师宗县智能操作面板生产加工项目
1、建设项目基本信息
企业基本信息
**** | 建设单位代码类型:|
****0323MA6NPB3D0C | 建设单位法人:周伟明 |
徐改林 | 建设单位所在行政区划:**省**市**县 |
云****工业园区**片区 |
建设项目基本信息
**县智能操作面板生产加工项目 | 项目代码:**** |
建设性质: | |
2021版本:30--067- 金属表面处理及热处理加工 | 行业类别(国民经济代码):C3360-C3360-金属表面处理及热处理加工 |
建设地点: | **省**市**县 ****园区**片区 |
经度:104.06002 纬度: 24.78826 | ****机关:****环境局 |
环评批复时间: | 2023-08-21 |
曲环审〔2023〕56号 | 本工程排污许可证编号:****0323MA6NPB3D0C001P |
2024-05-14 | 项目实际总投资(万元):28000 |
415.3 | 运营单位名称:**** |
****0323MA6NPB3D0C | 验收监测(调查)报告编制机构名称:**** |
****0323MA6NPB3D0C | 验收监测单位:**环绿****公司,******公司,****公司 |
915********1674614,******公司,915********270937Q | 竣工时间:2024-05-01 |
2024-05-20 | 调试结束时间:2024-06-01 |
2024-12-05 | 验收报告公开结束时间:2025-01-02 |
验收报告公开载体: | https://www.js-eia.cn/ |
2、工程变动信息
项目性质
/ | 实际建设情况:/ |
/ | 是否属于重大变动:|
规模
一期工程生产金属面板(阳极氧化工艺)600万件/a | 实际建设情况:一期工程生产金属面板(阳极氧化工艺)600万件/a |
无 | 是否属于重大变动:|
生产工艺
一期工程:首先用切割机将铝合金板材切割成不同的大小和形状,再根据产品需求进行CNC加工或机加工,拉丝机拉丝或喷砂机喷砂,随后将产品进行阳极氧化处理或喷涂或喷漆,工件经阳极氧化处理或喷涂或喷漆后进入印刷线印刷商标、文字,最后经配件组装、检验合格后包装为成品出厂。 拉丝:通过研磨产品在工件表面形成线纹,起到装饰效果。 喷砂:利用高速砂流的冲击作用清理和粗化基体表面。 阳极氧化工艺说明: ① 除油:铝和铝合金制品,其表面黏附油污几乎是不可避免的,因为在机械加工过程中要使用润滑油,另外,由于操作人员手上分泌物多含有油脂,故用手接触过的表面也会黏附油脂。采用化学除油的方式。化学除油液的成分主要是NaOH和Na3PO4,浓度范围为5~10g/L,铝件在化学除油槽中浸泡3~5min,温度为60~65°C,升温采用电加热加热。 产污环节:除油槽中除油液浓度降低,则需添加除油粉和水,槽液失效后更换配制新的除油液,除油液7d更换一次。化学除油槽更换除油液后产生失效的除油液,为含油废水W2,主要为碱性废水、含COD、石油类、SS、总磷等污染物,每次排放2.4m3。除油槽运行过程中会产生少量槽渣S5。 ② 水洗:化学除油后的铝件送至水洗槽采用自来水进行清洗,以清洗掉工件表面附着的除油液,水洗过程为二级逆流清洗,即镀件按顺序先后进入水洗槽1→水洗槽2,清洗水则由最后一个清洗槽进入,进入方向为水的流向与镀件的走向相反。 产污环节:水洗过程产生废水W3,主要为含油废水,主要为碱性废水、含COD、石油类、SS等污染物。水洗水一般7天更换一次,每次更换4.8m3。 ③ 化学抛光:抛光是使铝件表面光亮、光滑,利于阳极氧化。化学抛光是获得铝合金光亮表面的一种操作简单而又应用广泛的方法。化学抛光溶液中除有磷酸以外,通常按照有硝酸或者无硝酸分为两大类型。由于含硝酸的抛光溶液产生大量黄烟,严重污染车间大气环境,因此无硝酸的抛光溶液被称为环保型抛光液。因此本项目铝件化学抛光根据产品质量的需求使用二酸(50%磷酸、50%硫酸混合溶液)工艺,工作液温度90~100℃,浸入60~180S。对于生产过程中的损耗通过定期补充水及添加药品保证抛光液的正常工艺,不更换。 产污环节:抛光过程会产生酸雾废气G5,主要为硫酸雾。 ④ 水洗:抛光后铝件采用自来水进行清洗,以清洗掉铝件表面附着的酸液,水洗过程为二级逆流清洗。 产污环节:水洗过程产生废水W4,主要为酸性废水,含pH、COD、SS、总铝、总锌、总铜、总铁、总铬、总锰、总磷等污染物。W4中的磷酸浓度很高,宜采用浓缩回用的方法减少磷酸排放。水洗水一般3天更换一次,每次更换4.8m3。 ⑤ 碱蚀:碱蚀目的是进一步除去油脂及污物,同时初步除去铝件表面的氧化膜,使基体金属裸露,表面得以活化。碱蚀采用氢氧化钠,浓度范围为40-60g/L,铝件在碱蚀槽内浸蚀60~180s,工作液温度20~40℃,升温采用电加热。 产污环节:碱液在使用过程中需定期添加氢氧化钠和水,并进行碱液的再生,槽液循环使用至不能利用时更换配制新的碱液,此过程会产生废碱液S7,产生量约2t/a。碱蚀槽运行过程中会产生少量槽渣S6。 ⑥ 水洗:碱蚀后铝件采用自来水进行清洗,以清洗掉铝件表面附着的碱液,水洗过程为一级浸洗。 产污环节:水洗过程产生废水W5,主要为碱性废水,含pH、COD、SS、总铝等污染物。水洗水一般3天更换一次,每次更换2.4m3。 ⑦ 中和出光:又称除灰,碱侵蚀后由于铝合金中的硅、镁、铁、铜之类的元素在表面沉积,会形成“污斑”,因此需加以中和出光,以获得光亮洁净的金属表面,常规工艺有硫酸除灰、硝酸除灰两种,本项目采用硝酸(70~100g/L)中和出光。 产污环节:中和过程中会产生酸雾废气G7,为硝酸雾,硝酸雾中硝酸不稳定,生成NOX。对于生产过程中的损耗通过定期补充水及添加药品保证中和液的正常工艺,不更换。 ⑧ 水洗和顶喷纯水洗:中和后铝件采用自来水进行清洗,以清洗掉铝件表面附着的酸液,水洗过程为二级逆流水洗。水洗后进行顶喷纯水洗,****设备处理后的软水。 产污环节:水洗过程产生废水W6和W7,主要为酸性废水,含pH、COD、氨氮、SS、总铝、总锌、总铜、总铁、总铬、总锰、总氮等污染物。水洗水一般3天更换一次,每次更换4.8m3。 ⑨ 氧化:铝阳极氧化是一种电解过程,在该过程中铝或铝合金表面通常转化为一层氧化膜,这层膜具有防护性、装饰性、功能性等。阳极氧化的种类很多,较常用的有硫酸法,此外还有硝酸、铬酸、硬质、瓷质法等。本项目将采用硫酸阳极氧化。以铝和铝合金制品为阳极置于电解质溶液中,利用电解质作用,使其表面形成氧化膜的过程,称之为铝和铝合金制品的阳极氧化处理。氧化膜的成长过程包含着相辅相成的两个方面:1、膜的电化学生成过程;2、膜的化学溶解过程。两者缺一不可,而且必须使膜的生成速度恒大于溶解速度。 硫酸阳极氧化,氧化膜形成机理如下:通电以后,阳极和阴极上便发生如下的反应: 阴极区:2H++2e-→H2↑ 4OH-+4e-→2H2O+O2↑ 阳极区:2Al3++3O2-→Al2O3+热量 按反应式,开始在型材表面形成一层薄而致密的氧化膜后,一部分膜由于和硫酸起反应而发生溶解: Al2O3+3H2SO4→Al2(SO4)3+3H2O 于是,使致密的氧化膜变得多孔。随之电解液又渗入到空隙中同露出的铝作用,生成一层新的氧化膜,使整个氧化膜好像得到修补一样,接着新的完整的氧化膜又发生溶解。如此循环,不断地靠金属表面处生成新的氧化膜、也不断地创造出多孔的外层膜,结果生成了由厚而多孔的外层和薄而致密的内层所组成的氧化膜。阳极氧化产品有些用作装饰、有些需要高耐磨的特性、有些是工用铝型材,根据产品要求的不同,槽液中硫酸浓度、氧化时间、温度、电压、电流密度、阴极材料等均不尽相同。本评价采用通用工艺进行分析。 通用工艺氧化槽槽液一般配方及主要工艺条件如下: H2SO4 180~200g/L 铝离子<20g/L 温度15~25℃ 时间30~40min 氧化槽槽液中铝离子浓度在10~12/L时氧化效果最好,超过20g/L则会在型材表面产生白斑或白点,使氧化膜的吸附能力下降,染色困难,过低(<5g/L)则会氧化难以进行,无法得到好的氧化膜。 产污环节:阳极氧化过程会产生一定量的硫酸雾废气G8,主要为挥发的H2SO4。当氧化槽液中杂质增多,对氧化槽进行清理,产生槽渣S8,属于危险废物。 ⑩ 水洗、水洗+喷淋和超声波水洗:氧化后铝件采用自来水进行清洗,以清洗掉铝件表面附着的氧化液,水洗过程为一级浸洗+一级浸洗和喷淋+超声波水洗。 产污环节:水洗过程产生废水W8~W10,主要为酸性废水,含pH、COD、SS、总铝等污染物。水洗水一般3天更换一次,每次更换7.2m3。 水洗后根据产品需要,生产线分为2条,1条生产线有电解着色工序(后续流程为~),另外1条生产线有电解抛光工序(后续流程为~)。 ⑾ 水洗和水洗+喷淋:超声波水洗后的工件,再次进行二级逆流水洗和水洗+喷淋水洗。 产污环节:水洗过程产生废水W11~W12,含酸性pH、COD、SS、总铝等污染物。水洗水一般3天更换一次,每次更换7.2m3。 ⑿ 染色 本工艺采用有机染料作为染色剂,有红、黑、蓝、绿、黄、棕、紫等颜色,主要为铬配位偶氮系酸性染料、铜配位肽菁类酸性染料、有机化合物、有机酸盐染料,含铬、铜等重金属,未使用国家规定要逐步淘汰和禁用的染料和高毒性的稀有金属进行着色处理,未使用可分解出有害芳香胺的染料。 染色过程:加纯水至槽体的2/3~3/4,将有机染料在溶解罐中用槽液溶解;在搅拌状态下,缓慢加纯水至液位。将铝制品氧化水洗后以最大角度进入染色槽进行染色。有机染料浓度约4—6g/L,温度为25~45°C,pH5~6,染色时间1~20min。槽液升温采用电加热。染色液循环利用,对于使用过程中的损耗通过定期补充水及添加染料保证正常工艺。每个颜色均有单独的染色槽,染色液不需要进行更换。 产污环节:无污染物产生。 ⒀ 水洗和水洗+喷淋 染色后铝件采用自来水进行清洗,以清洗掉铝件表面附着的染色液,水洗过程为一级浸洗和水洗+喷淋。 产污环节:水洗过程产生废水W13~W20和W23,含酸性pH、COD、氨氮、SS、总铝、总铬、铜等。水洗水一般7天更换一次,每个染色后水洗工序均每次更换4.8m3。 ⒁ 电解着色 型材转移到酸性金属盐溶液中施以交流电解处理,将金属微粒不可逆地电沉积在氧化膜孔隙的底部,凡能够由水溶液中电沉积出来的金属,大部分可以用在电解着色上。本项目电解着色剂主要成分为硫酸亚锡盐。电解着色槽槽液内硫酸浓度较低,由同类型企业的调查可知,电解着色过程中一般不会产生酸雾。着色液不需要进行更换。 产污环节:无污染物产生。 ⒂ 水洗和水洗+喷淋 电解着色后对工件进行水洗和水洗+喷淋清洗,清除表面的着色液。 产污环节:水洗过程产生废水W21~W22,含酸性废水、COD、氨氮、SS、总铝、总铬、铜等。水洗水一般7天更换一次,每次更换4.8m。 ⒃ 封闭:铝件需采用封闭剂浸泡,在表面形成一层致密的保护膜,增强铝件的防锈、防腐蚀、防变色能力。 封闭过程:加水至槽体的2/3~3/4,加入醋酸镍封闭剂;在搅拌状态下,缓慢加纯水至液位。将铝制品氧化水洗后以最大角度进入封闭槽进行封闭。封闭液浓度为醋酸镍20g/L,醋酸钠1.3g/L,苯磺酸钠4g/L,pH5~6,温度为85~ 90°C,封闭时间2~10min。封闭液升温由电加热。 封闭的主要反应为: Al2O3+nH2O→Al2O3:nH2O Ni2++2H2O→Ni(OH)2+2H+ 封闭液循环利用,对于使用过程中的损耗通过定期补充水及添加封闭剂保证正常工艺,循环使用至不能利用时更换配制新的封闭液,7d更换一次。 产污环节:更换废封闭液产生含镍废水W24、W27和W30,含pH、COD、氨氮、总镍等污染物。每次排放7.2m3。 ⒄ 回收、水洗 封闭槽后设回收工序,用于回收铝件表面的封闭液,回收槽中的封闭液补充到封闭槽。回收后铝件采用水洗、水洗+喷淋和热纯水洗(软水制备设备软水)进行清洗,以清洗掉铝件表面附着的封液。 产污环节:水洗过程产生废水W25-26、W28-29和W31-33,含酸性废水、COD、SS、总镍、总铝等。水洗水一般7天更换一次,每次更换16.8m3。 ⒅ 烘干 采用电加热对水洗后工件进行烘干,烘干后下挂。 ⒆ 电解抛光 以被抛工件为阳极,不溶性金属为阴极,两极同时浸入到电解槽中,通以直流电而产生有选择性的阳极溶解,从而达到工件表面光亮度增大的效果。本项目根据产品需求进行化学抛光或电解抛光,抛光液的主要成分均为磷酸和硫酸。 产污环节:电解抛光过程会产生酸雾废气G9,为硫酸雾。电抛液定期补充损耗,不进行更换。 ⒇ 水洗:电解抛光后铝件采用自来水进行清洗,以清洗掉铝件表面附着的酸液,水洗过程为二级逆流清洗。 产污环节:水洗过程产生废水W34,主要为酸性废水,为酸性废水、含COD、SS、总铝、总锌、总铜、总铁、总铬、总锰、总磷等污染物。水洗水一般3天更换一次,每次更换2m3。 染色 本工艺采用有机染料作为染色剂,有红、黑、蓝、绿、黄、棕、紫等颜色,主要为铬配位偶氮系酸性染料、铜配位肽菁类酸性染料、有机化合物、有机酸盐,含铬、铜等重金属,未使用国家规定要逐步淘汰和禁用的染料和高毒性的稀有金属进行着色处理,未使用可分解出有害芳香胺的染料。 染色过程:加纯水至槽体的2/3~3/4,将有机染料在溶解罐中用槽液溶解;在搅拌状态下,缓慢加纯水至液位。将铝制品氧化水洗后以最大角度进入染色槽进行染色。有机染料浓度约4—6g/L,温度为25~45°C,pH5~6,染色时间1~20min。槽液升温采用电加热。染色液循环利用,对于使用过程中的损耗通过定期补充水及添加染料保证正常工艺。每个颜色均有单独的染色槽,染色液不需要进行更换。 产污环节:无污染物产生。 水洗 着色后铝件采用纯水进行清洗,以清洗掉铝件表面附着的染色液,水洗过程为一级浸洗。 产污环节:水洗过程产生废水W35~W37,为酸性废水、含pH、COD、氨氮、SS、总铝等。水洗水一般7天更换一次,每次更换2.1m。 封闭:铝件需采用封闭剂浸泡,在表面形成一层致密的保护膜,增强铝件的防锈、防腐蚀、防变色能力。 封闭过程:加水至槽体的2/3~3/4,加入醋酸镍封闭剂;在搅拌状态下,缓慢加纯水至液位。将铝制品氧化水洗后以最大角度进入封闭槽进行封闭。封闭液浓度为醋酸镍20g/L,醋酸钠1.3g/L,苯磺酸钠4g/L,pH5~6,温度为85~90°C,封闭时间2~10min。封闭液升温由电加热。 封闭的主要反应为: Al2O3+nH2O→Al2O3:nH2O Ni2++2H2O→Ni(OH)2+2H+ 封闭液循环利用,对于使用过程中的损耗通过定期补充水及添加封闭剂保证正常工艺,循环使用至不能利用时更换配制新的封闭液,7d更换一次。 产污环节:更换废封闭液产生含镍废水W38,为酸性废水、含pH、COD、SS、总镍、总铝等污染物。每次排放0.7m3。 回收、水洗 封闭槽后设回收工序,用于回收铝件表面的封闭液,回收槽中的封闭液补充到封闭槽。回收后铝件采用一级浸洗进行清洗,以清洗掉铝件表面附着的封液。 产污环节:水洗过程产生含镍废水W39,主要为酸性废水、含pH、COD、SS、总镍、总铝等。水洗水一般7天更换一次,每次更换0.7m。 烘干 采用电加热对水洗后工件进行烘干,烘干后下挂。 印刷网版制作工艺流程简述: 首先,根据产品的大小、表面纹路选择网框及网布,将网纱固定在框上。然后上感光胶,在碘镓灯下晒版。接着喷水使感光浆先行吸水溶涨,静置1~2分钟,再用高压水枪呈扇形来回显影,直至图像完全清晰为止。(注:高压水洗不能离网版太近,否则压力太大使线条易产生锯齿,严重时部分网浆会被冲掉。)将网版上水分干燥,温度不可过高,否则会产生网版张力变化,一般为40~45℃。对针孔及部分不需丝印的定位孔等需加以修补和检查。进行二次曝光进一步提高感光浆与网纱的附着力,增加使用寿命。最后封网,网版制作完成。 | 实际建设情况:首先用切割机将铝合金板材切割成不同的大小和形状,再根据产品需求进行CNC加工或机加工,拉丝机拉丝或喷砂机喷砂,随后将产品进行阳极氧化处理或喷涂或喷漆,工件经阳极氧化处理,检验合格后包装出厂运输至****同一组装出售。 注:环评中工艺中的印刷线本次一期项目未建设,印刷工艺委托****进行。 拉丝:通过研磨产品在工件表面形成线纹,起到装饰效果。 喷砂:利用高速砂流的冲击作用清理和粗化基体表面。 ① 除油:铝和铝合金制品,其表面黏附油污几乎是不可避免的,因为在机械加工过程中要使用润滑油,另外,由于操作人员手上分泌物多含有油脂,故用手接触过的表面也会黏附油脂。采用化学除油的方式。化学除油液的成分主要是NaOH和Na3PO4,浓度范围为5~10g/L,铝件在化学除油槽中浸泡3~5min,温度为60~65°C,升温采用电加热加热。 产污环节:除油槽中除油液浓度降低,则需添加除油粉和水,槽液失效后更换配制新的除油液,除油液7d更换一次。化学除油槽更换除油液后产生失效的除油液,为含油废水W2,主要为碱性废水、含COD、石油类、SS、总磷等污染物,每次排放2.4m3。除油槽运行过程中会产生少量槽渣S5。 ② 水洗:化学除油后的铝件送至水洗槽采用自来水进行清洗,以清洗掉工件表面附着的除油液,水洗过程为二级逆流清洗,即镀件按顺序先后进入水洗槽1→水洗槽2,清洗水则由最后一个清洗槽进入,进入方向为水的流向与镀件的走向相反。 产污环节:水洗过程产生废水W3,主要为含油废水,主要为碱性废水、含COD、石油类、SS等污染物。水洗水一般7天更换一次,每次更换4.8m3。 ③ 化学抛光:抛光是使铝件表面光亮、光滑,利于阳极氧化。化学抛光是获得铝合金光亮表面的一种操作简单而又应用广泛的方法。化学抛光溶液中除有磷酸以外,通常按照有硝酸或者无硝酸分为两大类型。由于含硝酸的抛光溶液产生大量黄烟,严重污染车间大气环境,因此无硝酸的抛光溶液被称为环保型抛光液。因此本项目铝件化学抛光根据产品质量的需求使用二酸(50%磷酸、50%硫酸混合溶液)工艺,工作液温度90~100℃,浸入60~180S。对于生产过程中的损耗通过定期补充水及添加药品保证抛光液的正常工艺,不更换。 产污环节:抛光过程会产生酸雾废气G5,主要为硫酸雾。 ④ 水洗:抛光后铝件采用自来水进行清洗,以清洗掉铝件表面附着的酸液,水洗过程为二级逆流清洗。 产污环节:水洗过程产生废水W4,主要为酸性废水,含pH、COD、SS、总铝、总锌、总铜、总铁、总铬、总锰、总磷等污染物。W4中的磷酸浓度很高,宜采用浓缩回用的方法减少磷酸排放。水洗水一般3天更换一次,每次更换4.8m3。 ⑤ 碱蚀:碱蚀目的是进一步除去油脂及污物,同时初步除去铝件表面的氧化膜,使基体金属裸露,表面得以活化。碱蚀采用氢氧化钠,浓度范围为40-60g/L,铝件在碱蚀槽内浸蚀60~180s,工作液温度20~40℃,升温采用电加热。 产污环节:碱液在使用过程中需定期添加氢氧化钠和水,并进行碱液的再生,槽液循环使用至不能利用时更换配制新的碱液,此过程会产生废碱液S7,产生量约2t/a。碱蚀槽运行过程中会产生少量槽渣S6。 ⑥ 水洗:碱蚀后铝件采用自来水进行清洗,以清洗掉铝件表面附着的碱液,水洗过程为一级浸洗。 产污环节:水洗过程产生废水W5,主要为碱性废水,含pH、COD、SS、总铝等污染物。水洗水一般3天更换一次,每次更换2.4m3。 ⑦ 中和出光:又称除灰,碱侵蚀后由于铝合金中的硅、镁、铁、铜之类的元素在表面沉积,会形成“污斑”,因此需加以中和出光,以获得光亮洁净的金属表面,常规工艺有硫酸除灰、硝酸除灰两种,本项目采用硝酸(70~100g/L)中和出光。 产污环节:中和过程中会产生酸雾废气G7,为硝酸雾,硝酸雾中硝酸不稳定,生成NOX。对于生产过程中的损耗通过定期补充水及添加药品保证中和液的正常工艺,不更换。 ⑧ 水洗和顶喷纯水洗:中和后铝件采用自来水进行清洗,以清洗掉铝件表面附着的酸液,水洗过程为二级逆流水洗。水洗后进行顶喷纯水洗,****设备处理后的软水。 产污环节:水洗过程产生废水W6和W7,主要为酸性废水,含pH、COD、氨氮、SS、总铝、总锌、总铜、总铁、总铬、总锰、总氮等污染物。水洗水一般3天更换一次,每次更换4.8m3。 ⑨ 氧化:铝阳极氧化是一种电解过程,在该过程中铝或铝合金表面通常转化为一层氧化膜,这层膜具有防护性、装饰性、功能性等。阳极氧化的种类很多,较常用的有硫酸法,此外还有硝酸、铬酸、硬质、瓷质法等。本项目将采用硫酸阳极氧化。以铝和铝合金制品为阳极置于电解质溶液中,利用电解质作用,使其表面形成氧化膜的过程,称之为铝和铝合金制品的阳极氧化处理。氧化膜的成长过程包含着相辅相成的两个方面:1、膜的电化学生成过程;2、膜的化学溶解过程。两者缺一不可,而且必须使膜的生成速度恒大于溶解速度。 硫酸阳极氧化,氧化膜形成机理如下:通电以后,阳极和阴极上便发生如下的反应: 阴极区:2H++2e-→H2↑ 4OH-+4e-→2H2O+O2↑ 阳极区:2Al3++3O2-→Al2O3+热量 按反应式,开始在型材表面形成一层薄而致密的氧化膜后,一部分膜由于和硫酸起反应而发生溶解: Al2O3+3H2SO4→Al2(SO4)3+3H2O 于是,使致密的氧化膜变得多孔。随之电解液又渗入到空隙中同露出的铝作用,生成一层新的氧化膜,使整个氧化膜好像得到修补一样,接着新的完整的氧化膜又发生溶解。如此循环,不断地靠金属表面处生成新的氧化膜、也不断地创造出多孔的外层膜,结果生成了由厚而多孔的外层和薄而致密的内层所组成的氧化膜。阳极氧化产品有些用作装饰、有些需要高耐磨的特性、有些是工用铝型材,根据产品要求的不同,槽液中硫酸浓度、氧化时间、温度、电压、电流密度、阴极材料等均不尽相同。本评价采用通用工艺进行分析。 通用工艺氧化槽槽液一般配方及主要工艺条件如下: H2SO4 180~200g/L 铝离子<20g/L 温度15~25℃ 时间30~40min 氧化槽槽液中铝离子浓度在10~12/L时氧化效果最好,超过20g/L则会在型材表面产生白斑或白点,使氧化膜的吸附能力下降,染色困难,过低(<5g/L)则会氧化难以进行,无法得到好的氧化膜。 产污环节:阳极氧化过程会产生一定量的硫酸雾废气G8,主要为挥发的H2SO4。当氧化槽液中杂质增多,对氧化槽进行清理,产生槽渣S8,属于危险废物。 ⑩ 水洗、水洗+喷淋和超声波水洗:氧化后铝件采用自来水进行清洗,以清洗掉铝件表面附着的氧化液,水洗过程为一级浸洗+一级浸洗和喷淋+超声波水洗。 产污环节:水洗过程产生废水W8~W10,主要为酸性废水,含pH、COD、SS、总铝等污染物。水洗水一般3天更换一次,每次更换7.2m3。 水洗后根据产品需要,生产线分为2条,1条生产线有电解着色工序(后续流程为~),另外1条生产线有电解抛光工序(后续流程为~)。 ⑾ 水洗和水洗+喷淋:超声波水洗后的工件,再次进行二级逆流水洗和水洗+喷淋水洗。 产污环节:水洗过程产生废水W11~W12,含酸性pH、COD、SS、总铝等污染物。水洗水一般3天更换一次,每次更换7.2m3。 ⑿ 染色 本工艺采用有机染料作为染色剂,有红、黑、蓝、绿、黄、棕、紫等颜色,主要为铬配位偶氮系酸性染料、铜配位肽菁类酸性染料、有机化合物、有机酸盐染料,含铬、铜等重金属,未使用国家规定要逐步淘汰和禁用的染料和高毒性的稀有金属进行着色处理,未使用可分解出有害芳香胺的染料。 染色过程:加纯水至槽体的2/3~3/4,将有机染料在溶解罐中用槽液溶解;在搅拌状态下,缓慢加纯水至液位。将铝制品氧化水洗后以最大角度进入染色槽进行染色。有机染料浓度约4—6g/L,温度为25~45°C,pH5~6,染色时间1~20min。槽液升温采用电加热。染色液循环利用,对于使用过程中的损耗通过定期补充水及添加染料保证正常工艺。每个颜色均有单独的染色槽,染色液不需要进行更换。 产污环节:无污染物产生。 ⒀ 水洗和水洗+喷淋 染色后铝件采用自来水进行清洗,以清洗掉铝件表面附着的染色液,水洗过程为一级浸洗和水洗+喷淋。 产污环节:水洗过程产生废水W13~W20和W23,含酸性pH、COD、氨氮、SS、总铝、总铬、铜等。水洗水一般7天更换一次,每个染色后水洗工序均每次更换4.8m3。 ⒁ 电解着色 型材转移到酸性金属盐溶液中施以交流电解处理,将金属微粒不可逆地电沉积在氧化膜孔隙的底部,凡能够由水溶液中电沉积出来的金属,大部分可以用在电解着色上。本项目电解着色剂主要成分为硫酸亚锡盐。电解着色槽槽液内硫酸浓度较低,由同类型企业的调查可知,电解着色过程中一般不会产生酸雾。着色液不需要进行更换。 产污环节:无污染物产生。 ⒂ 水洗和水洗+喷淋 电解着色后对工件进行水洗和水洗+喷淋清洗,清除表面的着色液。 产污环节:水洗过程产生废水W21~W22,含酸性废水、COD、氨氮、SS、总铝、总铬、铜等。水洗水一般7天更换一次,每次更换4.8m。 ⒃ 封闭:铝件需采用封闭剂浸泡,在表面形成一层致密的保护膜,增强铝件的防锈、防腐蚀、防变色能力。 封闭过程:加水至槽体的2/3~3/4,加入醋酸镍封闭剂;在搅拌状态下,缓慢加纯水至液位。将铝制品氧化水洗后以最大角度进入封闭槽进行封闭。封闭液浓度为醋酸镍20g/L,醋酸钠1.3g/L,苯磺酸钠4g/L,pH5~6,温度为85~ 90°C,封闭时间2~10min。封闭液升温由电加热。 封闭的主要反应为: Al2O3+nH2O→Al2O3:nH2O Ni2++2H2O→Ni(OH)2+2H+ 封闭液循环利用,对于使用过程中的损耗通过定期补充水及添加封闭剂保证正常工艺,循环使用至不能利用时更换配制新的封闭液,7d更换一次。 产污环节:更换废封闭液产生含镍废水W24、W27和W30,含pH、COD、氨氮、总镍等污染物。每次排放7.2m3。 ⒄ 回收、水洗 封闭槽后设回收工序,用于回收铝件表面的封闭液,回收槽中的封闭液补充到封闭槽。回收后铝件采用水洗、水洗+喷淋和热纯水洗(软水制备设备软水)进行清洗,以清洗掉铝件表面附着的封液。 产污环节:水洗过程产生废水W25-26、W28-29和W31-33,含酸性废水、COD、SS、总镍、总铝等。水洗水一般7天更换一次,每次更换16.8m3。 ⒅ 烘干 采用电加热对水洗后工件进行烘干,烘干后下挂。 ⒆ 电解抛光 以被抛工件为阳极,不溶性金属为阴极,两极同时浸入到电解槽中,通以直流电而产生有选择性的阳极溶解,从而达到工件表面光亮度增大的效果。本项目根据产品需求进行化学抛光或电解抛光,抛光液的主要成分均为磷酸和硫酸。 产污环节:电解抛光过程会产生酸雾废气G9,为硫酸雾。电抛液定期补充损耗,不进行更换。 ⒇ 水洗:电解抛光后铝件采用自来水进行清洗,以清洗掉铝件表面附着的酸液,水洗过程为二级逆流清洗。 产污环节:水洗过程产生废水W34,主要为酸性废水,为酸性废水、含COD、SS、总铝、总锌、总铜、总铁、总铬、总锰、总磷等污染物。水洗水一般3天更换一次,每次更换2m3。 染色 本工艺采用有机染料作为染色剂,有红、黑、蓝、绿、黄、棕、紫等颜色,主要为铬配位偶氮系酸性染料、铜配位肽菁类酸性染料、有机化合物、有机酸盐,含铬、铜等重金属,未使用国家规定要逐步淘汰和禁用的染料和高毒性的稀有金属进行着色处理,未使用可分解出有害芳香胺的染料。 染色过程:加纯水至槽体的2/3~3/4,将有机染料在溶解罐中用槽液溶解;在搅拌状态下,缓慢加纯水至液位。将铝制品氧化水洗后以最大角度进入染色槽进行染色。有机染料浓度约4—6g/L,温度为25~45°C,pH5~6,染色时间1~20min。槽液升温采用电加热。染色液循环利用,对于使用过程中的损耗通过定期补充水及添加染料保证正常工艺。每个颜色均有单独的染色槽,染色液不需要进行更换。 产污环节:无污染物产生。 水洗 着色后铝件采用纯水进行清洗,以清洗掉铝件表面附着的染色液,水洗过程为一级浸洗。 产污环节:水洗过程产生废水W35~W37,为酸性废水、含pH、COD、氨氮、SS、总铝等。水洗水一般7天更换一次,每次更换2.1m。 封闭:铝件需采用封闭剂浸泡,在表面形成一层致密的保护膜,增强铝件的防锈、防腐蚀、防变色能力。 封闭过程:加水至槽体的2/3~3/4,加入醋酸镍封闭剂;在搅拌状态下,缓慢加纯水至液位。将铝制品氧化水洗后以最大角度进入封闭槽进行封闭。封闭液浓度为醋酸镍20g/L,醋酸钠1.3g/L,苯磺酸钠4g/L,pH5~6,温度为85~90°C,封闭时间2~10min。封闭液升温由电加热。 封闭的主要反应为: Al2O3+nH2O→Al2O3:nH2O Ni2++2H2O→Ni(OH)2+2H+ 封闭液循环利用,对于使用过程中的损耗通过定期补充水及添加封闭剂保证正常工艺,循环使用至不能利用时更换配制新的封闭液,7d更换一次。 产污环节:更换废封闭液产生含镍废水W38,为酸性废水、含pH、COD、SS、总镍、总铝等污染物。每次排放0.7m3。 回收、水洗 封闭槽后设回收工序,用于回收铝件表面的封闭液,回收槽中的封闭液补充到封闭槽。回收后铝件采用一级浸洗进行清洗,以清洗掉铝件表面附着的封液。 产污环节:水洗过程产生含镍废水W39,主要为酸性废水、含pH、COD、SS、总镍、总铝等。水洗水一般7天更换一次,每次更换0.7m。 烘干 采用电加热对水洗后工件进行烘干,烘干后下挂。 环评中工艺中的印刷线本次一期项目未建设,印刷工艺委托****进行。 |
环评中工艺中的印刷线本次一期项目未建设,印刷工艺委托****进行。 | 是否属于重大变动:|
环保设施或环保措施
水环境保护措施:规范建设雨污分流系统,在厂区内设置的污水收集输送系统,不得采取明沟布设。电抛光废水进入抛光废水处理系统(规模不小于5m3/d,采用“过滤系统→低温蒸发→浓酸回收箱”处理工艺)处理,浓缩的酸浓液回到抛光槽,不外排;含镍废水进入含镍废水处理系统(规模不小于5m3/d,采用“一体化物化处理装置→回调箱→**箱→多介质过滤器→活性炭吸附器→两级重金属吸附罐”处理工艺)处理,总镍满足《电镀污染物排放标准》(GB21900-2008)中车间或生产设施排放限值,其余指标满足《污水排入城镇下水道水质标准》(GB/T31962-2015)限值要求后排入达标排放池,随同****工业园区污水管网****处理站。**1****处理站(规模不小于23m3/d,采用“芬顿工艺→物化反应→高效斜管沉淀池→回调箱中和pH→多介质过滤和活性炭过滤”处理工艺),染色废水经脱色处****处理站,脱脂废水、金属CNC废水、玻璃加工废水经“一体化物化处理装置→批次反应箱”处****处理站,阳极氧化生产线和喷粉生产线其余水洗槽废水、废气处理废水、制软水****处理站处理,食堂废水经隔油池沉淀后与其他生活污水进入化粪池处理,废水总铬、总镍满足《电镀污染物排放标准》(GB21900-2008)车间或生产设施排放限值,总铝、总锌、总铜、总铁满足《电镀污染物排放标准》(GB21900-2008),其余指标满足《污水排入城镇下水道水质标准》(GB/T31962-2015)限值要求后进入达标排放池,通****工业园区污水管网****处理站。你公司应进一步核实废水水质、处理工艺及处理系统规模,加强各污染处理设施运行管理,确保各污水处理设施正常运行,做到废水达标排放。 落实分区防控措施。处理站、化学品仓库、喷漆车间、酸洗磷化工段、阳极氧化间、污泥暂存间、危险废物暂存间等区域采取重点防渗,防渗层按等效黏土防渗层厚度不小于6.0m,渗透系数不大于1x10-7cm/s,或参考《危险废物填埋污染控制标准》(GB18598-2019)要求进行防渗;生产车间、一般固废暂存间等区域采取一般防渗,防渗层按等效黏土防渗层厚度不小于1.5m,渗透系数不大于1x10-7cm/s,或参考《****填埋场污染控制标准》(GB16889-2008)要求进行防渗;其他区域采取一般地面硬化。根据区域水文地质情况,合理设置地下水跟踪监测井,定期进行跟踪监测,根据监测情况及时完善相应的污染防治措施。 大气污染防治措施:铝合金喷砂工段产生的含颗粒物废气经袋式除尘器处理满足《大气污染物综合排放标准》(GB16297-1996)限值要求后,通过1根15m高的排气简(DA001)排放。中和出光槽和阳极氧化槽酸雾通过引风机收集后接入1#酸雾吸收塔处理后通过1根15m高的排气筒(DA002)排放;电解抛光和喷粉车间酸洗槽酸雾通过引风机收集后接入2#酸雾吸收塔处理后通过1根15m高的排气简(DA003)排放;硫酸雾、氮氧化物满足《电镀污染物排放标准》(GB21900-2008)限值要求。喷粉车间含颗粒物废气收集后经布袋除尘处理满足《大气污染物综合排放标准》(GB16297-1996)限值要求后,通过1根15m高的排气筒(DA004)排放。固化废气及印刷油墨废气主要污染物为非甲烷总烃、二甲苯,通过一套“换热器+二级活性炭吸附”装置处理满足《大气污染物综合排放标准》(GB16297-1996)限值要求后,通过1根15m高的排气简(DA005)排放。喷漆废气主要污染物为颗粒物、非甲烷总烃、二甲苯,通过一套“换热器+二级活性炭吸附”装置处理满足《大气污染物综合排放标准》(GB16297-1996)限值要求后,通过1根15m高的排气筒(DA006)排放。加强对废气无组织排放的管理,减少无组织排放量,确保无组织排放非甲烷总烃、二甲苯满足《大气污染物综合排放标准》(GB16297-1996)相关要求;厂界内车间外的非甲烷总烃满足《挥发性有机物无组织排放控制标准》(GB37822-2019)相关要求。 项目设置100m的卫生防护距离,你****政府及规划部门报告,严格控制厂界周围规划用地,明确提出项目卫生防护距****学校、医院、居民区等环境敏感目标。 固体废物的贮存、处理和处置措施。一般固体废物临时堆存场所应符合《一般工业固体废物贮存和填埋污染控制标准》(GB18599-2020)要求,边角料、废铁砂、废包装材料、铝合金板材加工和喷砂除尘器收尘、喷粉不合格品、金属面板和玻璃面板次品等分类收集后暂存于一般固废暂存间,定期外售。喷漆不合格品经过底漆或面漆修补后作为合格产品进入下一道工序;喷粉除尘器收尘灰收集回用于生产。废印刷版、槽渣、碱蚀槽弃液、漆渣、废显影液、污水处理站污泥、含镍污泥、乳化液、废机油、废包装桶、废油漆桶、废活性炭经分类收集后暂存于危废暂存间,定期交由有资质的单位进行处置,其收集、暂存及转运过程中的管理应严格按照《危险废物贮存污染控制标准》(GB18597-2023)《危险废物转移管理办法》(部令第23号)等规定执行,并做好台账记录。项目产生的固废种类较多,投入运营后,你公司应对加强固废属性鉴别,根据鉴**果确定管理办法,以确保处置方式的可行性。 噪声污染防治措施。加强产噪设备管理,通过建筑隔音、减震以及距离衰减等措施,确保厂界噪声满足《工业企业厂界环境噪声排放标准》(GB12348-2008)3类区标准,区域声环境满足《声环境质量标准》(GB3096-2008)2类区标准要求。 | 实际建设情况:项目一期工程已规范建设雨污分流系统,在厂区内设置了污水收集输送系统,未采取明沟布设。电抛光废水进入抛光废水处理系统(规模不小于5m3/d,采用“过滤系统→低温蒸发→浓酸回收箱”处理工艺)处理,浓缩的酸浓液委托**海螺****公司进行处理,不外排;含镍废水进入含镍废水处理系统(规模不小于5m3/d,采用“一体化物化处理装置→回调箱→**箱→多介质过滤器→活性炭吸附器→两级重金属吸附罐”处理工艺)处理后,总镍满足《电镀污染物排放标准》(GB21900-2008)中车间或生产设施排放限值,其余指标满足《污水排入城镇下水道水质标准》(GB/T31962-2015)限值要求,随同****工业园区污水管网****处理站。**1****处理站(规模为30m3/d,采用“芬顿工艺→物化反应→高效斜管沉淀池→回调箱中和pH→多介质过滤和活性炭过滤”处理工艺),染色废水经脱色处****处理站,脱脂废水经“一体化物化处理装置→批次反应箱”处****处理站,金属CNC废水循环使用,每年更换一次,委托**海螺****公司清运处置,阳极氧化生产线和喷粉生产线其余水洗槽废水、废气处理废水、制软水****处理站处理,食堂废水经隔油池沉淀后与其他生活污水进入化粪池处理,废水总铬、总镍满足《电镀污染物排放标准》(GB21900-2008)车间或生产设施排放限值,总铝、总锌、总铜、总铁满足《电镀污染物排放标准》(GB21900-2008),其余指标满足《污水排入城镇下水道水质标准》(GB/T31962-2015)限值要求后进入达标排放池,通****工业园区污水管网****处理站。根据监测结果,项目一期运营期废水可做到达标排放。 项目一期已落实分区防控措施。处理站、化学品仓库、阳极氧化间、污泥暂存间、危险废物暂存间等区域已采取重点防渗,防渗层按等效黏土防渗层厚度不小于6.0m,渗透系数不大于1x10-7cm/s,或参考《危险废物填埋污染控制标准》(GB18598-2019)要求进行防渗;生产车间、一般固废暂存间等区域已采取一般防渗,防渗层按等效黏土防渗层厚度不小于1.5m,渗透系数不大于1x10-7cm/s,或参考《****填埋场污染控制标准》(GB16889-2008)要求进行防渗;其他区域已采取一般地面硬化。根据区域水文地质情况,合理设置了地下水跟踪监测井,定期进行跟踪监测,并将根据监测情况及时完善相应的污染防治措施。 项目一期铝合金喷砂工段产生的含颗粒物废气经袋式除尘器处理通过1根15m高的排气简(DA001)排放,根据监测结果满足《大气污染物综合排放标准》(GB16297-1996)限值要求。中和出光槽和阳极氧化槽酸雾通过引风机收集后接入1#酸雾吸收塔处理后通过1根15m高的排气筒(DA002)排放;电解抛光酸洗槽酸雾通过引风机收集后接入2#酸雾吸收塔处理后通过1根15m高的排气简(DA003)排放;根据监测结果,硫酸雾、氮氧化物满足《电镀污染物排放标准》(GB21900-2008)限值要求。 已加强对废气无组织排放的管理:铝合金板材切割粉尘收集后进入袋式除尘器处理后,通过无组织排放方式通过厂房风扇外排,减少了无组织粉尘排放量,根据监测结果可做到达标排放。项目已设置100m的卫生防护距离。 项目一期已按《一般工业固体废物贮存和填埋污染控制标准》(GB18599-2020)要求建设一般固体废物临时堆存场所,边角料、废铁砂、废包装材料、铝合金板材加工和喷砂除尘器收尘、金属面板次品等分类收集后暂存于一般固废暂存间,定期外售。 已按照《危险废物贮存污染控制标准》(GB18597-2023)《危险废物转移管理办法》(部令第23号)要求建设危废暂存间,酸碱等化学原料废包装桶暂存于危废暂存间后由生产厂家回收,不外排。槽渣、碱蚀槽弃液、含镍污泥、污水处理站污泥、CNC废液(废切削液)、废酸液、乳化液、废机油收集后暂存于危废暂存间,定期交由**海螺****公司进行处置,其收集、暂存及转运过程中的管理均严格按照《危险废物贮存污染控制标准》(GB18597-2023)《危险废物转移管理办法》(部令第23号)等规定执行,并做好了台账记录。项目一期采取建筑隔音、减震以及距离衰减等措施,根据监测结果,厂界噪声满足《工业企业厂界环境噪声排放标准》(GB12348-2008)3类区标准。 |
(1)环评审批的一期建设项目阳极氧化工艺中的电解抛光废水、化学抛光废水更换后暂存于抛光废水暂存池,分批次进入抛光废水处理系统,处理后的浓缩的酸浓液回用到电抛槽,无废水外排,而实际生产过程处理后的浓缩的酸浓液暂存于危险废物暂存间后委托**海螺****公司处理,无废水外排。(2)环评审批的CNC废水经“一体化物化处理装置→批次反应箱”处****处理站,而实际生产过程CNC废水循环使用,每年更换一次,更换后暂存于危险废物暂存间后委托**海螺****公司处理,不外排。 | 是否属于重大变动:|
其他
/ | 实际建设情况:/ |
/ | 是否属于重大变动:|
3、污染物排放量
0 | 0.86 | 0 | 0 | 0 | 0.86 | 0.86 | |
0 | 0.524 | 4.5524 | 0 | 0 | 0.524 | 0.524 | |
0 | 0 | 0.3942 | 0 | 0 | 0 | 0 | |
0 | 0 | 0 | 0 | 0 | 0 | 0 | |
0 | 0 | 0 | 0 | 0 | 0 | 0 | |
0 | 0 | 0.0041 | 0 | 0 | 0 | 0 | |
0 | 0 | 0.0005 | 0 | 0 | 0 | 0 | |
0 | 0 | 0.0022 | 0 | 0 | 0 | 0 | |
0 | 0 | 0.0015 | 0 | 0 | 0 | 0 | |
0 | 0 | 0 | 0 | 0 | 0 | 0 | / |
0 | 0 | 0 | 0 | 0 | 0 | 0 | / |
0 | 0 | 0 | 0 | 0 | 0 | 0 | / |
0 | 0 | 0 | 0 | 0 | 0 | 0 | / |
0 | 0 | 0 | 0 | 0 | 0 | 0 | / |
4、环境保护设施落实情况
表1 水污染治理设施
1 | 隔油池、化粪池 | 《污水排入城镇下水道水质标准》(GB/T-31962-2015)表1中B等级 | 已建设 | 已监测 | |
2 | 抛光废水处理系统、染色废水处理系统、含镍废水处理系统、脱脂废水处理系统、综合废水处理系统 | 《电镀污染物排放标准》GB21900-2008和《污水排入城镇下水道水质标准》(GB/T-31962-2015)表1中B等 | 已建设 | 已监测 |
表2 大气污染治理设施
1 | 袋式除尘器 | 《大气污染物综合排放标准》(GB16297-1996) | 已建设 | 已监测 | |
2 | 袋式除尘器处理+1根高15m的排气筒 | 《大气污染物综合排放标准》(GB16297-1996) | 已建设 | 已监测 | |
3 | 1#酸雾吸收塔+15m高的排气筒 | 《电镀污染物排放标准》(GB21900-2008) | 已建设 | 已监测 | |
4 | 2#酸雾吸收塔+15m高的排气筒 | 《电镀污染物排放标准》(GB21900-2008) | 已建设 | 已监测 |
表3 噪声治理设施
1 | 设备全部置于厂房内、围墙隔声、合理布局、采用减震、隔声、消音绿化降噪 | 《工业企业厂界环境噪声排放标准》(GB12348-2008)中3类标准 | 已建成 | 已监测 |
表4 地下水污染治理设施
1 | 落实分区防控措施。处理站、化学品仓库、喷漆车间、酸洗磷化工段、阳极氧化间、污泥暂存间、危险废物暂存间等区域采取重点防渗,防渗层按等效黏土防渗层厚度不小于6.0m,渗透系数不大于1x10-7cm/s,或参考《危险废物填埋污染控制标准》(GB18598-2019)要求进行防渗;生产车间、一般固废暂存间等区域采取一般防渗,防渗层按等效黏土防渗层厚度不小于1.5m,渗透系数不大于1x10-7cm/s,或参考《****填埋场污染控制标准》(GB16889-2008)要求进行防渗;其他区域采取一般地面硬化。根据区域水文地质情况,合理设置地下水跟踪监测井,定期进行跟踪监测,根据监测情况及时完善相应的污染防治措施 | 项目一期已落实分区防控措施。处理站、化学品仓库、阳极氧化间、污泥暂存间、危险废物暂存间等区域已采取重点防渗,防渗层按等效黏土防渗层厚度不小于6.0m,渗透系数不大于1x10-7cm/s,或参考《危险废物填埋污染控制标准》(GB18598-2019)要求进行防渗;生产车间、一般固废暂存间等区域已采取一般防渗,防渗层按等效黏土防渗层厚度不小于1.5m,渗透系数不大于1x10-7cm/s,或参考《****填埋场污染控制标准》(GB16889-2008)要求进行防渗;其他区域已采取一般地面硬化。根据区域水文地质情况,合理设置了地下水跟踪监测井,定期进行跟踪监测,并将根据监测情况及时完善相应的污染防治措施。 |
表5 固废治理设施
1 | 认真落实固体废物的贮存、处理和处置措施。一般固体废物临时堆存场所应符合《一般工业固体废物贮存和填埋污染控制标准》(GB18599-2020)要求,边角料、废铁砂、废包装材料、铝合金板材加工和喷砂除尘器收尘、喷粉不合格品、金属面板和玻璃面板次品等分类收集后暂存于一般固废暂存间,定期外售。喷漆不合格品经过底漆或面漆修补后作为合格产品进入下一道工序;喷粉除尘器收尘灰收集回用于生产。废印刷版、槽渣、碱蚀槽弃液、漆渣、废显影液、污水处理站污泥、含镍污泥、乳化液、废机油、废包装桶、废油漆桶、废活性炭经分类收集后暂存于危废暂存间,定期交由有资质的单位进行处置,其收集、暂存及转运过程中的管理应严格按照《危险废物贮存污染控制标准》(GB18597-2023)《危险废物转移管理办法》(部令第23号)等规定执行,并做好台账记录。项目产生的固废种类较多,投入运营后,你公司应对加强固废属性鉴别,根据鉴**果确定管理办法,以确保处置方式的可行性。 | 项目一期已按《一般工业固体废物贮存和填埋污染控制标准》(GB18599-2020)要求建设一般固体废物临时堆存场所,边角料、废铁砂、废包装材料、铝合金板材加工和喷砂除尘器收尘、金属面板次品等分类收集后暂存于一般固废暂存间,定期外售。 已按照《危险废物贮存污染控制标准》(GB18597-2023)《危险废物转移管理办法》(部令第23号)要求建设危废暂存间,酸碱等化学原料废包装桶暂存于危废暂存间后由生产厂家回收,不外排。槽渣、碱蚀槽弃液、含镍污泥、污水处理站污泥、CNC废液(废切削液)、废酸液、乳化液、废机油收集后暂存于危废暂存间,定期交由**海螺****公司进行处置,其收集、暂存及转运过程中的管理均严格按照《危险废物贮存污染控制标准》(GB18597-2023)《危险废物转移管理办法》(部令第23号)等规定执行,并做好了台账记录。 |
表6 生态保护设施
表7 风险设施
1 | 加强应急处置。加强危险化学品运输、储存、使用过程环境风险防范措施,制定和完善环境风险及突发环境事件应急预案,****环境局**分局备案。落实各项环境风险防范对策措施,定期开展事故应急演练。 | 本项目已编制完成突发环境事件应急预案,并备案,备案号为530323-2024-031-L |
5、环境保护对策措施落实情况
依托工程
不涉及 | 验收阶段落实情况:不涉及 |
/ |
环保搬迁
不涉及 | 验收阶段落实情况:不涉及 |
/ |
区域削减
不涉及 | 验收阶段落实情况:不涉及 |
/ |
生态恢复、补偿或管理
不涉及 | 验收阶段落实情况:不涉及 |
/ |
功能置换
不涉及 | 验收阶段落实情况:不涉及 |
/ |
其他
项目建成后,你公司应按照《建设项目竣工环境保护验收暂行办法》(国环规环评[2017]4号)相关要求完成竣工环境保护自主验收,并按《排污许可管理条例》《排污许可管理办法(试行)》要求申领排污许可证。 | 验收阶段落实情况:项目已取得排污许可证,证书编号为:****0323MA6NPB3D0C001P。目前正在进行一期工程竣工环境保护验收 |
/ |
6、工程建设对项目周边环境的影响
/ |
/ |
/ |
/ |
/ |
/ |
7、验收结论
1 | 未按环境影响报告书(表)及其审批部门审批决定要求建设或落实环境保护设施,或者环境保护设施未能与主体工程同时投产使用 |
2 | 污染物排放不符合国家和地方相关标准、环境影响报告书(表)及其审批部门审批决定或者主要污染物总量指标控制要求 |
3 | 环境影响报告书(表)经批准后,该建设项目的性质、规模、地点、采用的生产工艺或者防治污染、防止生态破坏的措施发生重大变动,建设单位未重新报批环境影响报告书(表)或环境影响报告书(表)未经批准 |
4 | 建设过程中造成重大环境污染未治理完成,或者造成重大生态破坏未恢复 |
5 | 纳入排污许可管理的建设项目,无证排污或不按证排污 |
6 | 分期建设、分期投入生产或者使用的建设项目,其环境保护设施防治环境污染和生态破坏的能力不能满足主体工程需要 |
7 | 建设单位因该建设项目违反国家和地方环境保护法律法规受到处罚,被责令改正,尚未改正完成 |
8 | 验收报告的基础资料数据明显不实,内容存在重大缺项、遗漏,或者验收结论不明确、不合理 |
9 | 其他环境保护法律法规规章等规定不得通过环境保护验收 |
不存在上述情况 | |
验收结论 | 合格 |
招标导航更多>>
工程建筑
交通运输
环保绿化
医疗卫生
仪器仪表
水利水电
能源化工
弱电安防
办公文教
通讯电子
机械设备
农林牧渔
市政基建
政府部门
换一批
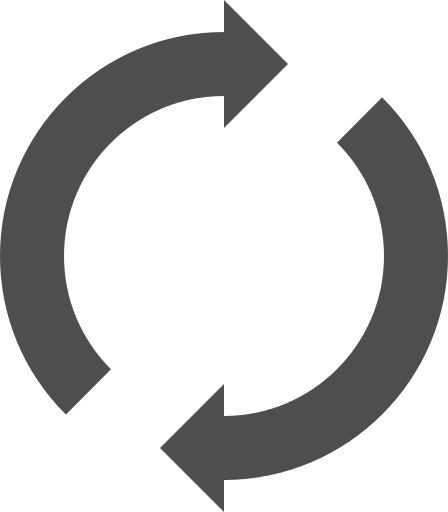