泊头市晟邦金属表面处理有限公司整体搬迁技术改造项目
1、建设项目基本信息
企业基本信息
**** | 建设单位代码类型:|
****0981MA081LNJ9T | 建设单位法人:孙树杰 |
孙连强 | 建设单位所在行政区划:**省**市**市 |
经济开发区 |
建设项目基本信息
****整体搬迁技术改造项目 | 项目代码:**** |
建设性质: | |
2021版本:067-金属表面处理及热处理加工 | 行业类别(国民经济代码):C3360-C3360-金属表面处理及热处理加工 |
建设地点: | **省**市**市 经济开发区 |
经度:116.643113 纬度: 38.050531 | ****机关:****审批局 |
环评批复时间: | 2024-09-05 |
泊审环书〔2024〕2号 | 本工程排污许可证编号:****0981MA081LNJ9T001P |
2024-09-30 | 项目实际总投资(万元):14000 |
500 | 运营单位名称:**** |
****0981MA081LNJ9T | 验收监测(调查)报告编制机构名称:**** |
****0981MA081LNJ9T | 验收监测单位:******公司 |
****0105MA3M4SGMXB | 竣工时间:2024-09-30 |
2024-09-30 | 调试结束时间:2024-10-02 |
2024-10-28 | 验收报告公开结束时间:2024-11-27 |
验收报告公开载体: | https://www.****.com/gs/ |
2、工程变动信息
项目性质
将现有一期2#镀锌生产线改为2#镀锡生产线,剩余原二期未建设的23条生产线分为两期建设(对23条生产线的镀种类型、电镀面积、原料用量和生产设备等进行技改调整,在技改工程中用二期、三期表述,分别对应备案中的二期一阶段、二期二阶段,不再赘述):二期建设15条电镀生产线,包括镀锌生产线5条、镀镍生产线2条、镀铬生产线2条、镀铜生产线2条、镀锡生产线4条,镀层面积合计为****965m2;三期建设8条电镀生产线,包括镀锌生产线4条、镀镍生产线1条、镀铬生产线2条、镀锡生产线1条,镀层面积合计为653471m2,二三期合计为****436m2。本项目建成后,企业年加工生产能力与原环评(《**市****公司整体搬迁项目》)审批文件一致,镀层面积合计****000m2。一期项目建成后,可实现年生产****965m2镀层面积。 | 实际建设情况:将现有一期2#镀锌生产线改为2#镀锡生产线,剩余原二期未建设的23条生产线分为两期建设(对23条生产线的镀种类型、电镀面积、原料用量和生产设备等进行技改调整,在技改工程中用二期、三期表述,分别对应备案中的二期一阶段、二期二阶段,不再赘述):二期建设15条电镀生产线,包括镀锌生产线5条、镀镍生产线2条、镀铬生产线2条、镀铜生产线2条、镀锡生产线4条,镀层面积合计为****965m2;三期建设8条电镀生产线,包括镀锌生产线4条、镀镍生产线1条、镀铬生产线2条、镀锡生产线1条,镀层面积合计为653471m2,二三期合计为****436m2。本项目建成后,企业年加工生产能力与原环评(《**市****公司整体搬迁项目》)审批文件一致,镀层面积合计****000m2。一期项目建成后,可实现年生产****965m2镀层面积。 |
无 | 是否属于重大变动:|
规模
一期项目建成后,可实现年生产****965m2镀层面积。 | 实际建设情况:一期项目建成后,可实现年生产****965m2镀层面积。 |
无 | 是否属于重大变动:|
生产工艺
镀锌工艺其过程主要包括前处理、镀覆处理和后处理,其具体工艺流程如下: (1)前处理 ①除油:镀件在机加工时都会使用油脂润滑,有时会留下很重的油污。所以,在电镀前要先除去这些油污。将镀件浸入加油碱性脱脂液的除油槽内,碱性脱脂液主要成分为 40~60g/LNaOH 、30~50g/LNa2CO3和3~5g/LNa3PO4 的混合溶液。工件上的油污与碱液发生皂化反应生成脂肪酸皂和甘油,典型反应方程式如下 R3(COO)3C3H5+3NaOH→3RCOONa+C3H5(OH)3 油脂氢氧化钠脂肪酸皂甘油生成的脂肪酸皂和甘油溶于水,在水的作用下离开金属表面,达到除油的目的。 ②水洗:除油处理的工件先送入水洗槽中进浸洗(水洗槽中的水来自喷头喷洗过程中产生的水),而后经喷头喷洗(采用新水)完成清洗作业,清洗掉工件表面残留的碱液,以利于下一工序操作。在此过程中会产生含碱废水(W1-1),属溢流式连续性排放,含有较高浓度的油污,收集后进入前处理废水处理装置。 除油过程中,除油槽定期清理,将上清液抽出重新配置后循环使用,底部废渣(S1-1)按危废处理。 ③酸洗:将除油并冲洗干净的工件浸入酸洗槽中,利用4~6%的 HC1水溶液,在常温条件下浸洗10~20min,去除工件表面锈蚀,露出金属基体。酸洗除锈应严格控制酸洗程度,酸洗不足,氧化膜不能除尽,钢板表面不能完全活化;酸洗过度,易造成氢脆现象。因此酸洗槽内一般均添加适量酸洗抑制剂,以避免工件酸洗过度。另外,在酸洗槽内添加酸雾覆盖剂,用以降低 HC1 挥发。 氧化层与盐酸反应: FeO+2HCl=FeCl2+H2O Fe3O4+8HCl=2FeCl3+FeCl2+4H2O Fe2O3+6HCl=2FeCl3+3H2O 铁基体与盐酸反应: Fe+2HCl=FeCl+H2 ↑ ④水洗:完成酸洗处理的工件先送入水洗槽中进浸洗(水洗槽中的水来自喷头喷洗过程中产生的水),而后经喷头喷洗(采用新水)完成清洗作业,清洗掉工件表面残留的酸液,以利于下一工序操作。在此过程中会产生清洗废水(W1-2),属溢流式连续性排放。酸洗过程中,盐酸和金属反应生成氢气,氢气析出的过程会带出 HCl,形成酸雾(G1-1);酸洗槽定期清理,将上清液抽出重新配置后循环使用,底部废渣(S1-2)按危废处理;清洗废水(W1-2)经收集后一起送入前处理废水处理设施。 (2)镀覆处理 部分工件由于工艺要求需要进行两次镀锌,预镀锌后进行使用盐酸进行退镀,退镀后进行二次镀锌,镀锌分为氯化钾镀锌、锌酸盐碱性镀锌。 ①预镀锌 a、氯化钾镀锌 镀液的配置: 用自来水溶解计算量的氯化钾,溶解时要不断搅拌,加热可加快溶解速度。将溶解后的氯化钾溶液用过滤机过滤到镀槽中。 在另一容器中用沸腾的水溶解计算量的硼酸,然后倒入镀槽中。 用自来水或上述氯化钾和硼酸水溶液溶解氯化锌,氯化锌很容易溶解。 取少量镀液进行分析,并做赫尔槽试验,确认质量没问题后再加入光亮剂。加入光亮剂后可进行试镀,若镀层合格,可投入正常生产;如出现镀层不均匀、发花或低电流区发黑等现象,则需进行低电流密度电解处理。 工艺参数: 电镀温度 20-30℃ , pH 值 4.4~5.4 ,阴极电流密度 1~4A/dm2。 将经过除油和酸洗的电镀件放在挂具上或置于滚镀机内,电镀采用氯化钾镀锌工艺,以锌板做阳极,电镀液成分为 55~75g/L 氯化锌,210~240g/L 氯化钾、25~30g/L硼酸。 电镀液中氯化钾作为导电盐,在电镀液中不会被消耗,仅是带出损失,它的主要作用是提高镀液的电导率。硼酸的主要作用是维持镀液的 pH 值,硼酸为**弱酸,在水中发生逐级电离: H3BO3→(H2BO3)-+H+ (H2BO3)-→(HBO3)2-+H+ (HBO3)2-→(BO3)3+H+ 当镀液中的氢离子减少而造成 pH 值升高时,由于同离子效应,离解平衡便向右移动,使硼酸发生电离释放出氢离子以弥补镀液中氢离子的不足,这就起到了稳定镀液pH 值的作用。所以硼酸为 pH 值缓冲剂。浓度低时缓冲效果不明显,浓度高时难于溶解。硼酸在电镀中不消耗,只是带出损失。 氯化锌是镀液中的主盐,它是一种白色的极易潮解物质。当氯化锌溶于水中后,便被电离成锌离子和氯离子,同时放出热量: ZnCl2→Zn2++2Cl- 由于锌离子带正电荷,在镀液中它会被阴极上带负电荷的镀件所吸引,继而在工件表面接受电子而形成镀层: Zn2++2eˉ→Zn 锌阳极的作用是补充电镀过程中不断消耗的锌离子,以保持镀锌液中锌离子浓度平衡。 b 、锌酸盐碱性镀锌 镀液的配置: 首先将氢氧化钠用两倍量的水溶解,加水后必须立即进行兜底搅拌,防止其结于槽底。氢氧化钠的溶解是放热反应,切勿使溶液飞溅入眼睛内。待氢氧化钠全部溶解后,将事先用冷水调成糊状的氧化锌加入,边加入边搅拌,直至溶液由乳白色变成浅黄色,此时氧化锌已完全溶解成为锌酸钠配合物。然后加水至槽液规定体积,最后加入添加剂,即可进行电解处理。电解时间的长短要根据氧化锌的纯度而定,纯度越高,时间越短,反之则越长。 工艺参数: 电镀温度 20-30℃ , pH 值 9.4~ 10.4 ,阴极电流密度 1~4A/dm2。 将经过除油和酸洗的电镀件放在挂具上或置于滚镀机内,电镀采用锌酸盐碱性镀锌,电镀液成分为 7~8g/L 氧化锌,120~ 140g/L 氢氧化钠。 在碱性镀锌中,氧化锌是电镀锌的主盐,但它不溶于水,却能溶于过量的氢氧化钠中而形成锌酸络合物,反应如下 ZnO+2NaOH+H2O→Na[Zn(OH)4] 上述反应,在配制镀液时就已完成了。反应产物 Na2[Zn(OH)4]在水中产生电离: Na[Zn(OH)4]→Zn2++4OH-+2Na+ 电离出来的锌离子(Zn2+)在镀件(阴极)得到电子后还原为锌原子附着在表面形成了镀锌层。 Zn2++2eˉ→Zn 在镀件表面上除了发生上述反应式之外,还发生了析氢反应 2H++2e→H2 ↑ 锌阳极的作用是补充电镀过程中不断消耗的锌离子,以保持镀锌液中锌离子浓度平衡。锌酸盐碱性镀锌反应耗电在70%左右,比氯化钾镀锌的电流效率(98%)要低近 30%。 ②水洗:经镀锌处理的工件先浸入内置新水的清洗回收槽中进行一道浸洗回收,进一步降低镀件带出液,镀液回收量可达70% ,定期回用于电镀槽内。完成**浸洗的工件先送入水洗槽中进浸洗(水洗槽中的水来自喷头喷洗过程中产生的水),而后经喷头喷洗(采用新水)完成清洗作业,清洗掉工件表面残留的镀液,以利于下一工序操作。在此过程中会产生含锌废水(W1-3),属溢流式连续性排放。 在预镀锌过程中,电镀液定期需要过滤,形成滤渣(S1-3);过滤器会形成废过滤器滤芯(S1-4),含锌废水(W1-3)进入综合废水处理单元进行处理。 ③退镀:预镀锌后工件进入退镀槽进行退镀,退镀液为 4~6%的盐酸溶液,为二次镀锌做准备。 ④水洗:经退镀后工件进入水洗槽进行清洗,去除表面残留酸液。此过程会产生酸碱废水(W1-4),属溢流式连续性排放。 在退镀过程中,盐酸会析出形成酸雾(G1-2);退镀槽定期清理,将上清液抽出重新配置后循环使用,底部废渣(S1-5)按危废处理;清洗废水(W1-4)经收集后一起送入综合废水处理设施。 ⑤电解:由于酸洗和电镀过程产生氢离子进入金属表面,氢离子会影响二次镀锌及后期钝化,需将镀件浸入电解槽内进行脱氢处理。电解槽内溶液为20~30g/L的氢氧化钠。通过电解去除金属表面残存氢离子。 ⑥水洗:经电解后工件进入水洗槽进行清洗,去除表面残留碱液。此过程会产生酸碱废水(W1-5),属溢流式连续性排放。 在电解过程中,电解槽定期清理,将上清液抽出重新配置后循环使用,底部废渣(S1-6)按危废处理;清洗废水(W1-5)经收集后一起送入前处理废水处理设施。 ⑦镀锌:将经过退镀、电解后的电镀件浸入镀锌槽内进行二次镀锌,电镀采用氯化钾镀锌工艺,与预镀锌同样工艺。 ⑧水洗:经电解后工件进入水洗槽进行清洗,去除表面残留镀液。此过程会产生含锌废水(W1-6),属溢流式连续性排放。 在二次镀锌过程中,电镀液定期需要过滤,形成滤渣(S1-7);过滤器会形成废过滤器滤芯(S1-8),含锌废水(W1-6)进入综合废水处理单元进行处理。 ⑨出光:镀锌件水洗后用稀硝酸溶液出光,可使镀件表面更加光亮。使用硝酸的主要原因是硝酸具有强氧化性,对镀锌层的腐蚀轻微,且有化学抛光的作用。项目部分工件在钝化之前需进行出光处理,镀锌水洗完成后,工件进入含 2%硝酸的出光槽中进行出光处理。根据《污染源源强核算技术指南-电镀》(HJ984-2018)附录B,电镀主要废气污染物产污系数表中要求,在质量百分浓度≤3%稀硝酸溶液中锌镀层出光产生的氮氧化物可忽略。 本项目使用外购桶装硝酸为68%,配酸过程采用液下稀释,通过液下泵将硝酸抽至出光槽内,因此配酸过程中不会有废气产生。 ⑩水洗:出光后工件进水洗槽进行清洗,去除表面残留镀液。此过程会产生酸碱废水(W1-7),属溢流式连续性排放在出光过程中,出光槽定期清理,将上清液抽出重新配置后循环使用,底部 废渣(S1-9)按危险废物处理;酸碱废水(W1-7)经收集后一起送入综合废水处理设施。 (3)后处理 ①钝化:锌属于两性金属,当镀锌层暴露在大气中时会与空气中的氧气、二氧化碳、二氧化硫等气体发生化学反应出现白色腐蚀产物。为减缓腐蚀,镀锌后应马上进行钝化处理。钝化处理技术的实质是通过化学反应,使得镀层表面形成 一层不溶于水的凝胶状钝化膜,阻止了锌层的腐蚀。本项目采用两种钝化工艺,三价铬钝化、六价铬钝化。 a、六价铬钝化 锌镀层经过六价铬钝化后,锌层表面会形成一层钝化膜。钝化膜的成分为不 溶于水的铬化合物,它主要由三价铬和六价铬的化合物组成。它的结构大致是: Cr2O3Cr(OH)CrO4Cr(CrO4)2ZnSO4●Zn(OH)2CrO4Zn(CrO2)●4H2O 经过铬酸盐钝化过的镀层,其耐蚀性大大提高。如果没有钝化膜,镀锌层会很快地被腐蚀掉,而钝化膜起到了“铠甲”的作用。六价铬钝化液分为高铬钝化液、低铬钝化液。本项目采用钝化液为低铬钝化液,成分中铬酐3g/L。钝化温度为室温,时间为 10~30S。六价铬钝化会产生铬酸雾(G1-3)。 b、三价铬钝化 三价铬毒性仅为六价铬的1% ,因此钝化处理时,用三价铬代替六价铬对降低污染、保护环境有极其重要的意义。本项目部分钝化采用三价铬工艺,因三价铬无自我修复能力,为弥补这一缺陷,三价铬钝化膜往往需要进行封闭处理。在运输过程中要特别注意包装,以免擦伤零件影响其质量。本项目采用三价铬溶液成分中三价铬盐15g/L,钝化温度为室温,时间为40S。 ②水洗:钝化后工件进入水洗槽进行清洗,清洗掉残存钝化液,采用逆流水洗,减少废水中铬的含量。此过程产生含铬废水(W1-8)。 在钝化过程中,钝化槽定期清理,将上清液抽出重新配置后循环使用,底部废渣(S1-10)按危险废物处理;含铬废水(W1-8)经收集后一起送入含铬废水处理设施。 ③封闭:封闭工艺主要针对三价铬钝化工艺。三价铬钝化膜中没有可渗出的六价铬,所以钝化膜没有自修复能力,当钝化膜破损时很容易发生腐蚀。为了弥补此缺陷,需要对钝化膜进行封闭处理。此外,封闭处理还可以起到降低摩擦因数、改善产品外观的作用。采用硅酸盐封闭工艺,将镀锌钝化件浸人硅酸钠混合溶液中 20~40s。 ④钝化:三价铬钝化工件封闭后再次进入钝化槽采用进行二次钝化(三价铬),形成二次钝化膜,可有效增加工件耐磨性及抗腐蚀性能。 ⑤水洗:钝化后工件进入水洗槽进行清洗,清洗掉残存封闭液。此过程产生含铬废水(W1-9)。 封闭槽及二次钝化槽定期清理,将上清液抽出重新配置后循环使用,底部废(S1-11、S1-12)按危险废物处理;含铬废水(W1-9)经收集后送入含铬废水处理设施。 ⑥烘干:水洗后工件进行烘干处理,采用电加热。 镀镍生产工艺具体流程如下: (1)前处理 ①抛光 待镀件通过振动抛光机振动抛光,振动抛光机内加入水、除油剂、光亮剂,利用磨石和工件的摩擦,去除待镀件表面的毛刺、油污。 ②水洗 振动抛光机后设置水洗槽,用于清洗工件上带出抛光液。 振动抛光机内需要定期补充水、除油剂、光亮剂,定期清理,抛光液循环使用,清理出的底渣(S2-1)按危废处理。清洗废水(W2-1)经收集后一起送入前处理废水处理设施。 ③除油 镀镍生产线除油工序分为超声波除油、电解除油。 a、超声波除油 将工件浸入超声波除油槽中,在超声波除油液与发射器发射的超声波双重作用下,使工件表面粘附的油污脱离工件本体,并得以去除。防止因油污覆盖使工件导致漏镀。超声波除油液为碱性除油液,其主要成分为40~60g/LNaOH 、30~ 50g/LNa2CO3 、15~30g/LNa3PO4 和 3~5g/LNa3PO4的混合溶液除油槽温度控制在60℃左右。 b、电解除油 电解除油是把黏附油污的金属制品置于碱性脱脂液中,以金属工件作为阳极或阴极,通以直流电进行脱脂的过程。电化学脱脂依靠电解的作用强化脱脂效果,能使油脂彻底除净。 在电解条件下,电极的极化作用使油-液界面的表面张力下降,电极上析出的大量氢气泡或氧气泡对油膜具有强烈的剥离作用和机械搅拌作用,加速了脱脂过程。脱脂液本身的皂化作用和乳化作用可使电化学脱脂的速度加快,使脱脂效果更彻底。 电化学脱脂的实质是水的电解: 2H2O→2H2 ↑+O2 ↑ 阴极脱脂时,工件表面进行的是还原反应,析出氢气 4H2O+4e-→2H2 ↑+4OH- ↑ 阳极脱脂时,工件表面进行的是氧化反应,析出氧气 4OH--4e- →O2 ↑+2H2O↑ 电化学脱脂时,金属工件作为电极发生极化,使金属工件表面与碱性溶液间的表面张力降低,脱脂液对金属工件表面的润湿性增强,可起到排挤黏附在金属表面上的油膜的作用,使油膜更容易破裂成小油珠。同时,阴极脱脂和阳极脱脂分别析出大量的氢气和氧气,这些气体猛烈撞击并撕裂油膜,使油膜分散为很多细小的油珠而脱离材料表面,分散进入溶液中形成乳浊液。电极上产生的气体还加强了对材料表面溶液的搅拌,使材料表面的碱溶液得到不断更新,因而使脱脂 过程得以强化。因此,电化学脱脂时,电极上析出的大量气体有两个作用:一是剧烈析出的气泡起机械搅拌和剥离作用,加速溶液对油脂的皂化和乳化作用;二是细小的气泡从材料表面通过油膜析出时,气泡吸附油膜一起脱离材料表面带入溶液。 ④水洗 除油处理的工件先送入水洗槽中进浸洗(水洗槽中的水来自喷头喷洗过程中产生的水),而后经喷头喷洗(采用新水)完成清洗作业,清洗掉工件表面残留的碱液,以利于下一工序操作。在此过程中会产生含碱废水(W2-2),属溢流式连续性排放。 除油过程中,除油槽定期清理,将上清液抽出重新配置后循环使用,底部废渣(S2-2)按危废处理。该工序产生的酸碱废水(W2-2)含有较高浓度的油污,收集后进入前处理废水处理装置。 ⑤酸洗 将除油并冲洗干净的工件浸入酸洗槽中,利用4~6%的 HCl水溶液,在常温条件下浸洗10~20min,去除工件表面锈蚀,露出金属基体。酸洗除锈应严格控制酸洗程度,酸洗不足,氧化膜不能除尽,钢板表面不能完全活化;酸洗过度,易造成氢脆现象。因此酸洗槽内一般均添加适量酸洗抑制剂,以避免工件酸洗过度。 另外,在酸洗槽内添加酸雾覆盖剂,用以降低 HC1 的挥发。 ⑥水洗 完成酸洗处理的工件先送入水洗槽中进浸洗(水洗槽中的水来自喷头喷洗过程中产生的水),而后经喷头喷洗(采用新水)完成清洗作业,清洗掉工件表面残留的酸液,以利于下一工序操作。在此过程中会产生清洗废水(W2-3),属溢流式连续性排放。 酸洗过程中,盐酸和金属反应生成氢气,氢气析出的过程会带出HCl,形成酸雾(G2-1);酸洗槽定期清理,将上清液抽出重新配置后循环使用,底部废渣(S2-3) 按危废处理;清洗废水(W2-3)经收集后一起送入前处理废水处理设施。 (2)镀覆处理 本项目镀镍采用双层镍工艺,双层镀镍是在底层上先镀上一层暗镍,然后再在其上光亮镍层。当发生腐蚀时,光亮镍作为阳极镀层要起到牺牲自己保护底镀层和基体的作用。 镀液的配置: 将计算量的硫酸镍、氯化镍放入备用槽中,加入约 1/2 水量,加热、搅拌至完全溶解。在另一非金属容器中,将计算量的硼酸用热水溶解,由于硼酸的溶解度较低,因而溶解时应充分搅拌,待全部溶化后,倒入上述已溶解好的镍盐溶液中。加水至规定体积后,调整 pH 值,即可试镀。 工艺参数: 电镀温度 55-65℃ , 阴极电流密度 2~3A/dm2。 ①镀暗镍 在装饰-防护性镀层中,钢铁件及其他金属需要在底层镀一层结合力好的镀层作铺垫。电镀液成分为 180-220g/L硫酸镍、30-40g/L氯化镍、30-40g/L硼酸等, 镀液中的硫酸镍为电镀主盐,含有6个结晶水易溶于水,并呈深绿色。单独溶于水时,pH 值稍显酸性;氯化镍主要是作为导电盐存在;硼酸作为**弱酸,可起到稳定镀液 pH 值的作用,硼酸在电镀中不消耗,只是带出损失。 电镀时,阴极上电镀时,阴极上首先发生镍离子的还原反应,镍离子运动到阴极(镀件)表面接受电子,还原为镍原子并形成镀镍层。 Ni2++2e→Ni 与镍离子还原的同时,镀液中的氢离子也会在阴极表面接受电子还原为原子氢。原子氢一部分渗入镀件(铁板)晶格中,大部分会结合成氢气分子逸出表面。 2H++2e→2H→H2 ↑ 在阳极发生氧化反应,镍阳极失去电子形成镍离子进入镀液 Ni-2e→Ni2+ ②回收 镀槽后设置回收槽,用于回收镀槽带出的镀液,回收槽内溶液定期补充至镀槽内。 ③镀亮镍 亮镍相对于暗镍加入了光亮剂,镀液中硫酸镍230-300g/L 、氯化镍35-50g/L、 硼酸 35-50g/L、糖精1.5-2.5g/L、烯丙基磺酸钠2.0~3.0g/L。 ④回收 镀槽后设置回收槽,用于回收镀槽带出的镀液,回收槽内溶液定期补充至镀槽内。 ⑤镍封 镍封又称复合镀镍或弥散镀镍。镍封是在光亮镀镍上进行的,旨在进一步提高耐蚀性。在光亮镀镍溶液中加入一些不溶于水的十分细小的微粒,直径在 0.01~0.1μm之间。在强烈搅拌下,这些细小的微粒悬浮在镀液中与镍共沉积于工件表面。由于这些微粒是不导电的,并搅匀地分散在镍层上。 由于微孔数量众多,形成无数个微电池结构。使得腐蚀仅在镀层间进行,而延缓了纵向贯穿的腐蚀速度,从而保护了基体金属。与此同时,微孔结构还消除了镀层的巨大内应力,从而减少了镀层的应力腐蚀。 ⑥水洗 回收槽或镍封槽后设置水洗槽,用于清洗工件上带出镀液。 暗镍槽、亮镍槽、镍封槽定期清理,将上清液抽出重新配置后循环使用,底部废渣(S2-4、S2-6、S2-8)属于危险废物。电镀槽配置过滤器,过滤器分隔为上、下腔,悬浮液加入上腔,在压力作用下通过滤芯进入下腔成为滤液,固体颗粒被截留在过滤介质表面形成滤渣(即为废渣S2-4、S2-6),在此过程中将产生废滤芯(S2-5、S2-7),废滤芯属于危险废物,收集后进入危废间。 回收后水洗废水(W2-4)、镍封后水洗废水(W2-5)属于含镍废水,经收集后一起送入含镍废水处理设施。 (3)后处理 ①钝化 镀镍后工件进入钝化槽进行钝化,钝化液为 3~5%的铬酐。铬酐在镀镍层上腐蚀形成致密金属层,进一步加强镀层硬度、抗腐蚀性。 ②水洗 钝化后工件进入水洗槽进行清洗,清洗掉残存槽液。此过程产生含铬废水(W2-6)。 钝化槽内铬酐挥发产生铬酸雾(G2-2),钝化槽定期清理,将上清液抽出重新配置后循环使用,底部废渣(S2-8)按危险废物处理;含铬废水(W2-6)经收集后送入含铬废水处理设施。 ③烘干:水洗后工件进行烘干处理,采用电加热。 镀铬生产工艺具体流程如下: (1)前处理 ①除油 镀铬生产线除油工序分为超声波除油、电解除油。 a、超声波除油 将工件浸入超声波除油槽中,在超声波除油液与发射器发射的超声波双重作用下,使工件表面粘附的油污脱离工件本体,并得以去除。防止因油污覆盖使工件导致漏镀。超声波除油液为碱性除油液,其主要成分为40~60g/LNaOH 、30~ 50g/LNa2CO3 、15~30g/LNa3PO4 和 3~5g/LNa3PO4的混合溶液除油槽温度控制在60℃左右。 b、电解除油 电解除油是把黏附油污的金属制品置于碱性脱脂液中,以金属工件作为阳极或阴极,通以直流电进行脱脂的过程。电化学脱脂依靠电解的作用强化脱脂效果,能使油脂彻底除净。 在电解条件下,电极的极化作用使油-液界面的表面张力下降,电极上析出的大量氢气泡或氧气泡对油膜具有强烈的剥离作用和机械搅拌作用,加速了脱脂过程。脱脂液本身的皂化作用和乳化作用可使电化学脱脂的速度加快,使脱脂效果更彻底。 电化学脱脂的实质是水的电解: 2H2O→2H2 ↑+O2 ↑ 阴极脱脂时,工件表面进行的是还原反应,析出氢气 4H2O+4e-→2H2 ↑+4OH- ↑ 阳极脱脂时,工件表面进行的是氧化反应,析出氧气 4OH--4e- →O2 ↑+2H2O↑ 电化学脱脂时,金属工件作为电极发生极化,使金属工件表面与碱性溶液间的表面张力降低,脱脂液对金属工件表面的润湿性增强,可起到排挤黏附在金属表面上的油膜的作用,使油膜更容易破裂成小油珠。同时,阴极脱脂和阳极脱脂分别析出大量的氢气和氧气,这些气体猛烈撞击并撕裂油膜,使油膜分散为很多细小的油珠而脱离材料表面,分散进入溶液中形成乳浊液。电极上产生的气体还加强了对材料表面溶液的搅拌,使材料表面的碱溶液得到不断更新,因而使脱脂 过程得以强化。因此,电化学脱脂时,电极上析出的大量气体有两个作用:一是剧烈析出的气泡起机械搅拌和剥离作用,加速溶液对油脂的皂化和乳化作用;二 是细小的气泡从材料表面通过油膜析出时,气泡吸附油膜一起脱离材料表面带入 溶液。 ②水洗 除油处理的工件先送入水洗槽中进浸洗(水洗槽中的水来自喷头喷洗过程中产生的水),而后经喷头喷洗(采用新水)完成清洗作业,清洗掉工件表面残留的碱液,以利于下一工序操作。在此过程中会产生含碱废水(W3-1),属溢流式连续性排放。 除油过程中,除油槽定期清理,将上清液抽出重新配置后循环使用,底部废渣(S3-1)按危废处理。该工序产生的酸碱废水(W3-1)含有较高浓度的油污,收集后进入前处理废水处理装置。 ③酸洗 将除油并冲洗干净的工件浸入酸洗槽中,利用4~6%的HCl水溶液,在常温条件下浸洗10~20min,去除工件表面锈蚀,露出金属基体。酸洗除锈应严格控制酸洗程度,酸洗不足,氧化膜不能除尽,钢板表面不能完全活化;酸洗过度,易造成氢脆现象。因此酸洗槽内一般均添加适量酸洗抑制剂,以避免工件酸洗过度。另外,在酸洗槽内添加酸雾覆盖剂,用以降低 HC1 的挥发。 ④水洗 完成酸洗处理的工件先送入水洗槽中进浸洗(水洗槽中的水来自喷头喷洗过程中产生的水),而后经喷头喷洗(采用新水)完成清洗作业,清洗掉工件表面残留的酸液,以利于下一工序操作。在此过程中会产生清洗废水(W3-2),属溢流式连续性排放。 酸洗过程中,盐酸和金属反应生成氢气,氢气析出的过程会带出HCl,形成酸雾(G3-1);酸洗槽定期清理,将上清液抽出重新配置后循环使用,底部废渣(S3-2); 清洗废水(W3-2)经收集后一起送入前处理废水处理设施。 (2)镀覆处理 ①镀暗镍 在装饰-防护性镀层中,钢铁件及其他金属需要在底层镀一层结合力好的镀层作铺垫。电镀液成分为 180-220g/L硫酸镍、30-40g/L氯化镍、30-40g/L硼酸等, 镀液中的硫酸镍为电镀主盐,含有6个结晶水易溶于水,并呈深绿色。单独溶于水时,pH 值稍显酸性;氯化镍主要是作为导电盐存在;硼酸作为**弱酸,可起到稳定镀液 pH 值的作用,硼酸在电镀中不消耗,只是带出损失。 电镀时,阴极上电镀时,阴极上首先发生镍离子的还原反应,镍离子运动到阴极(镀件)表面接受电子,还原为镍原子并形成镀镍层。 Ni2++2e→Ni 与镍离子还原的同时,镀液中的氢离子也会在阴极表面接受电子还原为原子氢。原子氢一部分渗入镀件(铁板)晶格中,大部分会结合成氢气分子逸出表面。 2H++2e→2H→H2 ↑ 在阳极发生氧化反应,镍阳极失去电子形成镍离子进入镀液 Ni-2e→Ni2+ ②水洗 镀槽后设置水洗槽,清洗带出槽液,清洗产生含镍废水(W3-3)。 镀暗镍定期清理,将上清液抽出重新配置后循环使用,底部废渣(S3-3)按危废处理;槽液过滤工序产生废滤芯(S3-4)按危险废物处置。清洗产生的含镍废水(W3-3)收集后进入含镍废水处理装置。 ③镀铜 镀铜采用硫酸铜工艺,镀液成分为硫酸铜 180-250g/L,硫酸 40-70g/L。硫酸铜为镀铜的主盐,在水溶液中会离解成铜离子和硫酸根离子 CuSO4→Cu2++SO42 在电镀过程中,铜离子带正电荷被电迁移到阴极(镀件)表面,并接受电子,还原成铜原子并形成镀层: Cu2++2e→Cu 硫酸是一种强电解质,在水中100%电离,在镀液不仅起到导电的作用,而且对镀层的细化、均镀能力、覆盖能力都有较大影响 H2SO4→2H++SO42- 酸性镀铜所用阳极为含磷的磷铜板,磷铜作为阳极可以阻止岐化反应优于纯铜。磷铜在阳极获得电子生成二价铜离子。 Cu-2e→Cu2+ ④水洗 镀槽后设置水洗槽,清洗带出槽液,清洗产生含铜废水(W3-4)。 镀铜槽内含有硫酸,硫酸挥发产生硫酸雾(G3-2);镀铜槽定期清理,将上清液抽出重新配置后循环使用,底部废渣(S3-5)按危废处理;槽液过滤工序产生废滤芯(S3-6)按危险废物处置。清洗产生的含铜废水(W3-4)收集后进入综合废水处理处理装置。 ⑤镀亮镍 亮镍相对于暗镍加入了光亮剂,镀液中硫酸镍230-300g/L 、氯化镍35-50g/L、硼酸35-50g/L、糖精1.5-2.5g/L、烯丙基磺酸钠2.0~3.0g/L。工艺条件为pH4.0~4.5、 温度一般控制在55-65℃, 阴极电流密度3~4A/(dm2)。 ⑥水洗 镀亮镍后设置水洗槽,用于清洗工件上带出镀液。 亮镍槽定期清理,将上清液抽出重新配置后循环使用,底部废渣(S3-7)按危废处理;槽液过滤工序产生废滤芯(S3-8)按危险废物处置。清洗产生的含镍废水(W3-5)收集后进入含镍废水处理装置。 ⑦镀铬 a、镀装饰铬 装饰性镀铬主要是镀在光亮镍层上,电镀铬镀液成分为 250g/L铬酐,1.5g/L硫酸,电流密度20~40A/dm2。 镀铬液的主要成分为铬酸和硫酸。铬在镀液中的存在形式为重铬酸(H2Cr2O4)和铬酸(H2CrO4),并且两者之间存在动态平衡. 2H2CrO4H2Cr2O7+H2O 在较正的电位条件下,阴极有氢气析出,并使六价铬还原为三价铬 2H++2e→H2 ↑ Cr2O7+6e+14H+→2Cr3++7H2O 这一反应使镀液 pH 值上升,镀液中铬酸形式增多,其还原反应如下 CrO42-+6e+8H+→Cr+4H2O 在阴极中硬铬酸首先还原为三价铬,随后还原为金属铬附着在工件上。 b、镀硬铬 在机械制造行业中,耐磨性镀铬层有着非常广泛的应用。这种镀铬层硬度高,所以又称为耐磨性镀铬。工件表面镀一层较厚的硬铬层后,其使用寿命会大大**。镀硬铬无中间镀层,前处理后直接进入镀铬环节。 硬铬电镀液成分为铬酐 250g/L、硫酸1.5g/L ,电流密度 50~60A/dm2。 ⑧水洗 完成镀铬处理的工件先送入水洗槽中进浸洗(水洗槽中的水来自喷头喷洗过程中产生的水),而后经喷头喷洗(采用新水)完成清洗作业,清洗掉工件表面残留的酸液,以利于下一工序操作。在此过程中产生含铬废水(W3-6),属溢流式连续性排放。 镀铬液挥发产生废气(G3-3),主要成分为硫酸雾、铬酸雾;镀铬槽定期清理,将上清液抽出重新配置后循环使用,底部废渣(S3-9)按危废处理;槽液过滤工序产生废滤芯(S3-10)按危险废物处置;清洗产生的含铬废水(W3-6)收集后进入含铬废水处理装置。 镀铜工艺其过程主要包括前处理、 镀覆处理,其具体工艺流程如下: (1)前处理 ①除油:镀件在机加工时都会使用油脂润滑,有时会留下很重的油污。所以,在电镀前要先除去这些油污。将镀件浸入加油碱性脱脂液的除油槽内,碱性脱脂液主要成分为 40~60g/LNaOH 、30~50g/LNa2CO3和 3~5g/LNa3PO4的混合溶液。工件上的油污与碱液发生皂化反应生成脂肪酸皂和甘油生成的脂肪酸皂和甘油溶于水,在水的作用下离开金属表面,达到除油的目的。 ②水洗:除油处理的工件先送入水洗槽中进浸洗(水洗槽中的水来自喷头喷洗过程中产生的水),而后经喷头喷洗(采用新水)完成清洗作业,清洗掉工件表面残留的碱液,以利于下一工序操作。在此过程中会产生含碱废水(W4-1),属溢流式连续性排放。 除油槽定期清理,将上清液抽出重新配置后循环使用,底部废渣(S4-1)按危废处理。该工序产生的酸碱废水(W4-1)含有较高浓度的油污,收集后进入前处理废水处理装置。 ③酸洗:将除油并冲洗干净的工件浸入酸洗槽中,利用4~6%的HC1水溶液,在常温条件下浸洗 10~20min,去除工件表面锈蚀,露出金属基体。酸洗除锈应严格控制酸洗程度,酸洗不足,氧化膜不能除尽,钢板表面不能完全活化;酸洗过度,易造成氢脆现象。因此酸洗槽内一般均添加适量酸洗抑制剂,以避免工件酸 洗过度。另外,在酸洗槽内添加酸雾覆盖剂,用以降低 HC1 挥发。 氧化层与盐酸反应: FeO+2HCl=FeCl2+H2O Fe3O4+8HCl=2FeCl3+FeCl2+4H2O Fe2O3+6HCl=2FeCl3+3H2O 铁基体与盐酸反应: Fe+2HCl=FeCl+H2 ↑ ④水洗:完成酸洗处理的工件先送入水洗槽中进浸洗(水洗槽中的水来自喷头喷洗过程中产生的水),而后经喷头喷洗(采用新水)完成清洗作业,清洗掉工件表面残留的酸液,以利于下一工序操作。在此过程中会产生酸碱废水(W4-2),属溢流式连续性排放。 酸洗过程中,盐酸和金属反应生成氢气,氢气析出的过程会带HCl,形成酸雾(G4-1);酸洗槽定期清理,将上清液抽出重新配置后循环使用,底部废渣(S4-2)按危废处理;清洗废水(W4-2)经收集后一起送入前处理废水处理设施。 (2)镀覆处理 ①镀铜 镀铜采用硫酸铜工艺,镀液成分为硫酸铜180-250g/L,硫酸40-70g/L。硫酸铜为镀铜的主盐,在水溶液中会离解成铜离子和硫酸根离子 CuSO4→Cu2++SO42- 在电镀过程中,铜离子带正电荷被电迁移到阴极(镀件)表面,并接受电子,还原成铜原子并形成镀层: Cu2++2e→Cu 硫酸是一种强电解质,在水中 100%电离,在镀液不仅起到导电的作用,而且对镀层的细化、均镀能力、覆盖能力都有较大影响 H2SO4→2H++SO42- 酸性镀铜所用阳极为含磷的磷铜板,磷铜作为阳极可以阻止岐化反应优于纯铜。磷铜在阳极获得电子生成二价铜离子,补充镀液中的铜。 Cu-2e→Cu2+ ②水洗 镀铜后设置水洗槽,清洗带出槽液,清洗产生含铜废水(W4-3)。 镀铜液内含有硫酸,硫酸挥发产生硫酸雾(G4-2),镀铜槽定期清理,将上清液抽出重新配置后循环使用,底部废渣(S4-3)按危废处理;槽液过滤工序产生废滤芯(S4-4)按危险废物处置。该工序产生的含铜废水(W4-3)收集后进入综合废水处理设施。 ③烘干:水洗后工件进行烘干处理,采用电加热。 | 实际建设情况:镀锌工艺其过程主要包括前处理、镀覆处理和后处理,其具体工艺流程如下: (1)前处理 ①除油:镀件在机加工时都会使用油脂润滑,有时会留下很重的油污。所以,在电镀前要先除去这些油污。将镀件浸入加油碱性脱脂液的除油槽内,碱性脱脂液主要成分为 40~60g/LNaOH 、30~50g/LNa2CO3和3~5g/LNa3PO4 的混合溶液。工件上的油污与碱液发生皂化反应生成脂肪酸皂和甘油,典型反应方程式如下 R3(COO)3C3H5+3NaOH→3RCOONa+C3H5(OH)3 油脂氢氧化钠脂肪酸皂甘油生成的脂肪酸皂和甘油溶于水,在水的作用下离开金属表面,达到除油的目的。 ②水洗:除油处理的工件先送入水洗槽中进浸洗(水洗槽中的水来自喷头喷洗过程中产生的水),而后经喷头喷洗(采用新水)完成清洗作业,清洗掉工件表面残留的碱液,以利于下一工序操作。在此过程中会产生含碱废水(W1-1),属溢流式连续性排放,含有较高浓度的油污,收集后进入前处理废水处理装置。 除油过程中,除油槽定期清理,将上清液抽出重新配置后循环使用,底部废渣(S1-1)按危废处理。 ③酸洗:将除油并冲洗干净的工件浸入酸洗槽中,利用4~6%的 HC1水溶液,在常温条件下浸洗10~20min,去除工件表面锈蚀,露出金属基体。酸洗除锈应严格控制酸洗程度,酸洗不足,氧化膜不能除尽,钢板表面不能完全活化;酸洗过度,易造成氢脆现象。因此酸洗槽内一般均添加适量酸洗抑制剂,以避免工件酸洗过度。另外,在酸洗槽内添加酸雾覆盖剂,用以降低 HC1 挥发。 氧化层与盐酸反应: FeO+2HCl=FeCl2+H2O Fe3O4+8HCl=2FeCl3+FeCl2+4H2O Fe2O3+6HCl=2FeCl3+3H2O 铁基体与盐酸反应: Fe+2HCl=FeCl+H2 ↑ ④水洗:完成酸洗处理的工件先送入水洗槽中进浸洗(水洗槽中的水来自喷头喷洗过程中产生的水),而后经喷头喷洗(采用新水)完成清洗作业,清洗掉工件表面残留的酸液,以利于下一工序操作。在此过程中会产生清洗废水(W1-2),属溢流式连续性排放。酸洗过程中,盐酸和金属反应生成氢气,氢气析出的过程会带出 HCl,形成酸雾(G1-1);酸洗槽定期清理,将上清液抽出重新配置后循环使用,底部废渣(S1-2)按危废处理;清洗废水(W1-2)经收集后一起送入前处理废水处理设施。 (2)镀覆处理 部分工件由于工艺要求需要进行两次镀锌,预镀锌后进行使用盐酸进行退镀,退镀后进行二次镀锌,镀锌分为氯化钾镀锌、锌酸盐碱性镀锌。 ①预镀锌 a、氯化钾镀锌 镀液的配置: 用自来水溶解计算量的氯化钾,溶解时要不断搅拌,加热可加快溶解速度。将溶解后的氯化钾溶液用过滤机过滤到镀槽中。 在另一容器中用沸腾的水溶解计算量的硼酸,然后倒入镀槽中。 用自来水或上述氯化钾和硼酸水溶液溶解氯化锌,氯化锌很容易溶解。 取少量镀液进行分析,并做赫尔槽试验,确认质量没问题后再加入光亮剂。加入光亮剂后可进行试镀,若镀层合格,可投入正常生产;如出现镀层不均匀、发花或低电流区发黑等现象,则需进行低电流密度电解处理。 工艺参数: 电镀温度 20-30℃ , pH 值 4.4~5.4 ,阴极电流密度 1~4A/dm2。 将经过除油和酸洗的电镀件放在挂具上或置于滚镀机内,电镀采用氯化钾镀锌工艺,以锌板做阳极,电镀液成分为 55~75g/L 氯化锌,210~240g/L 氯化钾、25~30g/L硼酸。 电镀液中氯化钾作为导电盐,在电镀液中不会被消耗,仅是带出损失,它的主要作用是提高镀液的电导率。硼酸的主要作用是维持镀液的 pH 值,硼酸为**弱酸,在水中发生逐级电离: H3BO3→(H2BO3)-+H+ (H2BO3)-→(HBO3)2-+H+ (HBO3)2-→(BO3)3+H+ 当镀液中的氢离子减少而造成 pH 值升高时,由于同离子效应,离解平衡便向右移动,使硼酸发生电离释放出氢离子以弥补镀液中氢离子的不足,这就起到了稳定镀液pH 值的作用。所以硼酸为 pH 值缓冲剂。浓度低时缓冲效果不明显,浓度高时难于溶解。硼酸在电镀中不消耗,只是带出损失。 氯化锌是镀液中的主盐,它是一种白色的极易潮解物质。当氯化锌溶于水中后,便被电离成锌离子和氯离子,同时放出热量: ZnCl2→Zn2++2Cl- 由于锌离子带正电荷,在镀液中它会被阴极上带负电荷的镀件所吸引,继而在工件表面接受电子而形成镀层: Zn2++2eˉ→Zn 锌阳极的作用是补充电镀过程中不断消耗的锌离子,以保持镀锌液中锌离子浓度平衡。 b 、锌酸盐碱性镀锌 镀液的配置: 首先将氢氧化钠用两倍量的水溶解,加水后必须立即进行兜底搅拌,防止其结于槽底。氢氧化钠的溶解是放热反应,切勿使溶液飞溅入眼睛内。待氢氧化钠全部溶解后,将事先用冷水调成糊状的氧化锌加入,边加入边搅拌,直至溶液由乳白色变成浅黄色,此时氧化锌已完全溶解成为锌酸钠配合物。然后加水至槽液规定体积,最后加入添加剂,即可进行电解处理。电解时间的长短要根据氧化锌的纯度而定,纯度越高,时间越短,反之则越长。 工艺参数: 电镀温度 20-30℃ , pH 值 9.4~ 10.4 ,阴极电流密度 1~4A/dm2。 将经过除油和酸洗的电镀件放在挂具上或置于滚镀机内,电镀采用锌酸盐碱性镀锌,电镀液成分为 7~8g/L 氧化锌,120~ 140g/L 氢氧化钠。 在碱性镀锌中,氧化锌是电镀锌的主盐,但它不溶于水,却能溶于过量的氢氧化钠中而形成锌酸络合物,反应如下 ZnO+2NaOH+H2O→Na[Zn(OH)4] 上述反应,在配制镀液时就已完成了。反应产物 Na2[Zn(OH)4]在水中产生电离: Na[Zn(OH)4]→Zn2++4OH-+2Na+ 电离出来的锌离子(Zn2+)在镀件(阴极)得到电子后还原为锌原子附着在表面形成了镀锌层。 Zn2++2eˉ→Zn 在镀件表面上除了发生上述反应式之外,还发生了析氢反应 2H++2e→H2 ↑ 锌阳极的作用是补充电镀过程中不断消耗的锌离子,以保持镀锌液中锌离子浓度平衡。锌酸盐碱性镀锌反应耗电在70%左右,比氯化钾镀锌的电流效率(98%)要低近 30%。 ②水洗:经镀锌处理的工件先浸入内置新水的清洗回收槽中进行一道浸洗回收,进一步降低镀件带出液,镀液回收量可达70% ,定期回用于电镀槽内。完成**浸洗的工件先送入水洗槽中进浸洗(水洗槽中的水来自喷头喷洗过程中产生的水),而后经喷头喷洗(采用新水)完成清洗作业,清洗掉工件表面残留的镀液,以利于下一工序操作。在此过程中会产生含锌废水(W1-3),属溢流式连续性排放。 在预镀锌过程中,电镀液定期需要过滤,形成滤渣(S1-3);过滤器会形成废过滤器滤芯(S1-4),含锌废水(W1-3)进入综合废水处理单元进行处理。 ③退镀:预镀锌后工件进入退镀槽进行退镀,退镀液为 4~6%的盐酸溶液,为二次镀锌做准备。 ④水洗:经退镀后工件进入水洗槽进行清洗,去除表面残留酸液。此过程会产生酸碱废水(W1-4),属溢流式连续性排放。 在退镀过程中,盐酸会析出形成酸雾(G1-2);退镀槽定期清理,将上清液抽出重新配置后循环使用,底部废渣(S1-5)按危废处理;清洗废水(W1-4)经收集后一起送入综合废水处理设施。 ⑤电解:由于酸洗和电镀过程产生氢离子进入金属表面,氢离子会影响二次镀锌及后期钝化,需将镀件浸入电解槽内进行脱氢处理。电解槽内溶液为20~30g/L的氢氧化钠。通过电解去除金属表面残存氢离子。 ⑥水洗:经电解后工件进入水洗槽进行清洗,去除表面残留碱液。此过程会产生酸碱废水(W1-5),属溢流式连续性排放。 在电解过程中,电解槽定期清理,将上清液抽出重新配置后循环使用,底部废渣(S1-6)按危废处理;清洗废水(W1-5)经收集后一起送入前处理废水处理设施。 ⑦镀锌:将经过退镀、电解后的电镀件浸入镀锌槽内进行二次镀锌,电镀采用氯化钾镀锌工艺,与预镀锌同样工艺。 ⑧水洗:经电解后工件进入水洗槽进行清洗,去除表面残留镀液。此过程会产生含锌废水(W1-6),属溢流式连续性排放。 在二次镀锌过程中,电镀液定期需要过滤,形成滤渣(S1-7);过滤器会形成废过滤器滤芯(S1-8),含锌废水(W1-6)进入综合废水处理单元进行处理。 ⑨出光:镀锌件水洗后用稀硝酸溶液出光,可使镀件表面更加光亮。使用硝酸的主要原因是硝酸具有强氧化性,对镀锌层的腐蚀轻微,且有化学抛光的作用。项目部分工件在钝化之前需进行出光处理,镀锌水洗完成后,工件进入含 2%硝酸的出光槽中进行出光处理。根据《污染源源强核算技术指南-电镀》(HJ984-2018)附录B,电镀主要废气污染物产污系数表中要求,在质量百分浓度≤3%稀硝酸溶液中锌镀层出光产生的氮氧化物可忽略。 本项目使用外购桶装硝酸为68%,配酸过程采用液下稀释,通过液下泵将硝酸抽至出光槽内,因此配酸过程中不会有废气产生。 ⑩水洗:出光后工件进水洗槽进行清洗,去除表面残留镀液。此过程会产生酸碱废水(W1-7),属溢流式连续性排放在出光过程中,出光槽定期清理,将上清液抽出重新配置后循环使用,底部 废渣(S1-9)按危险废物处理;酸碱废水(W1-7)经收集后一起送入综合废水处理设施。 (3)后处理 ①钝化:锌属于两性金属,当镀锌层暴露在大气中时会与空气中的氧气、二氧化碳、二氧化硫等气体发生化学反应出现白色腐蚀产物。为减缓腐蚀,镀锌后应马上进行钝化处理。钝化处理技术的实质是通过化学反应,使得镀层表面形成 一层不溶于水的凝胶状钝化膜,阻止了锌层的腐蚀。本项目采用两种钝化工艺,三价铬钝化、六价铬钝化。 a、六价铬钝化 锌镀层经过六价铬钝化后,锌层表面会形成一层钝化膜。钝化膜的成分为不 溶于水的铬化合物,它主要由三价铬和六价铬的化合物组成。它的结构大致是: Cr2O3Cr(OH)CrO4Cr(CrO4)2ZnSO4●Zn(OH)2CrO4Zn(CrO2)●4H2O 经过铬酸盐钝化过的镀层,其耐蚀性大大提高。如果没有钝化膜,镀锌层会很快地被腐蚀掉,而钝化膜起到了“铠甲”的作用。六价铬钝化液分为高铬钝化液、低铬钝化液。本项目采用钝化液为低铬钝化液,成分中铬酐3g/L。钝化温度为室温,时间为 10~30S。六价铬钝化会产生铬酸雾(G1-3)。 b、三价铬钝化 三价铬毒性仅为六价铬的1% ,因此钝化处理时,用三价铬代替六价铬对降低污染、保护环境有极其重要的意义。本项目部分钝化采用三价铬工艺,因三价铬无自我修复能力,为弥补这一缺陷,三价铬钝化膜往往需要进行封闭处理。在运输过程中要特别注意包装,以免擦伤零件影响其质量。本项目采用三价铬溶液成分中三价铬盐15g/L,钝化温度为室温,时间为40S。 ②水洗:钝化后工件进入水洗槽进行清洗,清洗掉残存钝化液,采用逆流水洗,减少废水中铬的含量。此过程产生含铬废水(W1-8)。 在钝化过程中,钝化槽定期清理,将上清液抽出重新配置后循环使用,底部废渣(S1-10)按危险废物处理;含铬废水(W1-8)经收集后一起送入含铬废水处理设施。 ③封闭:封闭工艺主要针对三价铬钝化工艺。三价铬钝化膜中没有可渗出的六价铬,所以钝化膜没有自修复能力,当钝化膜破损时很容易发生腐蚀。为了弥补此缺陷,需要对钝化膜进行封闭处理。此外,封闭处理还可以起到降低摩擦因数、改善产品外观的作用。采用硅酸盐封闭工艺,将镀锌钝化件浸人硅酸钠混合溶液中 20~40s。 ④钝化:三价铬钝化工件封闭后再次进入钝化槽采用进行二次钝化(三价铬),形成二次钝化膜,可有效增加工件耐磨性及抗腐蚀性能。 ⑤水洗:钝化后工件进入水洗槽进行清洗,清洗掉残存封闭液。此过程产生含铬废水(W1-9)。 封闭槽及二次钝化槽定期清理,将上清液抽出重新配置后循环使用,底部废(S1-11、S1-12)按危险废物处理;含铬废水(W1-9)经收集后送入含铬废水处理设施。 ⑥烘干:水洗后工件进行烘干处理,采用电加热。 镀镍生产工艺具体流程如下: (1)前处理 ①抛光 待镀件通过振动抛光机振动抛光,振动抛光机内加入水、除油剂、光亮剂,利用磨石和工件的摩擦,去除待镀件表面的毛刺、油污。 ②水洗 振动抛光机后设置水洗槽,用于清洗工件上带出抛光液。 振动抛光机内需要定期补充水、除油剂、光亮剂,定期清理,抛光液循环使用,清理出的底渣(S2-1)按危废处理。清洗废水(W2-1)经收集后一起送入前处理废水处理设施。 ③除油 镀镍生产线除油工序分为超声波除油、电解除油。 a、超声波除油 将工件浸入超声波除油槽中,在超声波除油液与发射器发射的超声波双重作用下,使工件表面粘附的油污脱离工件本体,并得以去除。防止因油污覆盖使工件导致漏镀。超声波除油液为碱性除油液,其主要成分为40~60g/LNaOH 、30~ 50g/LNa2CO3 、15~30g/LNa3PO4 和 3~5g/LNa3PO4的混合溶液除油槽温度控制在60℃左右。 b、电解除油 电解除油是把黏附油污的金属制品置于碱性脱脂液中,以金属工件作为阳极或阴极,通以直流电进行脱脂的过程。电化学脱脂依靠电解的作用强化脱脂效果,能使油脂彻底除净。 在电解条件下,电极的极化作用使油-液界面的表面张力下降,电极上析出的大量氢气泡或氧气泡对油膜具有强烈的剥离作用和机械搅拌作用,加速了脱脂过程。脱脂液本身的皂化作用和乳化作用可使电化学脱脂的速度加快,使脱脂效果更彻底。 电化学脱脂的实质是水的电解: 2H2O→2H2 ↑+O2 ↑ 阴极脱脂时,工件表面进行的是还原反应,析出氢气 4H2O+4e-→2H2 ↑+4OH- ↑ 阳极脱脂时,工件表面进行的是氧化反应,析出氧气 4OH--4e- →O2 ↑+2H2O↑ 电化学脱脂时,金属工件作为电极发生极化,使金属工件表面与碱性溶液间的表面张力降低,脱脂液对金属工件表面的润湿性增强,可起到排挤黏附在金属表面上的油膜的作用,使油膜更容易破裂成小油珠。同时,阴极脱脂和阳极脱脂分别析出大量的氢气和氧气,这些气体猛烈撞击并撕裂油膜,使油膜分散为很多细小的油珠而脱离材料表面,分散进入溶液中形成乳浊液。电极上产生的气体还加强了对材料表面溶液的搅拌,使材料表面的碱溶液得到不断更新,因而使脱脂 过程得以强化。因此,电化学脱脂时,电极上析出的大量气体有两个作用:一是剧烈析出的气泡起机械搅拌和剥离作用,加速溶液对油脂的皂化和乳化作用;二是细小的气泡从材料表面通过油膜析出时,气泡吸附油膜一起脱离材料表面带入溶液。 ④水洗 除油处理的工件先送入水洗槽中进浸洗(水洗槽中的水来自喷头喷洗过程中产生的水),而后经喷头喷洗(采用新水)完成清洗作业,清洗掉工件表面残留的碱液,以利于下一工序操作。在此过程中会产生含碱废水(W2-2),属溢流式连续性排放。 除油过程中,除油槽定期清理,将上清液抽出重新配置后循环使用,底部废渣(S2-2)按危废处理。该工序产生的酸碱废水(W2-2)含有较高浓度的油污,收集后进入前处理废水处理装置。 ⑤酸洗 将除油并冲洗干净的工件浸入酸洗槽中,利用4~6%的 HCl水溶液,在常温条件下浸洗10~20min,去除工件表面锈蚀,露出金属基体。酸洗除锈应严格控制酸洗程度,酸洗不足,氧化膜不能除尽,钢板表面不能完全活化;酸洗过度,易造成氢脆现象。因此酸洗槽内一般均添加适量酸洗抑制剂,以避免工件酸洗过度。 另外,在酸洗槽内添加酸雾覆盖剂,用以降低 HC1 的挥发。 ⑥水洗 完成酸洗处理的工件先送入水洗槽中进浸洗(水洗槽中的水来自喷头喷洗过程中产生的水),而后经喷头喷洗(采用新水)完成清洗作业,清洗掉工件表面残留的酸液,以利于下一工序操作。在此过程中会产生清洗废水(W2-3),属溢流式连续性排放。 酸洗过程中,盐酸和金属反应生成氢气,氢气析出的过程会带出HCl,形成酸雾(G2-1);酸洗槽定期清理,将上清液抽出重新配置后循环使用,底部废渣(S2-3) 按危废处理;清洗废水(W2-3)经收集后一起送入前处理废水处理设施。 (2)镀覆处理 本项目镀镍采用双层镍工艺,双层镀镍是在底层上先镀上一层暗镍,然后再在其上光亮镍层。当发生腐蚀时,光亮镍作为阳极镀层要起到牺牲自己保护底镀层和基体的作用。 镀液的配置: 将计算量的硫酸镍、氯化镍放入备用槽中,加入约 1/2 水量,加热、搅拌至完全溶解。在另一非金属容器中,将计算量的硼酸用热水溶解,由于硼酸的溶解度较低,因而溶解时应充分搅拌,待全部溶化后,倒入上述已溶解好的镍盐溶液中。加水至规定体积后,调整 pH 值,即可试镀。 工艺参数: 电镀温度 55-65℃ , 阴极电流密度 2~3A/dm2。 ①镀暗镍 在装饰-防护性镀层中,钢铁件及其他金属需要在底层镀一层结合力好的镀层作铺垫。电镀液成分为 180-220g/L硫酸镍、30-40g/L氯化镍、30-40g/L硼酸等, 镀液中的硫酸镍为电镀主盐,含有6个结晶水易溶于水,并呈深绿色。单独溶于水时,pH 值稍显酸性;氯化镍主要是作为导电盐存在;硼酸作为**弱酸,可起到稳定镀液 pH 值的作用,硼酸在电镀中不消耗,只是带出损失。 电镀时,阴极上电镀时,阴极上首先发生镍离子的还原反应,镍离子运动到阴极(镀件)表面接受电子,还原为镍原子并形成镀镍层。 Ni2++2e→Ni 与镍离子还原的同时,镀液中的氢离子也会在阴极表面接受电子还原为原子氢。原子氢一部分渗入镀件(铁板)晶格中,大部分会结合成氢气分子逸出表面。 2H++2e→2H→H2 ↑ 在阳极发生氧化反应,镍阳极失去电子形成镍离子进入镀液 Ni-2e→Ni2+ ②回收 镀槽后设置回收槽,用于回收镀槽带出的镀液,回收槽内溶液定期补充至镀槽内。 ③镀亮镍 亮镍相对于暗镍加入了光亮剂,镀液中硫酸镍230-300g/L 、氯化镍35-50g/L、 硼酸 35-50g/L、糖精1.5-2.5g/L、烯丙基磺酸钠2.0~3.0g/L。 ④回收 镀槽后设置回收槽,用于回收镀槽带出的镀液,回收槽内溶液定期补充至镀槽内。 ⑤镍封 镍封又称复合镀镍或弥散镀镍。镍封是在光亮镀镍上进行的,旨在进一步提高耐蚀性。在光亮镀镍溶液中加入一些不溶于水的十分细小的微粒,直径在 0.01~0.1μm之间。在强烈搅拌下,这些细小的微粒悬浮在镀液中与镍共沉积于工件表面。由于这些微粒是不导电的,并搅匀地分散在镍层上。 由于微孔数量众多,形成无数个微电池结构。使得腐蚀仅在镀层间进行,而延缓了纵向贯穿的腐蚀速度,从而保护了基体金属。与此同时,微孔结构还消除了镀层的巨大内应力,从而减少了镀层的应力腐蚀。 ⑥水洗 回收槽或镍封槽后设置水洗槽,用于清洗工件上带出镀液。 暗镍槽、亮镍槽、镍封槽定期清理,将上清液抽出重新配置后循环使用,底部废渣(S2-4、S2-6、S2-8)属于危险废物。电镀槽配置过滤器,过滤器分隔为上、下腔,悬浮液加入上腔,在压力作用下通过滤芯进入下腔成为滤液,固体颗粒被截留在过滤介质表面形成滤渣(即为废渣S2-4、S2-6),在此过程中将产生废滤芯(S2-5、S2-7),废滤芯属于危险废物,收集后进入危废间。 回收后水洗废水(W2-4)、镍封后水洗废水(W2-5)属于含镍废水,经收集后一起送入含镍废水处理设施。 (3)后处理 ①钝化 镀镍后工件进入钝化槽进行钝化,钝化液为 3~5%的铬酐。铬酐在镀镍层上腐蚀形成致密金属层,进一步加强镀层硬度、抗腐蚀性。 ②水洗 钝化后工件进入水洗槽进行清洗,清洗掉残存槽液。此过程产生含铬废水(W2-6)。 钝化槽内铬酐挥发产生铬酸雾(G2-2),钝化槽定期清理,将上清液抽出重新配置后循环使用,底部废渣(S2-8)按危险废物处理;含铬废水(W2-6)经收集后送入含铬废水处理设施。 ③烘干:水洗后工件进行烘干处理,采用电加热。 镀铬生产工艺具体流程如下: (1)前处理 ①除油 镀铬生产线除油工序分为超声波除油、电解除油。 a、超声波除油 将工件浸入超声波除油槽中,在超声波除油液与发射器发射的超声波双重作用下,使工件表面粘附的油污脱离工件本体,并得以去除。防止因油污覆盖使工件导致漏镀。超声波除油液为碱性除油液,其主要成分为40~60g/LNaOH 、30~ 50g/LNa2CO3 、15~30g/LNa3PO4 和 3~5g/LNa3PO4的混合溶液除油槽温度控制在60℃左右。 b、电解除油 电解除油是把黏附油污的金属制品置于碱性脱脂液中,以金属工件作为阳极或阴极,通以直流电进行脱脂的过程。电化学脱脂依靠电解的作用强化脱脂效果,能使油脂彻底除净。 在电解条件下,电极的极化作用使油-液界面的表面张力下降,电极上析出的大量氢气泡或氧气泡对油膜具有强烈的剥离作用和机械搅拌作用,加速了脱脂过程。脱脂液本身的皂化作用和乳化作用可使电化学脱脂的速度加快,使脱脂效果更彻底。 电化学脱脂的实质是水的电解: 2H2O→2H2 ↑+O2 ↑ 阴极脱脂时,工件表面进行的是还原反应,析出氢气 4H2O+4e-→2H2 ↑+4OH- ↑ 阳极脱脂时,工件表面进行的是氧化反应,析出氧气 4OH--4e- →O2 ↑+2H2O↑ 电化学脱脂时,金属工件作为电极发生极化,使金属工件表面与碱性溶液间的表面张力降低,脱脂液对金属工件表面的润湿性增强,可起到排挤黏附在金属表面上的油膜的作用,使油膜更容易破裂成小油珠。同时,阴极脱脂和阳极脱脂分别析出大量的氢气和氧气,这些气体猛烈撞击并撕裂油膜,使油膜分散为很多细小的油珠而脱离材料表面,分散进入溶液中形成乳浊液。电极上产生的气体还加强了对材料表面溶液的搅拌,使材料表面的碱溶液得到不断更新,因而使脱脂 过程得以强化。因此,电化学脱脂时,电极上析出的大量气体有两个作用:一是剧烈析出的气泡起机械搅拌和剥离作用,加速溶液对油脂的皂化和乳化作用;二 是细小的气泡从材料表面通过油膜析出时,气泡吸附油膜一起脱离材料表面带入 溶液。 ②水洗 除油处理的工件先送入水洗槽中进浸洗(水洗槽中的水来自喷头喷洗过程中产生的水),而后经喷头喷洗(采用新水)完成清洗作业,清洗掉工件表面残留的碱液,以利于下一工序操作。在此过程中会产生含碱废水(W3-1),属溢流式连续性排放。 除油过程中,除油槽定期清理,将上清液抽出重新配置后循环使用,底部废渣(S3-1)按危废处理。该工序产生的酸碱废水(W3-1)含有较高浓度的油污,收集后进入前处理废水处理装置。 ③酸洗 将除油并冲洗干净的工件浸入酸洗槽中,利用4~6%的HCl水溶液,在常温条件下浸洗10~20min,去除工件表面锈蚀,露出金属基体。酸洗除锈应严格控制酸洗程度,酸洗不足,氧化膜不能除尽,钢板表面不能完全活化;酸洗过度,易造成氢脆现象。因此酸洗槽内一般均添加适量酸洗抑制剂,以避免工件酸洗过度。另外,在酸洗槽内添加酸雾覆盖剂,用以降低 HC1 的挥发。 ④水洗 完成酸洗处理的工件先送入水洗槽中进浸洗(水洗槽中的水来自喷头喷洗过程中产生的水),而后经喷头喷洗(采用新水)完成清洗作业,清洗掉工件表面残留的酸液,以利于下一工序操作。在此过程中会产生清洗废水(W3-2),属溢流式连续性排放。 酸洗过程中,盐酸和金属反应生成氢气,氢气析出的过程会带出HCl,形成酸雾(G3-1);酸洗槽定期清理,将上清液抽出重新配置后循环使用,底部废渣(S3-2); 清洗废水(W3-2)经收集后一起送入前处理废水处理设施。 (2)镀覆处理 ①镀暗镍 在装饰-防护性镀层中,钢铁件及其他金属需要在底层镀一层结合力好的镀层作铺垫。电镀液成分为 180-220g/L硫酸镍、30-40g/L氯化镍、30-40g/L硼酸等, 镀液中的硫酸镍为电镀主盐,含有6个结晶水易溶于水,并呈深绿色。单独溶于水时,pH 值稍显酸性;氯化镍主要是作为导电盐存在;硼酸作为**弱酸,可起到稳定镀液 pH 值的作用,硼酸在电镀中不消耗,只是带出损失。 电镀时,阴极上电镀时,阴极上首先发生镍离子的还原反应,镍离子运动到阴极(镀件)表面接受电子,还原为镍原子并形成镀镍层。 Ni2++2e→Ni 与镍离子还原的同时,镀液中的氢离子也会在阴极表面接受电子还原为原子氢。原子氢一部分渗入镀件(铁板)晶格中,大部分会结合成氢气分子逸出表面。 2H++2e→2H→H2 ↑ 在阳极发生氧化反应,镍阳极失去电子形成镍离子进入镀液 Ni-2e→Ni2+ ②水洗 镀槽后设置水洗槽,清洗带出槽液,清洗产生含镍废水(W3-3)。 镀暗镍定期清理,将上清液抽出重新配置后循环使用,底部废渣(S3-3)按危废处理;槽液过滤工序产生废滤芯(S3-4)按危险废物处置。清洗产生的含镍废水(W3-3)收集后进入含镍废水处理装置。 ③镀铜 镀铜采用硫酸铜工艺,镀液成分为硫酸铜 180-250g/L,硫酸 40-70g/L。硫酸铜为镀铜的主盐,在水溶液中会离解成铜离子和硫酸根离子 CuSO4→Cu2++SO42 在电镀过程中,铜离子带正电荷被电迁移到阴极(镀件)表面,并接受电子,还原成铜原子并形成镀层: Cu2++2e→Cu 硫酸是一种强电解质,在水中100%电离,在镀液不仅起到导电的作用,而且对镀层的细化、均镀能力、覆盖能力都有较大影响 H2SO4→2H++SO42- 酸性镀铜所用阳极为含磷的磷铜板,磷铜作为阳极可以阻止岐化反应优于纯铜。磷铜在阳极获得电子生成二价铜离子。 Cu-2e→Cu2+ ④水洗 镀槽后设置水洗槽,清洗带出槽液,清洗产生含铜废水(W3-4)。 镀铜槽内含有硫酸,硫酸挥发产生硫酸雾(G3-2);镀铜槽定期清理,将上清液抽出重新配置后循环使用,底部废渣(S3-5)按危废处理;槽液过滤工序产生废滤芯(S3-6)按危险废物处置。清洗产生的含铜废水(W3-4)收集后进入综合废水处理处理装置。 ⑤镀亮镍 亮镍相对于暗镍加入了光亮剂,镀液中硫酸镍230-300g/L 、氯化镍35-50g/L、硼酸35-50g/L、糖精1.5-2.5g/L、烯丙基磺酸钠2.0~3.0g/L。工艺条件为pH4.0~4.5、 温度一般控制在55-65℃, 阴极电流密度3~4A/(dm2)。 ⑥水洗 镀亮镍后设置水洗槽,用于清洗工件上带出镀液。 亮镍槽定期清理,将上清液抽出重新配置后循环使用,底部废渣(S3-7)按危废处理;槽液过滤工序产生废滤芯(S3-8)按危险废物处置。清洗产生的含镍废水(W3-5)收集后进入含镍废水处理装置。 ⑦镀铬 a、镀装饰铬 装饰性镀铬主要是镀在光亮镍层上,电镀铬镀液成分为 250g/L铬酐,1.5g/L硫酸,电流密度20~40A/dm2。 镀铬液的主要成分为铬酸和硫酸。铬在镀液中的存在形式为重铬酸(H2Cr2O4)和铬酸(H2CrO4),并且两者之间存在动态平衡. 2H2CrO4H2Cr2O7+H2O 在较正的电位条件下,阴极有氢气析出,并使六价铬还原为三价铬 2H++2e→H2 ↑ Cr2O7+6e+14H+→2Cr3++7H2O 这一反应使镀液 pH 值上升,镀液中铬酸形式增多,其还原反应如下 CrO42-+6e+8H+→Cr+4H2O 在阴极中硬铬酸首先还原为三价铬,随后还原为金属铬附着在工件上。 b、镀硬铬 在机械制造行业中,耐磨性镀铬层有着非常广泛的应用。这种镀铬层硬度高,所以又称为耐磨性镀铬。工件表面镀一层较厚的硬铬层后,其使用寿命会大大**。镀硬铬无中间镀层,前处理后直接进入镀铬环节。 硬铬电镀液成分为铬酐 250g/L、硫酸1.5g/L ,电流密度 50~60A/dm2。 ⑧水洗 完成镀铬处理的工件先送入水洗槽中进浸洗(水洗槽中的水来自喷头喷洗过程中产生的水),而后经喷头喷洗(采用新水)完成清洗作业,清洗掉工件表面残留的酸液,以利于下一工序操作。在此过程中产生含铬废水(W3-6),属溢流式连续性排放。 镀铬液挥发产生废气(G3-3),主要成分为硫酸雾、铬酸雾;镀铬槽定期清理,将上清液抽出重新配置后循环使用,底部废渣(S3-9)按危废处理;槽液过滤工序产生废滤芯(S3-10)按危险废物处置;清洗产生的含铬废水(W3-6)收集后进入含铬废水处理装置。 镀铜工艺其过程主要包括前处理、 镀覆处理,其具体工艺流程如下: (1)前处理 ①除油:镀件在机加工时都会使用油脂润滑,有时会留下很重的油污。所以,在电镀前要先除去这些油污。将镀件浸入加油碱性脱脂液的除油槽内,碱性脱脂液主要成分为 40~60g/LNaOH 、30~50g/LNa2CO3和 3~5g/LNa3PO4的混合溶液。工件上的油污与碱液发生皂化反应生成脂肪酸皂和甘油生成的脂肪酸皂和甘油溶于水,在水的作用下离开金属表面,达到除油的目的。 ②水洗:除油处理的工件先送入水洗槽中进浸洗(水洗槽中的水来自喷头喷洗过程中产生的水),而后经喷头喷洗(采用新水)完成清洗作业,清洗掉工件表面残留的碱液,以利于下一工序操作。在此过程中会产生含碱废水(W4-1),属溢流式连续性排放。 除油槽定期清理,将上清液抽出重新配置后循环使用,底部废渣(S4-1)按危废处理。该工序产生的酸碱废水(W4-1)含有较高浓度的油污,收集后进入前处理废水处理装置。 ③酸洗:将除油并冲洗干净的工件浸入酸洗槽中,利用4~6%的HC1水溶液,在常温条件下浸洗 10~20min,去除工件表面锈蚀,露出金属基体。酸洗除锈应严格控制酸洗程度,酸洗不足,氧化膜不能除尽,钢板表面不能完全活化;酸洗过度,易造成氢脆现象。因此酸洗槽内一般均添加适量酸洗抑制剂,以避免工件酸 洗过度。另外,在酸洗槽内添加酸雾覆盖剂,用以降低 HC1 挥发。 氧化层与盐酸反应: FeO+2HCl=FeCl2+H2O Fe3O4+8HCl=2FeCl3+FeCl2+4H2O Fe2O3+6HCl=2FeCl3+3H2O 铁基体与盐酸反应: Fe+2HCl=FeCl+H2 ↑ ④水洗:完成酸洗处理的工件先送入水洗槽中进浸洗(水洗槽中的水来自喷头喷洗过程中产生的水),而后经喷头喷洗(采用新水)完成清洗作业,清洗掉工件表面残留的酸液,以利于下一工序操作。在此过程中会产生酸碱废水(W4-2),属溢流式连续性排放。 酸洗过程中,盐酸和金属反应生成氢气,氢气析出的过程会带HCl,形成酸雾(G4-1);酸洗槽定期清理,将上清液抽出重新配置后循环使用,底部废渣(S4-2)按危废处理;清洗废水(W4-2)经收集后一起送入前处理废水处理设施。 (2)镀覆处理 ①镀铜 镀铜采用硫酸铜工艺,镀液成分为硫酸铜180-250g/L,硫酸40-70g/L。硫酸铜为镀铜的主盐,在水溶液中会离解成铜离子和硫酸根离子 CuSO4→Cu2++SO42- 在电镀过程中,铜离子带正电荷被电迁移到阴极(镀件)表面,并接受电子,还原成铜原子并形成镀层: Cu2++2e→Cu 硫酸是一种强电解质,在水中 100%电离,在镀液不仅起到导电的作用,而且对镀层的细化、均镀能力、覆盖能力都有较大影响 H2SO4→2H++SO42- 酸性镀铜所用阳极为含磷的磷铜板,磷铜作为阳极可以阻止岐化反应优于纯铜。磷铜在阳极获得电子生成二价铜离子,补充镀液中的铜。 Cu-2e→Cu2+ ②水洗 镀铜后设置水洗槽,清洗带出槽液,清洗产生含铜废水(W4-3)。 镀铜液内含有硫酸,硫酸挥发产生硫酸雾(G4-2),镀铜槽定期清理,将上清液抽出重新配置后循环使用,底部废渣(S4-3)按危废处理;槽液过滤工序产生废滤芯(S4-4)按危险废物处置。该工序产生的含铜废水(W4-3)收集后进入综合废水处理设施。 ③烘干:水洗后工件进行烘干处理,采用电加热。 |
无 | 是否属于重大变动:|
环保设施或环保措施
项目2#镀锡生产线废气经铬酸雾回收装置+碱液喷淋塔处理后由1根20m排气筒(DA004)排放;污水处理站废气经碱液喷淋塔处理后由1根 20m 排气筒(DA005);5#镀锌生产线废气经铬酸雾回收装置+碱液喷淋塔处理后由1根 20m 排气筒(DA006)排放;6#镀锌生产线废气经铬酸雾回收装置+碱液喷淋塔处理后由1根 20m 排气筒(DA007)排放;7#镀锌生产线废气经铬酸雾回收装置+碱液喷淋塔处理后由1根 20m 排气筒(DA008)排放;8#镀锌生产线废气经铬酸雾回收装置+碱液喷淋塔处理后由1根 20m 排气筒(DA009)排放;18#镀锌生产线、25#镀镍生产线、27#镀锡生产线废气经铬酸雾回收装置+碱液喷淋塔处理后由1根20m 排气筒(DA010)排放;15#镀铬生产线废气经铬酸雾回收装置+碱液喷淋塔处理后由1根 20m 排气筒(DA011)排放;12#镀镍生产线、17#镀铜生产线、23#镀锡生产线、24#镀锡生产线废气经铬酸雾回收装置+碱液喷淋塔处理后由1根 20m 排气筒(DA012)排放;16#镀铬生产线废气经铬酸雾回收装置+碱液喷淋塔处理后由1根 20m 排气筒(DA013)排放;28#镀锡生产线、32#镀铜生产线废气经碱液喷淋塔处理后由1根 20m 排气筒(DA014)排放;未被收集废气车间内无组织排放,同时加强管理,增加有组织收集率。 | 实际建设情况:项目2#镀锡生产线废气经铬酸雾回收装置+碱液喷淋塔处理后由1根20m排气筒(DA004)排放;污水处理站废气经碱液喷淋塔处理后由1根 20m 排气筒(DA005);5#镀锌生产线废气经铬酸雾回收装置+碱液喷淋塔处理后由1根 20m 排气筒(DA006)排放;6#镀锌生产线废气经铬酸雾回收装置+碱液喷淋塔处理后由1根 20m 排气筒(DA007)排放;7#镀锌生产线废气经铬酸雾回收装置+碱液喷淋塔处理后由1根 20m 排气筒(DA008)排放;8#镀锌生产线废气经铬酸雾回收装置+碱液喷淋塔处理后由1根 20m 排气筒(DA009)排放;18#镀锌生产线、25#镀镍生产线、27#镀锡生产线废气经铬酸雾回收装置+碱液喷淋塔处理后由1根20m 排气筒(DA010)排放;15#镀铬生产线废气经铬酸雾回收装置+碱液喷淋塔处理后由1根 20m 排气筒(DA011)排放;12#镀镍生产线、17#镀铜生产线、23#镀锡生产线、24#镀锡生产线废气经铬酸雾回收装置+碱液喷淋塔处理后由1根 20m 排气筒(DA012)排放;16#镀铬生产线废气经铬酸雾回收装置+碱液喷淋塔处理后由1根 20m 排气筒(DA013)排放;28#镀锡生产线、32#镀铜生产线废气经碱液喷淋塔处理后由1根 20m 排气筒(DA014)排放;未被收集废气车间内无组织排放,同时加强管理,增加有组织收集率。 |
无 | 是否属于重大变动:|
其他
无 | 实际建设情况:无 |
无 | 是否属于重大变动:|
3、污染物排放量
0 | 0 | 0 | 0 | 0 | 0 | 0 | |
0 | 0 | 0 | 0 | 0 | 0 | 0 | |
0 | 0 | 0 | 0 | 0 | 0 | 0 | |
0 | 0 | 0 | 0 | 0 | 0 | 0 | |
0 | 0 | 0 | 0 | 0 | 0 | 0 | |
0 | 0 | 0 | 0 | 0 | 0 | 0 | / |
0 | 0 | 0 | 0 | 0 | 0 | 0 | / |
0 | 0 | 0 | 0 | 0 | 0 | 0 | / |
0 | 0 | 0 | 0 | 0 | 0 | 0 | / |
0 | 0 | 0 | 0 | 0 | 0 | 0 | / |
4、环境保护设施落实情况
表1 水污染治理设施
1 | 项目主要废水为生产废水和生活污水前处理酸碱废水进入前处理废水处理设施处理后,进入综合污水处理设施; 含镍废水进入含镍废水处理设施处理后,由车间排放口(DW002)排入综合污水处理设施;含铬废水进入含铬废水处理设施处理后,由车间排放口(DW001)排入综合污水处理设施; 废水前处理废水处理设施出水以及其他酸碱废水、含锌废水、含铜废水进入综合废水处理设施(一级物化处理+二级生化处理);含镍废水处理设施出水、含铬废水处理 设施出水直接进入二级生化处理;****处理站出水部分进入反渗透装置回用于生产,部分经总排口(DW003****开发区污水处理厂。生活污水经化粪池处理后定期清掏,用作农肥,不外排。 | 《电镀污染物排放标准》(GB21900-2008)表2车间废水排放口浓度限值要求及《污水综合排放标准》GB8978-1996表4****经济开发区污水处理厂进水指标要求 TDS 执行《污水排入城镇下水道水质标准》(GBT31962-2015))表 1 中 B 级标准 | 已建设完成,投入使用 | 经检测,本项目DW001含铬废水排放口总铬排放浓度最大值为0.08mg/L、六价铬排放浓度最大值为0.004mg/L;DW002含镍废水排放口总镍排放浓度最大值为0.18mg/L;DW003厂区生产废水总排口pH排放浓度最大值为7.5无量纲、化学需氧量排放浓度最大值为49mg/L、生化需氧量排放浓度最大值为14.4mg/L、氨氮排放浓度最大值为1.51mg/L、悬浮物排放浓度最大值为18mg/L、总磷排放浓度最大值为0.27mg/L、总氮排放浓度最大值为3.94mg/L、总铜排放浓度最大值为0.2mg/L、总锌排放浓度最大值为0.2mg/L、石油类排放浓度最大值为0.89mg/L、溶解性总固体排放浓度最大值为1.58×103mg/L,满足《电镀污染物排放标准》(GB21900-2008)表2车间废水排放口浓度限值要求(总铬≤1.0mg/L、六价铬≤0.2mg/L、总镍≤0.5mg/L)及《污水综合排放标准》GB8978-1996表4****经济开发区污水处理厂进水指标要求 TDS 执行《污水排入城镇下水道水质标准》(GBT31962-2015))表 1 中 B 级标准(即pH:6.5~9、COD:500mg/L、BOD5:150mg/L、SS:250mg/L、TDS:2000mg/L、氨氮:30mg/L、总氮:45mg/L、总磷:2.5mg/L、石油类:20mg/L、总铜:2.0mg/L、总锌:2.0mg/L)。 |
表2 大气污染治理设施
1 | 项目2#镀锡生产线废气经铬酸雾回收装置+碱液喷淋塔处理后由1根20m排气筒(DA004)排放;污水处理站废气经碱液喷淋塔处理后由1根 20m 排气筒(DA005);5#镀锌生产线废气经铬酸雾回收装置+碱液喷淋塔处理后由1根 20m 排气筒(DA006)排放;6#镀锌生产线废气经铬酸雾回收装置+碱液喷淋塔处理后由1根 20m 排气筒(DA007)排放;7#镀锌生产线废气经铬酸雾回收装置+碱液喷淋塔处理后由1根 20m 排气筒(DA008)排放;8#镀锌生产线废气经铬酸雾回收装置+碱液喷淋塔处理后由1根 20m 排气筒(DA009)排放;18#镀锌生产线、25#镀镍生产线、27#镀锡生产线废气经铬酸雾回收装置+碱液喷淋塔处理后由1根20m 排气筒(DA010)排放;15#镀铬生产线废气经铬酸雾回收装置+碱液喷淋塔处理后由1根 20m 排气筒(DA011)排放;12#镀镍生产线、17#镀铜生产线、23#镀锡生产线、24#镀锡生产线废气经铬酸雾回收装置+碱液喷淋塔处理后由1根 20m 排气筒(DA012)排放;16#镀铬生产线废气经铬酸雾回收装置+碱液喷淋塔处理后由1根 20m 排气筒(DA013)排放;28#镀锡生产线、32#镀铜生产线废气经碱液喷淋塔处理后由1根 20m 排气筒(DA014)排放;未被收集废气车间内无组织排放,同时加强管理,增加有组织收集率。 | 《电镀污染物排放标准》(GB21900—2008)、《恶臭污染物排放标准》(GB 14554-93)、《大气污染物综合排放标准》(GB16297-1996) | 已建设完成,投入使用 | 经检测,本项目在2#镀锡生产线废气排气筒(DA004)硫酸雾实测浓度最大值为0.29mg/m3、排放速率最大值为1.50×10-2kg/h,满足《电镀污染物排放标准》(GB21900—2008)表 5 **企业大气污染物排放限值及表 6 基准排气量要求:基准排气量,即硫酸雾≤30mg/m3;镀锌:18.6 m3/m2,镀铬:74.4 m3/m2,镀镍、镀铜、镀锡:37.3 m3/m2; 污水处理站废气排气筒(DA005)硫酸雾实测浓度未检出,硫化氢实测浓度最大值为0.038mg/m3、排放速率为5.27×10-4kg/h,氨实测浓度最大值为0.38mg/m3、排放速率为5.31×10-3kg/h,臭气浓度实测浓度最大值为977(无量纲),满足《电镀污染物排放标准》(GB 21900-2008)表5**企业大气污染物排放限值及《恶臭污染物排放标准》(GB 14554-93)表 2 恶臭污染物排放标准值,即硫酸雾排放浓度≤30mg/m3、氨气≤8.7kg/h、硫化氢≤0.58kg/h、臭气浓度≤2000无量纲; 5#镀锌生产线废气排气筒(DA006)铬酸雾实测浓度最大值为0.018mg/m3、排放速率为4.68×10-4kg/h,氯化氢实测浓度最大值为3.50mg/m3,排放速率为8.93×10-2kg/h,满足《电镀污染物排放标准》(GB 21900-2008)表5**企业大气污染物排放限值,即氯化氢≤30mg/m3、铬酸雾≤0.05mg/m3;镀锌:18.6 m3/m2,镀铬:74.4 m3/m2,镀镍、镀铜、镀锡:37.3 m3/m2; 6#镀锌生产线废气排气筒(DA007)铬酸雾实测浓度最大值为0.025mg/m3、排放速率为1.05×10-3kg/h,氯化氢实测浓度最大值为3.62mg/m3、排放速率为0.154kg/h,满足《电镀污染物排放标准》(GB 21900-2008)表5**企业大气污染物排放限值,即氯化氢≤30mg/m3、铬酸雾≤0.05mg/m3;镀锌:18.6 m3/m2,镀铬:74.4 m3/m2,镀镍、镀铜、镀锡:37.3 m3/m2; 7#镀锌生产线废气排气筒(DA008)铬酸雾实测浓度最大值为0.029mg/m3、排放速率为1.08×10-3kg/h,氯化氢实测浓度最大值为2.45mg/m3、排放速率为9.10×10-2kg/h,满足《电镀污染物排放标准》(GB 21900-2008)表5**企业大气污染物排放限值,即氯化氢≤30mg/m3、铬酸雾≤0.05mg/m3;镀锌:18.6 m3/m2,镀铬:74.4 m3/m2,镀镍、镀铜、镀锡:37.3 m3/m2; 8#镀锌生产线废气排气筒出口(DA009)铬酸雾实测浓度最大值为0.019mg/m3、排放速率为6.74×10-4kg/h,氯化氢实测浓度最大值为3.42mg/m3、排放速率为0.123kg/h,满足《电镀污染物排放标准》(GB 21900-2008)表5**企业大气污染物排放限值,即氯化氢≤30mg/m3、铬酸雾≤0.05mg/m3;镀锌:18.6 m3/m2,镀铬:74.4 m3/m2,镀镍、镀铜、镀锡:37.3 m3/m2; 18#镀锌生产线、25#镀镍生产线、27#镀锡生产线废气排气筒(DA010)硫酸雾实测浓度最大值为0.32mg/m3、排放速率为1.24×10-2kg/h,铬酸雾实测浓度最大值为0.029mg/m3、排放速率为1.12×10-3kg/h,氯化氢实测浓度最大值为3.51mg/m3、排放速率为0.134kg/h,满足《电镀污染物排放标准》(GB 21900-2008)表5**企业大气污染物排放限值,即氯化氢≤30mg/m3、铬酸雾≤0.05mg/m3、硫酸雾≤30mg/m3;镀锌:18.6 m3/m2,镀铬:74.4 m3/m2,镀镍、镀铜、镀锡:37.3 m3/m2; 15#镀铬生产线废气排气筒(DA011)硫酸雾实测浓度最大值为0.37mg/m3、排放速率为1.91×10-2kg/h,铬酸雾实测浓度最大值为0.028mg/m3、排放速率为1.47×10-3kg/h,氯化氢实测浓度最大值为2.44mg/m3、排放速率为0.129kg/h,满足《电镀污染物排放标准》(GB 21900-2008)表5**企业大气污染物排放限值,即氯化氢≤30mg/m3、铬酸雾≤0.05mg/m3、硫酸雾≤30mg/m3;镀锌:18.6 m3/m2,镀铬:74.4 m3/m2,镀镍、镀铜、镀锡:37.3 m3/m2; 12#镀镍生产线、17#镀铜生产线、23#镀锡生产线、24#镀锡生产线废气排气筒(DA012)硫酸雾实测浓度最大值为0.34mg/m3、排放速率为2.50×10-2kg/h,铬酸雾实测浓度最大值为0.028mg/m3、排放速率为2.05×10-3kg/h,氯化氢实测浓度最大值为3.49mg/m3、排放速率为0.256kg/h,满足《电镀污染物排放标准》(GB 21900-2008)表5**企业大气污染物排放限值,即氯化氢≤30mg/m3、铬酸雾≤0.05mg/m3、硫酸雾≤30mg/m3;镀锌:18.6 m3/m2,镀铬:74.4 m3/m2,镀镍、镀铜、镀锡:37.3 m3/m2; 16#镀铬生产线废气排气筒(DA013)硫酸雾实测浓度最大值为0.33mg/m3、排放速率为5.64×10-3kg/h,铬酸雾实测浓度最大值为0.029mg/m3、排放速率为4.21×10-4kg/h,满足《电镀污染物排放标准》(GB 21900-2008)表5**企业大气污染物排放限值,即铬酸雾≤0.05mg/m3、硫酸雾≤30mg/m3;镀锌:18.6 m3/m2,镀铬:74.4 m3/m2,镀镍、镀铜、镀锡:37.3 m3/m2; 28 #镀锡生产线、32#镀铜生产线废气排气筒(DA014)硫酸雾实测浓度最大值为0.39mg/m3、排放速率为1.93×10-2kg/h,氯化氢实测浓度最大值为3.51mg/m3、排放速率为0.179kg/h,满足《电镀污染物排放标准》(GB 21900-2008)表5**企业大气污染物排放限值,即氯化氢≤30mg/m3、硫酸雾≤30mg/m3;镀锌:18.6 m3/m2,镀铬:74.4 m3/m2,镀镍、镀铜、镀锡:37.3 m3/m2。 经检测,本项目厂界硫酸雾周界外浓度未检出,氯化氢周界外浓度未检出,铬酸雾周界外浓度未检出,硫化氢周界外浓度最高值为0.005mg/m3,氨周界外浓度最高值为0.04mg/m3,臭气浓度周界外浓度最高值为16无量纲,满足《大气污染物综合排放标准》(GB16297-1996)表2无组织排放监控浓度限值及《恶臭污染物排放标准》(GB14554-93)表1二级改扩建标准(硫酸雾≤1.2mg/m3、氯化氢≤0.2mg/m3、铬酸雾≤0.006mg/m3、硫化氢≤0.06mg/m3、氨≤1.5mg/m3、臭气浓度≤20无量纲)。 |
表3 噪声治理设施
1 | 项目噪声污染防治,优先选用低噪声设备,基础减振、厂区内合理布置、厂房隔声。 | 《工业企业厂界环境噪声排放标准》(GB12348-2008)3类标准 | 已建设完成,投入使用 | 经检测,本项目厂界昼间噪声最大值为58dB(A),夜间噪声最大值为49,满足《工业企业厂界环境噪声排放标准》(GB12348-2008)3类标准限值要求(昼间≤65dB(A)、夜间≤55dB(A))。 |
表4 地下水污染治理设施
表5 固废治理设施
1 | 项目产生的固体废物表面处理废渣、含镍废渣、含铬废渣、含锌废渣、含铜废渣、含锡废渣、退镀废渣、废滤布、废滤芯、废反渗透膜、废包材、在线监测废液、含镍污泥、含铬污泥、综合污泥均属于危险废物,在危废暂存间暂存,定期交由有资质的单位进行处理;办公生活产生生活垃圾,收集后交由环卫部门处理。 | 已落实,与环评批复要求一致 |
表6 生态保护设施
表7 风险设施
5、环境保护对策措施落实情况
依托工程
无 | 验收阶段落实情况:无 |
/ |
环保搬迁
无 | 验收阶段落实情况:无 |
/ |
区域削减
无 | 验收阶段落实情况:无 |
/ |
生态恢复、补偿或管理
无 | 验收阶段落实情况:无 |
/ |
功能置换
无 | 验收阶段落实情况:无 |
/ |
其他
无 | 验收阶段落实情况:无 |
/ |
6、工程建设对项目周边环境的影响
/ |
/ |
/ |
/ |
/ |
/ |
7、验收结论
1 | 未按环境影响报告书(表)及其审批部门审批决定要求建设或落实环境保护设施,或者环境保护设施未能与主体工程同时投产使用 |
2 | 污染物排放不符合国家和地方相关标准、环境影响报告书(表)及其审批部门审批决定或者主要污染物总量指标控制要求 |
3 | 环境影响报告书(表)经批准后,该建设项目的性质、规模、地点、采用的生产工艺或者防治污染、防止生态破坏的措施发生重大变动,建设单位未重新报批环境影响报告书(表)或环境影响报告书(表)未经批准 |
4 | 建设过程中造成重大环境污染未治理完成,或者造成重大生态破坏未恢复 |
5 | 纳入排污许可管理的建设项目,无证排污或不按证排污 |
6 | 分期建设、分期投入生产或者使用的建设项目,其环境保护设施防治环境污染和生态破坏的能力不能满足主体工程需要 |
7 | 建设单位因该建设项目违反国家和地方环境保护法律法规受到处罚,被责令改正,尚未改正完成 |
8 | 验收报告的基础资料数据明显不实,内容存在重大缺项、遗漏,或者验收结论不明确、不合理 |
9 | 其他环境保护法律法规规章等规定不得通过环境保护验收 |
不存在上述情况 | |
验收结论 | 合格 |
招标导航更多>>
工程建筑
交通运输
环保绿化
医疗卫生
仪器仪表
水利水电
能源化工
弱电安防
办公文教
通讯电子
机械设备
农林牧渔
市政基建
政府部门
换一批
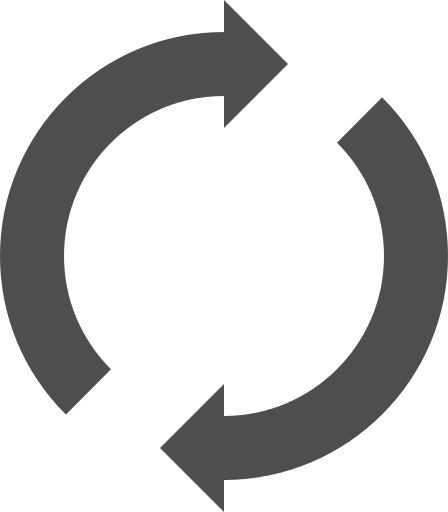