图表或电子记录储存方法 |
补充静水压试验 | |
尺寸检验 | |
外观检查 | |
无损检测 | 钢管检验的射线照相图像或拍片 |
其它方法的无损检验 | |
无损检验人员资质 | |
注:附录或订单中规定的任何其它试验的记录。 |
14.1 钢管装运前生产厂装运作业文件应首先报购方或其代表批准。
14.2 当制造厂负责装运钢管时,制造厂应制定装运程序并附有装载图,详细描述钢管在卡车、火车、驳船或远洋货轮上如何装置、保护和固定。装运设计方案应能防止管端损伤、擦伤、撞击和疲劳开裂。装运应符合公路、铁路等运输有关的法规、规范、标准和
推荐做法。
14.3 装运过程中不应造成钢管损伤和碰伤、局部受力疲劳、严重腐蚀,不应造成钢管标志无法识别和各种污染(铜污染、油污染等)。
14.4 钢管补充装运技术要求见表 10。
14.5 购方对钢管装运保护另有要求的,按照订货合同规定执行。
表 10 钢管补充装运技术要求
生产厂应给购方提供一份运输、装卸方法说明书,也包括管端保护、堆放、捆扎的程序 | |
和一份装运图,所有这些程序都应在交货之前提交购方认可。 | |
钢管吊装应采用经认可的管子吊钩,吊钩不得衬垫铜或用铜合金制作。 | |
搬运:在车间和发货场的搬运应采用尼龙吊带或带有软补垫(不允许用铜及其它低熔点 | |
金属或其合金)的吊勾或真空吸盘。制造商应向购方提交书面的搬运方法供购方认可。 | |
搬运时应防止碰撞损伤。 | |
钢管装运 | |
存放:制造商应提交准备采用的存放(堆放和固定钢管)的方法及其图纸供购方认可。 | |
成品钢管存放时,相邻钢管之间不应有金属与金属的接触,防止变形、损坏和腐蚀。 | |
装运:制造商应在装运之前提交完整的装运方法说明供认可之用。铁路运输时应符合API RP 5L1或其它等同、等效标准,海运时应符合API RP 5LW或其它等同、等效标准,公路运输时应符合API RP 5LT 或其它等同、等效标准。所提出的方法应包括必要的计算 方法并表示出堆放布置图、承重带位置、垫块和系紧链带等。在钢管与钢管之间,钢管 | |
与系紧链带之间或管子与隔板之间不应有直接的硬接触。卡车或拖车在装运钢管之前应 | |
予以清理。放置钢管的地板、舱壁的烂木板应更换,舱壁应与实木料覆盖。 |
15.1 ****工厂钢管堆放作业文件进行。
15.2 制造厂应采取有效的措施,以尽可能降低钢管的锈蚀速度。钢管****制造厂确定,应符合 HSE 有关规定。
15.3 钢管堆放基本原则:不应造成钢管几何尺寸超标;不应造成钢管明显的腐蚀;不应造成钢管标志无法识别;不应与不合格钢管混放;不应造成钢管污染(铜污染、油污染等)。
15.4 购方另有规定的,根据订货合同要求执行。
钢管管端应采用措施保护,具体形式可由双方协商确定。
17.1.1 钢管生产厂应具有国家****总局颁发的制造许可证(对国内制造企业),钢管生产厂应已经通过ISO质量体系认证或与之等效的质量体系认证。
17.1.2 钢管生产厂应具有生产同类钢管的经验与资质,生产钢管应经过专业石油管材检测机构的质量检验与评价。
17.2.1 制造厂应建立合理的质量管理体系并保证有效运行。
17.2.2 正式生产前,制造厂应建立本合同批钢管生产的质量控制程序文件和生产检验技术规范(MPS)等。
17.2.3 生产前应该按照 GB/T 9711 的要求进行制造工艺评定。
(资料性附录)
管道设计参数及数据单
使用本标准时,需要设计者确定的参数及数据单如下:
——工程名称;
——工程概况;
——环境条件;
——地区类别;
——输送介质;
——设计温度;
——工作压力;
——钢管参数:钢管类型、钢级、管径、壁厚;
——止裂韧性夏比冲击韧性指标(输气管道);
——防腐技术要求;
——其它;
——数据表(见表A.1)。
表A.1 管材、防腐统计表(可根据实际情况适当调整表格形式)
施工标段 | 行政区划 | 线路长度(km) | ||||||
一般线路 | 冷弯管 | 热煨弯管 | ||||||
钢管参数 (类型、钢级、口径、壁厚) | 钢管参数 | 钢管参数 | ||||||
防腐形式 (高温/常温、普通/加强) | 防腐形式 | 防腐形式 | ||||||
合计长度 | ||||||||
重量 | ||||||||
总长度 | ||||||||
总重量 |
B.1 总则
(规范性附录)
首批检验和首批出证试验
B.1.1 首批检验和首批出证试验应在购方代表或购方委托的监督人员在场的情况下进行。首批检验和首批出证试验样管应由购方代表或购方委托的监督人员在首次生产的成品钢管中抽取。
B.1.2 若首批检验和首批出证试验的结果不符合要求,则另取同炉双倍钢管进行复验。若复验合格,则首批检验和首批出证试验合格,若复验仍不合格,工厂可选择所有钢管报废或逐根进行试验,并根据合格与否进行验收;同时制造厂应改进工艺,重新进行首批检验,直到达到本标准要求,方可正式生产。
B.1.3 钢管制造工艺发生较大变化或者钢管出现重大质量问题时,制造商需要重新进行首批检验和首批出证试验。
B.2 首批检验
B.2.1 抽样
从首次生产的两个熔炼炉次的钢管中各抽取 5 根钢管。
B.2.2 检验和试验项目
抽取的 10 根钢管均应进行 f)、g)项目的检验;每炉各取 2 根钢管,每根均应进行 a)~e)项目的检验:每炉各取 1 根钢管,进行规定的最小屈服强度 100%的静水压试验 h)(其它钢管按正文中规定的压力进行水压试验)。静水压试验压力采用规定的外径和名义壁厚计算。如果静水压试验后,钢管的几何尺寸不符合技术条件的要求,则对同一熔炼炉次的紧后两根钢管进行上述相同的静水压试验:
a) 化学分析;
b) 拉伸试验(管体横向);
c) 夏比冲击(管体横向);
d) 维氏硬度;
e) 金相检验;
f) 外观质量及尺寸;
g) 无损检查;
h) 静水压试验。
B.3 首批出证试验
B.3.1 取样
由购方在已抽取的两个熔炼炉次钢管(各 5 根)中各随机抽取 1 根钢管进行钢管首批出证试验。对由购方抽取的 2 根焊管,进行 B.3 规定的所有项目的检验,并提供试验报告。
B.3.2 化学成分
B.3.2.1 熔炼分析
熔炼分析应提供报告。
B.3.2.2 产品分析
产品分析应在所抽取的钢管上进行。
B.3.3 尺寸及外观质量检查
取样之前,应围绕钢管圆周等分 8 点沿长度方向不大于 1000mm 间隔测量壁厚。同时测量钢管的直径、不圆度和磨削深度(如果有)。
B.3.4 钢管管体力学性能
B.3.4.1 试样的取向
按下列方向取样: a)管体纵向; b)管体横向。
B.3.4.2 拉伸试验
各取三个纵向、横向试样进行试验。每一个试样都应报告其屈服强度、拉伸强度、伸长率,并提供拉伸试验曲线。
B.3.4.3 夏比冲击试验
取纵向、横向试样进行试验,每个取向都应提交完整的断口剪切面积百分数和夏比冲击功的转变曲线。试验温度至少应包括下列温度点:20℃、0℃、-10℃、-20℃、
-40℃、-60℃。
B.3.5 晶粒尺寸
取样按 ASTM E112(或 GB/T 6394)或购方和制造商商定的其它方法进行晶粒度测量。
B.3.6 夹杂物
取纵向试样按 ASTM E45 方法 A(或 GB/T 10561 方法 A)进行非金属夹杂物的级别分析。
B.3.7 显微组织
取纵向试样按照 ASTM E1268(或 GB/T 13299)方法进行组织分析。
B.3.8 横向截面维氏硬度
按 7.3.4 的规定进行管体横截面硬度测试。
B.4 检验报告
制造商应向购方提交首批检验报告和首批出证试验报告。
C.1 总则
(规范性附录) 生产过程控制试验
C.1.1 制造商应按下述要求进行钢管生产过程控制试验,并提交试验报告:
a)钢管制造工艺发生变化时; b)钢管出现重大质量问题时;
c)同一制造工艺生产一定批量钢管(多于 2000 吨)后,则每 10000 吨钢管进行一次;
订货重量不是 10000 吨的整倍数时,则以 10000 吨圆整。钢管生产过程控制试验应在该制造期内规定时间间隔按时进行。
C.1.2 钢管生产过程控制试验结果不合格,制造商应及时报告购方,查明原因,同时应查明该不合格对其间(自上次合格控制试验到本次控制试验期间)所生产的全部产品的影响范围,并与购方协商处理,提出改进措施,重新评定合格后方可进行生产。
C.2 钢管生产过程控制试验
C.2.1 抽样和试验项目
制造商应在两个熔炼炉次的钢管中各抽取 1 根钢管分别进行C.2.2~C.2.8 中要求的所有试验。作为产品交付条件的试验或检验应符合相应要求,其它试验或检验数据或结果仅供参考。
制造商应在两个熔炼炉次的钢管中各抽取 5 根钢管进行静水压试验、无损探伤、尺寸和表面质量的检查。
C.2.2 化学成分
产品分析应在所抽取的钢管上进行。
C.2.3 钢管管体力学性能
C.2.3.1 试样的取向
按下列方向取样: a)管体纵向; b)管体横向。
C.2.3.2 拉伸试验
在管体纵向取两个试样进行试验,在管体横向取两个试样进行试验。每一个试样都应报告其屈服强度、拉伸强度、屈强比和伸长率。
C.2.3.3 夏比冲击试验
规定的每个取向都应提交断口剪切面积百分数和夏比吸收功的转变曲线。试验温度至少应包括下列温度点:20℃、0℃、-10℃、-20℃、-40℃、-60℃。
C.2.4 晶粒尺寸
取样按 ASTM E112 (或 GB/T6394)或购方和制造商商定的其它方法进行晶粒度测量。
C.2.5 夹杂物
非金属夹杂物的级别可用C.2.4 中所使用的试样按ASTM E45 方法A(或GB/T 10561
方法 A)进行评定。
C.2.6 显微组织
取样提****中心的组织。
C.2.7 横向截面维氏硬度
按 7.3.4 的规定进行管体横截面硬度测试。
D.1 人员资质评定
(规范性附录)无损检测
D.1.1 所有无损检测工作都要在 3 级人员负责的情况下进行,并且至少要由具有 2 级资格水平的人员完成,具有 1 级资格的人员可以在 2 级人员的监督下进行无损检测。
为保证钢管缺陷无损检测的有效性和可靠性,上岗从事手动、半自动和全自动无损检测人员以及对检验结果进行解释的无损检测人员,还应经购方委托的无损检测人员资格鉴定考核机构或经购方认可的专业无损检测人员资格鉴定考核机构,按照 GB/T 9445或 ISO 11484 或 ASNT SNT-TC-1A 或等效标准要求、油气管道用钢管专用无损检测方法技术和本技术规格书无损检测要求培训考核资格鉴定合格,取得相应等级资格证书后,方可上岗检测操作。已评定合格的检测人员如未从事该项无损检测工作超过 12 个月,其资格应重新评定。购方有权审查和验明有关操作人员的资质证书。
在制管过程中操作自动设备的无损检测人员,除了按上述要求取得资格证书外,还需具备检测设备故障处理以及设备标定的操作能力,同时具备在生产场地/现场条件下进行操作检验和进行缺陷尺寸及缺陷位置估算的能力证明。
D.2 检验标准
除本附录另有特殊规定,对于要求进行的无损检测(表面检查和壁厚检测除外)应按照下述标准或其它等效标准(需提供证明材料供购方认可)进行。
a) 电磁(漏磁)GB/T 12606 或ISO 10893-3 或ASTM E 570
b) 电磁(涡流)GB/T 7735 或ISO 10893-2 或ASTM E 309
c)超声波 GB/T 5777 或ISO 10893-10 或ISO 10893-8 或ISO 10893-12 或ASTM E213 或ASTM A435 或ASTM A 578。
d) 磁粉 ISO 10893-5 或ASTM E 709
e) 渗透 ISO 10893-4 或ASTM E 165
D.3 检验方法
D.3.1 管体无损检测
热处理和冷****管所要求的无损检测,应安排在热处理和冷扩径之后进行,但宜在切端头、加工坡口和管端定径之**行。具体检测要求如下:
a) 管体缺陷检测
无缝钢管应按照相关标准进行全管体纵向和横向缺陷的超声波检测。检测对比试块见表D.1;
b) 管体测厚
无缝钢管应进行超声波壁厚测量。无缝钢管应按照相关标准进行全圆周超声波壁厚检测,以证实符合适用的最小允许厚度要求。检验时覆盖范围应≥钢管表面的20%,或经协商,可规定更大的覆盖范围;
c) 管体分层检测
无缝钢管管体应按照相关标准,进行管体分层超声波检测。自动检测时覆盖范围应≥钢管表面的20%。
D.3.2 管端无损检测
若使用满足D.3.1 要求的自动超声波或电磁检测系统(由设备、操作程序以及人员组合构成)时,对未被自动检测系统覆盖的管端,至少应距管端300mm 范围内采用手动或半自动超声波或磁粉检查方法进行缺陷检查,否则应切除。
按照ISO 10893-8 规定的超声波方法检测,每根钢管管端50mm 区域内无分层缺陷。
D.3.3 检验有关文件要求
D.3.3.1在生产之前钢管制造企业应将所有无损检测方法和要求用书面方式提交给购方。 D.3.3.2所有无损检测都要有相应方法的无损检测操作规程和工艺卡。
D.3.3.3 制造企业应保存超声波检测每一根钢管的自动检测记录和每检验班自动标定检测记录至少5年;
D.3.3.4 所有无损检测结果应有正规报告并作为正式检验文件提交给购方。
D.3.4 检验方法通则
D.3.4.1 无缝钢管超声波或电磁检测 D.3.4.1.1设备
任何利用超声波或电磁原理,并能够连续不断地检验钢管外表面和内表面的自动检验设备均可使用。自动超声检测设备系统的有效性,应经中国石油授权的专业无损检测
人员或机构对其检测能力及其有效性进行评审,评定合格后,方可进行钢管制造检验。正常检验时,检验设备应采用对比标样进行标定,每工作班开始及以后每4 h至少进行一次,以证实检验设备及检验程序的有效性。
当按照D.3.4.1.3 的规定检验对比标样时,应调整设备,使其产生清晰的规定的指示信号。
自动超声波检测设备系统应配有喷标、声、光自动报警系统及缺陷自动记录装置。
D.3.4.1.2 超声波或电磁检测方法
按照ISO 10893-10、ISO 10893-3 或等效超声波或电磁检测标准规定执行。
D.3.4.1.3 超声波或电磁检测用对比标样
对比试块为校准无损检测设备比较方便的试块。这些对比试块的人工缺陷尺寸不应理解为设备系统可以发现的最小缺陷尺寸,对比试块或样管应选取和检验钢管相同的规格和材质,每个对比标样的外径与壁厚应在被检产品钢管规定偏差范围内,****制造厂视方便而定,对比标样应按照表D.1规定有一个或多个机械加工刻槽或一个或多个径向钻孔。
对比刻槽或钻孔之间应分开一段距离,以便足以产生分离的可辨别的信号。 对比标样应标识。对比刻槽或钻孔的尺寸和类型应按照文件化程序进行校验。不同级别油气输送管道用钢管人工缺陷的种类规定见表D.1。
D.3.4.1.4 仪器标定
制造厂应采用文件化的程序建立相应的超声波或电磁检验拒收界限,表C.1给出的相应对比刻槽或钻孔应能够在正常操作条件下被检出。仪器对刻槽或钻孔的检出能力应进行动态验证,采用****制造厂选择。验证时传感器和钢管表面之间所使用的移动速度应与成品钢管检验时所采用的速度一样。
应进行附加验证,验证设备对对比标样内表面和外表面的刻槽校准时产生的信号大于或等于用钻孔建立拒收界限的信号。
应采用对比标样对仪器进行标定,以证明仪器的有效性和检验程序的有效性。每班标定至少两次,在第一次标定完3~4小时后,进行第二次标定。仪器标定应在本班检测工作结束后,关掉仪器之**行确定。
当检验对比试块时,仪器应进行调整以产生明确的信号,此信号来自相应对比刻槽
或钻孔。
D.3.4.1.5 校验系统能力记录
制造厂应保留无损检测校验系统能力记录,以检出对比标样的刻槽或钻孔用来建立设备灵敏度试验的能力。
校验记录至少应包括下列标准值: a)覆盖区域计算(如扫查区域); b)校验预期壁厚的能力;
c) 可重复性;
d) 检测制管工艺产生的典型缺陷的探头布置方法;
e) 采用适用的无损检测方法检测在制造过程中出现的缺陷类型的证明资料; f)门限设定参数。
2)另外,制造厂应保留下列相关文件: a)无损检测系统操作规程;
b)无损检测设备说明书; c)无损检测人员资格信息;
d)在生产检测条件下,证明无损检测系统/操作能力的动态试验数据。 D.3.4.1.6验收极限
表D.2给出了由对比标样的刻槽或钻孔产生的验收极限信号的高度。
如果缺陷产生的信号大于表D.2中给出的验收极限信号的任何缺欠应判为缺陷。
表 D.1 对比用刻槽和钻孔制作要求
对比用刻槽和钻孔 | |||||||
刻槽位置 | 刻槽方向 | 深度 b mm | 刻槽尺寸 | 通孔直径 a mm | |||
外壁 | 内壁 | 纵向 | 横向 | 最大长度c | 最大宽度 | ||
mm | mm | ||||||
d | d | e | d | 5.0 | 50 | 1.0 | 1.6 |
注1: 刻槽为矩形或 V 形。 注2:对电磁检验,也许需要包括钢管外壁刻槽、内壁刻槽和通孔的对比标样。 a 通孔直径是以标准钻头尺寸为基础确定的,如果用刻槽建立拒收界限,不要求通孔。 b 深度用规定壁厚百分比表示。刻槽深度不需低于 0.3mm(0.012in)。深度允许偏差应为规定刻槽深度的±15%,或 ±0.05mm(0.002in),取较大者。 |
D.3.4.1.7超声波或电磁检测过程中观测到的缺陷的处理含缺陷的钢管应按照D.5规定的任何一种方法处置。
表 D.2 验收极限
刻槽类型 | 钻孔的尺寸(mm) | 合格极限信号(%) |
N5 | 1.6 | 100 |
D.3.4.2 分层超声波检查 D.3.4.2.1分层检查设备要求
任何利用超声波原理,并能够连续不断地检测钢管管体分层的超声波自动检验设备系统均可使用,自动化超声波检测系统应配有喷标及声、光自动报警系统,并具备记录功能。
探伤系统探头布局和探头扫查间距至少应覆盖管体表面的20%;可依照ISO 10893-8、ASTM A435 或等效标准规定选择扫查方式。
D.3.4.2.2 分层检查对比试块和检验方法
分层检查对比试块按照GB/T 9711标准要求执行,检测方法按照ASTM A435或等效超声波检测标准执行。
D.3.4.2.3 验收标准
验收标准的要求如下:
无缝钢管管端50mm范围内不允许存在分层,有这种分层缺陷的钢管应切除,直到除去这种分层为止;无缝钢管管体部位的分层限值按表D.3执行。
表 D.3 分层缺欠的验收标准
最大单个缺欠 | 考虑的最小缺欠尺寸 | 最大分布密度a | |||
面积 mm2 | 长度 mm | 面积 mm2 | 长度 mm | 宽度 mm | |
1000 | 无规定 | 300 | 35 | 8 | 10[每 1.0m×1.0m的正方形] |
注1:对一个大于最小缺欠尺寸的缺欠来说,均超出了表中给出的管体最小面积,最小长度,最小宽 度。 |
D.3.4.3 管体其它无损检测方法检查
凡能进行管体分层缺陷检查的其它有效的无损检测方法技术允许使用,但须经有资质的检测单位鉴定有效合格后方可使用
D.4剩磁测量要求
D.4.1 剩磁测量的要****制造厂内测量。
注:****制造厂后,钢管剩磁测量可能会受到测量程序以及钢管装运过程中及钢管发运后钢管状态的影响。
D.4.2 应对成品钢管的钝边或切斜的纵向磁场进行测量。
注:在管垛上测量视为无效。
D.4.3 应采用校准的霍尔效应高斯计或其它类型已校准的仪器测量剩磁。但有争议时,应以霍尔效应高斯计的测量为准。高斯计应按照准确性经验证的书面程序操作。
D.4.4 每班每4h应至少抽取一根钢管,对钢管两端进行测量。
D.4.5 应在任何一种利用磁场检测后、****制造厂装运**行钢管磁性测量。对测量剩磁后采用电磁设备搬运的钢管,应证实搬运方式不会产生超过D.4.6规定的剩磁。 D.4.6钢管每一端沿圆周方向每相距90°应读取一个读数。当采用霍尔效应高斯计或其它类型测量仪器测量时,4个读数的平均值应≤3.0mT(30Gs),且任一读数不应超过3.5mT
(35Gs)。
D.4.7 不满足D.4.6要求的任何钢管应视为有缺陷的钢管。除非D.4.8允许,有缺陷的钢管和最后一根合格钢管之间生产的所有钢管应逐根测量。
D.4.8 如钢管生产顺序有记录文件可查,可从有缺陷的钢管前面生产的那根钢管开始反向测量,直到至少3根连续生产的钢管符合要求为止。
注:不需要继续测量该3根合格钢管前生产的钢管。
D.4.9 有缺陷钢管后面生产的钢管应逐根测量,直至至少连续3根钢管符合要求。 D.4.10所有有缺陷钢管应进行全长退磁,并应进行测量直到至少连续3根钢管符合D.4.6的要求。
D.5缺陷钢管的处理 D.5.1总要求
含缺陷钢管的处理,除符合GB/T 9711的附录C规定外,还应符合下列补充规定。 D.5.2含缺陷钢管处理方法
含缺陷钢管处理应按下述一种方法处置:
a) 可以采用修磨方法去除的管体缺陷,修磨区域应与钢管轮廓平缓过渡。应采用磁粉或渗透的方法证实表面缺陷完全清除掉,修磨区域的壁厚应符合8.4.3的规定。
b) 缺陷不允许采用补焊的方式进行补焊。
c) 在本部分规定的长度范围内,应将有缺陷的管段切除。 d)整根钢管拒收。
D.5.3管体缺陷的处理
管体上的缺陷应按如下方法处理:所有能引起应力集中的缺陷,如尖缺口、凿痕及尖锐划伤等应全部磨光,其剩余壁厚应符合本标准的规定;否则,受影响的管段应切掉。所有孤立的“不致引起应力集中”的缺欠,如圆底痕,不必修磨便可验收。
(规范性附录)
购方检验
E.1 检验的通知
代表购方的检验人员要求进厂检验钢管或见证试验时,制造厂应合理地通知作业时间。
E.2工厂进出
在履行购方合同期间,代表购方的检验人员有权在用户合同生产正在进行的****制造厂与订购钢管生产有关的所有部门。制造厂应向检验人员提供尽可能适当的便利条件,使购方检验人员确信合同钢管是按照本部分制造的。所有****制造厂内进行(订货合同另有规定时除外),而且****工厂的作业应无不必要的干扰。
E.3符合性
制造厂有责任遵守本部分上述所有条款。购方可进行任何必要的调查,****制造厂满足本部分的所有要求,并可以拒收任何不符合本部分的任何材料。
E.4拒收
除另有规定外,****工厂的检验中或在随后的验收中发现有缺陷的材料,或在正常使用过程中证明有缺陷的材料,****制造厂。如果需要对材料进行破坏性试验,则被检明不符合本部分要求的任何产品应拒收。
附件五:报价单位报价文件格式
(报价单位需按照下列格式顺序制作报价文件,并加盖公章)
1、 报价单一览表。
序号 | 产品名称 | 规格型号 | 牌号商标 | 材质 | 单位 | 数量 | 单价 | 总金额 | 备注 |
1 | |||||||||
2 | |||||||||
3 | |||||||||
4 | |||||||||
5 | |||||||||
合计 |
2、按照附件二“资格审查的合格条件”内容依次提供相关材料。
3、技术/商务偏离表。(如有偏离,需提供下表。如无偏离或未提供偏离表,则视同为完全响应询价函)
(报价文件与询价函的偏离)
序号 | 询价函 | 报价文件 | 说 明 | ||
条目号 | 技术/商务条款 | 条目号 | 技术/商务条款 | ||
报价人承诺:除上表中的偏差外,完全响应询价函的其他条款。
报价人全称(盖章):
日期: 年 月 日
4、按评分标准和办法中要求的技术业绩、商务部分评分标准要求按顺序提交材料。
5、报价单位认为需要提供的其他材料。
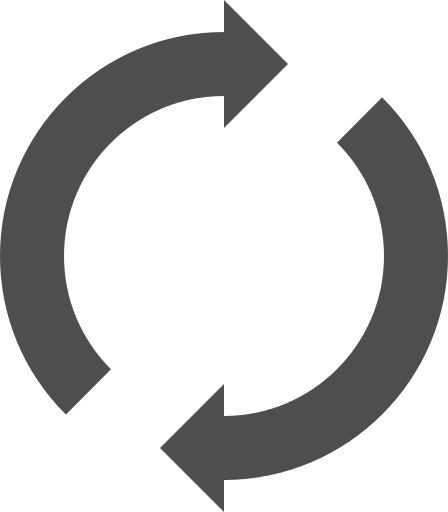